High Voltage Boost Converters: Principles and Applications
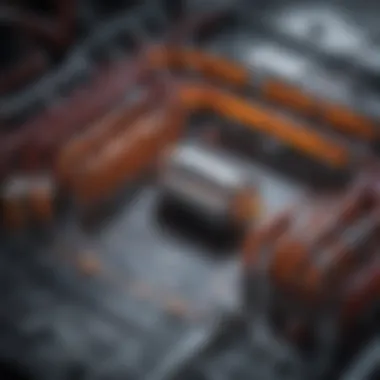

Research Overview
Summary of Key Findings
High voltage boost converters are notable for their ability to transform low input voltages to significantly higher output voltages. This transformation is crucial in various applications, particularly those in renewable energy systems and aerospace technology. The core of these devices revolves around switching elements, inductors, and various control mechanisms that redefine energy transfer efficiency. Notably, challenges remain in optimizing their performance and reliability. Solutions are continuously explored and implemented, pushing the boundaries of current technology.
Background and Context
To understand the critical role high voltage boost converters play, consider the increase in demand for efficient power management in modern electronic systems. As society becomes more reliant on sustainable energy resources, the ability to convert and manipulate power becomes ever more essential. From solar panels generating power for homes to satellites navigating the Earthβs orbit, boost converters assist in achieving the necessary voltage levels for varied functionalities. The intricacies behind their design and operational principles represent a unique blend of electrical engineering and practical application.
Boost converters are not just components; they are the unseen chariots of energy through which innovative technologies ride to the forefront.
Methodology
Experimental Design
In exploring the operational principles of boost converters, one must begin with the understanding of their basic architecture. Primarily, these circuits consist of an inductor, a switch, a diode, and a capacitor. Each of these elements plays a specific role in energy conversion, and the arrangement determines the efficiency and effectiveness of the boost converter. An experimental setup typically involves varying input voltages and loads while measuring output performance to analyze efficiency.
Data Collection Techniques
The data collection process can often employ tools such as oscilloscopes to capture the waveform changes during operation, while multimeters can provide precise voltage and current readings. Advanced control algorithms may also be integrated to assess performance under different operational conditions.
This comprehensive approach reveals insights into the challenges that high voltage boost converters faceβtemperatures, electromagnetic interference, and component wear are crucial factors that can influence the design process. The interplay between theoretical models and empirical data forms the crux of advancing knowledge in this field, ensuring that applications can continue to grow alongside technological innovations.
Preamble to Boost Converters
In the realm of power electronics, boost converters have carved out an essential niche, functioning as pivotal devices that convert low voltage to high voltage. Given the ever-growing demand for efficient energy conversion in various sectors, understanding the underlying principles and functionalities of these converters is not merely academicβit's a necessity. In particular, high voltage boost converters play a notable role in applications ranging from renewable energy systems to medical devices, making their study highly relevant today.
Definition and Function
At its core, a boost converter is a type of DC-DC converter that steps up (increases) the input voltage to a higher output voltage. This transformation is achieved through an ingenious combination of inductors, switches, diodes, and capacitors. When power enters the boost converter, the inductor stores energy during the switch's 'on' period. Once the switch turns off, this stored energy is released, boosting the voltage output. The effective conversion can be defined by the relationship between input and output voltage as dictated by the converterβs duty cycle. This process is crucial for applications where higher voltage levels are required, such as in battery-powered devices or solar energy systems, which increasingly rely on efficient energy management solutions.
Historical Development
The boost converterβs evolution is tied closely with advancements in power electronics. The fundamental concepts date back to the mid-20th century, paralleling developments in semiconductor technology. Early models resembled simple circuits comprising resistors and switches, largely limited in efficacy. As technology advanced, complex control techniques and improved components such as MOSFETs and IGBTs became available. These innovations ushered in higher efficiencies and better performance in various applications.
Today, modern high voltage boost converters integrate sophisticated control systems, allowing for fine-tuning and optimization in real-time. This adaptability has made them indispensable in high-tech industries where precision is vital. The continuous drive for enhanced performance is fueled by researchers and engineers pushing the boundaries of what these devices can achieve in terms of efficiency, reliability, and robustness.
Theoretical Background
Understanding the theoretical background of boost converters is crucial as it lays the groundwork for comprehending how these devices function in various applications. The principles of operation, key components, and mathematical modeling together form an intricate fabric that dictates the performance and efficiency of high voltage boost converters. This section embarks on a journey through these essentials, unveiling their significance and relevance in achieving optimal voltage conversion. A solid grasp of these concepts not only elucidates the working mechanics of boost converters but also primes engineers and researchers to innovate and address challenges in the field.
Basic Principles of Operation
Boost converters operate on the principle of energy storage in inductors to step up voltage levels from a lower input to a higher output. The process involves a switching mechanism that rapidly connects and disconnects the inductor in a manner that allows energy harvesting during the on phase and energy delivery during the off phase. In the simplest terms, when the switch closes, current flows through the inductor, storing energy in its magnetic field. When the switch opens, the inductor releases this stored energy, boosting the voltage at the output.
This fundamental operation is predicated on the law of conservation of energy, where energy cannot be created or destroyed but can be transformed from one form to another. The efficiency of this transformation is influenced by various factors, including the quality of components used and the design of the circuit.
Key Components of Boost Converters
Inductor
The inductor serves as the heart of a boost converter. Its primary role is to store energy in the magnetic field when current flows through it. A significant characteristic of inductors is their ability to resist changes in current, making them an essential part of energy conversion. Typical materials used for inductors include ferrite and iron, contributing to high efficiency.
One unique feature is the inductor's saturation current, which defines the maximum current that can flow without losing its inductive characteristics. Should this current be exceeded, the inductor ceases to operate effectively, leading to inefficiencies. Hence, selecting an inductor with an appropriate saturation current is vital to ensuring robust performance in high voltage applications.
Switching Device
The switching device, often a MOSFET, is another critical component. It facilitates the rapid on/off cycling necessary for energy transfer within the circuit. The key characteristic of the switching device is its switching speed. A fast-switching device can minimize energy losses, promoting efficiency in voltage conversion.
A unique aspect of the switching device is its gate control, which regulates its on-off states. While offering greater control, it can introduce challenges in managing heat dissipation. Proper thermal management is thus essential to maintain the longevity and reliability of the device.
Diode
Diodes are pivotal for ensuring unidirectional current flow, allowing the output voltage to maintain its level post energy release from the inductor. The critical characteristic of a diode is its reverse breakdown voltage, which must exceed the output voltage to prevent failure.
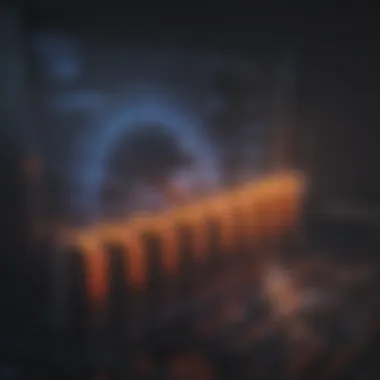
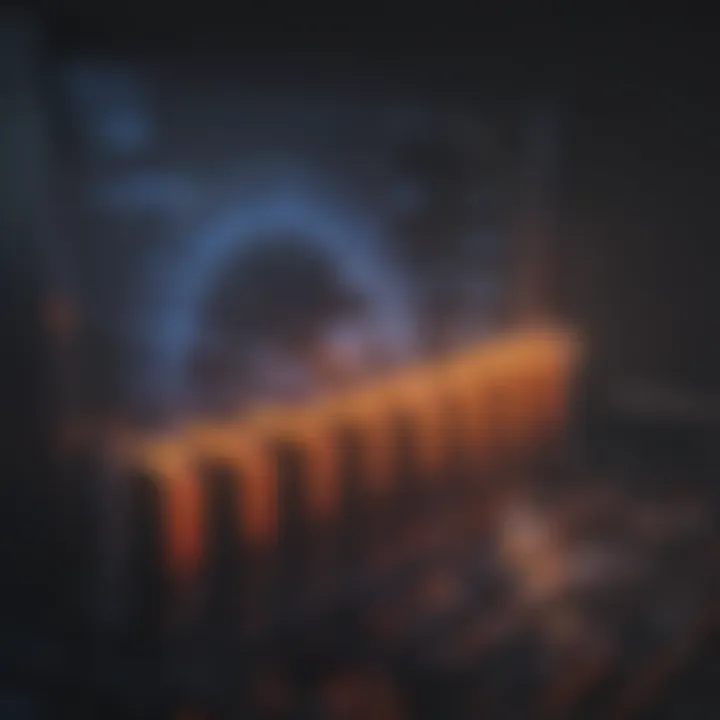
The unique feature of Schottky diodes is their low forward voltage drop, which leads to lesser power losses and marks them as a popular choice in boost converter circuits. However, their relatively lower reverse breakdown voltage can be a limiting factor in high voltage applications.
Capacitor
Capacitors in boost converters smooth out voltage fluctuations at the output. Their primary role is to store energy temporarily and release it when needed, ensuring a stable output. A fundamental characteristic of capacitors is their capacitance value, impacting the amount of energy they can store.
An interesting feature is the Equivalent Series Resistance (ESR), which affects efficiency. A lower ESR means less energy loss during operation, making low-ESR capacitors desirable in high voltage converters. However, cost considerations may sometimes lead to a trade-off between performance and budget.
Mathematical Modeling of Boost Converters
Mathematical modeling acts as the backbone for understanding the dynamic behavior of boost converters. By employing these models, engineers can predict how voltage, current, and power interact within the system. One widely used model is the state-space averaging technique, which simplifies the analysis of switched systems by averaging the state equations over a switching cycle.
The mathematical representation often includes several crucial equations such as the voltage gain equation, which relates input and output voltages. Additionally, system parameters, such as inductor and capacitor values, can be tweaked within the model to simulate various operational conditions, thus aiding in design optimization.
Moreover, the insights gained from these models inform practical implementations, helping engineers to make data-driven decisions to enhance performance and efficiency.
In summary, the theoretical foundations discussed in this section not only provide insight into the operational principles and components but also carve a pathway for innovative design approaches in high voltage boost converters.
High Voltage Considerations
High voltage considerations hold a pivotal role in the functionality and application of boost converters. They directly impact both the design process and the operational safety of electrical systems. It's crucial to unpack various elements surrounding high voltage to appreciate how they shape the behavior of boost converters and their integration in real-world applications. This section discusses the definitions, implications, and necessary regulations that surround high voltage, laying a solid foundation for understanding its significance.
Defining High Voltage in Context
When discussing boost converters, defining what constitutes high voltage can be quite subjective. In general terms, high voltage is often categorized as any voltage over 1,000 volts for alternating current and 1,500 volts for direct current. However, the context matters significantly. For instance, an application in industrial settings may view 1,000 volts differently than in medical or consumer electronics, where even 50 volts could be potentially dangerous. Understanding these definitions is critical, as they inform design parameters and safety measures.
Voltage Conversion Ratios
Voltage conversion ratios are a vital component of boost converters, determining how effectively input voltage is transformed to higher output voltage levels. Such ratios can vary widely based on the specific application. For instance, a solar power system may require significant boosts to convert solar energy into usable electricity. However, compression of voltage isn't simply about ratios; it also ties back to efficiency. High conversion ratios can signal power loss in some applications, making it vital to engage in thorough analysis during the design phase.
"Losing power in the conversion process is like putting money in a leaky bucket. No matter how much you pour in, you wonβt have that much left at the end."
Safety Standards and Regulations
Adhering to safety standards and regulations is non-negotiable in high voltage applications. Regulatory bodies, such as the International Electrotechnical Commission (IEC) and Underwriters Laboratories (UL), establish guidelines to ensure safety and efficiency in designing electrical systems. These standards dictate everything from the materials used in components to the layout of circuits and protective measures required to avoid electrical hazards.
Failing to comply with safety standards can lead to catastrophic failures, which can cause not just damage to equipment but also pose risks to human safety. Therefore, manufacturers must be diligent about current regulations, staying informed about changes that affect high voltage system designs. This involves:
- Regular audits of materials and manufacturing processes
- Continuous compliance checks with regional and global safety mandates
- Utilization of protective devices such as fuses and circuit breakers to prevent overload
By addressing these considerations, engineers can better ensure the robust performance of boost converters operating at high voltage.
Efficiency Metrics
Efficiency metrics are a critical aspect of understanding high voltage boost converters, emphasizing how effectively they convert input voltage to a higher output voltage. These metrics not only determine the performance of the converters but also impact their broader application in various technologies. By analyzing the efficiency, designers and engineers can ensure that the converters operate optimally, ultimately leading to more sustainable and cost-effective solutions.
Efficiency in boost converters typically refers to the ratio of output power to input power, often expressed as a percentage. A high efficiency means that a larger portion of the input energy is converted into useful output energy, while a low efficiency indicates higher energy losses. This aspect holds significance not just from a performance viewpoint but also for applications in renewable energy, where maximizing output is crucial due to resource constraints.
Factors Influencing Efficiency
Several elements influence the overall efficiency of high voltage boost converters. These include:
- Component quality: The materials and components used can significantly affect efficiency. For instance, high-quality diodes and inductors minimize losses, while subpar components can lead to inefficient energy conversion.
- Design topologies: The configuration of the power stage, such as the choice between voltage mode and current mode control, plays a role in achieving better efficiency.
- Load conditions: Operating under different load conditions affects the efficiency; converters may perform optimally under certain loads while struggling under others.
Loss Mechanisms in Boost Converters
Understanding loss mechanisms is key to improving efficiency in boost converters. Losses can generally be grouped into three categories:
Conduction Losses
Conduction losses occur primarily due to the resistance of the components, especially the switching device and diodes when they conduct current. These losses are proportional to the square of the current, meaning that as the load increases, the losses also rise. A significant characteristic of conduction losses is that they can be somewhat mitigated by using components with larger cross-sectional areas or materials that exhibit lower resistivity. This makes them a crucial consideration in the design process, given that reducing conduction losses can lead to substantial efficiency gains. However, using larger or more exotic materials may come with trade-offs in terms of cost and size.
Switching Losses
Switching losses are associated with the transitions of the switching device, including the time taken for the device to turn on and off. These losses can be particularly significant at high frequencies, where each transition creates a brief period of energy loss. The key characteristic of switching losses is that they become more relevant with faster switching speeds, which might be desirable for achieving higher efficiency in some designs. However, this can also introduce concerns regarding electromagnetic interference and thermal management. Developers often need to strike a balance between improved switching characteristics and acceptable loss levels.
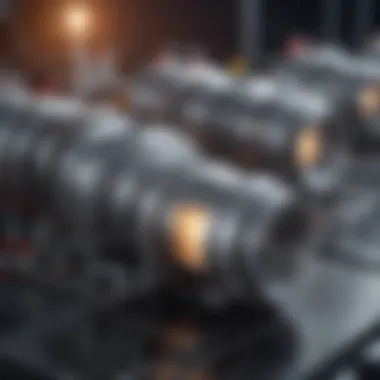
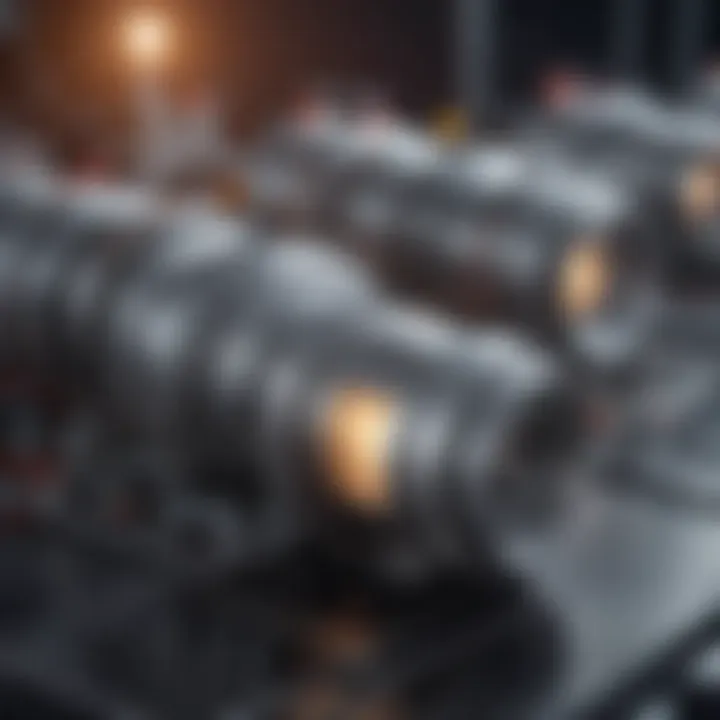
Core Losses
Core losses occur in inductors and transformers and consist mainly of hysteresis and eddy current losses in the magnetic materials. A notable feature of core losses is that they are frequency-dependent, meaning that as the switching frequency increases, these losses can rise as well. This context makes core loss management particularly relevant in high-frequency applications. Using materials like ferrites can help mitigate these losses, although they may also come at a higher cost. This calls for careful selection and sizing of magnetic components to optimize performance.
Techniques for Efficiency Improvement
To enhance the efficiency of high voltage boost converters, several techniques can be employed:
- Optimizing component selection: Choosing components designed for low loss and high efficiency is fundamental. This includes switching devices with low on-resistance and diodes with minimal forward voltage.
- Advanced circuit techniques: Techniques like synchronous rectification, where two switches are used instead of diodes, can drastically reduce conduction losses.
- Thermal management solutions: Proper heat dissipation methods can help all components remain within their optimal operating temperatures, further improving overall performance.
- Control strategies: Implementing adaptive control schemes allows the converter to adjust to changing load conditions in real-time, thus maintaining efficiency across various scenarios.
Applications of High Voltage Boost Converters
High voltage boost converters occupy a central role in numerous technologies and industries. Their ability to convert low voltage to significantly higher voltages makes them indispensable, particularly in applications where maintaining efficiency alongside voltage stability is crucial. The benefits of these converters extend beyond mere power supply; they aid in enhancing the performance of various systems, improving reliability, and facilitating innovative solutions to existing challenges. Letβs dive into four prominent fields where high voltage boost converters shine.
Renewable Energy Systems
In the arena of renewable energy, high voltage boost converters play a pivotal role, particularly in solar power systems. These converters enhance the efficiency of energy conversion from photovoltaic (PV) panels by optimizing the voltage to match grid requirements. When sunlight hits a solar panel, the generated voltage may not be sufficient to power the system directly. A boost converter steps this voltage up, ensuring that even low levels of sunlight can be converted into usable electricity.
- Key Aspects:
- The use of boost converters allows for greater flexibility in system design, accommodating various PV panel configurations.
- They help in maximizing the Maximum Power Point Tracking (MPPT) technology, which adjusts voltage according to environmental conditions to achieve optimum output.
- In wind energy applications, these converters ensure efficient energy transfer from generators to the power grid, even under varying wind speeds.
Aerospace Technology
In aerospace applications, high voltage boost converters contribute to the optimal functioning of electronic systems aboard aircraft and spacecraft. With the increasing reliance on electrical systems for navigation, communication, and control, these converters provide the necessary power levels efficiently.
- Key Aspects:
- Lightweight and compact design is critical in this sector, and boost converters must meet strict weight and size criteria while delivering high outputs.
- They enhance reliability and performance, which is vital for the safety and efficacy of missions. For instance, in satellite technology, converters ensure stable power conversion across various operating conditions.
- Many modern aircraft utilize high voltage systems, where boost converters are employed to power multiple onboard systems, thereby reducing the energy footprint.
Medical Devices
The healthcare sector also benefits remarkably from high voltage boost converters. Many medical devices, such as imaging equipment and portable diagnostic devices, require reliable power sources that can handle a range of input voltages without compromising performance.
- Key Aspects:
- Devices like MRI machines and CT scanners need consistent voltage supplies to function correctly, and boost converters significantly enhance this capability.
- In portable applications, like wearable health monitors, the compact design and efficiency of boost converters allow for extended battery life, ensuring that these devices can operate for longer time periods without interruption.
- Moreover, the ability to adjust voltage levels precisely is crucial in applications where different components may require diverse operating voltages.
Automotive Applications
The automotive industry is rapidly transforming with the implementation of electric and hybrid vehicles, where high voltage boost converters are integral. They ensure that battery power is efficiently converted to drive motors and other electrical systems.
- Key Aspects:
- Boost converters assist in managing the high voltages necessary for electric vehicle (EV) driving systems, enhancing the vehicle's performance.
- They contribute to regenerative braking systems, converting kinetic energy back into usable electrical energy stored in the vehicle's batteries.
- With advancements in battery technology, the demand for versatile and efficient boost converters has grown, making them a focal point of innovation within automotive engineering.
"The demand for high voltage boost converters is only expected to grow as industries push towards efficiency and sustainability in energy use."
Through these examples, it is evident that high voltage boost converters are not just components but are pivotal in driving technological advancements across various sectors. Their versatility and efficiency pave the way for innovation and performance optimization, allowing systems to adapt to dynamic demands and ensuring that industries stay competitive in a rapidly changing landscape.
Challenges in Design and Implementation
Designing and implementing high voltage boost converters can feel like walking a tightrope. The balance between performance, efficiency, and reliability is a delicate endeavor. With advancing technology and increasing applications in fields like renewable energy and aerospace, understanding the challenges associated with boost converters becomes pivotal. Addressing these challenges not only enhances operational capabilities but also fosters innovation in circuit design.
Thermal Management Issues
When it comes to boost converters, managing heat is akin to keeping a tight ship. Higher voltages often lead to increased power losses, especially in the form of heat. This heat can damage components over time, leading to failure and reduced lifespan.
To navigate thermal management, designers must consider several strategies:
- Effective Heat Sinks: Utilizing heat sinks can dissipate heat satisfactorily when paired with suitable materials that improve thermal conductivity.
- Cooling Mechanisms: Active cooling systems such as fans or liquid cooling can be necessary for applications where components operate at a high temperature for extended periods.
- Thermal Simulation Tools: These allow engineers to predict thermal behavior under various conditions, helping in layout optimization.
An understanding of thermal dynamics can ultimately lead to more reliable and efficient designs. Without effective thermal management, a design that works well on paper can quickly fall apart in practice.
Component Selection and Sizing
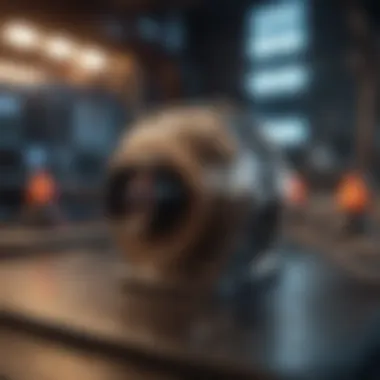
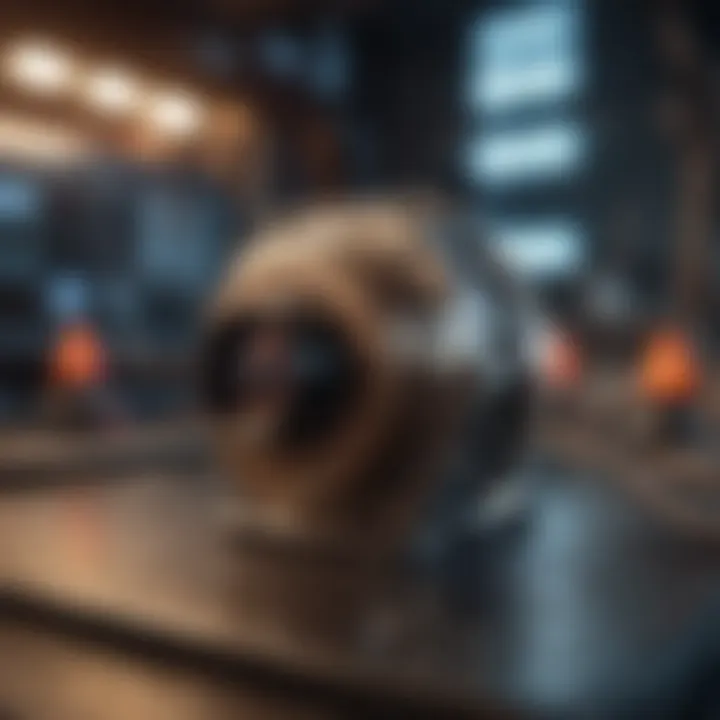
Selecting the right components in a boost converter is a bit like picking the right tools for a job. The wrong choices can lead to inefficiency or failure. Each component, from inductors to capacitors, carries specific characteristics that influence overall performance.
Important factors to consider include:
- Voltage Rating: Every component must exceed the maximum operating voltage to prevent breakdown.
- Current Rating: Components should handle the maximum load fault, which may be different during typical operations compared to sudden spikes.
- Quality and Reliability: Not all components are created equal. Sourcing high-quality parts can save time and money in the long run.
Sizing also holds significance. Components must not only fit physically but also match the circuit requirements. This careful orchestration ensures that the converter performs flawlessly without unexpected behavior.
Reliability and Longevity Challenges
In the world of boost converters, reliability can make or break applications. Components facing high-stress conditions, like automotive or aerospace, need to endure rigorous environments without faltering.
The following are key considerations for enhancing reliability and longevity:
- Derating Components: Using components at lower than their maximum ratings can improve lifespan, as there's less stress on the system.
- Degressive Load Testing: Stress testing under extreme conditions can identify weak points that may fail under real-world demands.
- Regular Maintenance Protocols: Establishing a protocol for scheduled inspection and maintenance helps catch potential issues before they lead to disastrous failures.
By proactively addressing these design and implementation challenges, engineers can significantly bolster the reliability of high voltage boost converters. Building a system that you trust to handle the unpredictable elements of the environment is paramount to technological advancement in various fields.
"In the realm of electronic design, understanding the intricacies of each component and their relationship with natural forces is key to innovation."
Navigating these challenges may seem daunting, yet it can lead to designs that not only meet the current demands but also push the boundaries of what's possible in boost converter technology.
Recent Developments in Boost Converter Technology
Recent advancements in boost converter technology are reshaping the landscape of power electronics, particularly in the realm of high voltage applications. These developments address critical issues such as efficiency, thermal management, and miniaturization, providing the tools necessary for the ever-growing demand for more efficient and compact electronic devices. Key trends underscore the important interplay between research and practical applications, ultimately leading to enhanced performance and reliability in various fields, including renewable energy, automotive systems, and aerospace.
Emerging Research Trends
A surge of activity in research reflects the pressing need for improved boost converters capable of handling higher voltages while maintaining efficiency. Significant areas of focus include:
- Control Algorithms: New algorithms are being developed to optimize the operation of converters under varying load conditions. Optimal control strategies can lead to improved response time and reduced power losses.
- Topological Innovations: Researchers are exploring novel converter topologies that offer greater efficiency and performance at high voltages. For example, the integration of multi-level converters is attracting attention as a means to increase output voltage and reduce harmonics.
- Smart Power Devices: There's ongoing work in smart power semiconductors that can adaptively control their operation. This adaptation enhances switching performance and overall converter efficiency.
These trends not only facilitate advancement but also guide industry players in aligning their product development with emerging technologies.
Innovative Materials and Components
The materials utilized in boost converters profoundly affect their performance. Engineers are investigating new materials that can withstand high voltages while ensuring minimal energy loss and good thermal performance. Some noteworthy advancements include:
- Wide Bandgap Semiconductors: Silicon Carbide (SiC) and Gallium Nitride (GaN) are taking the stage. These materials can handle higher voltages and temperatures than standard silicon-based devices, reducing switching losses significantly.
- Advanced Magnetic Materials: Utilizing nanocrystalline cores in inductors leads to lower core losses, enhancing the overall performance of the converter. These materials can provide better magnetic performance in smaller sizes, which is crucial in compact applications.
- High-Efficiency Capacitors: Innovative dielectric materials are being researched to produce capacitors that can operate reliably at higher voltages while maintaining low Equivalent Series Resistance (ESR).
Innovation in materials promises not just enhanced functionality of existing devices but the ability to develop entirely new applications that were once deemed impractical due to component limitations.
Integration with Advanced Control Systems
The synergy between boost converters and advanced control systems is pivotal in optimizing performance. Integrating smart control technologies fosters better efficiency and functionality in high voltage applications. Key aspects include:
- Digital Control Techniques: The shift from analog to digital control helps in implementing sophisticated algorithms that improve response times and adapt to changing load conditions.
- Real-Time Monitoring: Modern control systems facilitate real-time data analysis, allowing for immediate adjustments to operational parameters, thus enhancing reliability.
- System-Level Optimization: Integrating converters into larger energy management systems enables more effective power distribution and usage. This can result in substantial energy savings across diverse applications.
As the interplay between control systems and boost converters continues to evolve, we can expect a robust future where power systems are not just electronically smart but also greatly efficient.
"The integration of advanced technologies and materials will drive the next evolution in power converter design, unlocking new levels of efficiency and performance."
In summary, the developments in boost converter technology signal a bright future for a range of applications. By focusing on innovative materials, emerging research, and advanced control systems, engineers and researchers are well-equipped to face the challenges presented by the demands of high voltage applications.
Finale and Future Perspectives
High voltage boost converters are pivotal in powering the modern electronic landscape. As technologies progress and demands grow, these converters are stepping up their game. In summarizing the key insights from this article, we recognize the essential role boost converters play across various applications, from renewable energy systems to critical aerospace technologies. Their ability to efficiently step up voltage levels is not simply a technical feat; itβs the linchpin facilitating the integration of clean energy solutions and the advancement of sophisticated electronic devices.
Understanding the innovation trends and the evolving nature of these systems is imperative for researchers and practitioners alike. The increase in operational efficiency and reliability is a constant goal, and it directs much of the recent research efforts. Recognizing these improvements can lead to breakthroughs that enhance the overall functionality of electronic systems. Furthermore, our exploration highlights key challenges like thermal management, which must be addressed to fully leverage the capabilities of boost converters.
"The future of energy systems relies heavily on the advancements in high voltage boost converter technology to meet both performance and sustainability goals."
Summary of Key Points
- Functionality: Boost converters perform the crucial task of increasing voltage levels, serving a foundational role in electronic systems.
- Efficiency: Achieving high efficiency is paramount, as losses can significantly hamper performance. This article provides insights into loss mechanisms and efficiency-improving techniques.
- Applications: Diverse fields such as renewable energy, aerospace, and medical devices showcase how integral boost converters are to practical technology solutions.
- Challenges: Ongoing design and implementation challenges necessitate ongoing innovation, especially concerning thermal management and component reliability.
Future Directions in Research
The research landscape for high voltage boost converters is vibrant, and several directions are gaining traction:
- Advanced Materials: The pursuit of novel materials that can withstand higher voltages and dissipate heat more effectively is crucial. Materials like silicon carbide and gallium nitride are being explored extensively for improvements in switching performance and efficiency.
- Smart Control Systems: Integrating artificial intelligence and machine learning to optimize converter operation in real-time could enhance efficiency and reliability. This is especially vital in dynamic environments like automotive or renewable energy systems, where conditions change rapidly.
- Miniaturization: As electronic devices become smaller and more compact, research into the miniaturization of boost converters without compromising performance is essential. Smaller, lighter converters open avenues for new applications in portable electronics.
- Sustainability Initiatives: The rise of green technologies highlights the need for sustainable practices in converter design. Future research needs to focus on recycling methods for components and energy-efficient manufacturing processes.
In culmination, the journey of high voltage boost converters is just beginning. Embracing innovation and tackling the challenges head-on will ensure their continued relevance in a fast-evolving technological landscape.