Foamed Rubber: Properties, Applications, Innovations
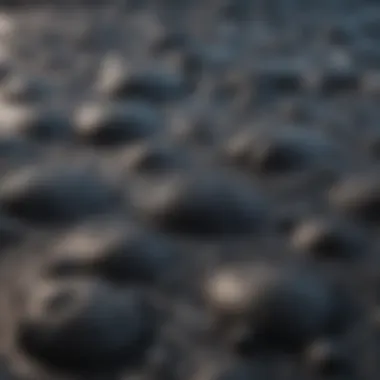
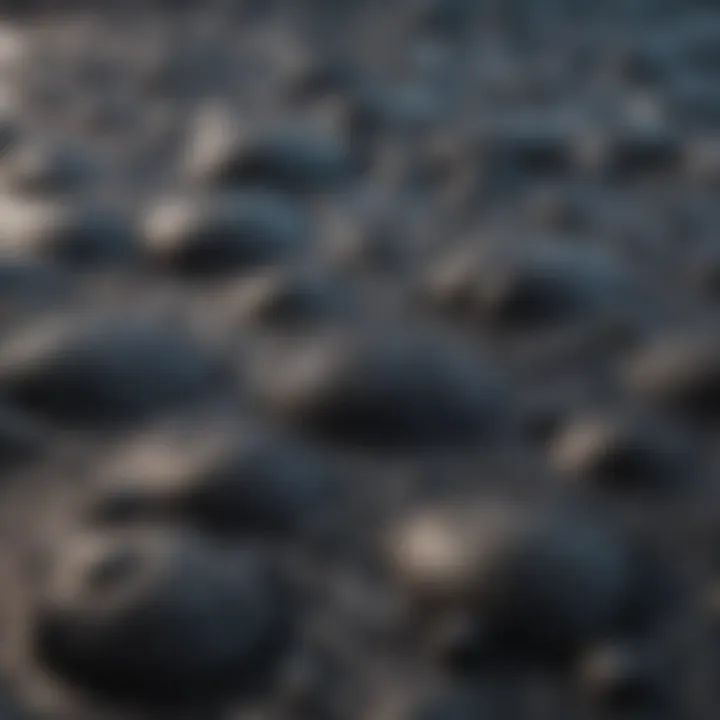
Intro
Foamed rubber stands at the intersection of innovation and functionality, capturing the interest of various sectors from automotive engineering to consumer goods. This material is not just a manufacturing whim; it offers a unique combination of properties that makes it indispensable in todayās marketplace. Lightweight, cushioning, and offering excellent insulation, foamed rubber is a prime choice for applications where versatility and durability are paramount.
The expanding landscape of foamed rubber technology leads us to explore its properties in greater detail. As industries evolve, so too do the expectations placed upon materials. In this article, we aim to highlight the advancements in foamed rubber production and its innovative applications.
As we delve into this subject, it's crucial to understand how these mechanical and thermal properties translate into various practical uses, reshaping the way products are designed and developed.
"Understanding the properties of foamed rubber is not just academic; it informs every decision in product design, ensuring users get the best performance without unnecessary weight."
This narrative will not only dissect the composition and production of foamed rubber but also offer a glimpse into the future with rising trends and environmental considerations. This way, we can appreciate the impact and importance of foamed rubber in our daily lives.
Prelude to Foamed Rubber
Foamed rubber has carved a niche in various industries, prized for its versatile properties and applications. It serves not just as padding or insulation but also as a fundamental element in products ranging from automotive components to consumer goods. With its unique blend of lightweight and cushioning capabilities, foamed rubber is increasingly relevant as manufacturers seek materials that balance performance and sustainability.
The importance of foamed rubber cannot be understated, especially as we delve into the interplay of physics and innovation within this domain. Its role in enhancing product performance while also contributing to energy efficiency in applications is significant. In today's fast-paced industrial landscape, understanding foamed rubber and its characteristics becomes a key advantage.
Definition and Overview
Foamed rubber, in simple terms, refers to a class of materials that have undergone a process to introduce gas bubbles within the rubber matrix, creating a lightweight and compressible foam. These materials typically belong to the category of elastomers, which are known for their elastic properties, allowing them to stretch and deform under pressure, then return to their original shape.
Depending on the production methods and additives used, foamed rubber can be categorized primarily into two types: open-cell and closed-cell. Open-cell foams have interconnected voids that result in a softer texture, ideal for applications like cushioning or sound absorption. In contrast, closed-cell foams have sealed bubbles, making them more suitable for insulation and flotation devices due to their water resistance.
Notably, foamed rubber is produced using various rubbers such as neoprene, silicone, or EPDM, each serving different functional purposes like durability, temperature resistance, and flexibility. The foaming process can involve chemical reactions or physical methods, often depending on the desired properties of the final product.
Historical Development
The journey of foamed rubber is as fascinating as the material itself. It began in the early 20th century, coinciding with the rise of synthetic rubbers. Before this, natural rubber was the predominant type in use, but its limitations in terms of moisture absorption and temperature stability paved the way for innovations in rubber technology.
The significant breakthrough came in the 1930s with the introduction of chemical foaming agents, which allowed manufacturers to create foamed rubber on a larger scale. Companies began experimenting with various formulations, leading to more diverse applications. The post-World War II era saw an uptick in the usage of foamed rubber in automotive and construction sectors, displacing traditional forms of insulation and padding due to its superior properties.
In recent decades, advancements have continued, with an emphasis on environmental sustainability. Innovations in production processes now allow for the creation of biodegradable foamed rubber options, catering to the modern consumer's demand for eco-friendliness.
As industries evolve, so does foamed rubber. Today, students and professionals alike must grasp the history and development of this material to understand its profound impact on modern manufacturing and its potential in future applications.
Characteristics of Foamed Rubber
Foamed rubber stands as a cornerstone material across various industries due to its unique properties. Understanding these characteristics is vital, as they directly influence how foamed rubber is utilized in practical applications. From the automotive sector to consumer products, the physical, mechanical, and acoustic properties tailor its usability, making it a go-to solution for many design challenges. These properties not only determine the effectiveness of foamed rubber in specific roles but also contribute to ongoing innovations in material science.
Physical Properties
Density
Density plays a critical role in the performance and application of foamed rubber. It refers to the mass of rubber per unit volume and can be a decisive factor in choosing the right type of foam for a specific use. A lower density generally means a lighter material, which is advantageous in applications like automotive interiors or portable consumer products. However, while low-density foamed rubber is favored for its lightweight nature, it might compromise on durability under high stress or load. High-density options, on the other hand, provide enhanced structural integrity but add weight.
Unique to density is its ability to influence other properties. A higher density material often offers superior energy absorption, which is particularly desirable in cushioning applications. The challenge lies in balancing weight and resilienceāstriking the right chord in choosing a density based on the intended application.
Elasticity
Elasticity refers to the ability of foamed rubber to return to its original shape after being deformed. This property is key in applications where repeated stress is a regular occurrence, such as in shoe inserts or car seats. The elasticity of foamed rubber allows it to provide comfort and support, absorbing impact while returning to form.
A notable factor in elasticity is the formulation of the foamādifferent blends can result in varying degrees of stretch and recovery. Materials with high elasticity are particularly popular among manufacturers due to their capacity to offer prolonged use without deterioration. However, it also poses a trade-off: highly elastic foams may be less stable under extreme temperature variations, affecting their long-term performance.
Thermal Insulation
Thermal insulation is another significant characteristic of foamed rubber. It effectively prevents the transfer of heat, making it a preferred material in construction and automotive applications where temperature control is essential. Its closed cellular structure inhibits heat conduction, resulting in superior insulation properties.
This property is beneficial in numerous ways: it enhances energy efficiency within buildings and vehicles and contributes to overall comfort. A downfall is that while foamed rubber excels at insulation, it can be sensitive to moisture. Integration of additional treatments or additives may be necessary to enhance moisture resistance in specific scenarios, allowing foamed rubber to thrive in environments it would otherwise struggle in.
Mechanical Properties
Compression Resistance
Compression resistance indicates how well a material can withstand being squished or compressed without permanent deformation. For foamed rubber, this is crucial in applications like automotive seat cushions that undergo frequent pressure. The ideal foam offers enough compression resistance to maintain its form while also being supportive when compressed.
This property allows for durability and enhances comfort factors in various applications. The intricacies of compression resistance depend on the foam's density and formulation. However, more rigid materials can sometimes lead to comfort issues, which necessitates careful selection based on intended use.
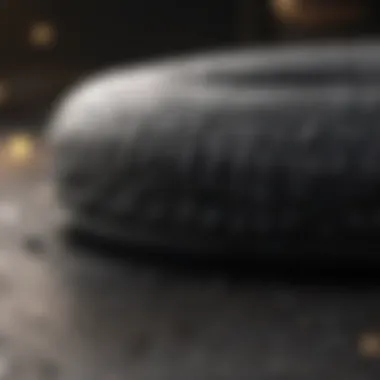
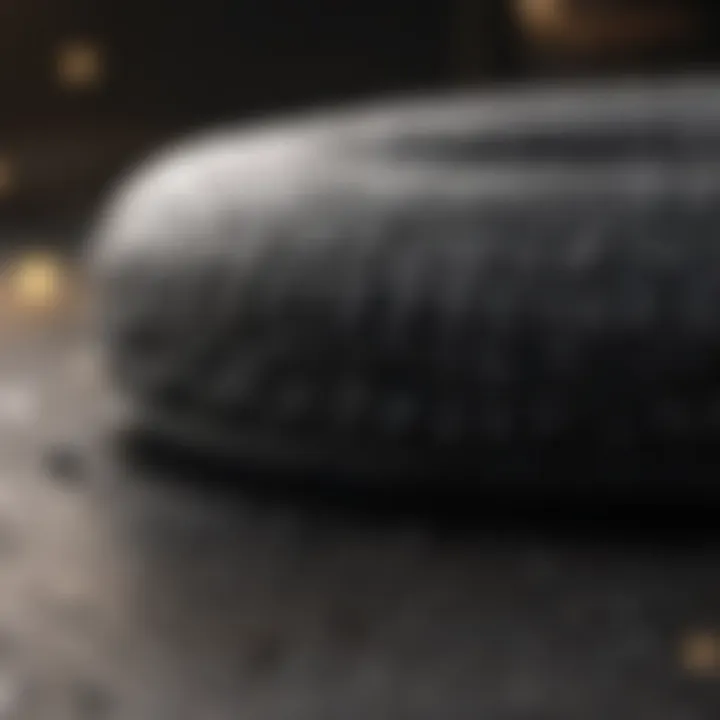
Shear Strength
Shear strength measures a material's ability to resist forces that can cause it to slide or break apart. For foamed rubber, shear strength becomes particularly relevant in applications where the foam must remain intact while subjected to lateral movement or stress. High shear strength ensures longevity and effectiveness in dynamic environments.
This property is important in elements like automotive vibrations and industrial machinery. While achieving high shear strength, manufacturers face a challenge: increasing this strength often leads to increased density, which might negate some lightweight advantages of foamed rubber.
Fatigue Resistance
Fatigue resistance is the ability of foamed rubber to endure repeated loading cycles without significant degradation. This is especially important in applications like sporting goods or components in vehicles, where repeated motions can lead to material failure. A foamed rubber with good fatigue resistance can withstand continuous stress over time while maintaining its performance integrity.
In environments subject to vibration and repetitive loads, fatigue resistance is non-negotiable. It is often achieved through optimized material compositions that allow it to absorb stress without succumbing to wear.
Acoustic Properties
Sound Absorption
Sound absorption refers to a material's ability to reduce sound energy through internal damping. Foamed rubber is particularly effective in this regard, making it an outstanding choice for soundproofing and acoustic applications. Its porous cellular structure captures sound waves, thus minimizing echo and reverberation in spaces like theaters or studios.
This property is advantageous in various commercial settings, as well as in residential designs focused on comfort. An important aspect to keep in mind, however, is that not all foamed rubber maintains consistent sound absorption across different frequencies. Calibration and careful consideration of application need to be applied to ensure optimal performance.
Vibration Dampening
In a world full of vibrationsāfrom machinery to vehiclesāvibration dampening is a considerable advantage of foamed rubber. It allows for effective isolation of vibrations, minimizing their transfer from one surface to another. This feature is leveraged in automotive applications to enhance ride comfort and in machinery to increase longevity and reduce noise.
The unique feature here is the materialās ability to dissipate vibrational energy. However, similar to sound absorption, performance can vary based on the formulation and density of the foamed rubber, which requires some degree of customization for best results.
In summary, the characteristics of foamed rubberāranging from its physical properties like density and elasticity to its mechanical advantages such as compression resistanceāform the basis of its application across diverse sectors. Understanding these properties ensures that the right choices are made for specific needs and challenges in design and manufacturing.
Manufacturing Processes
The section on manufacturing processes serves as a critical backbone for understanding how foamed rubber transforms from raw materials into the versatile products utilized across a multitude of industries. The methods of creating foamed rubber importantly influence its characteristics, such as density, elasticity, and thermal resistance. By examining the distinct processes of expansion and curing techniques alongside molding and shaping methods, we can appreciate the intricate relationships that these procedures have with the final properties of foamed rubber. This deep dive illuminates both the challenges faced by manufacturers and the innovations that continue to broaden the scope of foamed rubber applications.
Expansion and Curing Techniques
This subsection examines how foamed rubber reaches its signature lightweight and insulating characteristics through expansion and curing techniques. These processes not only define the structure but also significantly impact the performance attributes of foamed rubber products, making them suitable for various applications.
Chemical Foaming Agents
Chemical foaming agents play an essential role in the process of creating foamed rubber. They produce gas through a chemical reaction, which causes the material to expand. One key characteristic of chemical foaming agents is their ability to maintain a stable cell structure. This feature is critical because it contributes to the durability and resilience of the final product.
A beneficial aspect of chemical foaming agents is their overwhelming popularity in manufacturing foamed rubber due to their ease of use and precise control over the expansion process. However, chemical foaming agents come with trade-offs; the resultant emissions can pose environmental concerns, particularly if not managed well. Nonetheless, when incorporated properly, they yield a consistently high-quality foam that meets demanding industry standards.
Physical Blowing Agents
Next, physical blowing agents have garnered considerable attention in the manufacturing of foamed rubber. These agents rely on physical changes, like evaporation, rather than chemical reactions to generate gas. A defining feature of physical blowing agents is their cleaner and often more sustainable profile compared to chemical counterparts. As they can be less volatile, they help in producing rubber with fewer harmful byproducts.
Their unique capability to create uniform foam structures without complex chemical interactions makes them a favored option among manufacturers aiming for eco-friendliness. However, the reliance on temperature changes during the manufacturing process can pose challenges in controlling the final density and structure of the foamed rubber, which manufacturers must deftly manage.
Molding and Shaping Methods
Moving beyond the initial expansion, molding and shaping methods further refine the properties of foamed rubber. The choices made in these processes are pivotal in determining the final form and functionality of the product.
Open Cell vs. Closed Cell Manufacturing
The debate between open cell and closed cell foamed rubber manufacturing is substantial. Open cell manufacturing allows air to flow freely through the structure, which enhances breathability and softness; characteristics that make it a mainstay in applications like mattresses and cushions. Its key advantage is comfort, making it appealing to consumers. However, this porous nature reduces its insulation capabilities, often limiting its application in environments requiring substantial thermal resistance.
On the flip side, closed cell manufacturing traps the air within its cells, leading to superior insulation and higher durability. This process lends itself well to various industrial applications, including packaging and construction. Still, the rigidity of closed cell foams can be a drawback in consumer products seeking flexibility and soft touch. It becomes clear that the choice between these methods hinges on the intended use of the final product.
Injection Molding Techniques
Injection molding techniques stand out as a sophisticated method for producing foamed rubber. This process provides manufacturers with precision and efficiency, creating foamed rubber parts with intricate designs and stable structural integrity. One key feature of injection molding is its capacity for high volume production, making it a go-to method in industries where scalability is imperative.
Additionally, injection molding can integrate varying materials in a single piece, enhancing performance through multi-compound features. However, this technique requires significant investment in specialized machinery and molds, leading to higher upfront costs. Itās a balancing act where production efficiency competes against investment return, yet when executed successfully, the benefits can far outweigh the challenges, providing high-quality products to a wide range of markets.
In summary, the manufacturing processes of foamed rubberāthrough careful selection of expansion and shaping methodsāultimately determine its characteristics and suitability for applications, paving the way for innovations and improvements in the field.
Applications of Foamed Rubber
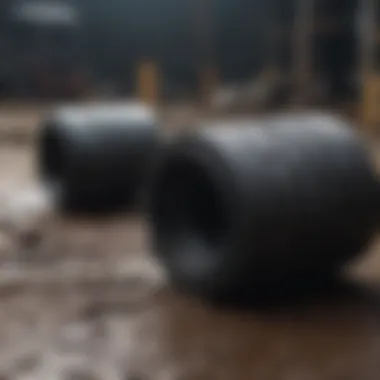
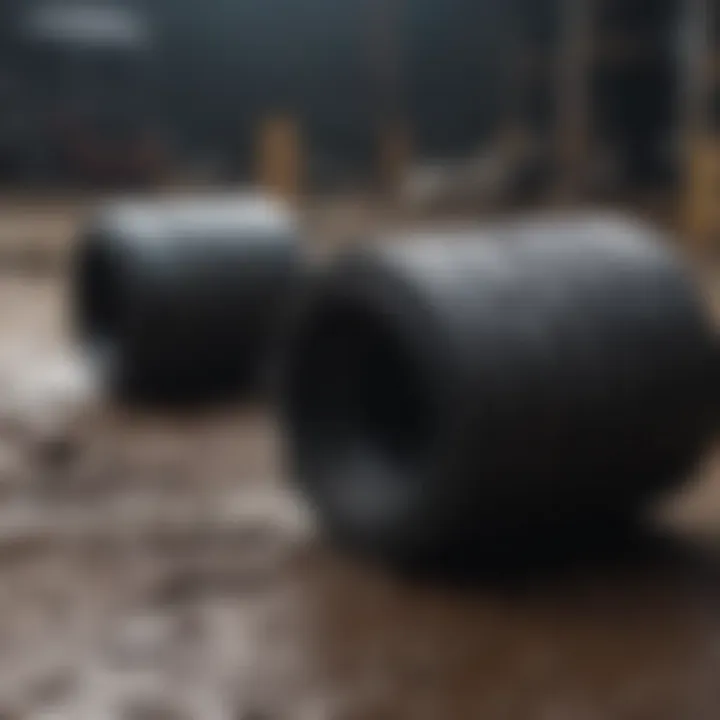
Foamed rubber finds its footing in a wide array of industries, each harnessing its unique properties to meet specific needs. As a flexible and lightweight material, it presents advantages that make it indispensable in many applications. From cushioning solutions in consumer products to sound and vibration control in automobiles, foamed rubber dramatically enhances functionality and comfort. Its versatility allows it to adapt to various environments and requirements, providing a solution tailored for every challenge.
Automotive Industry
Sound Insulation
Sound insulation is one of the standout features of foamed rubber in the automotive sector. The ability to dampen sound waves is crucial for creating a quiet, comfortable driving experience. Foamed rubber acts as a barrier, absorbing vibrations that would otherwise resonate through vehicle panels. This characteristic is not only beneficial for driver comfort but also for safety, as excessive noise can distract drivers.
A unique attribute of foamed rubber sound insulation is its lightweight nature. Traditional sound-proofing materials can add significant weight to vehicles, impacting fuel efficiency. However, foamed rubber strikes a balance, offering effective sound absorption without the bulk. The advantages clearly tilt in favor of foamed rubber, cementing its role as a popular choice among manufacturers.
Vibration Control
Vibration control, another critical application in the automotive industry, relies heavily on foamed rubber. In vehicles, numerous components generate vibrations, which can lead to discomfort and wear over time. Foamed rubber's inherent resilience allows it to absorb and disperse these vibrations efficiently. This reduces wear on both the vehicle and its occupants, contributing to longevity and comfort.
Moreover, the unique structure of foamed rubber can be tailored to specific vibration frequencies, enhancing its efficacy. The material's capacity to manage vibrations not only improves performance but also enhances vehicle handling, making it an attractive solution for auto manufacturers seeking to meet stricter performance criteria.
Construction and Interior Design
Thermal Insulation
In the realm of construction and design, thermal insulation plays a pivotal role in energy efficiency. Foamed rubber excels in this aspect, providing an excellent barrier against heat transfer. Effective thermal insulation contributes significantly to reducing energy costs, making buildings more sustainable.
Foamed rubber is also appreciated for its lightweight quality, as heavy insulation materials can complicate structural integrity. The unique feature here is its adaptability; it can be easily shaped and installed in various applications, from walls to ceilings. However, itās worth noting that while it provides good insulation, proper installation is essential to maximize its benefits, preventing air leaks that can compromise performance.
Cushioning Solutions
Cushioning solutions require a delicate balance of comfort and support, where foamed rubber truly shines. Whether in furniture or acoustic panels, its ability to compress and return to its original shape serves as a natural choice for manufacturers. This cushioning characteristic adds significant value to products, as it enhances comfort without compromising durability.
A key strength of foamed rubber in cushioning is its resistance to wear and tear. Unique formulations enable it to withstand heavy use without losing its properties over time. However, it is essential to consider the density and type of foamed rubber used, as different applications may require varying levels of firmness and flexibility.
Consumer Products
Footwear
When it comes to footwear, foamed rubber is increasingly favored due to its lightweight and cushioning properties. It offers a unique blend of support and comfort, making it ideal for various shoe types, from athletic to casual wear. This characteristic is particularly appealing for long-term wear, where fatigue can be a concern for consumers.
Foamed rubberās ability to mold to the foot provides a customized fit that enhances the walking experience. Its durability ensures that the benefits last through extensive use, though itās vital for manufacturers to balance cushioning with stability, as too much softness can sometimes compromise support.
Mattresses and Pillows
In the sleep industry, foamed rubber remains a sought-after choice for mattresses and pillows. Its adaptability allows it to contour to the bodyās shape, promoting proper spinal alignment and relieving pressure points. This characteristic emphasizes the importance of comfort during sleep, contributing to overall well-being.
Moreover, foamed rubber's resilience contributes to its longevity in this context. However, there can be drawbacks; some users may find it retains heat, which can lead to discomfort during warmer nights. Therefore, incorporating cooling technologies alongside foamed rubber remains a priority for manufacturers aiming to improve their products in this competitive market.
The dynamic nature of foamed rubber scenarios illustrates broad applicability across multiple sectors, each leveraging unique characteristics to enhance product offerings.
In summary, the applications of foamed rubber extend far beyond simple cushioning. Its strategic use in automotive industries for sound insulation and vibration control, as well as in construction for thermal insulation and cushioning, showcases its adaptability. Additionally, in consumer products like footwear and sleep items, foamed rubber significantly impacts user experience through comfort, durability, and performance.
Advancements in Foamed Rubber Technology
The evolution of foamed rubber technology is paramount for both manufacturers and consumers. By adopting innovative materials and methods, this sector continues to thrive while addressing environmental issues and enhancing product performance. The advancements outlined below not only improve the existing properties of foamed rubber but also expand its application possibilities, ultimately leading to a more sustainable and efficient industry.
Innovative Formulations
Biodegradable Foamed Rubber
Biodegradable foamed rubber is a game-changer that tackles the pressing concern of environmental waste associated with traditional rubber products. Made from renewable resources, this type of rubber breaks down more easily in the environment, reducing long-term pollution. Its key characteristic is its ability to decompose under specific conditions, which sets it apart from conventional foamed rubber materials that can take decades to degrade.
This makes it a wise choice for brands aiming for eco-friendliness. One unique feature of biodegradable foamed rubber is its performance during its use phase. It retains essential properties like cushioning and insulation while ensuring that it wonāt linger in landfills. However, a potential downside is that its manufacturing process may still have a higher cost compared to standard foamed rubber, which could deter some manufacturers from adopting this sustainable alternative.
Enhanced Performance Materials
Enhanced performance materials in foamed rubber bring forth superior qualities such as improved durability and strength. This formulation often includes additives that enhance elasticity and resistance to wear, making it an attractive choice for demanding applications. One important trait is its capacity to perform well under extreme conditions, whether itās temperature fluctuations or heavy load-bearing scenarios.
Such materials are gaining popularity for use in sectors that require top-notch elements, like the automotive and construction industries. A specific feature worth noting is the gradient density structure, which allows for tailored support in various applications. While these materials elevate performance, an important consideration is their potential impact on production costs, which might hinder broader adoption.
Recycling and Sustainability Efforts
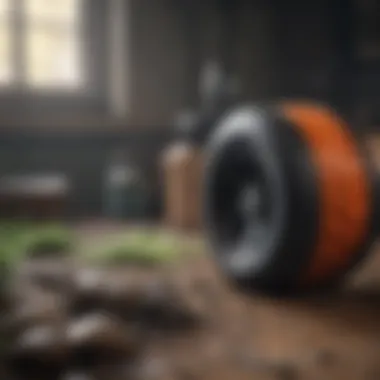
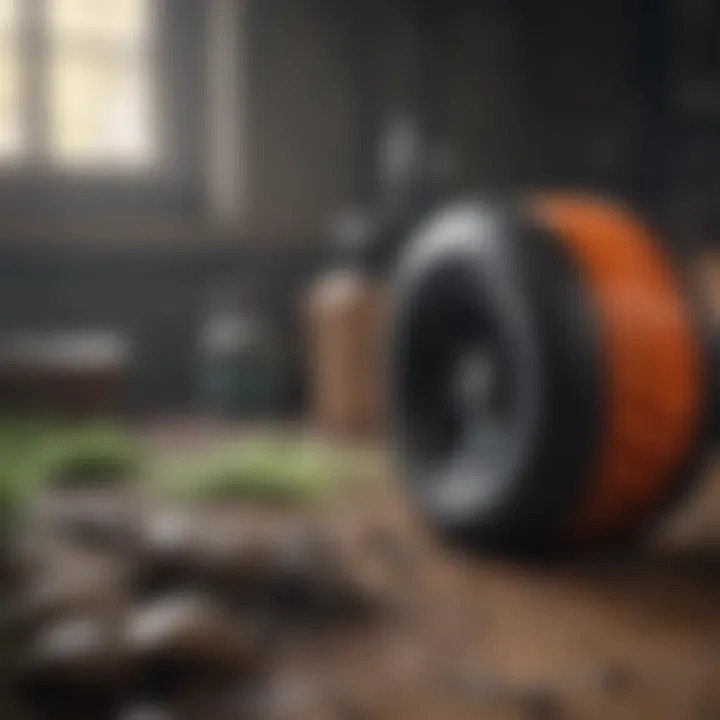
Closed Loop Recycling
Closed loop recycling in the foamed rubber sector streamlines the reclaiming of materials, making it both economically and environmentally viable. In this system, products made from foamed rubber can be recycled and remade into new rubber products, minimizing waste and improving resource efficiency. This is particularly beneficial, as it reduces the reliance on virgin materials and lessens the carbon footprint of production.
An important aspect of closed loop recycling is that it often results in high-quality recycled materials that can compete with new products. Moreover, it encourages a circular economy, fostering a culture of sustainability in manufacturing practice. However, there may be challenges such as ensuring consistent material quality throughout multiple recycling cycles.
Environmental Impact Assessments
Environmental impact assessments (EIAs) are crucial for understanding the effects of foamed rubber manufacturing on the ecosystem. EIAs provide a thorough evaluation of the environmental consequences, guiding businesses in making informed decisions about material sourcing and production practices. The significance of conducting these assessments cannot be overstated, as they help mitigate negative impacts and signal transparency to consumers and regulatory bodies.
One notable advantage of EIAs is their ability to foster innovation; by identifying potential environmental risks, companies are motivated to develop better, greener technologies. Nonetheless, conducting a comprehensive assessment can be resource-intensive, which may deter smaller enterprises from engaging in the process. Ultimately, balancing thoroughness and practicality is key to effectively utilizing EIAs in the growth of foamed rubber technology.
"The advancements in foamed rubber technology remind us that innovation doesn't just include new products, but also sustainable practices that respect our environment."
Through understanding these advancements, stakeholders within the foamed rubber industry can recognize their importance in driving forward sustainable development and performance enhancements crucial to future prospects.
Challenges in the Foamed Rubber Industry
Foamed rubber, while an incredibly versatile material, faces some significant hurdles in its production and application phases. These challenges are not just a minor inconvenience; they can affect everything from cost to reliability in various industries. Understanding these issues is essential for anyone in the field, be they manufacturers, researchers, or even end-users. Addressing these challenges not only helps improve the quality of foamed rubber but also drives innovation and sustainability in the production process.
Supply Chain Issues
The supply chain for foamed rubber is complex and can be a significant bottleneck in the industry. Several factors contribute to this:
- Raw Material Availability: Sourcing high-quality raw materials is crucial. Fluctuations in the availability of materials like latex, chemicals, and other essential components can disrupt production schedules.
- Transportation: Logistics play a vital role. Delays in transportation can lead to increased costs and missed deadlines, especially in industries like automotive and construction where time is often of the essence.
- Supplier Reliability: Dependence on a limited number of suppliers for crucial components poses a risk. Any disruption in those suppliers can lead to widespread production halts.
Furthermore, the introduction of eco-friendly practices and materials affects traditional supply chains, requiring stakeholders to adapt quickly without sacrificing the quality and functionality of foamed rubber products. For instance, the demand for biodegradable options could leave suppliers scrambling to meet standards.
Market Competition
The foamed rubber market is densely populated with competitors, each vying for a slice of the pie. Here are some pivotal aspects to consider:
- Price Wars: Companies often engage in price cuts to attract new clients. This can lead to a race to the bottom, where quality suffers in favor of cost-effectiveness.
- Innovation Pressure: Thereās a pressing need for constant innovation. Businesses must invest significantly in research and development to stay ahead. Failing to do so may result in a loss of market share to competitors who are quicker to adapt to new trends, such as sustainable product offerings.
- Globalization: With a broader international market, local players face stiff competition from overseas companies. Often, these foreign manufacturers can produce foamed rubber at lower costs due to various economic factors, making it challenging for local firms to compete.
"Navigating through market competition is like sailing in choppy waters; one wrong turn can lead to capsizing in a sea of options."
The combination of these factors highlights the challenges within the rubber foam sector, illuminating the need for companies to strategize efficiently. As companies grapple with these hurdles, those that can adapt and innovate are likely to thrive in a competitive landscape.
Future Trends and Prospects
As we navigate the shifting landscapes of technology, society, and environmental priorities, foamed rubber stands at the crossroads of innovation and application. The future trends in foamed rubber are not only pivotal to its ongoing relevance but also reflect broader changes in market demands and sustainable practices. By observing these trends, stakeholders can strategically position themselves to leverage the unique advantages that foamed rubber offers.
Emerging Markets
The global marketplace for foamed rubber is evolving, with emerging markets carving out significant niches. Countries in Asia and South America, for instance, have seen an uptick in infrastructure development projects, which necessitate materials that offer adaptability and performance under pressure.
Moreover, in developed regions like North America and Europe, the demand is increasingly driven by environmentally conscious consumers. New businesses in these markets focus on sustainable solutionsļ¼ prompting manufacturers to explore innovative formulations that minimize waste and enhance recyclability. Consider these factors:
- Urbanization: As cities expand, the need for sound insulation and thermal insulation products in buildings is growing. Foamed rubber's properties suit these applications well.
- Green Initiatives: Companies are more focused on using renewable resources in production, boosting the interest in biodegradable foamed rubber options.
- Consumer Electronics: The uptick in tech gadgets creates a rising demand for lightweight and durable cushioning materials, providing another market for foamed rubber.
These emerging markets not only offer financial opportunities but also contribute to driving forward sustainable practices in manufacturing and product development.
Research and Development Opportunities
With the push for innovation, research and development (R&D) within the foamed rubber industry is expanding rapidly. Firms are now investing in processes that enhance the functionality and sustainability of this material. Here are some critical areas of focus in R&D:
- Performance Enhancements: New formulations aim to improve the physical properties of foamed rubber, such as its temperature resistance and moisture barrier capabilities. This can broaden its usability in diverse environments.
- Sustainability Practices: Initiatives are underway to develop recycling methods that would allow foamed rubber products to re-enter the supply chain, reducing waste and conserving resources.
- Smart Materials: The fusion of foamed rubber with smart technologies presents fascinating possibilities. Research into integrating sensors into foamed rubber can lead to new applications in automotive and construction industries, such as creating adaptive insulation systems.
Investing in R&D not only propels a company's offerings but also fosters an industry mindset that values sustainability and innovation over mere profit.
As we stand at the brink of these advancements, the potential of foamed rubber technology is limitless, promising to shape not just products but entire markets and communities. Engaging with these developments enables scholars, manufacturers, and consumers alike to tap into the vast implications of foamed rubber for the future.
The End
In wrapping up our exploration into foamed rubber, it becomes clear that this material is not just a feature of some tedious engineering textbook; itās alive and buzzing in many industries today. The significance of foamed rubber lies in its multifaceted properties that cater to different needsāfrom cushioning in automotive seats to thermal insulation in buildings. As weāve discussed, the versatility of foamed rubber is astonishing and deeply impacts the efficiency and sustainability of various applications.
Summary of Key Points
To bring everything full circle, here are the key takeaways:
- Unique Properties: Foamed rubber exhibits exceptional density variations, elasticity, thermal insulation, and sound absorption capabilities.
- Varied Applications: It serves critical roles in the automotive, construction, and consumer products industries, each benefiting from its unique qualities.
- Advancements in Technology: Innovations like biodegradable formulations and improved manufacturing techniques are pushing the boundaries of what foamed rubber can do.
- Challenges and Sustainability: The industry faces challenges such as market competition and supply chain issues, yet strives for solutions through recycling and sustainable practices.
Final Thoughts
As technology evolves, so too does the foamed rubber landscape. Future innovations are likely to pave the way for even more sustainable and effective solutions. With increasing awareness about environmental concerns, a shift towards greener materials is not just a possibility but a necessity. The potential of foamed rubber will surely grow, aligning with global efforts for sustainability and efficiency. This promising outlook reinforces the importance of continued research and development in the field, ensuring that foamed rubber will remain a relevant and dynamic player in the material world.