Comprehensive Insights into AB Coating Technology
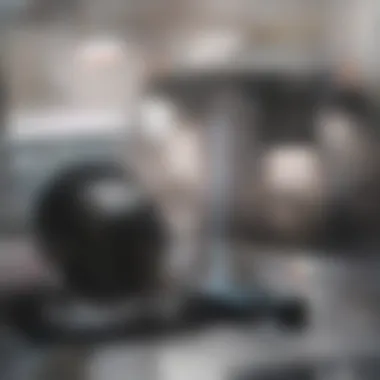
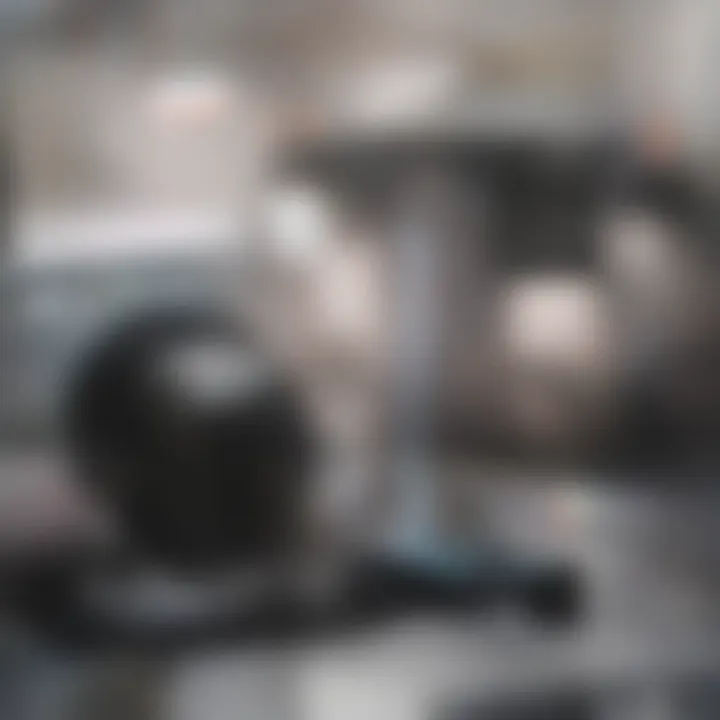
Intro
AB coating is a precision chemical processing method that has gained significant traction across multiple industries. This innovative technology plays a crucial role in enhancing the performance and durability of various materials, especially in optics and electronics. Understanding how AB coating operates, along with its diverse applications, is essential for students, researchers, and professionals seeking to utilize this technology effectively.
As industries evolve, the demand for high-quality materials increases. AB coating contributes to this need by providing advanced surface properties that improve product performance. This article aims to unpack the principles behind AB coating, exploring its importance and future trends that are shaping its ongoing development in technical fields.
Research Overview
Summary of Key Findings
- Applications across Sectors: AB coatingβs reach extends to optics, electronics, and beyond, making it a versatile technique.
- Enhanced Performance: The process provides excellent durability and function, essential in enhancing various applications.
- Future Developments: Evolving technologies and methods could reshape AB coating applications and efficiency in the years to come.
Background and Context
AB coating refers to a specialized process employed mainly to modify the surface properties of materials. The significance of this technology lies in its ability to enhance substrate underlying qualities such as chemical resistance, adhesion, and overall performance. In optics, coatings can be employed to produce anti-reflective surfaces or specialized filters, while in electronics, they are vital for creating protective layers on circuit boards and components.
The evolution of AB coating is closely linked to advancements in materials science and chemistry. As manufacturing processes continue to integrate more sophisticated technologies, the scope and complexity of AB coating are likely to advance as well. Understanding this background is essential for professionals aiming to incorporate AB coating into modern applications.
Prelude to AB Coating
The introduction of AB Coating serves as a fundamental part of this article, guiding the reader into the realm of this specialized chemical process. Understanding AB Coating is essential due to its extensive relevance across several industries today. It offers numerous advantages that not only enhance performance but also contribute to durability in varied applications. Given the rapid advancements in technology, a comprehensive overview becomes crucial for those seeking both theoretical knowledge and practical insights.
Definition and Overview
AB Coating refers to a unique chemical layering technique where two different substances are layered to achieve specific properties. Typically, this involves applying a thin film of material onto a substrate, which can be glass, plastic, or metal. The primary goal is to enhance certain characteristics such as optical properties, resistance to scratching, or improved electrical performance. The chemical process plays a crucial role in controlling how these materials bond and perform under various conditions.
For instance, in the optics industry, AB Coating provides anti-reflective properties which are critical in lens manufacturing. This enhances light transmission and provides better clarity in optical devices. The combination of materials in AB Coating can also improve surface properties, contributing to the functionality in electrical components.
Historical Context and Development
Examining the historical context of AB Coating reveals a progressive evolution driven by technological demands. The origins can be traced back to the mid-20th century when researchers began exploring thin film technologies. As industries like electronics and optics emerged, the need for effective surface coatings became apparent.
Through the decades, the principles of AB Coating experienced significant refinement. Innovations in chemical compositions and application techniques led to wider adoption across various sectors. Companies started to recognize the benefits, including enhanced performance and longer-lasting products. Today, continuous advancements in materials science enable the development of smarter coatings, which suggests that the journey of AB Coating is as dynamic as the technologies it supports.
As technology evolves, AB Coating stands at the forefront, anticipating changes and challenges of the future across many disciplines.
Fundamentals of AB Coating
The fundamentals of AB Coating provide critical insight into the reinforcement of various applications across multiple industries. Understanding the core concepts about this process is essential for revealing how it meets the unique needs of optical, electronic, and medical sectors. One of the main benefits is that AB Coating enhances the performance and longevity of coated surfaces. Additionally, knowledge about its components and methods establishes a solid foundation for researchers and practitioners aiming to innovate or apply this technology.
Chemical Composition
AB Coatings are typically composed of a blend of polymers and additives that determine final attributes such as adhesion, durability, and optical clarity. The poly(methyl methacrylate) known as PMMA is often used for its optical transparency and resistance to UV light. The specific formulation can vary, allowing for customization depending on the end-use requirements.
This variability allows chemists to fine-tune properties to achieve desired characteristics that can better serve specific industrial purposes. For example, coatings containing silanes can improve bonding to substrates, while adding certain fillers can modify light transmission properties. Understanding this composition is paramount as it directly affects how well the coating performs in practical applications.
Application Techniques
AB Coating can be applied through various techniques that have distinct benefits and suitability depending on the project.
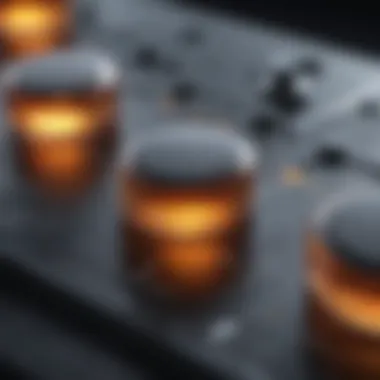
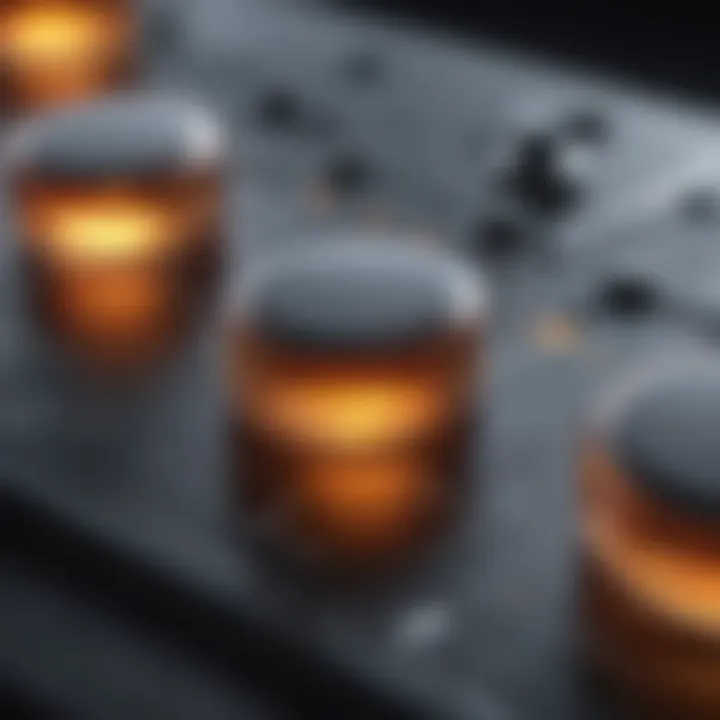
Spin Coating
Spin coating is a process where a small amount of liquid coating is dispensed onto a substrate, which is then spun rapidly to spread the liquid evenly. This technique is highly valued due to its ability to create thin and uniform films. A key characteristic of spin coating is its efficiency in covering large areas quickly with minimal material waste, making it a popular choice in laboratories and production environments.
However, while it excels in creating uniform films, it can also be limited when dealing with substrates that are not flat or have complicated geometries.
Dip Coating
Dip coating involves immersing objects into a liquid coating solution, allowing for even coverage as the object is pulled out of the liquid. This method is particularly advantageous for covering intricate shapes and large surfaces uniformly. Its key contribution lies in the simplicity of the process, which is both time-efficient and cost-effective for batch production.
One downside is the potential for excess coating material, which may require additional steps for removal or control. Nonetheless, its versatility in various applications makes it a valuable technique in the AB Coating domain.
Spray Coating
Spray coating is a process that utilizes a spray gun to atomize the coating material, allowing for even application over complex surfaces. This method is notable for its adaptability; it can be used on small components and large structures alike. The key characteristic of spray coating is its ability to provide good control over layer thickness and coverage, which can be crucial for achieving specific performance characteristics.
On the downside, this technique may lead to overspray and waste unless managed carefully. Environmental factors such as temperature and humidity can also impact the coating quality during the application process. However, the overall flexibility and efficiency of spray coating make it essential in many industrial applications, from electronics to automotive.
Properties of AB Coating Materials
The properties of AB coating materials are central to their application in various industries. Understanding these properties allows engineers and scientists to tailor coatings for specific uses. The significance of optical, mechanical, and thermal characteristics can not be overstated. Each of these attributes contributes to performance, longevity, and overall functionality of the end products.
Optical Properties
AB coatings are notable for their optical properties, particularly their ability to manipulate light. They can enhance or diminish transparency and alter light reflection and absorption. This is crucial in sectors like optics and photonics. For instance, anti-reflective coatings improve visibility and efficiency in lenses and screens.
- Transparency: The clarity of a coating affects light transmission.
- Refractive Index: This measures how light bends when passing through the coating.
- Reflectivity: Some coatings are designed to reflect light efficiently, useful in mirrors.
Improving these properties can lead to better performance in photonic devices, such as lasers. A well-designed optical coating maximizes output by minimizing loss.
Mechanical Properties
Mechanical properties determine how AB coatings withstand physical forces, essential for durability and reliability. The coatings must resist scratches, wear, and impact. Their resistance to deformation and breakage dictates suitability in several applications.
- Adhesion: A strong bond between the coating and the substrate enhances durability.
- Hardness: This defines the ability to resist scratches and abrasion.
- Flexibility: Some applications require coatings to bend without cracking.
Striking a balance between these attributes is vital. For example, a very hard coating might be brittle, increasing the risk of cracking during handling or application.
Thermal Stability
Thermal stability refers to the coating's performance at varying temperatures. In many applications, exposure to extreme heat or cold can lead to failure or inefficiency. For instance, coatings used in aerospace must maintain integrity under high-stress situations, such as fluctuating temperatures and pressures.
- Decomposition Temperature: This indicates the point at which the coating begins to break down.
- Thermal Conductivity: A coating with appropriate thermal conductivity can manage heat effectively, preventing overheating or temperature-related failures.
- Thermal Expansion: A good coating should expand and contract with minimal stress, avoiding fractures.
The properties of AB coating materials dictate their suitability for use across various applications. By understanding these properties, professionals can make informed decisions about material selection and application methods. Ultimately, these properties not only enhance functionality but also play a vital role in the longevity of products.
Applications of AB Coating
AB coating technology is integral to numerous industries, each leveraging its unique properties for enhanced performance and functionality. Understanding these applications helps to appreciate the influence of AB coatings across different sectors. The benefits of these coatings often translate into improved efficiency, durability, and performance in various demanding environments.
Optics and Photonics
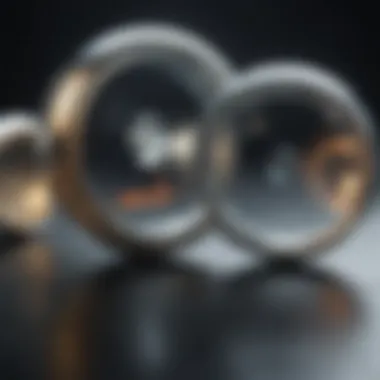
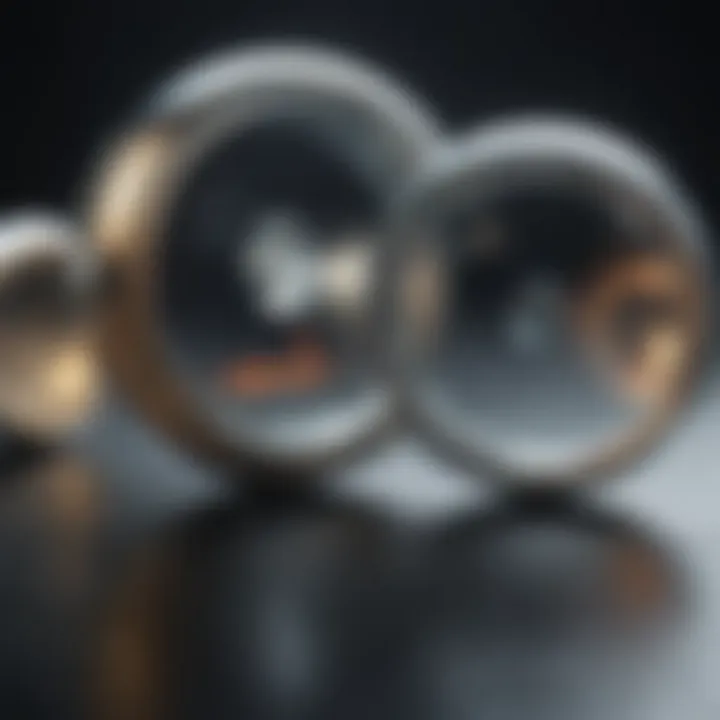
In the field of optics and photonics, AB coatings play a crucial role. They are used to create anti-reflective surfaces which enhance light transmission through lenses and other optical devices. By minimizing surface reflection, these coatings improve the overall efficiency of optical systems, allowing for clearer images and better performance in applications ranging from cameras to telescopes.
Coating processes like spin coating are often employed to achieve uniform thickness. The precise control in thickness ensures consistent optical properties. Innovations in materials, such as high-index and low-index films, can optimize performance even further. Testing for clarity and effectiveness is essential in this application to ensure high standards are met.
Electronics and Semiconductors
AB coating is vital in the electronics and semiconductor industries. These coatings protect sensitive circuits from environmental factors like moisture, dust, and chemicals. They provide insulation, thus enhancing the reliability and longevity of electronic devices.
Spray coating techniques are commonly used here to apply protective layers. The flexibility in application allows coatings to conform to various shapes and sizes, which is especially necessary for modern intricate designs in semiconductors. Furthermore, the dielectric properties of these coatings hold significant importance for performance, enabling better signal integrity and reduced electrical noise.
Medical Devices
AB coatings find extensive use in medical devices. They are utilized to enhance biocompatibility, preventing adverse reactions when devices come into contact with biological tissues. Coatings like silicone or hydrophilic polymers create a smoother interface, which can also aid in the longevity of implants or surgical instruments.
Instruments coated with AB materials tend to resist bacterial growth, thus improving hygiene and safety. The coating processes must adhere to strict regulatory standards to ensure safety and effectiveness, making this application one of the most scrutinized in terms of quality control.
Aerospace Applications
In aerospace, the applications of AB coatings are complex and multifaceted. Coatings help to reduce drag on aircraft surfaces, thereby improving fuel efficiency. Additionally, these coatings provide protection against extreme temperatures and environmental degradation.
The application of AB coatings to aircraft and spacecraft requires specialized techniques, such as dip coating, to ensure thorough coverage. The coatings need to exhibit not just durability, but also a lightweight characteristic. The future of AB coatings in aerospace looks promising, with ongoing research focused on enhancing their thermal stability and lightweight properties.
"AB coating technology not only improves the performance of products but also extends their operational life across several challenging environments."
Advantages of AB Coatings
AB coatings provide a variety of advantages that make them a valuable choice in numerous industries. Their significance lies in the unique properties they confer on the substrates they coat. These advantages can enhance both performance and durability, influencing design choices in optics, electronics, and other fields. Understanding these benefits allows professionals to make informed decisions regarding their applications.
Enhanced Performance
Enhanced performance is one of the primary advantages of AB coatings. When properly applied, these coatings can significantly improve the optical qualities of materials. For instance, anti-reflective coatings reduce glare and increase transmission rates. This is crucial in optical devices where clarity and light penetration are paramount. Similarly, in electronics, AB coatings can enhance signal integrity. They can provide better insulation and improve the overall functionality of electronic components.
The effectiveness of AB coatings in boosting performance is evident in various sectors. For example, in telecommunications, using AB coated lenses can lead to better signal quality by minimizing distortions. In medical devices, improved performance can lead to precise measurements and better patient outcomes.
Improved Durability
Durability is another essential benefit of AB coatings. These coatings provide protection against environmental factors such as moisture, dust, and chemicals. This is particularly important in industrial settings where machinery and equipment face harsh conditions. The coatings can act as barriers, preventing wear and corrosion, which in turn prolongs the life of the coated materials.
Additionally, AB coatings can improve scratch resistance. This characteristic is highly valued in consumer electronics and optics. Screens and lenses that are coated with durable materials can withstand everyday use better, thus maintaining their clarity and functionality over time.
In summary, the advantages of AB coatings extend across different domains, making them a critical element in modern technology. Emphasizing enhanced performance and improved durability not only benefits manufacturers but also contributes to customer satisfaction and operational efficiency.
Challenges in AB Coating Implementation
The implementation of AB coating presents several challenges that can affect its efficacy and acceptance across various sectors. Understanding these challenges is crucial for professionals involved in the process, as it directly impacts not only cost but also the quality and sustainability of the coatings being produced. Analyzing these challenges reveals the intricate balance between performance expectations and practicality for industries that depend on AB coatings.
Cost of Materials
The financial aspect of AB coating materials cannot be understated. The raw materials required for AB coatings often carry a premium price tag. High-quality polymers and inert solvents are essential for achieving the desired coating properties, and these can significantly increase production costs. In industries where profit margins are tightly controlled, such as electronics and optics, the cost of materials becomes an essential consideration.
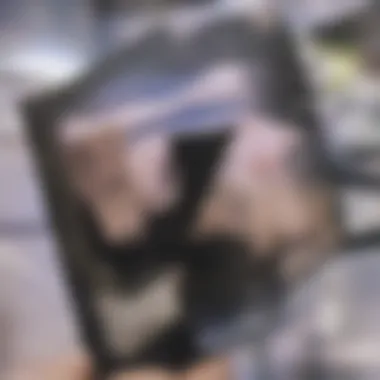
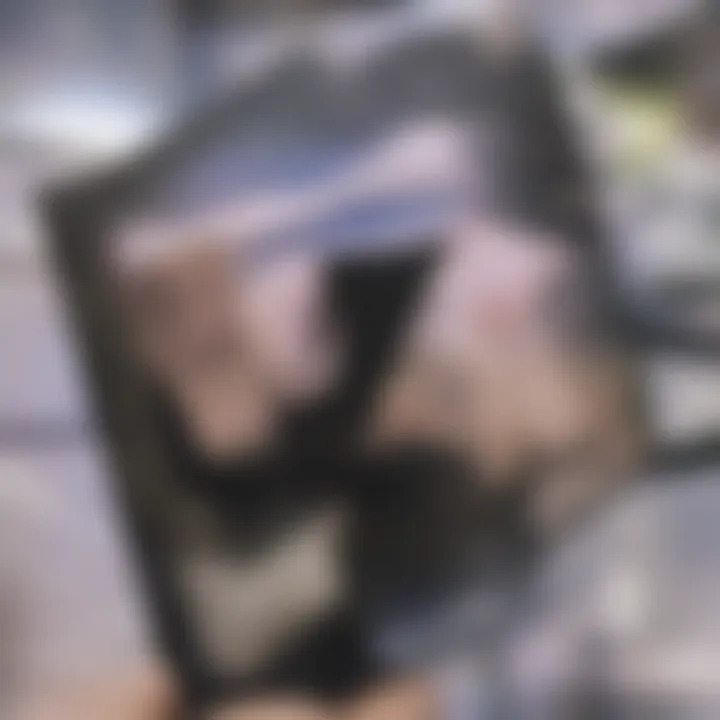
Additionally, fluctuating prices for these materials can affect long-term project budgets. Companies may find it beneficial to investigate alternatives, but substitutes can lead to balanced performance and quality concerns. An analysis of bulk purchasing strategies and supplier relationships may offer some mitigation of these costs.
Quality Control Issues
Quality control remains a critical point in the successful implementation of AB coatings. Due to the sensitivity of the coating process, slight variations can result in significant differences in coating performance. For instance, if the application procedure is not meticulously controlled, outcomes can range from subpar adhesion to uneven layering, leading to a loss of integrity in the final product.
Implementation of comprehensive quality control protocols is essential. This includes regular monitoring of the application equipment, precise measurements of material mixtures, and thorough inspections of the final coating. Nonetheless, ensuring consistency in these factors can be labor-intensive, demanding both skilled labor and technological investment. Hence, companies must weigh the costs of these processes against the benefits of high-quality output.
Environmental Concerns
Environmental issues associated with AB coatings have garnered attention in recent years. The solvents used in the AB coating process can be volatile and harmful to both health and the environment. Many regions are imposing regulations on the levels of volatile organic compounds (VOCs) permissible in industrial applications. Manufacturers must navigate these regulations carefully to avoid substantial penalties.
Furthermore, the disposal of waste materials from the coating process can pose additional environmental risks. Innovations in recycling and waste reduction methods are being explored, but these also require an upfront investment and a shift in operational practices.
There is a growing emphasis on sustainability in many industries. As such, the adoption of eco-friendly materials and processes is becoming a strategic focus. It is essential for firms to stay ahead of regulatory requirements and consumer expectations, which often prioritize eco-friendly solutions.
To succeed in AB coating implementation, companies must address cost, quality, and environmental concerns simultaneously. A balanced approach fosters innovation while steering compliance with regulations and market expectations.
Future Trends in AB Coating Technology
Future trends in AB coating technology are critical to the ongoing advancement in various industries. The ability to innovate in this area can lead to improved performance, functionality, and sustainability. As the demand for high-quality coatings grows, understanding these trends will help professionals and researchers stay ahead in the market.
Innovations in Materials
Recent advancements in materials science have driven significant innovations in AB coating. Researchers are exploring new polymer composites and nanomaterials, which offer enhanced characteristics such as increased durability and superior optical properties. For example, incorporating graphene into coatings can improve both mechanical strength and thermal conductivity.
These innovations are essential to meet the specific needs of different industries. The electronics sector, for instance, may benefit from coatings that provide better conductivity or dielectric properties. Similarly, in medical devices, coatings that resist biofilm formation can enhance device longevity and patient outcomes.
Automation and Smart Coating Processes
Automation in AB coating processes is another significant trend. Streamlining application techniques through automated systems reduces human error and increases efficiency. Smart coating processes that use sensors and real-time data analysis can ensure optimal application conditions.
Such automation also allows for greater customization. Manufacturers can adjust parameters rapidly based on specific requirements, leading to improved product quality while reducing waste. This alignment of technology with production not only enhances productivity but also makes it easier to maintain consistent coating applications across different environments.
Sustainability Practices
Sustainability is becoming an essential factor in all sectors, and AB coating technology is no exception. Companies are increasingly focused on developing eco-friendly materials and processes. This includes using non-toxic solvents and minimizing hazardous waste during the coating application.
Furthermore, the push for sustainable practices also leads to research in biodegradable coatings that meet the same performance standards as traditional materials. Such advancements not only comply with regulations but also appeal to environmentally conscious consumers, providing a competitive edge in the marketplace.
"The future of AB coating technology hinges on a commitment to innovation and sustainability."
Epilogue
In this article, we have traversed the multifaceted world of AB Coating. The importance of this topic cannot be overstated. AB Coating is foundational to many modern technological applications. Its impact on sectors such as optics, electronics, and aerospace showcases its versatility. The detailed exploration reveals how AB Coating enhances product performance while addressing real-world challenges.
Summary of Key Insights
AB Coating serves critical roles in various industries. Its unique properties such as thermal stability, mechanical strength, and optical clarity are essential for the functionality of many products. Here are the core insights from our examination:
- The chemical composition of AB Coating is pivotal for achieving desired characteristics.
- Multiple application techniques, including spin and dip coating, allow versatility and adaptability.
- While there are significant advantages like improved durability, challenges such as material costs and environmental implications demand attention.
- Future trends hint at innovations that could transform production processes and enhance sustainability.
"Understanding AB Coating is vital for industries aiming for excellence in their offerings."
Final Thoughts on AB Coating
As we conclude our exploration, it is clear that AB Coating is more than just a technical process. It holds the potential to drive innovation and improve the quality of life through advanced technology. For students, researchers, and professionals, a thorough understanding of AB Coating opens doors to various opportunities in crafting superior products. Being aware of the ongoing developments will also enable these stakeholders to navigate the complexities of material science effectively. In summary, AB Coating will remain a pivotal focus for industries striving for better solutions.