Foamed Polymers: Composition and Applications
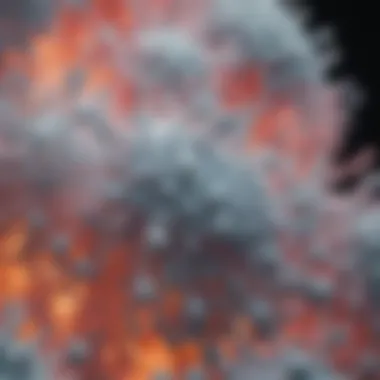
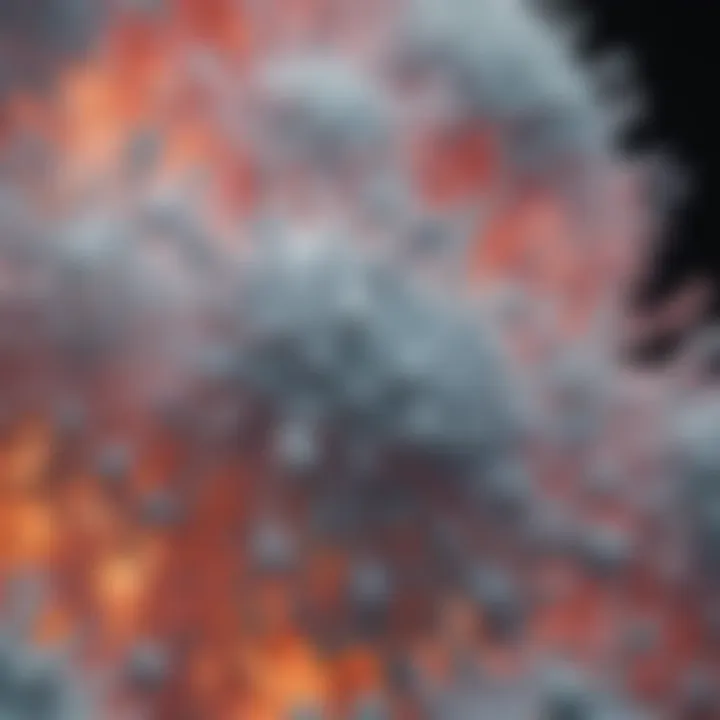
Intro
Foamed polymers have emerged as a significant category of materials, known for their unique structures and versatile applications. This article delves into their composition, properties, and manufacturing techniques, as well as their wide-ranging uses in industries such as automotive, packaging, construction, and healthcare. Understanding the characteristics of foamed polymers is vital for advancing current technology and improving the performance of products derived from these materials.
Foamed polymers can be distinguished by their cellular structures, which contribute to their lightweight, insulating, and cushioning properties. In recent years, innovations in manufacturing and product design have led to expanded applications and improved material performance. These developments are particularly important given the growing demand for sustainable materials in various sectors.
"Understanding foamed polymers is essential for their application in modern industries, impacting everything from sustainability to innovative product design."
As we explore the depths of foamed polymers, this article aims to provide an insightful overview and thorough analysis that caters to students, researchers, educators, and professionals engaged in materials science and engineering.
Prelude to Foamed Polymers
Foamed polymers are increasingly recognized for their unique properties and vast applications. They serve critical roles across various industries, such as construction, automotive, and healthcare. Understanding the composition and characteristics of these materials is essential for researchers, students, and professionals. This article provides a comprehensive guide to foamed polymers, bringing to light their composition, properties, and applications.
The importance of the introduction lies in establishing a foundational understanding of foamed polymers before delving into their specific types and manufacturing methods. By laying this groundwork, we ensure that readers appreciate the nuances in the subsequent sections, which detail varying types and their various utilitarian functions.
Definition and Characteristics
Foamed polymers are materials characterized by their cellular structures, which are formed through the inclusion of gas bubbles during their creation. These bubbles can greatly influence their mechanical properties, density, and thermal insulation capabilities. The most significant type of foamed polymers includes thermoplastic, thermosetting, and elastomeric foams. Each of these foams exhibits distinct characteristics and responds differently to external conditions and applications.
One key characteristic of foamed polymers is their lightweight nature, which makes them extremely advantageous for applications requiring a reduction in weight without compromising durability. Furthermore, the cells or pores in foamed polymers contribute to their excellent thermal and acoustic insulation properties, making them suitable for various purposes ranging from insulation in buildings to cushioning in packaging.
Historical Context
The development of foamed polymers can be traced back to the mid-20th century when the demand for lightweight, durable materials began to rise. The first significant advancements occurred in the 1940s and 1950s, when scientists started manipulating the chemical processes to create various types of foams. Expanded polystyrene, commonly known as EPS, emerged during this period and became a staple in packaging materials.
Over the decades, research and innovation have led to the emergence of newer foamed polymers with enhanced properties. This ongoing evolution has responded to increasing global demands for more sustainable and efficient materials. Today, the field of foamed polymers continues to grow with more interest in environmentally friendly manufacturing processes.
Types of Foamed Polymers
Foamed polymers are essential materials in various industries due to their lightweight structures and versatility. Understanding the types of foamed polymers is critical in selecting the right material for specific applications. Each type possesses unique properties that cater to different needs, from thermal insulation to mechanical stability.
Thermoplastic Foams
Thermoplastic foams are made from thermoplastic polymers, which become soft when heated and harden upon cooling. This property allows for easy processing and reshaping of the material, making it suitable for a variety of applications.
Key Characteristics:
- Lightweight: These foams are typically lighter than other types, which is advantageous in industries that prioritize weight reduction.
- Recyclability: Thermoplastic foams can be reprocessed multiple times, aligning with sustainability efforts.
- Versatility: They can be easily bonded and formed into complex shapes.
Common Applications:
- Packaging materials for fragile items.
- Insulation boards in construction.
- Automotive interiors that require lightweight sound and thermal insulation.
Thermosetting Foams
Thermosetting foams are formed from thermosetting polymers, which undergo a chemical change during the curing process. Once set, these foams do not soften upon heating. This characteristic leads to superior thermal and chemical resistance, although they cannot be reshaped or recycled after the curing process.
Key Characteristics:
- High dimensional stability: They retain their shape and mechanical properties under varying conditions.
- Excellent thermal resistance: Ideal for applications requiring exposure to heat.
- Chemical resistance: They withstand exposure to certain chemicals better than thermoplastics.
Common Applications:
- Electrical insulation in various devices.
- Construction components that need durability and heat resistance.
- Structural parts where strength is a critical factor.
Elastomeric Foams
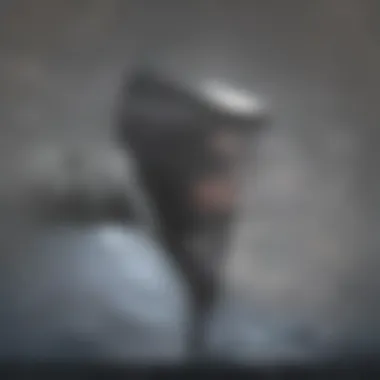
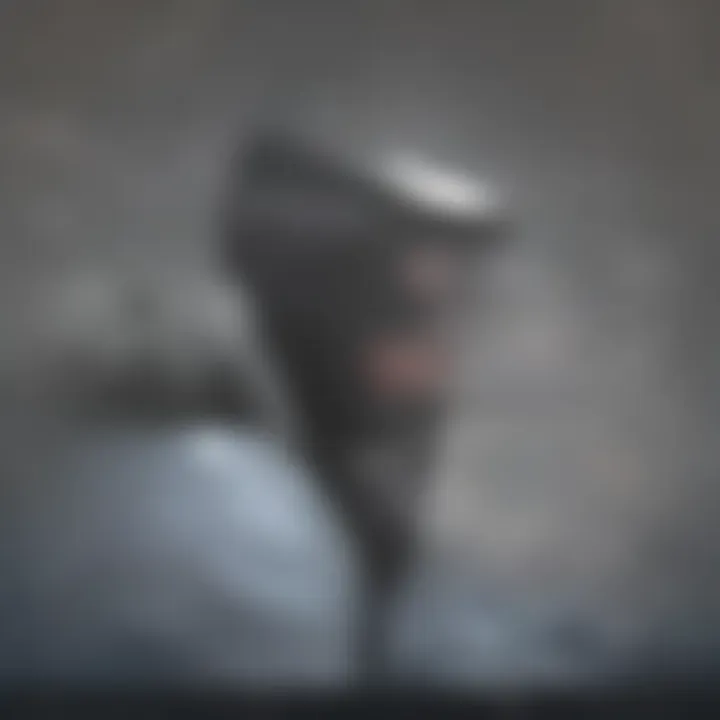
Elastomeric foams are unique due to their elastomer base, providing flexibility and resilience. They combine properties of traditional rubber with foamed structures. This gives elastomeric foams excellent cushioning effects and the ability to recover from deformation.
Key Characteristics:
- High elasticity: They can be compressed or stretched and return to their original shape.
- Impact resistance: Suitable for applications requiring cushioning.
- Moisture-resistant: This makes them ideal for environments where resistance to water is necessary.
Common Applications:
- Mattresses and cushions for comfort and support.
- Seals and gaskets in appliances or automotive parts.
- Sports equipment that requires shock absorption.
Manufacturing Processes
The manufacturing processes for foamed polymers are critical to their overall performance and functionality. Understanding these methods allows manufacturers to tailor the foams for specific applications, achieving desired properties such as density, thermal insulation, and mechanical strength. Various processes may be employed, each with unique benefits and considerations. These can impact the end product's quality, efficiency, and cost-effectiveness.
Physical Foaming Methods
Physical foaming methods involve the use of physical means to create a foam structure. These techniques rely primarily on the dispersion of gas within the polymer matrix. Common physical foaming methods include:
- Extrusion Foaming: This process involves melting the polymer and adding a blowing agent, which rapidly expands under controlled conditions to form foam.
- Injection Foaming: In this method, a polymer is injected into a mold along with a gaseous blowing agent, creating foam upon cooling.
- Compression Foaming: Here, pressure is applied to a polymer melt to create a foam structure as it cools.
Each of these methods allows for control over final foam properties, such as density and cell structure. The selection of the appropriate method depends on the required specifications for the foamed polymer.
Chemical Foaming Agents
Chemical foaming agents are substances that generate gas upon mixing with the polymer or during heating. They create foam by releasing gas as the polymer undergoes thermal processes. Common chemical foaming agents include azodicarbonamide and sodium bicarbonate.
These agents can be categorized into:
- Endothermic Agents: They absorb heat during chemical reactions, producing gas at elevated temperatures.
- Exothermic Agents: These release heat and gas during reactions, allowing for foaming to occur at lower temperatures.
Utilizing chemical foaming agents can enhance the properties of the produced foam. However, they must be carefully selected to ensure they do not degrade the polymer or create harmful byproducts in the process.
Factors Influencing Foam Formation
Several factors influence the formation and quality of foamed polymers. These include:
- Blowing Agent Type: The selection between physical or chemical foaming agents is crucial. Depending on the application, one may yield better results than the other.
- Processing Temperature: Higher temperatures often allow better gas expansion, but excessive heat can harm polymer structure.
- Polymer Viscosity: Low viscosity polymers typically create finer and uniform cell structures, enhancing insulation properties.
- Cooling Rate: Fast cooling may trap gas within bubbles, affecting the foam density and mechanical properties.
By adjusting these factors, remarkable control can be exerted over the final product's characteristics.
"Understanding the manufacturing processes is essential for optimizing the performance of foamed polymers in their designated applications."
Physical Properties of Foamed Polymers
The physical properties of foamed polymers are crucial for understanding their functionality and applicability in diverse sectors. Their unique cellular structure not only influences performance characteristics but also determines their suitability for specific uses. These properties include density, thermal insulation, mechanical strength, elasticity, and sound absorption. The interplay of these factors makes foamed polymers highly valued materials in applications ranging from construction to medical devices.
Density and Porosity
Density is one of the primary physical properties affecting foamed polymers. It significantly influences the weight, strength, and insulation qualities of the material. Generally, lower density equates to lighter materials, making them ideal for applications such as packaging and automotive parts, where weight reduction can enhance performance. The relationship between density and porosity is vital; higher porosity can lead to increased thermal insulation properties but may impact mechanical strength.
Foamed polymers with controlled porosity can achieve optimal performance for specific applications, balancing insulation and durability.
Thermal Insulation
Thermal insulation is another key property of foamed polymers. It is particularly important for applications in construction and manufacturing. Foamed polymers provide effective thermal barriers, helping to maintain temperature control in buildings and appliances. Such insulation functionalities contribute to energy efficiency, thereby reducing operational costs in both residential and commercial settings. Materials like expanded polystyrene and polyurethane foams are common examples known for their superior thermal insulating capabilities.
Mechanical Strength and Elasticity
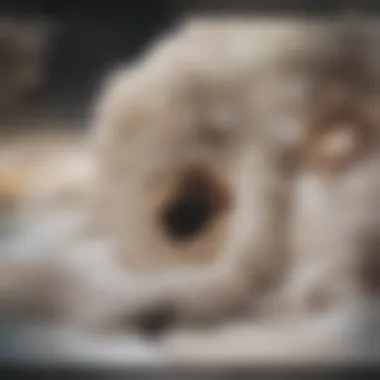
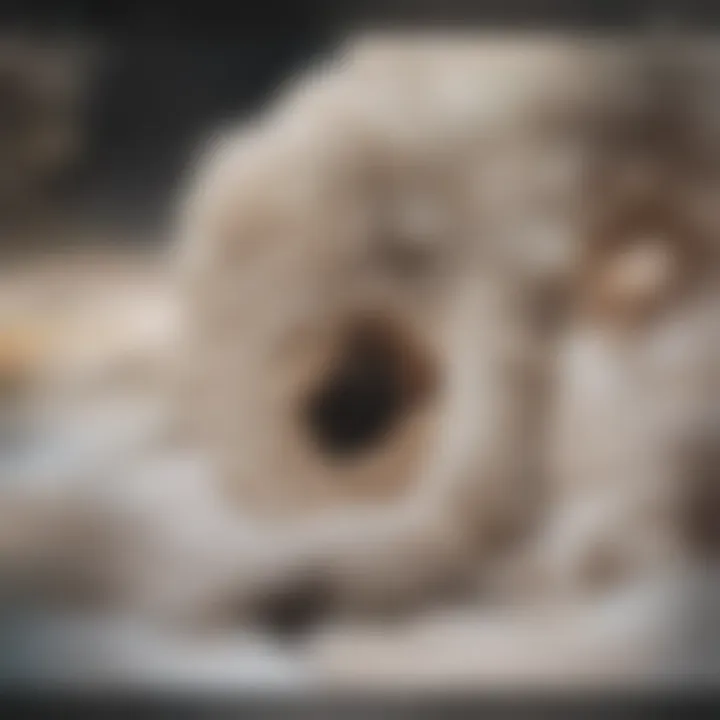
Mechanical strength and elasticity are essential for ensuring that foamed polymers can endure stress without permanent deformation. The foam's cellular structure allows for a degree of flexibility, crucial for applications involving impact absorption, such as in automotive components and protective gear. High mechanical strength combined with good elasticity makes foamed polymers suitable for various demanding environments. Engineering choices must consider these attributes to ensure that the material can perform reliably over its intended lifespan.
Sound Absorption Properties
Sound absorption is an additional important characteristic of foamed polymers, making them beneficial in acoustical applications. The porous structure of these materials allows them to dampen sound waves effectively. This property is particularly valuable in the design of noise control products, including soundproofing panels and automotive interiors. Utilizing foamed polymers for sound absorption enhances user comfort and promotes quieter environments in both residential and commercial applications.
Applications of Foamed Polymers
Foamed polymers have become essential in various sectors, offering unique properties that cater to specific industry needs. Their applications span construction, automotive, packaging, and the medical field. Each sector benefits from the lightweight nature, low thermal conductivity, and versatile mechanical properties of these materials. Understanding these applications highlights the growing relevance of foamed polymers in industrial and daily use environments.
Construction Industry
In the construction industry, foamed polymers are crucial. They are primarily used for insulation, offering superior thermal resistance. Expanded polystyrene (EPS) and extruded polystyrene (XPS) are common choices for wall and roof insulation. Their lightweight composition simplifies transport and installation, reducing labor costs. Additionally, they help to enhance energy efficiency in buildings by minimizing heat loss, which is becoming increasingly important in the fight against climate change.
Moreover, these materials serve as sound barriers. Acoustic foamed polymers absorb sound, making urban environments more livable by reducing noise pollution. Their durability ensures they can withstand harsh environmental conditions, vital in prolonged constructions.
Automotive Sector
Foamed polymers have vital applications in the automotive sector. They are used in vehicle components for insulation and sound deadening. Polyurethane foams are commonly found in seats, dashboards, and headliners. These materials ensure comfort while contributing to the vehicle's safety by absorbing impact energy during collisions.
Furthermore, foamed polymers are integral to lightweighting efforts in vehicle design. By reducing weight without compromising structural integrity, manufacturers can enhance fuel efficiency. This characteristic aligns with stricter environmental regulations and consumer demand for eco-friendly vehicles.
Packaging Solutions
The packaging industry has embraced foamed polymers due to their protective qualities. These materials are lightweight yet provide excellent cushioning for products during transit. Polyethylene and polystyrene foams serve various packaging needs, ranging from electronic devices to fragile items. The ability to absorb shock helps to reduce breakage and improve customer satisfaction through reliable delivery.
Additionally, foamed polymers can be customized for specific uses. Their versatility allows manufacturers to design packaging that fits the product perfectly, minimizing waste. This adaptability, in turn, plays a role in sustainability efforts within the industry as companies seek to reduce excess material usage.
Medical and Healthcare Applications
In the medical sector, foamed polymers play significant roles. They are used in various applications, including prosthetics, orthotics, and surgical cushioning. The softness of polyurethane foams is ideal for comfort, while their durability ensures longevity in use.
Moreover, some foams are designed to be sterilizable, which is crucial in medical settings. The lightweight nature of these materials also assists in creating equipment that is easier for patients and healthcare workers to handle. The use of foamed polymers in medical applications showcases their ability to enhance patient care and comfort.
"Foamed polymers are vital in creating efficient and safe products across multiple industries."
Overall, the variety of applications underscores the significance of foamed polymers in modern industries. Their unique properties not only satisfy current market demands but also position them as key materials in future innovations.
Environmental Considerations
In recent years, the spotlight on environmental impact has become integral to various industries. Foamed polymers, while offering benefits such as insulation and lightweight properties, also present significant sustainability challenges. It is crucial to understand these considerations to promote responsible use and disposal of such materials.
Sustainability Challenges
Foamed polymers often come from non-renewable resources, which raises questions about sustainability. The manufacturing of these materials usually involves processes that consume substantial energy and water. For instance, the production of polystyrene foam can emit harmful substances, impacting air quality. Furthermore, the end-of-life phase for foamed polymers can lead to environmental issues like pollution and increased landfill waste. The challenges include:
- Resource Depletion: Extracting fossil fuels for production can lead to scarcity and ecological damage.
- Carbon Footprint: The energy used in production contributes to greenhouse gas emissions.
- Chemical Waste: Chemical agents used in foam production may not decompose easily, leaving a long-term environmental impact.
Recognizing these challenges is essential for advancing technologies and methods that reduce environmental harm.
Recycling and Waste Management
Effective recycling and waste management strategies for foamed polymers can significantly mitigate their environmental footprint. Many foamed polymers are not accepted in standard recycling programs. However, innovation in recycling processes is crucial for enhancing sustainability. Some important aspects include:
- Enhanced Recycling Techniques: New methods, such as chemical recycling, can break down foamed polymers to their original monomers, making them recyclable.
- Industry Collaboration: Partnerships among manufacturers, recyclers, and policymakers can improve recycling rates and establish better waste strategies.
- Consumer Awareness: Educating consumers about proper disposal and recycling options is critical.
Implementing these strategies can facilitate a circular economy where foamed polymers are reused rather than discarded, ensuring their benefits are harnessed while minimizing environmental impact.
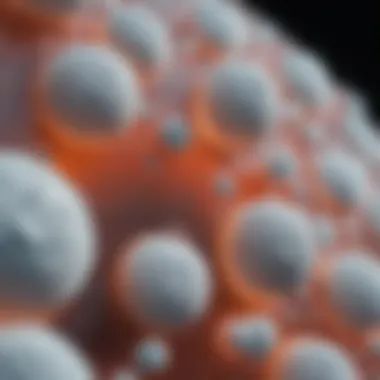
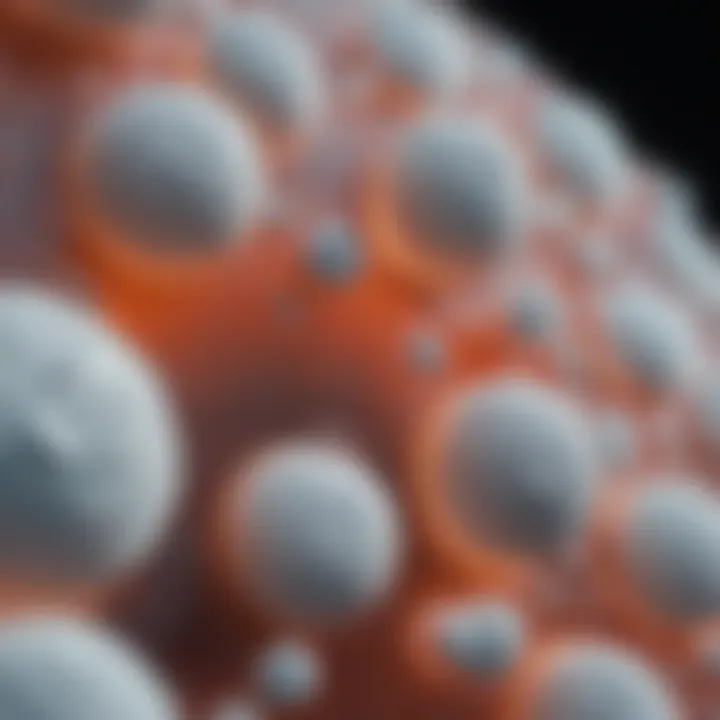
"A comprehensive approach to sustainability involves not only reducing waste but also designing products for longevity and recyclability."
By addressing sustainability challenges and enhancing recycling efforts, the foamed polymer industry can contribute to a sustainable future while fulfilling market needs.
Recent Advancements in Foamed Polymer Technology
Recent advancements in foamed polymer technology play a critical role in enhancing the efficiency and sustainability of these materials. Innovations in manufacturing processes, coupled with improved material properties, have expanded their applications and performance capabilities. Understanding these advancements is essential for students, researchers, and industry professionals who seek to leverage foamed polymers in various fields.
Innovative Manufacturing Techniques
The manufacturing of foamed polymers has seen significant progress in recent years. One major area of innovation includes the development of in-situ foaming. This process allows the foaming and polymerization to occur simultaneously, reducing production time and minimizing energy consumption. Moreover, the use of microcellular foaming techniques has led to lighter foams with enhanced mechanical properties. These advanced manufacturing processes enable the production of foams with controlled cell structures, which can significantly influence the final material properties.
Modern techniques also embrace automation, resulting in increased precision and consistency. Automated foam density distribution has become more feasible, enabling manufacturers to tailor materials for specific applications, such as in automotive parts or insulation materials.
Material Enhancements
Advancements in material science have also impacted foamed polymer technology. The incorporation of nanomaterials into foamed polymer matrices has enhanced properties such as thermal stability and mechanical strength. For example, the addition of graphene or carbon nanotubes can significantly increase the tensile strength of foams while maintaining their lightweight characteristics.
Another notable development is the integration of bio-based additives. These eco-friendly solutions not only improve the sustainability profile of foamed polymers but also enhance biodegradability. As industries increasingly focus on reducing their carbon footprint, these innovations represent a shift toward greener materials.
Innovation Summary: Advances in both manufacturing and material science lead to improvements in property enhancement, performance, and environmental sustainability.
This section highlights how the landscape of foamed polymers is evolving. Stakeholders in various industries must remain cognizant of these advancements to harness the full potential of foamed polymers in future applications. Each innovation not only contributes to improved performance but also enhances the scope of applications in sectors ranging from construction to automotive.
Challenges in Foamed Polymer Performance
The performance of foamed polymers is shaped by various factors that influence their reliability and effectiveness in diverse applications. Understanding these challenges is vital for improving the composition and manufacturing of these materials. Among these issues, durability and aging, along with fire resistance, are crucial considerations. Addressing these concerns can lead to enhanced material longevity and safety, which are paramount in sectors like construction and automotive industries.
Durability and Aging
Durability refers to the ability of foamed polymers to withstand environmental stressors over time. Aging can cause significant changes to their structure, affecting performance attributes. Factors contributing to aging include exposure to UV light, temperature fluctuations, and moisture. Each of these elements can lead to physical and chemical changes in the polymer matrix.
- UV Light Exposure: Prolonged exposure to ultraviolet radiation can cause surface degradation, leading to cracking and color fading.
- Temperature Fluctuations: Thermal cycling can induce expansion and contraction, potentially causing delamination or embrittlement.
- Moisture Absorption: Many foamed polymers can absorb water, which compromises their mechanical properties and thermal insulation efficiency.
Strategies for improving durability include the incorporation of stabilizers that enhance resistance to UV light and the use of coatings that mitigate moisture ingress. Testing methods to simulate aging and evaluate performance can provide valuable insights during the product development phase.
Fire Resistance
Fire resistance is another critical challenge in the realm of foamed polymers. Many applications call for materials that can withstand high temperatures and resist ignition. Traditional foamed polymers are often flammable, posing safety risks in various environments. To improve fire resistance, manufacturers often add flame retardants to the composition. However, the effectiveness of these additives can vary widely.
The choice of flame retardant is essential. Some retardants work by forming a protective char layer when exposed to heat, while others interfere with combustion at a molecular level.
Key considerations for enhancing fire resistance:
- Material Selection: The base polymer's flammability plays a significant role. Selecting inherently flame-retardant polymers can benefit the overall fire resistance of the foam.
- Additives: Flame retardants need to be chosen carefully, considering their potential impact on mechanical properties and environmental safety.
- Testing Standards: Compliance with fire safety regulations is paramount. Various testing methods, such as UL 94 and ASTM E84, ensure that foamed polymers meet necessary fire-resistance criteria.
Understanding and addressing the challenges of durability and fire resistance enhances the potential applications of foamed polymers, making them suitable for various high-performance scenarios.
As research and development continue to evolve, ongoing innovations aim to tackle these challenges, contributing to the advancement of foamed polymer technology.
Epilogue
In examining foamed polymers, we recognize their significance in various sectors, from construction to healthcare. The composition and properties of these materials make them uniquely suited for specific applications, offering advantages that traditional solid materials cannot provide. Understanding the complexities of foamed polymers helps stakeholders make informed decisions regarding selection and usage based on performance characteristics.
Foamed polymers are not just about material properties; they influence design and functionality across multiple industries. As we look to the future, stakeholders must consider not only current applications but also how emerging trends in manufacturing processes and materials science could shape the landscape of foamed polymers.
Future Directions for Research
As the field of foamed polymers evolves, several key areas warrant further investigation:
- Advanced Material Development: Research into bio-based polymers and composites can lead to sustainable foamed options. These materials may present new properties while reducing environmental impact.
- Enhanced Performance Metrics: Understanding the effects of temperature, humidity, and other environmental factors can help improve the longevity and applicability of foamed polymers.
- Recycling Technologies: With sustainability becoming more critical, developing effective recycling methods for foamed polymers could mitigate waste and increase their lifecycle.
- Industry-Specific Innovations: Tailoring foamed polymer formulations for specialized applications could open new market opportunities, particularly in high-performance sectors.
Research in these areas can drive innovation and allow foamed polymers to adapt to evolving industry needs. By addressing current challenges and exploring new possibilities, we can ensure that foamed polymers maintain their essential role in modern applications.