Assembly Machines: Shaping the Future of Manufacturing
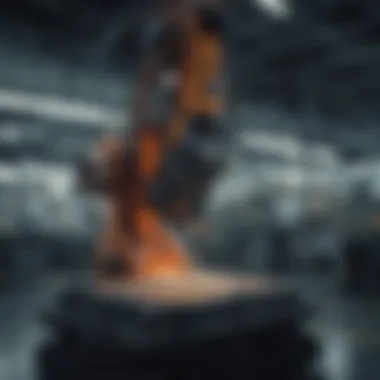
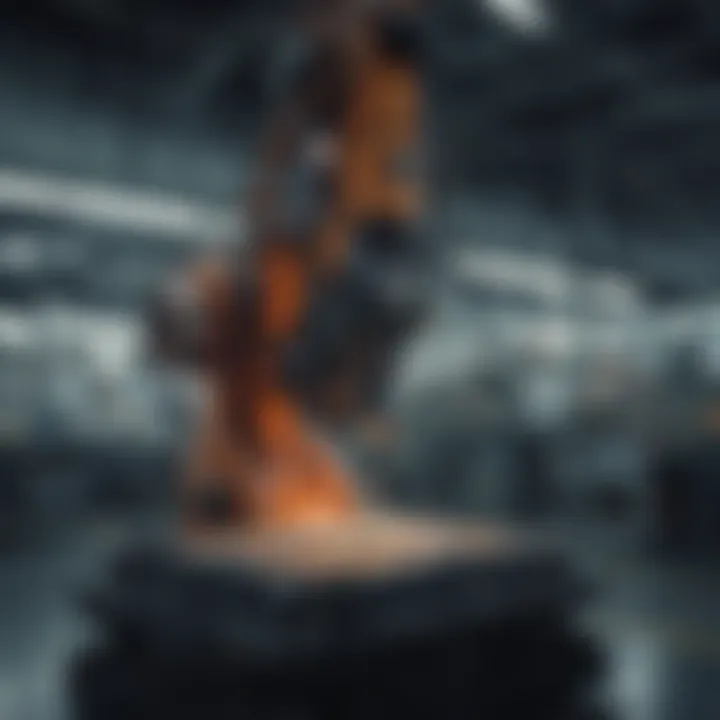
Intro
In the realm of manufacturing, efficiency and precision are paramount. Assembly machines serve as the backbone of modern production lines, drastically altering how industries approach production tasks. This article aims to provide an in-depth look into the evolution, current applications, and future potential of these critical machines. By understanding assembly machines, one gains insight into the future of industrial production and its challenges.
Research Overview
Summary of Key Findings
The examination of assembly machines reveals several critical elements: their evolution from simple mechanical devices to sophisticated systems that integrate automation and artificial intelligence. Key findings include:
- Technological Advancement: Assembly machines have transitioned from manual operation to fully automated systems, increasing production rates.
- Impact on Quality: Advanced assembly machines enhance product consistency and reduce defects.
- Integration with AI and Robotics: These machines now often incorporate AI algorithms to optimize workflows and adapt to varying production requirements.
Background and Context
Historically, the introduction of assembly lines revolutionized manufacturing processes. Early assembly machines were primarily mechanical, yet they laid the groundwork for future innovations. The 20th century saw a surge in technological progress, driven by electronics and computers. Today, assembly machines are not just tools of production; they are intelligent systems capable of learning and adjusting to their environment.
Technological Advancements in Assembly Machines
The development of assembly machines reflects broader trends in technology. Notable advancements include:
- Robotic Integration: Many assembly processes now employ robotics, which significantly enhance precision and handle complex tasks.
- Automation: Automation reduces the need for manual labor while improving consistency, resulting in higher overall production efficiency.
- Data Analytics: Real-time data tracking allows for better decision-making and predictive maintenance, extending the lifespan of the machines.
Current Applications in Industry
Assembly machines are pivotal across various industries. Some key applications include:
- Automotive Industry: Here, assembly machines handle everything from welding to painting. Their accuracy ensures safety and compliance with standards.
- Electronics Manufacturing: In this sector, machines are used to assemble components with minute tolerances. Their capability to adapt to different types of devices adds versatility.
- Consumer Goods Production: Fast-moving consumer goods benefit from assembly machines that facilitate rapid production cycles, meeting market demands efficiently.
Future Trends and Challenges
The future of assembly machines is shaped by ongoing trends and potential challenges. This includes:
- Emerging AI Technologies: As AI continues to evolve, assembly machines will become even more autonomous, capable of performing complex tasks without human intervention.
- Sustainability: There is a growing emphasis on environmentally friendly practices. Future assembly machines may integrate recycling capabilities and minimize waste.
- Skills Gap: As machines become more advanced, there is a pressing need for skilled workers who can operate and maintain these systems. This poses a challenge for industries.
Important Note: Embracing these advancements in assembly machines requires careful consideration of the implications on labor and production processes.
Closure
The trajectory of assembly machines outlines a path toward increased productivity and more intelligent manufacturing. As industries invest in these technologies, understanding their evolution, applications, and future potential become essential for anyone involved in production today or in the future.
Preface to Assembly Machines
Assembly machines play a significant role in modern manufacturing processes. They serve as a core element in the industrial landscape by streamlining production, enhancing efficiency, and ensuring product consistency. Understanding assembly machines is vital as they have undergone significant transformations to adapt to technological advancements and market demands. In this article, we will delve into the various types of assembly machines and their applications across different industries, while also exploring the benefits and challenges associated with these systems.
Definition and Purpose
Assembly machines are designed to automate and facilitate the process of assembling various components into a finished product. These machines can operate in different capacities, ranging from manual to fully automated systems. Their primary purpose is to reduce labor intensity, minimize errors, and increase production rates.
The efficiency brought by assembly machines significantly impacts production output. They allow manufacturers to produce large volumes of goods in shorter timeframes compared to traditional manual methods. Furthermore, they contribute to improved quality control. With precise specifications, these machines ensure that each component is assembled accurately, resulting in a higher standard of finished products.
Historical Context
The evolution of assembly machines is closely tied to the rise of industrialization. The late 18th and early 19th centuries saw significant manufacturing changes with the introduction of mechanization. Early assembly techniques, such as the use of simple tools and hand-operated machines, laid the foundation for more advanced solutions.
In the early 20th century, Henry Ford revolutionized manufacturing with the introduction of the assembly line concept in automobile production. This innovation increased efficiency dramatically and is often credited as a benchmark in manufacturing history. Over time, assembly machines have become more sophisticated, integrating technology such as robotics and artificial intelligence.
Today, assembly machines continue to evolve, reflecting advancements in fields like automation and IoT (Internet of Things). As industries embrace new technologies, the future of assembly machines looks promising, emphasizing flexibility, adaptability, and further improvements in operational efficiency.
Types of Assembly Machines
Understanding the types of assembly machines is crucial in the study of modern manufacturing. Each type serves different needs and possesses unique features that cater to specific production requirements. Recognizing these distinctions helps businesses choose the most suitable option depending on their workflow, product nature, and budget constraints.
Manual Assembly Machines
Manual assembly machines offer a straightforward approach to product assembly. These machines rely heavily on human labor, combining hands-on skill and expertise. While this method may not achieve rapid production, it allows for a personalized touch on products. Workers can make adjustments on-the-fly, ensuring that each piece meets quality standards.
The main benefit of manual assembly is flexibility. Workers can easily switch tasks and adapt to different products without the need for extensive reconfiguration. This is particularly beneficial for businesses producing a low volume of customized goods. However, the drawbacks are also significant. Manual assembly is more susceptible to human errors, leading to inconsistencies in product quality. Additionally, the production rate is usually slower compared to automated systems, meaning that businesses might struggle to keep up with high demand.
Semi-Automatic Assembly Machines
Semi-automatic assembly machines represent a middle ground between manual and fully automatic systems. They require some human input but perform the bulk of the work with machines. Workers may load components onto the assembly line or monitor the process, while machines handle repetitive tasks automatically.
This hybrid approach provides several advantages. It allows for improved efficiency compared to manual methods while retaining flexibility. Common in industries that require moderate production levels, semi-automatic systems can adapt to different product formats without significant downtime. However, they also come with the challenge of needing skilled operators who can manage the human and machine interactions effectively.
Fully Automatic Assembly Machines
Fully automatic assembly machines are the epitome of efficiency in manufacturing. These systems operate without human intervention, relying on complex algorithms and robotics to complete tasks. The main advantage of fully automatic machines is their speed and precision. They can produce large volumes of products consistently, reducing labor costs significantly.
However, the initial investment for fully automatic systems can be quite high. Businesses must weigh the cost against the potential long-term savings and efficiency gains. Maintenance is another issue; these machines require regular servicing to ensure continuance. Fully automatic systems also limit flexibility, as changing product lines can necessitate extensive reprogramming or reconfiguration.
In summary, understanding the different types of assembly machines is essential for selecting the right system in manufacturing. Each type—manual, semi-automatic, and fully automatic—has its own advantages and challenges. Evaluating the specific needs and conditions of a production environment will guide companies in making informed decisions.
Components of Assembly Machines
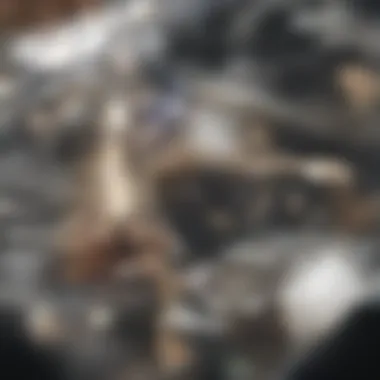
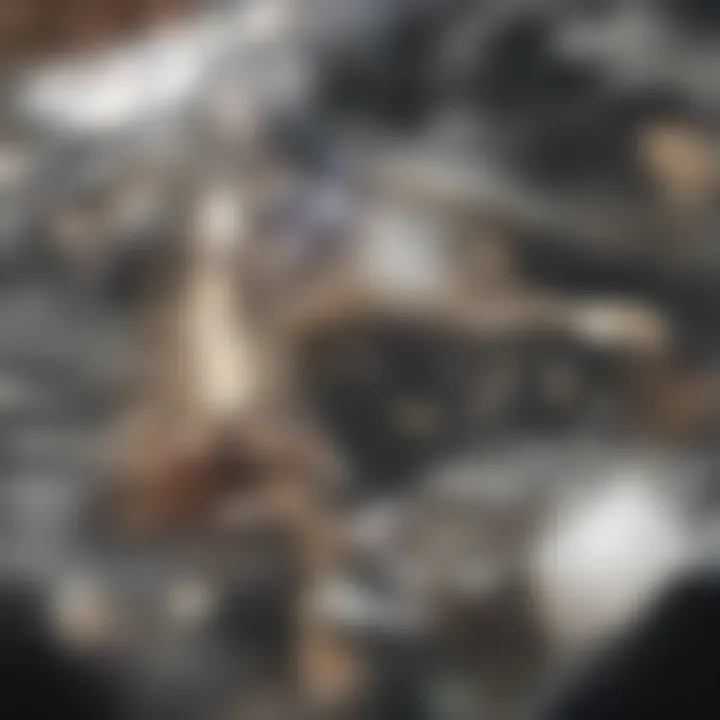
Understanding the components of assembly machines is crucial. These elements work together to streamline the manufacturing process. They contribute significantly to increased efficiency and product consistency. Each component plays its unique role in the overall system. Their integration is vital for optimal functioning.
Conveyor Systems
Conveyor systems form the backbone of most assembly machines. They transport materials and components across different stages of production. This continuous movement reduces manual handling. As a result, it enhances speed and minimizes the risk of errors. Incorporating conveyor systems leads to:
- Improved workflow
- Reduced cycle time
- Increased safety for workers
Conveyor belts, rollers, and chains are common types used. They can be customized based on the products being manufactured. A well-designed conveyor system is essential for maintaining production pace. It also helps to align various assembly processes seamlessly.
Robotic Arms
Robotic arms are redefining the assembly landscape. These machines perform tasks that require precision. They can assemble, pick, and place components effectively. Their programmable nature allows for flexibility in operations. Here are some benefits of robotic arms:
- Enhanced precision and repeatability
- Capability to work in hazardous environments
- Reduced labor costs over time
Many industries utilize robotic arms for repetitive tasks. In the automotive sector, for instance, they assemble parts with high efficiency. This not only speeds up production but also ensures quality consistency throughout.
Sensors and Controls
Sensors and controls are integral for monitoring the assembly process. They gather data and help in adjusting operations in real-time. With accurate data input, manufacturers can:
- Detect faults or irregularities
- Optimize quality control measures
- Streamline operations through automation
Common types of sensors include proximity sensors, vision systems, and force sensors. They enhance the capability of assembly machines by providing feedback. This feature is essential for maintaining high standards in production.
All these components together form a cohesive unit. Their interaction determines the overall efficiency of assembly processes.
Advantages of Using Assembly Machines
The use of assembly machines in manufacturing isn’t just a trend; it represents a vital shift in how products are created. This section elaborates on the various advantages associated with these machines. Their impact spans production rate, product quality, and cost efficiencies. Understanding these elements allows industry stakeholders to make informed decisions regarding their production methods.
Increased Production Rate
One of the most significant benefits of assembly machines is the considerable increase in production rate. These machines operate continuously and with high precision. Unlike manual labor, where human fatigue can slow down work, machines maintain a consistent output. This reliability leads to a steady flow of products, which helps meet market demand effectively.
- Automation plays a key role here. Automated systems can work 24/7, which means that a manufacturing unit can produce more units in the same timeframe.
- Assembly machines often feature optimizations in design that enable faster assembly processes, minimizing idle times.
In industries like automotive and electronics, every second saved can lead to significant gains in overall productivity. The ability to quickly ramp up production during peak times becomes crucial for businesses competing in fast-paced markets.
Enhanced Product Quality
Maintaining high quality is critical in manufacturing. Assembly machines contribute positively by ensuring enhanced product quality. These machines apply uniform force and precision during the assembly process, minimizing human error and variability. When machines handle tasks that require meticulous attention to detail, consistency in quality improves.
- Quality Control systems integrated into assembly machines often involve sensors that detect issues in real-time. This allows for immediate correction, reducing the chances of defective products reaching the market.
- The application of advanced technologies, such as machine learning, enables these systems to adapt and improve continuously, further enhancing the final products.
This focus on quality helps build brand reputation and customer trust, crucial elements for sustaining long-term success in any industry.
Cost Efficiency
Lastly, cost efficiency is a crucial advantage of employing assembly machines. Though the initial investment may be significant, the reduction in long-term operational costs justifies the outlay. Assembly machines minimize labor costs as they require fewer operators to achieve the same output as a larger manual workforce.
- Reduced waste is another financial benefit. Automated processes lead to better material utilization, whereas manual processes can often result in scrap or rework.
- Additionally, maintenance costs can be effectively managed through scheduled upkeep, ensuring the machines run efficiently without costly downtimes.
In summary, the advent of assembly machines marks a pivotal change in industrial production. The advantages of increased productivity, enhanced quality, and cost efficiency make them indispensable in today’s manufacturing landscape. As industries continue to evolve, these machines will likely play a central role in shaping the future of production.
Challenges in Implementing Assembly Machines
High Initial Investment
Implementing assembly machines can be financially daunting for many firms. The high initial investment can include costs for purchasing the machinery, installation, and the necessary technology for integration. This financial burden is a critical barrier, especially for small and medium-sized enterprises. Many businesses might find it hard to secure funds or justify the expenditure, particularly when operating on tight margins.
Despite this challenge, companies must evaluate the long-term return on investment. As assembly machines streamline operations, they can significantly boost productivity and reduce labor costs over time. Thus, the initial capital outlay should be analyzed in the context of potential savings and increased revenue in the future.
Maintenance and Downtime
The ongoing maintenance of assembly machines is another significant concern. Any mechanical or operational failure can lead to unplanned downtime, disrupting production workflows. This situation can lead to delays in meeting customer demands and potential financial losses. Regular maintenance schedules can help mitigate such risks, but they require additional planning and resources.
It is crucial for businesses to invest in training their staff, ensuring they understand how to carry out routine maintenance and effectively troubleshoot minor issues. This proactive approach is key to maximizing the lifespan of the machines and minimizing costly interruptions during the production process.
Workforce Adaptation
Workforce adaptation emerges as a notable challenge when integrating assembly machines. As systems become more automated, existing employees may feel threatened by the technology. There can be a gap in skills required for operating sophisticated machinery. As a result, firms may need to invest in retraining programs to help current staff adapt to their new roles alongside machinery.
Resistance to change can also present obstacles. Employees familiar with traditional methods might struggle with new processes. Open communication about the benefits of the new technology can foster a more positive transition.
Technological Advances in Assembly Machines
Technological advances in assembly machines represent a crucial aspect of modern manufacturing. These innovations not only enhance efficiency but also redefine how production lines operate. Understanding these advances is essential for students, researchers, educators, and professionals in the field. Various technologies work in concert to create a more agile and responsive manufacturing environment.
Automation and Industry 4.
Automation forms the backbone of Industry 4.0, the current trend of automation and data exchange in manufacturing technologies. Assembly machines increasingly employ automated systems to streamline operations.
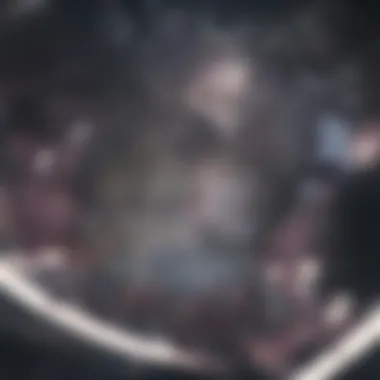
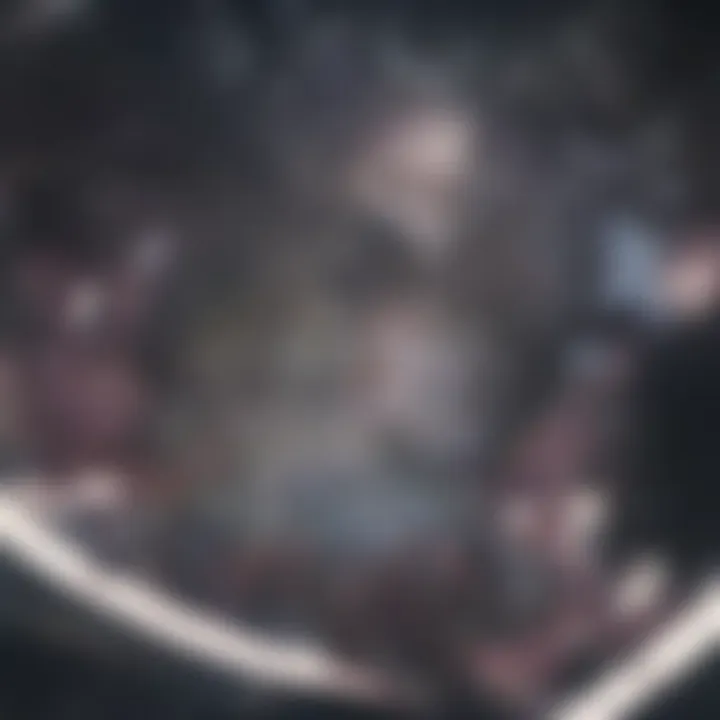
Benefits include:
- Increased Efficiency: Assembly lines that utilize automation can operate continuously, minimizing downtime.
- Real-time data analysis: Automated systems can collect data to inform operational decisions quickly.
- Scalability: Automated assembly solutions can scale production based on demand without compromising quality.
As factories adopt automation, there is a need for workers who can manage and troubleshoot these systems. This creates shifts in workforce skills, emphasizing the need for training programs to prepare existing employees for such changes.
Integration with AI and Machine Learning
The integration of artificial intelligence (AI) and machine learning technologies into assembly machines is transforming production. AI systems can analyze patterns in production data, optimizing workflows and reducing waste.
Key advantages include:
- Predictive Maintenance: AI can predict when machines require maintenance, potentially avoiding costly breakdowns.
- Quality Control: Machine learning algorithms can detect defects in products faster and more accurately than human inspectors.
- Adaptive Manufacturing: Machines can adjust to changes in product design or specifications automatically.
This integration underscores the importance of interdisciplinary expertise. Engineers must understand both manufacturing processes and AI technologies to design systems that leverage their full potential.
Internet of Things (IoT) in Assembly
The Internet of Things (IoT) allows assembly machines to connect and communicate throughout the production process. Through interconnected sensors and devices, manufacturers can monitor operations remotely and in real-time.
Benefits of IoT in assembly include:
- Enhanced Monitoring: Real-time monitoring of equipment can lead to improved operational efficiency.
- Data-Driven Insights: Generating large volumes of data helps manufacturers make informed decisions.
- Resource Optimization: IoT enables better management of inventories and supplies, reducing waste.
Implementation of IoT systems does require careful consideration of security measures to protect sensitive data from cyber threats. As with other technologies, the potential rewards come with inherent risks that must be managed carefully.
Technological advances, especially in automation, AI, and IoT, are not merely trends but fundamental shifts redefining industrial production dynamics.
In summary, the integration of advanced technologies into assembly machines plays an essential role in revitalizing manufacturing. Understanding and adapting to these technological changes will be key for anyone involved in the industry. As these technologies evolve, they will continue to shape the future landscape of production.
Applications of Assembly Machines in Industries
The application of assembly machines spans various industries, each benefiting from increased efficiency, consistency, and adaptability. Understanding these applications is crucial for recognizing the transformative role assembly technology plays in modern manufacturing. The rise of assembly machines has not only optimized production flows but also allowed companies to meet consumer demands effectively. As industries evolve, the integration of these machines becomes equally important for maintaining competitive advantage.
Automotive Industry
In the automotive sector, assembly machines form the backbone of vehicle production. Complex assemblies, such as engines and chassis, require precision and speed. Automotive manufacturers like Toyota and Ford leverage fully automatic and robotic assembly systems to enhance productivity. By employing robotics, tasks such as welding, painting, and assembly of components are executed with high accuracy.
These machines are vital in reducing cycle times and minimizing defects. Additionally, automated systems allow for increased customization options and flexibility in production lines, catering to varying consumer preferences without significantly disrupting the workflow.
Electronics Manufacturing
The electronics industry is another sector where assembly machines demonstrate their significance. Devices such as smartphones, tablets, and computers require intricate assembly processes. By using advanced technologies like surface mount technology (SMT) machines, manufacturers can increase their production capacity while ensuring quality control.
Assembly machines in this domain enable rapid prototyping and expedite product testing, critical in a fast-paced market. Firms like Samsung and Apple benefit from these technologies, allowing them to release products faster, thus responding swiftly to market trends.
Consumer Goods Production
In consumer goods production, assembly machines streamline the assembly of everyday items, ranging from household appliances to packaged foods. The use of semi-automatic machines allows manufacturers to maintain a balance between human oversight and machine efficiency. Brands such as Procter & Gamble and Unilever exploit these systems to enhance production capabilities while keeping costs manageable.
These machines are designed to accommodate various packaging formats and sizes, thus offering businesses adaptability in their manufacturing processes.
Automation in consumer goods production has become essential, especially as demands for speed and variety increase.
Future Trends in Assembly Machines
Future trends in assembly machines are shaping the landscape of industrial production. Understanding these trends is crucial for industry stakeholders seeking to stay competitive in an evolving marketplace. This section explores key elements such as collaborative robots, flexible manufacturing systems, and sustainable practices.
Collaborative Robots (Cobots)
Collaborative robots, often called cobots, are designed to work alongside human workers. They enhance the efficiency of assembly lines by taking on repetitive tasks, which frees human workers to focus on more complex activities. This synergy not only increases productivity but also reduces the risk of injury for human operators, as the cobots handle heavy lifting or dangerous processes. Moreover, cobots are often equipped with advanced sensors and AI, enabling them to adapt to their environment and work safely beside humans.
Benefits of implementing cobots in manufacturing include:
- Improved worker safety
- Increased flexibility in production lines
- Enhanced productivity
- Cost-effectiveness due to lower labor expenses
However, companies must address the integration of cobots with existing systems carefully. A comprehensive training program is vital to ensure employees can effectively collaborate with these machines.
Flexible Manufacturing Systems
Flexible manufacturing systems (FMS) represent another important trend. These systems can quickly adapt to changes in the type and quantity of products being produced. With consumer preferences shifting rapidly, businesses are under pressure to reduce lead times and increase variety. An FMS allows for this adaptability, facilitating a more efficient response to market demands.
Key features of flexible manufacturing systems include:
- Modular machinery that can be reconfigured easily
- Automated tools that change based on product specifications
- Real-time monitoring for optimal performance and maintenance
Implementing an FMS leads to higher efficiency and lower inventory costs, crucial for maintaining competitiveness in today's manufacturing landscape. However, businesses must prepare for significant technological investments and training.
Sustainability and Eco-Friendly Practices
Sustainability is becoming an essential consideration in industry practices. Assembly machines must not only focus on efficiency and productivity but also on reducing environmental impact. Eco-friendly practices can include energy-efficient machinery, waste reduction programs, and the use of sustainable materials.
Incorporating sustainable practices into assembly processes offers numerous advantages:
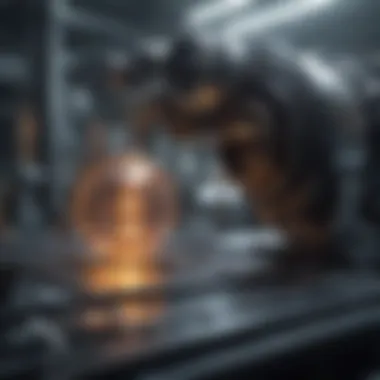
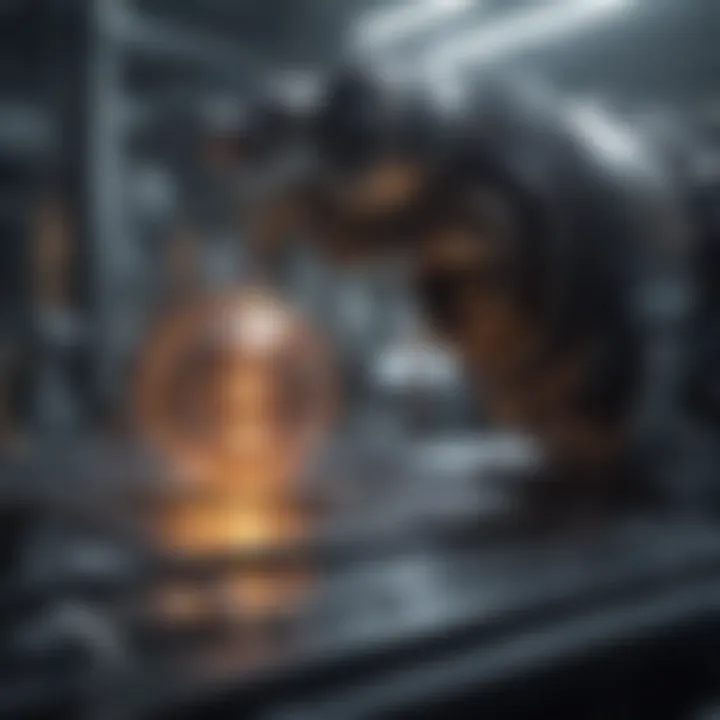
- Enhanced brand reputation
- Compliance with regulatory standards
- Long-term cost savings through reduced energy use
As companies strive for sustainable operations, they face challenges. Balancing costs while investing in green technologies can be complex. Nonetheless, sustainability is no longer just a trend; it is becoming a necessity for future growth in the industrial sector.
"Embracing sustainability is not just about responsibility but also about seizing new business opportunities in the green economy."
Case Studies: Successful Implementation
The importance of case studies in understanding the implementation of assembly machines cannot be understated. They provide concrete examples of how businesses adopt these technologies to improve production efficiency and enhance product quality. By examining real-world scenarios, insights can be gained into the unique challenges each organization faces and the strategies they employ to overcome them. These case studies also highlight the tangible benefits that can be derived from assembly machines, which reinforces their value in modern manufacturing.
Global Automotive Leader
One notable case involves a global automotive leader, Toyota, which has integrated advanced assembly machines into its production lines. The company has utilized a combination of fully automatic assembly machines and collaborative robots, known as cobots. The results have been outstanding. Efficiency increased significantly, and production times were reduced. The robots work alongside human workers, taking over repetitive tasks, allowing the human workforce to focus on quality control and other complex operations.
Benefits observed include:
- Increased throughput: By streamlining the assembly process, Toyota can produce vehicles at a much faster rate.
- Enhanced quality control: Robots are programmed to execute precise tasks consistently, reducing errors in assembly.
- Safety improvements: The use of machines for hazardous tasks has led to a safer work environment for employees.
These advantages illustrate how learning from such implementations can offer valuable lessons for other manufacturers aiming to modernize their processes.
Innovative Electronics Firm
Similarly, an innovative electronics firm, Apple, has transformed its manufacturing approach through the adoption of semi-automatic assembly machines. By incorporating automation in the assembly of devices like iPhones, Apple has managed to maintain a competitive edge in the market. The integration of sensors and machine learning algorithms has allowed for real-time adjustments in assembly processes, further optimizing production.
Key outcomes from this case study include:
- Consistency in product quality: Automated systems minimize variations, ensuring that each product meets strict quality standards.
- Cost reduction: Automation decreases labor costs and the potential for human error, leading to overall savings.
- Adaptability: The company can easily repurpose machines to accommodate new product lines, ensuring longevity in their capital investments.
This proactive approach demonstrates the necessity of embracing technology for sustained success in the electronics sector.
Consumer Goods Company Transformation
Another informative case is the transformation undertaken by Procter & Gamble (P&G). This consumer goods company faced challenges with traditional assembly lines that were proving inflexible and costly to maintain. By switching to flexible manufacturing systems that incorporate assembly machines, they significantly improved their operational effectiveness.
The specific benefits noted in this transition included:
- Greater flexibility: The machines can be programmed for different assembly tasks, which enables quicker changes in production lines based on market demand.
- Inventory management: Improved systems lead to better tracking and handling of raw materials, reducing waste and storage costs.
- Sustainability: P&G emphasized eco-friendly practices by opting for energy-efficient machines, which aligns with the growing demand for sustainable manufacturing.
This case study emphasizes the role of assembly machines in adapting to market demands while addressing environmental concerns.
"Learning from successful implementations provides a roadmap for others in the industry, demonstrating not only the immediate benefits but also the strategic advantages of assembly machines."
Regulatory Considerations
The role of regulatory considerations in the implementation of assembly machines cannot be overstated. As industries advance towards more automated processes, understanding safety regulations and environmental standards becomes crucial. Compliance with various regulations ensures not only the safety of workers but also the long-term sustainability of production practices.
Regulatory frameworks guide the design, operation, and maintenance of assembly machines. These frameworks enhance safety standards, thus protecting employees from potential hazards that can arise during machine operation. Moreover, adhering to these standards can lead to increased efficiency and reliability in manufacturing processes.
Safety Standards and Compliance
Safety standards are essential for any industry that utilizes assembly machines. Agencies such as the Occupational Safety and Health Administration (OSHA) set regulations that companies must follow to ensure a safe working environment. These regulations cover various aspects, including machine guarding, ergonomic practices, and employee training.
By complying with safety standards, firms can minimize workplace accidents which are costly both in human and financial terms. Companies that prioritize safety through compliance not only protect their workforce but also improve their reputation and foster trust among consumers.
Important aspects include:
- Regular risk assessments to identify potential hazards.
- Implementation of safety measures such as emergency stop buttons and safety guards.
- Routine training programs for employees on safe operation procedures and protocols.
"Compliance with safety regulations is not just a requirement, but a commitment to operational excellence."
Environmental Regulations
Environmental regulations have become increasingly relevant in the context of assembly machines. These regulations focus on reducing environmental impact, ensuring that the manufacturing processes are sustainable. Compliance with such regulations can influence an organization’s operational decisions and their supply chain management.
Assembly machines can have a significant environmental footprint, especially through energy consumption and waste generation. Regulations often require organizations to adopt more sustainable practices, such as:
- Utilizing energy-efficient machines.
- Implementing waste reduction strategies in production.
- Monitoring emissions to comply with local environmental standards.
By integrating these environmentally friendly practices, companies do not just adhere to regulations; they also embrace corporate responsibility. This shift toward sustainability can lead to cost savings and improved public perception.
In summary, regulatory considerations are essential for businesses that rely on assembly machines. Safety standards protect workers while environmental regulations promote sustainable practices. Understanding and complying with these various regulations is a necessary step for firms aiming to maintain competitiveness in an increasingly regulated marketplace.
Finale
The conclusion of this article serves as a vital element in synthesizing the information provided throughout regarding assembly machines and their growing significance in industrial production. It encapsulates the essential insights discussed in earlier sections, providing clarity on the complex interactions between technology, production efficiency, and product quality. A well-structured conclusion reflects on the advantages and challenges outlined, reinforcing the need for strategic planning in adopting assembly machines.
Summary of Key Insights
In reviewing the key points from this article, several insights emerge:
- Technological Evolution: Assembly machines have advanced significantly from manual systems to highly automated solutions, integrating robotics and AI.
- Industry Applications: Various sectors, including automotive and electronics manufacturing, benefit from efficiencies realized through assembly machine deployment.
- Production Efficiency: Increased production rates and improved product quality are direct results of sophisticated assembly technology, which leads to greater customer satisfaction and competitive advantage.
- Challenges in Implementation: While the benefits are clear, organizations often face hurdles such as high initial costs, the need for workforce adaptation, and maintenance concerns.
Reflecting on these points helps stakeholders appreciate the complexities of implementing assembly machines while recognizing their essential contributions to modern manufacturing practices.
Implications for Future Research
As assembly machines continue to evolve, they beckon further exploration in several key areas:
- Integration with Advanced Technologies: Future research should focus on how emerging technologies like IoT and AI can further enhance assembly processes.
- Sustainability Concerns: Investigations into eco-friendly practices within assembly lines will be increasingly important as global production standards shift toward sustainability.
- Workforce Dynamics: As machine capabilities expand, studies are needed to understand the implications for workforce dynamics and job training in industrial settings.
- Market Dynamics and Economic Impact: Understanding the broader economic implications of widespread assembly machine adoption will help forecast trends and inform policy decisions.