Innovations in Laser Micromachining Applications
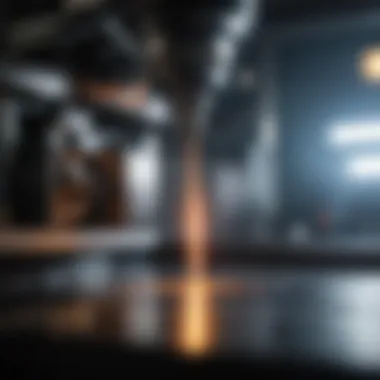
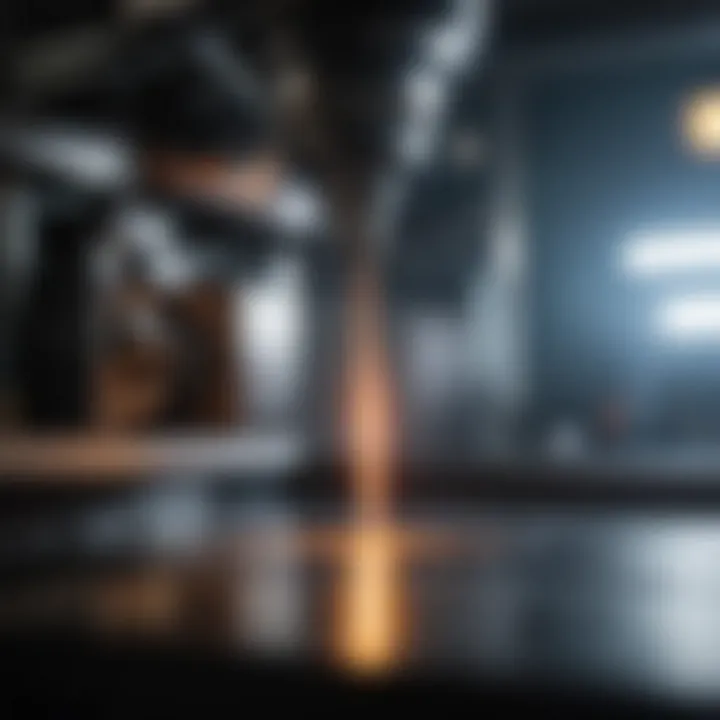
Intro
Laser micromachining represents a pivotal advancement in manufacturing, enabling precise material processing across various industries. This technology has unlocked new possibilities, transforming how components are fabricated, especially in niches where accuracy is critical.
The following sections delve deeply into the intricacies of laser micromachining applications. By examining the fundamental principles and innovative methodologies, we aim to provide a robust understanding of the significant role this technology plays in modern manufacturing.
Research Overview
Summary of Key Findings
The extensive application of laser micromachining techniques reveals several key findings:
- Precision and Accuracy: Laser micromachining allows for the removal of material at the micrometer scale, demonstrating unparalleled accuracy compared to conventional methods.
- Versatility of Applications: The technology is not limited to any single field; it spans electronics, aerospace, biomedical devices, and microfluidics, indicating its adaptability.
- Cost-Effectiveness: Over time, laser micromachining often proves to be more economical for mass production, owing to reduced processing time and material waste.
- Continuous Advancements: The ongoing research in laser technologies, including fiber lasers and ultrafast lasers, enhances the efficiency and capabilities of existing methods.
Background and Context
To appreciate the significance of laser micromachining, it's essential to understand its historical context. The concept of using lasers for industrial applications originated in the 1960s, primarily as a method for cutting metals. Since then, the technology has evolved remarkably. The introduction of high-precision laser systems allowed manufacturers to refine their techniques, leading to applications in microelectronics and within the biomedical field. Today, the spotlight is on optimizing processes to achieve even finer tolerances, something traditional machining methods struggle to replicate.
Methodology
Experimental Design
- Selection of materials, such as polymers, metals, or ceramics, based on their intended use.
- Choosing the appropriate type of laser (e.g., CO2, fiber, or solid state) for achieving desired results.
- Implementing various pulse durations and focusing techniques to evaluate their effects on material response.
Data Collection Techniques
Data collection during such experiments can involve:
- Utilizing high-resolution imaging to assess the quality of machined surfaces.
- Employing laser-induced breakdown spectroscopy to analyze material composition post-machining.
- Analyzing performance metrics like speed, precision, and material yield to draw conclusions about the efficacy of different methods.
"The effective application of laser micromachining not only enhances productivity but also paves the way for innovations. Each advance helps propel industries into the next era of manufacturing."
Intro to Laser Micromachining
The field of laser micromachining has emerged as a significant force in modern manufacturing, transforming how various sectors operate. This technology goes beyond simple cutting; it offers precision and versatility that traditional methods often cannot match. In this section, we delve into what laser micromachining is, and why it plays a pivotal role in today’s high-tech world.
Definition and Importance
Laser micromachining refers to the use of concentrated laser energy to remove material from a workpiece in exceptionally small dimensions. This technique affords an unmatched level of control, making it essential in the production of intricate components where traditional machining methods might fall short.
Some of the core aspects of laser micromachining that underscore its importance includes:
- Precision: The capability to achieve tolerances on the micron scale is invaluable, especially in industries like electronics and biomedical engineering.
- Versatility: It can be applied to a diverse range of materials, from metals to polymers to ceramics, making it adaptable for various applications.
- Efficiency: The speed of production in laser micromachining often surpasses that of conventional techniques, thus reducing lead times and costs.
Despite these advantages, it's essential to know that not all materials are equally amenable to laser micromachining. Understanding the material properties can affect the outcome significantly, which adds a layer of complexity to the process. Nevertheless, the benefits often outweigh the downsides, providing compelling reasons for its adoption across sectors.
Historical Background
The concept of laser micromachining isn’t as new as some might think. The first practical laser was developed in the early 1960s; however, its application in micromachining began to gain traction in the late 20th century. Early adopters recognized the technology's potential for high precision and fine detail, but it wasn't until advancements in laser technology, particularly in the types of lasers available, that its use truly flourished.
Some key milestones in this history include:
- 1970s: The introduction of CO2 lasers brought significant advancements in cutting and engraving materials. They became popular in industrial settings due to their efficiency and effectiveness in working with a variety of substances.
- 1980s: The development of fiber lasers provided a game-changing approach, as they allowed for greater flexibility and ease of use compared to their predecessors.
- 1990s to early 2000s: With the rise of computer-aided design (CAD) technologies, laser micromachining began to see increased integration in manufacturing processes due to its ability to handle complex geometries.
Today, laser micromachining continues to evolve, integrating advancements in optics and software that make it more efficient and user-friendly. As industries face increasingly complex requirements, the history of laser micromachining serves as a testament to its timeless relevance and adaptability.
"The future of manufacturing hinges on our ability to utilize advanced technologies like laser micromachining to meet growing demands for accuracy and efficiency."
In sum, laser micromachining represents not just a method but a critical innovative approach to manufacturing that will shape the future of various industries.
Fundamental Principles of Laser Micromachining
A firm grasp on the fundamental principles of laser micromachining is essential in comprehending its applications and implications in various industries. This section aims to provide a thorough understanding of how laser technology interacts with materials at a microscopic level. Such technologies serve as the backbone for precision machining, making it possible to create intricate designs and structures that traditional methods simply cannot achieve. These principles encompass the science of how lasers ablate, cut, and engrave materials with high precision, while also addressing the advantages offered by different types of lasers employed.
Laser-Material Interaction
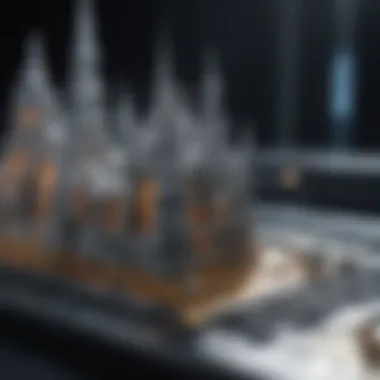
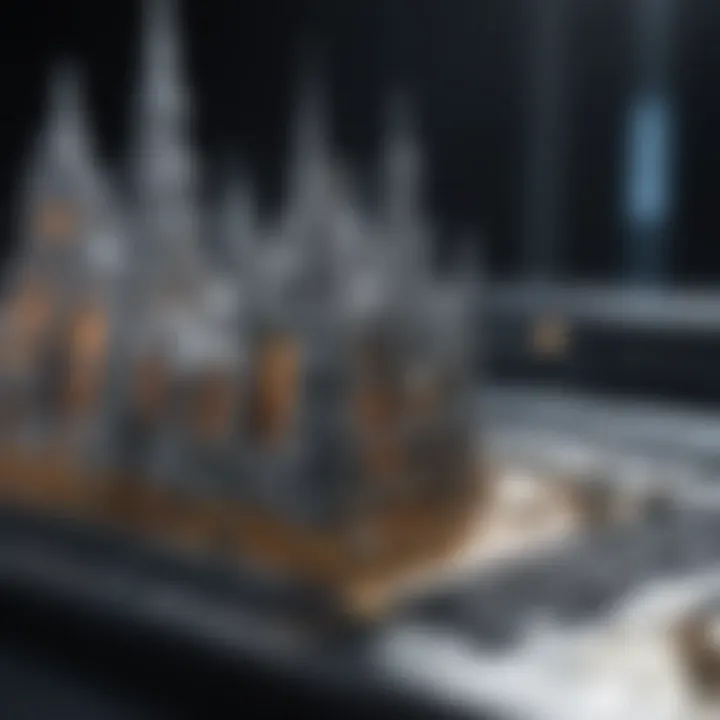
At the heart of laser micromachining lies the interaction between the laser beam and the material being processed. The energy produced by the laser is absorbed by the material, leading to various phenomena—such as thermal excitation and phase change—that dictate how the material will respond. The absorption characteristics of different materials play a critical role in this interaction. Understanding these characteristics allows engineers and researchers to select appropriate laser parameters, such as wavelength, power, and pulse duration, to optimize the machining process.
For instance, when a laser strikes a metal, it often results in melting or vaporization, depending on the intensity and type of laser employed. In contrast, non-metallic materials might undergo a more varied reaction, such as cracking, charring, or even complete vaporization. Consequently, mastering the science behind laser-material interaction not only enhances precision machining but also improves efficiency.
Types of Laser Sources
Different types of laser sources have distinct characteristics that make them suitable for various applications in micromachining. Understanding these types helps in optimizing outcomes depending on the specific task at hand.
CO2 Lasers
CO2 lasers are widely recognized for their utility in cutting and engravings applications. The key characteristic of CO2 lasers is their ability to produce a highly focused beam of infrared light, which efficiently interacts with non-metal materials such as wood, plastic, and glass. One unique feature of CO2 lasers is their adaptability to varying thicknesses of materials.
The substantial advantage of CO2 lasers is their low operational costs and high efficiency compared to other laser types. Their longer wavelength allows for better absorption in organic materials, making them an excellent choice for those specific applications. However, they may fall short in processing metals, where alternative laser sources with shorter wavelengths are preferable.
Fiber Lasers
Fiber lasers stand out due to their compact design and versatility in applications. The main point of attraction for fiber lasers is their ability to deliver a very high output power combined with excellent beam quality. This is thanks to the innovative way they generate laser light, which occurs directly in the optical fiber using doped materials.
One unique feature of fiber lasers is their ability to operate efficiently in harsh environments, making them a beneficial choice for industrial applications. They are particularly popular for metal processing, where their wavelength allows them to penetrate deeper into the material. However, the downside includes a somewhat higher initial setup cost compared to CO2 lasers, which might be a consideration for smaller operations.
Solid-State Lasers
Solid-state lasers are known for their robustness and reliability, contributing significantly to laser micromachining. The key characteristic of solid-state lasers is their ability to produce high-intensity light through a solid gain medium, often resulting in superior brightness. One salient feature of these lasers is their flexibility, as they can be adjusted to produce different wavelengths suitable for diverse machining needs.
The advantages of solid-state lasers include their high efficiency, advanced precision, and lower maintenance requirements over time. Nevertheless, they often require more complex cooling systems due to the heat generated during the lasing process, adding layers of complexity to their use.
In summary, a comprehensive understanding of the fundamental principles of laser micromachining—especially how different laser types interact with materials—forms the foundation for effective application across a range of industries, from electronics to biomedical innovations.
Techniques in Laser Micromachining
Techniques in laser micromachining play a vital role in the realm of precision manufacturing, offering unparalleled levels of accuracy and efficiency across various industries. With the ability to manipulate materials at the micro-level, these techniques enable the creation of intricate components that are essential in today's technologically driven world. Emphasizing the significance of these methodologies helps to illustrate how laser micromachining not only enhances product performance but also drives innovation in manufacturing processes.
The benefits of adopting advanced laser techniques are manifold, including:
- Precision: Achieving finer details that traditional machining cannot deliver.
- Versatility: Application across a wide spectrum of materials ranging from metals to polymers.
- Less Material Waste: Targeted removal reduces excess material, contributing to sustainability efforts.
Additionally, considerations regarding the selection of specific techniques must be taken into account based on the desired outcome. Factors like material properties, thickness, and intended application dictate the choice of method, making an understanding of these techniques essential.
Laser Ablation
Laser ablation is a foundational technique in laser micromachining, characterized by its ability to remove material from a substrate surface through intense laser energy. This method employs high-power laser pulses, which create a plume of vaporized material. One significant aspect of laser ablation is its control over the depth and area of removal, paving the way for intricate pattern engravings and cutting designs in various materials.
Consider the electronics industry; when creating complex circuit patterns, laser ablation allows manufacturers to achieve high precision without causing damage to adjoining components. The process minimizes heat effects, which is crucial in maintaining the integrity of sensitive elements.
"Laser ablation provides the means to directly influence component fidelity, significantly elevating the robustness of electronic devices."
This technique is particularly valuable in microelectronics, where every millimeter counts. What’s also important is the equipment used. Variations in laser sources can influence outcomes; for example, using ultra-short pulse lasers can improve the quality of ablation by reducing thermal damage.
Laser Cutting
Laser cutting stands out for its capability to produce clean and precise cuts in a variety of materials. By focusing high-energy laser beams onto a workpiece, the material reacts, forming a cut due to the intense thermal energy. It’s widely used in industries such as aerospace and automotive, where precision is paramount.
One of the newer advances in this area includes using fiber lasers, which have gained popularity due to their efficiency and ability to cut through thicker materials compared to traditional CO2 lasers. Their operational speed, paired with a narrow kerf width, minimizes material loss, making them attractive for manufacturers focused on reducing waste.
This technique is not just limited to straight cuts; it enables the creation of complex shapes and profiles, which opens up design possibilities.
Laser Drilling
Laser drilling is yet another critical technique in laser micromachining, particularly well-suited for creating micro-holes or intricate patterns. The precision of laser drilling allows for the fabrication of features that are often too small or detailed for conventional drilling methods. This technique plays a crucial role in industries like biomedical device manufacturing, where microscale holes are often required in devices for specific, often life-saving applications.
Furthermore, variances in hole size and shape can be easily accommodated through adjustments in laser parameters, making this technique incredibly adaptable. Notably, applications in the production of implants, where fluid pathways must be engineered, highlight the practical significance of laser drilling technology in the biomedical field.
The continual evolution of these micromachining techniques showcases the potential to integrate even more precision and efficiency into future applications. As these methodologies are refined and tailored, they will undoubtedly pave the way for new innovations and discoveries across all sectors that benefit from laser micromachining.
Applications in Electronics Industry
The electronics industry plays a pivotal role in global technological advancement, with laser micromachining standing out as a game-changer in the precision fabrication of electronic components. From smartphones to sophisticated computing devices, the demand for miniaturization and enhanced performance fuels the need for advanced manufacturing techniques. Laser micromachining serves as the backbone for numerous applications, providing unparalleled accuracy, efficiency, and versatility. By harnessing focused laser beams, manufacturers can achieve intricate designs that are essential in today’s fast-paced tech environment.
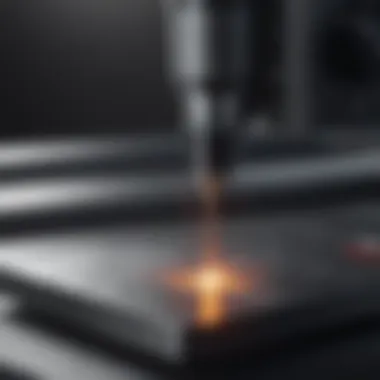
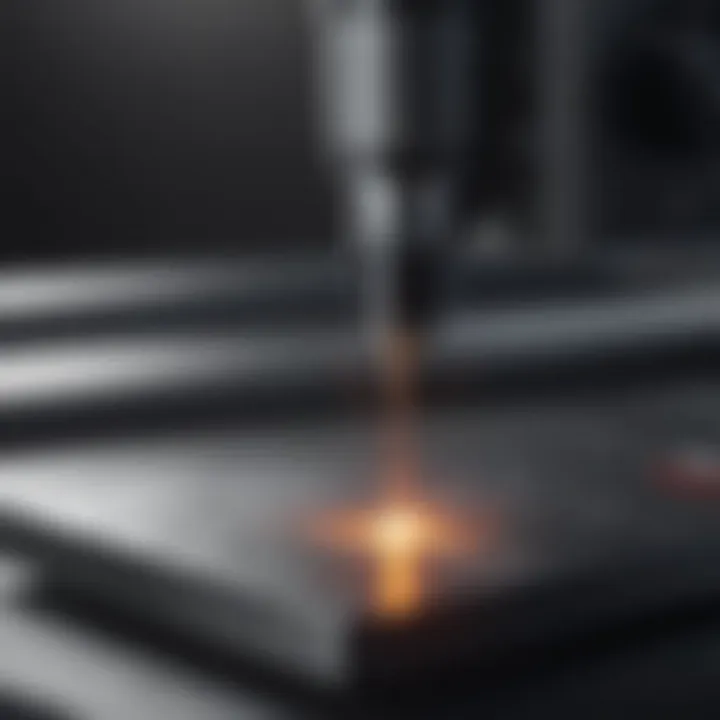
Circuit Board Fabrication
Circuit boards are often considered the heart of electronic devices. The process of circuit board fabrication is a meticulous endeavor requiring high precision. With laser micromachining, manufacturers can produce fine traces and intricate patterns that are vital for circuit functionality. The use of lasers in etching enables the creation of highly detailed designs that traditional methods struggle to achieve.
Key benefits of using laser micromachining in circuit board fabrication include:
- Precision: Lasers can cut through materials with micron-level accuracy, which is crucial for the compact nature of modern electronic devices.
- Reduced Waste: Unlike conventional machining methods that can generate a significant amount of scrap, laser micromachining minimizes material waste, making it a more eco-friendly option.
- Flexibility: Lasers can easily adapt to different materials like FR-4, polyimide and even metals, allowing engineers the freedom to innovate.
Moreover, the ability to process multiple layers simultaneously leads to significant reductions in production time. This rapid fabrication capability aligns perfectly with the industry's demand for shorter lead times and greater cost efficiency, proving that laser micromachining is not just beneficial, but essential.
"Laser micromachining is transforming how circuit boards are made, fundamentally enhancing the manufacturing process with precision and speed." - A thought from industry experts.
Micro-LED Manufacturing
Micro-LED technology represents a significant leap in display technology, competing against traditional LCD and OLED technologies. Micro-LEDs are tiny light-emitting diodes that measure just a few micrometers. Their production requires a high level of precision in the placement and interconnection of millions of tiny chips. Here, laser micromachining proves to be invaluable by providing the ability to handle these delicate components with utmost care.
Some critical aspects of using laser micromachining in micro-LED manufacturing include:
- High Precision Positioning: Lasers ensure the accurate placement necessary for proper functioning of each micro-LED within displays, which is critical for performance and image quality.
- Effective Bonding: Laser technology facilitates the creation of reliable connections between micro-LEDs and peripheral circuitry.
- Scalability: With the rise of consumer demand for larger and more advanced displays, the scalability of laser micromachining makes it an attractive option for production.
Furthermore, the continuous evolution of micro-LEDs into flexible and transparent applications could greatly benefit from ongoing advancements in laser micromachining. As the industry drives toward thinner designs and superior performance, integrating laser technologies could very well define the future of display manufacturing.
In summary, laser micromachining has firmly established its role in the electronics industry. Both in circuit board fabrication and micro-LED manufacturing, the technology not only enhances efficiency and precision but also opens new doors for innovation and sustainability in production processes.
Biomedical Applications
The realm of biomedical applications showcases the pivotal role laser micromachining plays in enhancing medical technologies. This segment dives into the distinct advantages that laser micromachining brings to the table for the healthcare industry. Apart from its precise capabilities, the adaptability of various laser techniques enables the creation of complex structures which are vital in today’s medical domain. As the demand for minimally invasive procedures rises, laser micromachining stands out as a capital technology capable of pushing the boundaries of what is possible.
Microfluidic Devices
Microfluidic devices are often heralded as the future of medical diagnostics and drug delivery systems. These devices integrate small volumes of fluids to carry out diverse biochemical analyses. The precision required at such miniature scales can only be efficiently handled through advanced fabrication techniques. Laser micromachining allows for intricate channel designs and controlled fluid dynamics, which are crucial in applications such as cellular analysis and point-of-care diagnostics.
- Customization: Laser micromachining allows for tailored microfluidic systems based on specific research and clinical requirements. This flexibility means that prototypes can quickly evolve to meet new challenges.
- Material Variety: With the ability to work with various substrates, from polymers to glass, laser techniques accommodate a wide range of applications. For instance, PDMS (Polydimethylsiloxane) and PMMA (Polymethyl methacrylate) are commonly used materials for these devices, and laser micromachining handles their intricacies well.
- Integration with Sensors: Many microfluidic devices have sensors designed to detect biochemical reactions. Laser fabrication can embed these sensors into the micromachined structures, enhancing their functionalities and providing real-time data.
The ability to create precise microchannels through laser techniques transforms medical diagnostics, leading to enhancements in patient outcomes and streamlined processes.
Implantable Devices
The development of implantable devices is another arena where laser micromachining shines brightly. These devices, which range from pacemakers to biosensors, require impeccable precision during fabrication to guarantee safety and functionality.
- Complex Geometries: Implants often feature complex shapes and surfaces designed to interact harmoniously with biological tissues. Laser micromachining supports the creation of these designs without compromising structural integrity.
- Surface Modification: The performance of implantable devices can significantly enhance through tailored surface textures. Laser techniques enable selective area treatment which can improve aspects like biocompatibility, promoting better integration within the body.
- Reduced Production Times: As the market for implantable devices continues to grow, the efficiency in production processes becomes essential. Laser micromachining not only enhances speed but also maintains high standards of quality control.
Ultimately, the interplay between laser micromachining and biomedical applications is paving a promising path toward innovative solutions. By marrying precision with adaptability, these technologies contribute significantly to advancements in healthcare, promising better tools and devices for medical professionals and patients alike.
Challenges in Laser Micromachining
The landscape of laser micromachining is not without its share of hurdles. Understanding these challenges is crucial for anyone looking to grasp the broader implications of this advanced manufacturing technology. Each of the difficulties presented can greatly influence not only the efficiency of the techniques employed but also the overall success of the applications in various sectors. An appreciation of these specific elements can drive innovations that push the boundaries of what's possible in laser micromachining.
Material Limitations
When it comes to laser micromachining, the choice of material can make or break the outcome of a project. Different materials react distinctively to laser light, making some easier to machine than others. For instance, metals like copper and aluminum can absorb laser energy significantly more efficiently compared to plastics or ceramics. This leads to variations in the speed and quality of micromachining processes.
Furthermore, some materials can suffer from heat-affected zones, where the laser's energy alters the material’s properties beyond the immediate area of the cut or drilled hole.
"A laser might slice through metal like hot butter, but that same precision can melt and warp weaker materials if not handled wisely."
Such limitations can turn a straightforward task into a complex challenge where experimentation becomes necessary to identify the right settings and techniques for various materials.
Precision and Accuracy Concerns
Precision is, without doubt, the hallmark of laser micromachining. However, achieving the desired level of accuracy is sometimes a tightrope walk. Factors like beam focus, pulse duration, and energy density come into play, and even the slightest miscalibration can lead to subpar results. The interaction between the laser and materials creates dynamic variables, such as thermal expansion or unintended ablation effects, which can compromise the intended design.
Higher precision demands not only advanced equipment but also skilled operators familiar with the nuances of laser settings. Missteps here can mean more than just a failed project; they can incur significant costs in wasted materials and time.
Often, manufacturers have to implement extensive testing phases to ensure that the laser micromachining processes yield results that meet the required specifications. This can introduce delays, affecting production schedules and making just-in-time manufacturing a bit more challenging.
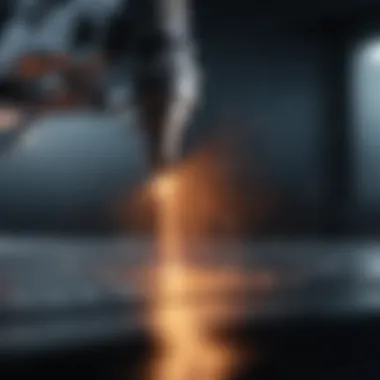
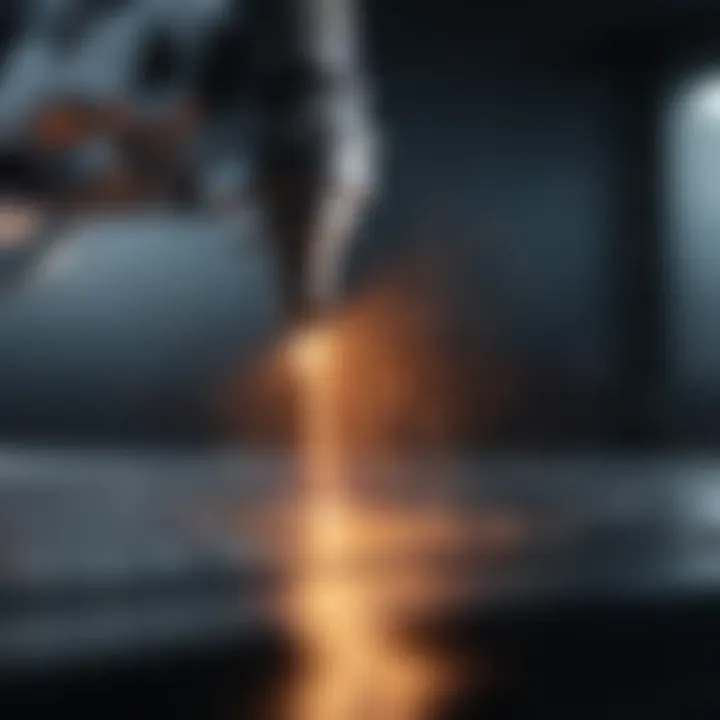
Cost Considerations
While laser micromachining can enhance production efficiency and provide high-quality outputs, the initial investment required can be a sticking point for many companies. The cost of laser systems, maintenance, and skilled workforce adds up quickly, turning what might be perceived as a long-term savings strategy into a short-term financial strain.
Economics also play a role when it comes to the price of raw materials that can influence the feasibility of certain projects. As manufacturers increasingly favor high-quality outputs, they might lean towards pricier materials that are better suited for laser micromachining.
To successfully navigate these challenges, a balance needs to be struck between the initial investments and the potential for increased efficiency and quality. Businesses often weigh these costs against the potential return on investment, which requires comprehensive market analyses and projections.
In summary, the challenges in laser micromachining—be they related to materials, precision accuracy, or costs—are multifaceted and require careful consideration. However, overcoming these hurdles could very well lead to significant advancements in both technology and application across numerous industries.
Innovations in Laser Micromachining
Innovations in laser micromachining are crucial for driving the technological advancements in various industries. As manufacturing processes demand higher precision and efficiency, these innovations play a pivotal role in enhancing performance, reducing waste, and improving overall productivity. The incorporation of cutting-edge techniques not only elevates the standard for manufacturing but also lays the groundwork for future developments.
Adaptive Optics in Laser Systems
Adaptive optics has emerged as a game-changer in laser micromachining. This technique involves using a system of mirrors that can be adjusted in real time to compensate for any optical distortions encountered. The goal here is to enhance the focus of laser beams on the material being processed which, in turn, leads to improved accuracy and resolution.
- Benefits: By achieving better focus, the process allows for intricate designs and features to be executed without compromising on quality.
- Considerations: Implementing adaptive optics can be resource-intensive. It requires sophisticated software and hardware which might not be accessible in every manufacturing plant.
The integration of adaptive optics can significantly refine the ablation process, particularly in microelectronics where miniaturization is the norm.
Real-Time Monitoring Techniques
Real-time monitoring techniques are another innovative aspect of laser micromachining that cannot be overlooked. This method involves continuously observing the machining process while it occurs. Sensors and imaging technologies work in tandem to provide immediate feedback.
- Importance: Real-time monitoring allows for immediate adjustments to be made, ensuring that any variance from the desired output can be corrected on-the-fly. This boosts efficiency and minimizes errors, which is vital in highly sensitive applications such as biomedical device fabrication.
- Tools Used: Various sensors, like laser displacement sensors and high-speed cameras, are utilized to gather data. Methods such as machine learning can analyze this data for better predictive capabilities.
"Incorporating real-time monitoring not only optimizes production processes but also significantly cuts down on material wastage, which is often a major concern in precision manufacturing."
Both adaptive optics and real-time monitoring techniques highlight the depth of innovation in laser micromachining. They illustrate how technology is not just evolving but is also adapting to meet the rigorous demands of modern manufacturing environments. By understanding and leveraging these innovations, industries can achieve unprecedented levels of precision and efficiency.
Future Directions in Laser Micromachining
As we look ahead, the field of laser micromachining stands to gain immensely from innovations and advancements in technology. This section delves into the emerging trends that are shaping the future landscape of micromachining, offering a glimpse into what industries and researchers can expect. The ability to revolutionize manufacturing processes is deeply tied to ongoing developments, underscoring laser micromachining’s pivotal role in modern production.
Emerging Technologies
Emerging technologies in laser micromachining offer not only enhanced capabilities but also promise to meet the increasing demand for precision and efficiency in manufacturing. Several noteworthy advancements are currently making waves:
- Ultrafast Lasers: With pulse widths in the picosecond (trillionth of a second) or femtosecond (quadrillionth of a second) range, ultrafast lasers allow for precision micromachining without generating significant heat. This minimizes thermal damage to the workpiece, making it ideal for sensitive materials commonly found in the electronics and biomedical fields.
- High-Throughput Laser Systems: These systems combine multiple laser sources, drastically increasing production efficiency. They can process several parts simultaneously or perform multiple operations in a single pass. This means reduced cycle times in manufacturing, ultimately leading to cost savings.
- Artificial Intelligence Integration: The integration of AI algorithms into laser micromachining systems is revolutionizing the way we approach design and manufacturing. By utilizing machine learning, systems can adapt in real-time, optimizing the laser parameters and machining strategies based on feedback from the material characteristics and desired outcome.
These trends suggest that laser micromachining will not only enhance existing applications but also enable entirely new possibilities. As these technologies mature, we expect to see a broader adaptation across various sectors.
Sustainable Practices in Manufacturing
Sustainability is no longer a buzzword; it’s now a global requirement. The era of manufacturing that disregards environmental impacts is coming to an end, and laser micromachining is in a unique position to advance sustainable practices in production processes. Here’s how:
- Reduction in Material Waste: Compared to traditional machining methods, laser micromachining is inherently more material-efficient. The precision of laser systems minimizes waste generated during production. This precision is critical, especially in industries where materials are costly and must be used judiciously.
- Energy Efficiency: Lasers tend to consume less energy than conventional machining processes, especially when considering the rapid processing capabilities. Technology like fiber lasers has proven to be particularly energy-efficient while providing high-quality results.
- Pollution Management: With advancements in filtration and laser processing systems, the generation of hazardous emissions can also be greatly reduced. By minimizing the creation of fumes and debris, manufacturers contribute to a cleaner environment.
“Manufacturing processes are evolving towards greener alternatives. Laser micromachining can reduce waste and enhance energy efficiency, heralding a new era of sustainable production.”
As we venture into the future of laser micromachining, it is clear that its potential in revolutionizing production is immense. The confluence of emerging technologies and sustainable practices will not only satisfy market demands but also pave the way for a more responsible and environmentally conscious manufacturing landscape.
Culmination
The conclusion serves as a pivotal segment in any article, especially when discussing nuanced topics such as laser micromachining. It provides a solid wrap-up, reinforcing the significance of the subject matter, while also inviting further contemplation. In this case, the relevance nearly shouts through the detailed exploration of laser micromachining applications across varied domains. The intricate dance of technology and methodology involved in this field benefits industries ranging from electronics to biomedical applications.
Summary of Key Points
A fundamental objective of this article was to lift the veil on laser micromachining, shedding light on its importance and multitude of uses. Key points addressed include:
- The versatility of laser micromachining: The technology is applied not just in crafting electronic circuits but also plays a vital role in developing cutting-edge medical devices.
- Principles of operation: Understanding how different laser types interact with materials allows professionals to optimize processes for specific applications.
- Innovations driving the field: The incorporation of advanced practices, such as adaptive optics, enhances precision and flexibility in manufacturing processes.
- Challenges faced by the industry: These range from material limitations to cost concerns, which practitioners must navigate to fully leverage the technology.
Having dissected these points, it’s clear that the ongoing evolution of laser micromachining comes with its share of complexities and potential.
Final Thoughts on Future Prospects
Looking ahead, it is apparent that laser micromachining stands on the precipice of groundbreaking advancements. Emerging technologies promise to further refine this already precise technique. Notably, there is room for improvement in sustainable practices, balancing efficiency with environmental considerations. Innovations in machine learning and AI could lead to smarter, more adaptive micromachining processes that anticipate equipment failings or material behavior before they become issues. Each advancement propels the technology further, paving the way for applications yet to be imagined.
The value of laser micromachining is not just in its current applications but in what it foreshadows for tomorrow's manufacturing landscape. As the industry evolves, maintaining a sword’s edge between innovation and practical application will prove essential for educators, researchers, and professionals alike. The future indeed holds exciting prospects for those invested in this transformative technology.
"As we stand at the threshold of innovation, the only limit to what we can achieve is the breadth of our imagination."