An In-Depth Exploration of Nitrile Rubber Compounds
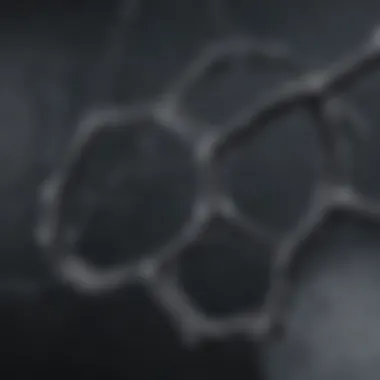
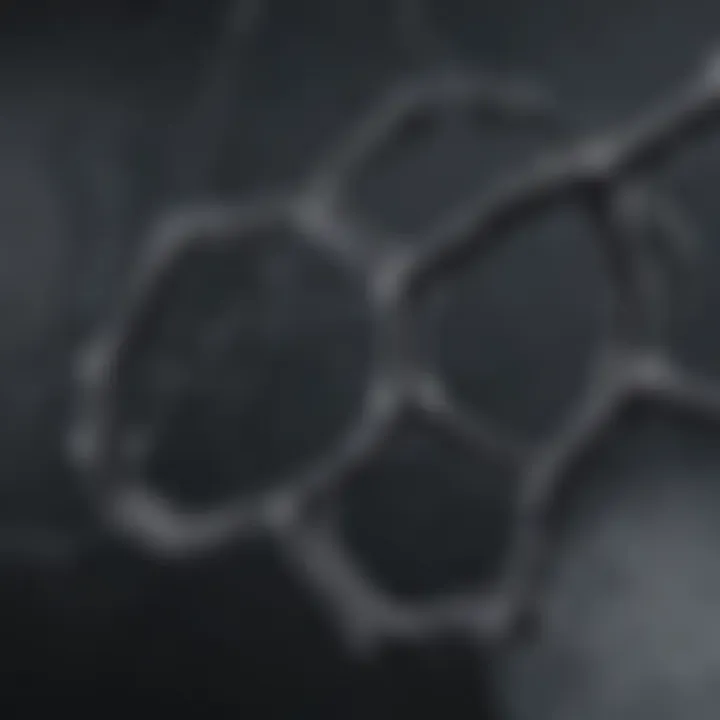
Intro
Nitrile rubber compounds have carved a niche for themselves across a variety of industries, thanks to their remarkable properties. When one considers the realms of automotive, aerospace, or even medical manufacturing, the presence of nitrile rubber is often a cornerstone in design and utility. With its ability to withstand oil, chemicals, and elevated temperatures, it’s no wonder that this material has gained serious traction over the years.
Often referred to as NBR (nitrile butadiene rubber), this synthetic elastomer showcases exceptional resilience and durability. The chemical structure plays a significant role in this character, allowing it to maintain flexibility in conditions where other materials might falter.
As we dive deeper, the article aims to unravel not just the inherent qualities of these compounds, but also their manufacturing processes. Insights into how these versatile materials are produced will enrich our understanding. Furthermore, exploring their widespread applications will highlight their importance in various sectors.
Research Overview
Summary of Key Findings
- Chemical Resistance: Nitrile rubber's resistance to various chemicals is unmatched, particularly in oil-heavy environments.
- Heat Tolerance: Withstanding higher temperatures compared to many traditional rubber types gives nitrile rubber a distinct advantage in multiple applications.
- Diverse Applications: Used in automotive seals, gaskets, and medical gloves, its versatility cannot be overstated.
Background and Context
The journey of nitrile rubber started during the early 20th century when the need for synthetic materials overtook natural resources. In an era where durability was paramount, especially with the rise of automobiles and machinery, nitrile rubber quickly emerged as a practical solution. Initially developed for industrial applications, its adaptability paved the way for it to seep into other sectors. The 1930s marked a pivotal point when researchers realized the potential of combining butadiene with acrylonitrile. This combination resulted in the formation of elastomers that exhibited extraordinary performance characteristics.
As the years progressed, industries began to recognize that natural rubber often fell short in applications where exposure to oils and chemicals was a concern. Thus, nitrile rubber became indispensable, bridged the gap, and remains continuously evolving in its applications.
In summary, the understanding of nitrile rubber compounds is crucial for anyone looking to grasp the materials that shape our modern world. Whether it’s in automotive assembly or healthcare tools, the complexities add layers of appreciation for these compounds that often go unnoticed.
Preamble to Nitrile Rubber Compounds
Nitrile rubber compounds serve an essential role in modern industry, particularly in sectors that rely heavily on materials that can withstand harsh conditions. The significance of nitrile rubber cannot be overstated; its unique attributes make it a go-to solution for many applications. Understanding this material allows us to appreciate its multifaceted benefits, considerations in usage, and how it has shaped various industries.
The importance of this topic extends beyond its basic definitions and properties. It involves a thorough examination of the chemical makeup of nitrile rubber, its historical developments, and its applications across various fields. Manufacturers lean on nitrile rubber for its remarkable resistance to oils and chemicals, which are commonplace in everyday industrial operations. Furthermore, the versatility of these compounds opens doors to innovations that can enhance productivity, safety, and sustainability.
This comprehensive exploration will aim to equip students, researchers, and professionals with a deep understanding of nitrile rubber compounds, paving the way for advanced applications and better material selections in their respective fields.
Definition and Overview
Nitrile rubber, also known as acrylonitrile-butadiene rubber (NBR), is a synthetic rubber copolymer of acrylonitrile and butadiene. It offers a balance of desirable properties such as notable resistance to fuels, oils, and harsh chemicals, which makes it invaluable in various applications ranging from automotive components to medical gloves. Nitrile rubber exhibits elasticity and tensile strength, ensuring that products made from it can maintain functionality under stress.
The formulation of nitrile rubber can be tailored, altering its properties to meet specific requirements. This aspect means complex designs can achieve both cost-effectiveness and high performance, making it attractive to manufacturers around the globe.
Historical Context
The history of nitrile rubber traces back to the late 1930s when the first samples were produced. The initial development stemmed from the need for materials that could withstand oil and fuel, particularly during World War II. Engineers sought alternatives to natural rubber, which often succumbed to degrading factors like heat and chemicals. The Army's demand led to advancements in synthetic rubber technologies which endeavored to meet the rigorous requirements of warfare and industry.
The post-war boom propelled nitrile rubber into the civilian market, witnessing its use expand into sectors such as automotive, aerospace, and even medical applications. Over time, its formulation evolved, adapting to the growing demands for durability and resilience across diverse climates and conditions. The adaptability of nitrile rubber compounds can be linked directly to its ongoing relevance in industrial production today.
"Nitrile rubber has positioned itself as a linchpin in multiple industries, driven by both necessity and innovation."
The journey of nitrile rubber compounds tells a story of resilience and progression, embodying the spirit of continuous improvement in material sciences.
Chemical Structure of Nitrile Rubber
Understanding the chemical structure of nitrile rubber is akin to unraveling the very fabric that gives this material its unique properties. At its core, the structure determines how nitrile rubber behaves under various conditions, impacting its applications and performance. The specific arrangement of atoms within nitrile rubber enables it to excel in challenging environments, particularly with respect to heat and chemical exposure. Thus, a grasp of its chemical structure isn't just a technical detail; it's essential for anyone working within industries that rely on this versatile material.
Monomers and Polymerization Process
Nitrile rubber is primarily synthesized from a specific mixture of monomers, the most common being acrylonitrile and butadiene. The proportion of these monomers significantly influences the final properties of the rubber. After all, not every rubber is created equal; a higher acrylonitrile content provides enhanced resistance to oils and fuels, while increased butadiene content improves elasticity and low-temperature flexibility.
The polymerization process, where these monomers unite, typically occurs through a process called emulsion polymerization. This technique suspends the monomers in water, using a surfactant to stabilize the emulsion. As the reaction progresses, polymer chains, which are long strings of repeating units, start forming. This process is crucial since it dictates not only the molecular weight of the final product but also the cross-link density, which relates directly to the rubber’s performance characteristics.
"The choice of monomers and the details of the polymerization process craft the distinct personality of nitrile rubber."
These chains can vary greatly, ranging from a few hundred to several thousand repeating units long. This variation influences the mechanical properties, such as tensile strength and elongation at break, making it vital for engineers to select the right conditions during synthesis.
Cross-Linking Mechanisms
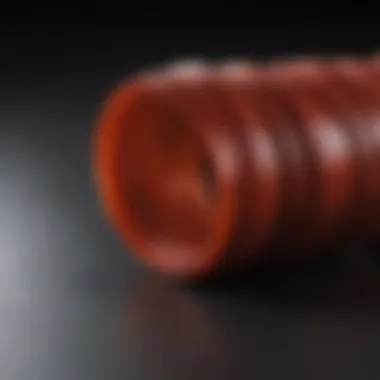
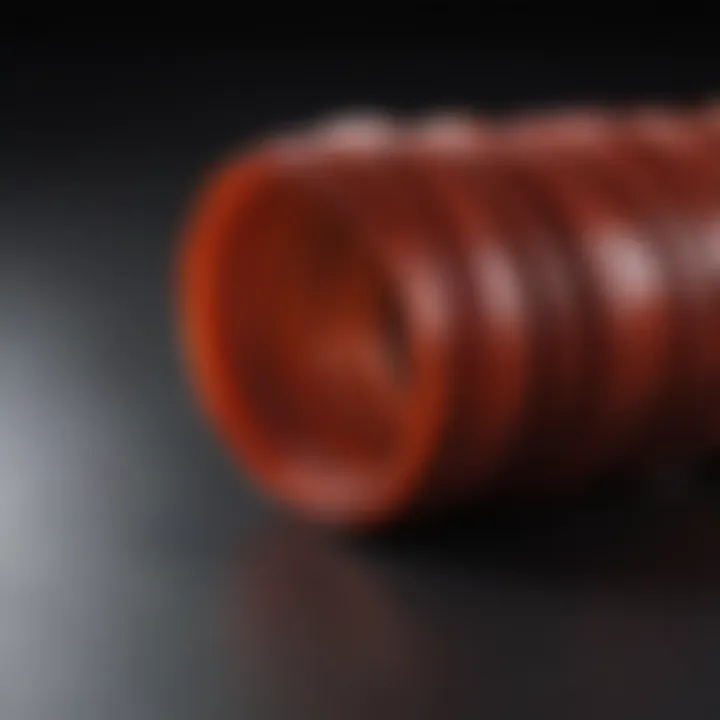
Cross-linking is the process that transforms the polymer chains into a more rigid and durable structure. For nitrile rubber, this is often achieved through the addition of curing agents during its manufacturing phase. The most common agent used is sulfur, which creates bridges between the polymer chains. This cross-linking is fundamental, as it enhances the rubber's strength and resilience.
Several methods to achieve cross-linking exist, including:
- Heat curing: Involves heating the rubber with sulfur to promote cross-linking. This is a traditional method that can produce reliable and strong rubber products.
- Radiation curing: Utilizes electron beams or ultraviolet light to induce cross-linking. This method can be more environmentally friendly and often results in shorter curing times.
- Chemical curing: Other compounds, like peroxides, might also be used to achieve cross-linking through chemical reactions at lower temperatures.
Depending on the chosen method, the final properties of nitrile rubber may vary, determining its suitability for specific applications. Overall, understanding cross-linking mechanisms allows engineers to harness the full potential of nitrile rubber compounds, optimizing them for everything from automotive seals to medical devices.
Properties of Nitrile Rubber Compounds
The notion of nitrile rubber compounds extends beyond mere material description; it envelops a variety of physical properties, chemical resistance, and thermal stability that make these materials remarkably resilient. Understanding these attributes is crucial not just for material scientists but also for industry professionals who rely on these compounds in their products. As such, this section aims to delve into the specifics of nitrile rubber properties, providing insights that highlight their significance in various applications.
Physical Properties
Nitrile rubber compounds are marked by their innate resilience and strength. This durability plays a pivotal role in many applications where mechanical stress and abrasion are common. (Think of car parts that face relentless wear.) Below are some key physical properties:
- Tensile Strength: This measures how much force a material can withstand when being pulled. Nitrile rubber boasts impressive tensile strength, allowing it to maintain integrity under strenuous conditions.
- Elongation at Break: It defines the extent to which nitrile rubber can stretch before failing. High elongation rates mean that the material won't just snap under pressure; instead, it gives way gradually.
- Hardness: Nitrile compounds can be engineered to varying durometers, which helps in tailoring them to specific application needs. A harder rubber might be suitable for seals, while something more flexible could be ideal for gaskets.
These properties form a baseline for performance in anything from automotive seals to industrial hoses.
Chemical Resistance
One of the crowning achievements of nitrile rubber is its robust chemical resistance. This trait is a game changer in industries where exposure to oils, solvents, and fuels is the order of the day. It’s like having a trusty shield against corrosive agents, ensuring longevity and reliability in products.
- Oil Resistance: These compounds are particularly resistant to mineral oils and fuels. This quality is what earns nitrile rubber its place in the automotive industry—think fuel lines and gaskets that are constantly exposed to aggressive mediums.
- Resilience Against Solvents: Nitrile exhibits exceptional resistance to various solvents, making it invaluable in sectors involving chemicals. Whether it’s in laboratory settings or manufacturing processes, the ability to withstand harsh solvents cannot be overstated.
- Degradation Resistance: This rubber level of chemical resilience prolongs the lifespan of components, ensuring they do not degrade prematurely.
"Nitrile rubber compounds can handle the heat; they just don’t buckle under pressure when chemicals are thrown their way."
Thermal Stability
Thermal stability in nitrile rubber compounds is another critical aspect. As industries are more frequently operating under extreme temperature conditions, the importance of thermal resistance cannot be ignored.
- Heat Resistance: Nitrile can endure elevated temperatures while still maintaining its physical and mechanical properties. This makes it suitable for materials used in high-heat applications, such as O-rings in engines.
- Cold Flexibility: Not to be outdone in colder environments, nitrile rubber maintains its flexibility even in frigid conditions. This ensures that seals or gaskets do not become brittle and crack when the temperature drops.
- Decomposition Point: Understanding the decomposition temperature is vital, especially in applications where heat is a concern. Nitrile rubber typically exhibits good thermal aging properties, translating to a longer service life.
These properties together illustrate why nitrile rubber compounds are prominent in critical applications. They bring together a unique blend of physical strength, chemical resilience, and thermal endurance, making them an indispensable material in a variety of fields.
Applications of Nitrile Rubber Compounds
Nitrile rubber compounds are widely recognized for their versatility and wide-ranging applicability across various industries. Their unique properties—such as resistance to oil, chemicals, and temperature fluctuations—make them indispensable. Businesses and manufacturers actively seek these qualities when developing components to meet stringent performance standards. Understanding specific applications not only showcases the compound's effectiveness but also underscores its importance in modern manufacturing processes.
Automotive Industry
In the automotive sector, nitrile rubber plays a critical role. It is often utilized for gaskets, seals, and hoses due to its resistance to high temperatures and chemical exposure. For instance, when oil leaks or high engine temperatures are concerns, manufacturers lean towards nitrile rubber parts to ensure durability and reliability.
- Fuel System Components: Hoses and seals made from nitrile rubber prevent fuel from leaking and keep the system operating smoothly.
- O-Rings: These are essential in preventing fluid leaks and maintaining pressure within various automotive systems.
"The automotive industry has seen a dramatic decrease in product failures thanks to the adoption of nitrile rubber compounds."
This compound's ability to withstand extreme conditions without degrading is why it's often a top choice for many automotive applications.
Aerospace Applications
The aerospace industry demands materials that can handle severe stresses and environmental conditions. Nitrile rubber compounds meet these requirements, providing excellence in sealing, cushioning, and insulating applications. In aircraft, they serve in areas such as fuel systems and hydraulic systems, ensuring the safety and efficiency of air travel.
- Sealing: Nitrile's low gas permeability is crucial for sealing components, thereby maintaining cabin pressure.
- Insulation: Its thermal properties protect sensitive mechanisms from extreme temperatures.
These features ultimately lead to safer and more efficient aircraft, which is especially important considering the rigorous safety regulations in this field.
Medical Devices
The medical sector is another area where nitrile rubber compounds shine. They are incorporated into a variety of medical devices, due to their biocompatibility and resistance to sterilization methods. Nitrile rubber ensures that equipment remains hygienic and functional.
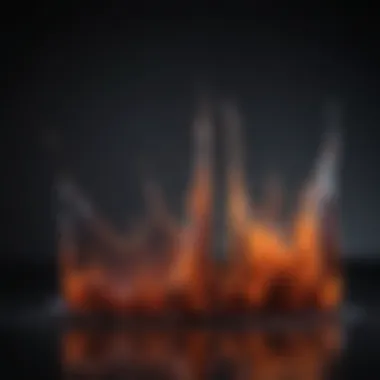
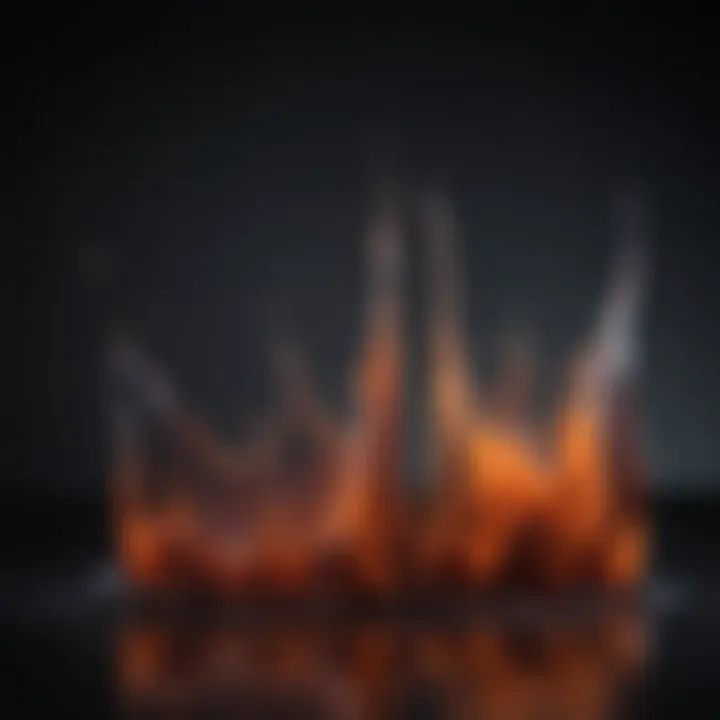
- Gloves: Widely preferred for their tactile sensitivity and chemical resistance, making them essential for healthcare professionals.
- Seals and Gaskets: Used in medical devices to ensure contamination-free environments.
Moreover, as patient safety remains paramount, the usage of nitrile rubber compounds helps bolster industry standards and regulations.
Industrial Uses
In industrial applications, the strength and resilience of nitrile rubber make it a go-to material. It finds a home in manufacturing settings where working with oils, solvents, and other hazardous materials is routine.
- Hoses: Used in equipment that transports aggressive fluids, nitrile rubber hoses are designed to withstand harsh environments.
- Conveyor Belts: These are often coated with nitrile rubber to enhance grip and durability.
The reliance on nitrile rubber compounds in these settings can lead to improved efficiency and reduced downtime, thus enhancing overall productivity.
Thus, nitrile rubber compounds not only serve distinct and varied applications across different industries, but their special properties also indicate their essential role in achieving performance, durability, and safety.
Manufacturing Processes
The manufacturing processes for nitrile rubber compounds hold a significant place in their overall success and functionality. Understanding how these compounds are created allows us to grasp both their advantages and limitations. Proper techniques can enhance the properties of nitrile rubber, resulting in superior performance in a variety of applications. Techniques for manufacturing offer detailed insights into the science behind the materials, guiding the choice of compounds for specific needs.
Compounding Techniques
Compounding is crucial in determining the final properties of nitrile rubber. During this phase, various ingredients are blended with the nitrile base polymer to achieve desired characteristics. These ingredients typically include fillers, plasticizers, stabilizers, and curing agents. Each of these components plays a different role:
- Fillers: These materials can improve mechanical properties and cut costs. Common fillers include carbon black and silica, which bolster strength and resilience.
- Plasticizers: Aldehyde plasticizers help enhance flexibility and processability.
- Stabilizers: They protect against heat and oxidative degradation, ensuring longevity and strength under various conditions.
- Curing Agents: Systems like peroxides and sulfur are used, effectively cross-linking the rubber to improve its performance.
The compounding process isn’t just a mix-and-match; it requires precise calculations and understanding of chemical interactions. Too little or too much of a component can make a world of difference, leading to failure in service.
Molding and Extrusion Methods
Once compounded, nitrile rubber can be shaped through several methods, two of the most common being molding and extrusion. Both techniques offer unique advantages, and the choice depends on the desired form and application.
- Molding: This involves shaping the rubber using molds. It allows for the creation of complex geometries and is often used for products like seals and gaskets. There are various types of molding, including:
- Extrusion: This process is perfect for creating continuous shapes, such as tubes or sheets. The rubber is forced through a die, shaping it into the desired profile. It is especially effective for high-output needs and allows for uniform thickness along long sections of material. The main advantage of extrusion is that it provides a continuous product with high precision in dimensions.
- Compression Molding: Great for larger volumes and simple designs, where material is placed in a mold and heated.
- Transfer Molding: Ideal for intricate designs, this method involves transferring material into a mold cavity under heat and pressure.
- Injection Molding: Notably faster and efficient, especially for small to medium parts, where the rubber is injected into molds at high temperatures.
Molding is beneficial when unique shapes are needed, while extrusion allows for high-volume production and uniformity. The choice largely depends on the application!
In summary, the manufacturing processes for nitrile rubber compounds are essential to ensure the quality and efficiency of the end products. By understanding the intricacies behind compounding, molding, and extrusion, one can appreciate how these techniques contribute to the versatile applications of nitrile rubber across different industries.
Performance Evaluation
In any field where materials are central to function, performance evaluation becomes critical. When it comes to nitrile rubber compounds, the assessment of their performance ensures not only the longevity and reliability of end products but also their effectiveness in the intended application. This section takes a closer look at various aspects of performance evaluation, exploring testing standards and field testing methodologies.
Testing Standards
Testing standards set the benchmarks against which the performance of nitrile rubber compounds is measured. These standards ensure consistency and reliability, providing a structured approach to evaluate the properties of these materials. Organizations such as ASTM (American Society for Testing and Materials) and ISO (International Organization for Standardization) play a crucial role in developing these benchmarks.
A few commonly referenced standards include:
- ASTM D1418: This standard provides a systematic approach in classifying rubber materials, which helps identify the specific type of nitrile rubber used in various applications.
- ASTM D2000: Focused on the properties of rubber materials, this standard outlines the necessary tests for evaluating physical and mechanical properties, including tensile strength and elongation.
- ISO 37: This standard details a method for the determination of tensile strength, elongation at break, and other mechanical properties regarding rubber products.
The significance of these standards cannot be understated. They ensure that products meet industry specifications, which is vital for sectors like automotive or medical, where failure can have dire consequences. Moreover, compliance with these testing standards not only amplifies consumer trust but also enhances marketability, adding an edge in a competitive landscape.
Field Testing and Assessment
Field testing serves as an extension of laboratory evaluations, providing real-world insights into the performance of nitrile rubber compounds. This practical approach is particularly essential in applications exposed to varied conditions. Any discrepancies between lab and field performance can lead to major adjustments in production or use of the material.
Field assessments often consider several factors:
- Environmental Conditions: Nitrile rubber may behave differently under UV light exposure, extreme temperatures, and varying humidity levels.
- Operational Loads: Testing includes evaluating how nitrile compounds perform under repeated stress or fatigue, simulating operational stresses they will encounter in real applications.
- Compatibility Testing: In industries like automotive, materials come into contact with different fluids. Field tests assess how well nitrile rubber interacts with oils and chemicals, verifying the chemical resistance documented in lab tests.
"Experiments in controlled environments often overlook the complexities of real-world scenarios; that’s where field assessments come in to play a crucial role."
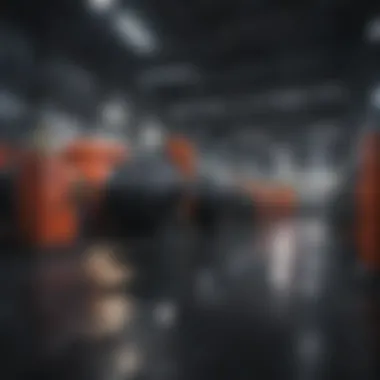
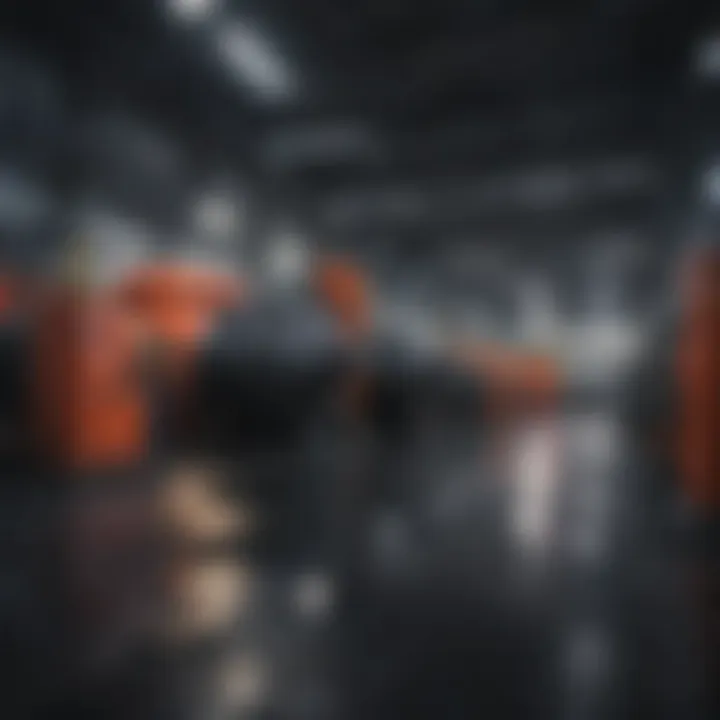
Ultimately, both testing standards and field testing mechanisms work hand-in-hand to provide a comprehensive understanding of nitrile rubber compounds' performance. Such evaluations not only inform manufacturers about their product quality but also help in refining formulations to better suit consumer and industrial needs, ensuring that the materials keep pace with evolving technological demands.
Environmental Considerations
The growing awareness around environmental issues has led industries to scrutinize their production processes. Nitrile rubber compounds, once viewed primarily through the lens of material performance and economic viability, now require a comprehensive understanding of their environmental impact. It's crucial for both manufacturers and consumers to consider aspects such as sustainability in production and recycling options.
Sustainability in Production
The footprint of nitrile rubber production can be significant, involving energy-intensive processes and contributing to greenhouse gas emissions. However, manufacturers are increasingly motivated to adopt sustainable practices.
- Use of Bio-Based Resources: Some innovators are experimenting with bio-based nitrile rubber sources. Replacing petrochemical materials with renewable resources helps to reduce the overall environmental impact. While still in its infancy, this approach showcases potential for greener production.
- Energy Efficient Processes: Deploying energy-efficient technologies in manufacturing can cut costs and emissions simultaneously. Companies are investing in advanced machinery that reduces energy consumption while maintaining high-quality output. This alignment of economic and environmental goals facilitates a sustainable production paradigm.
- Waste Reduction Strategies: Implementing strategies such as lean manufacturing can minimize waste. Manufacturers can optimize raw material usage and reduce off-cuts, thus lowering the volume of waste generated during production.
Sustainable practices not only make the production of nitrile rubber more eco-friendly but can also facilitate compliance with increasing regulatory pressures.
Recycling and Disposal Options
With the rise in environmental awareness, understanding how to dispose of or recycle nitrile rubber compounds becomes essential. Nitrile, while robust in properties, presents challenges in terms of end-of-life management. Here are some key elements to consider:
- Recycling Facilities: Currently, the recycling of nitrile rubber isn't widespread, but facilities dedicated to reprocessing rubber materials are emerging. These primarily focus on turning scrap rubber into crumb, which can be repurposed in other applications (like paving materials). Encouraging local recycling efforts can ensure these facilities remain viable.
- Repurposing Strategies: Beyond official recycling channels, there are creative ways to repurpose discarded nitrile rubber. It can be used in playground surfaces, automotive mats, or to create insulation materials. Embracing versatile reuse strategies helps mitigate waste.
- Disposal Concerns: While disposing of nitrile rubber in landfills is still common, it’s crucial to be aware of the long-term implications. Nitrile can take significant time to decompose, which contributes to landfill mass. Developing more effective disposal methods, such as incineration with energy recovery, can help to alleviate these concerns.
"Considering the life cycle of nitrile rubber from production to disposal encourages a transformative outlook on material use and its impact on our planet."
Addressing the environmental aspects of nitrile rubber is pivotal not only for compliance but also for fostering a culture of sustainability in the industry. As consumers become more environmentally conscious, manufacturers will likely feel the pressure to adapt practices that not only enhance performance but also lessen ecological footprints.
Future Trends in Nitrile Rubber Development
Exploring the future trends in nitrile rubber development is critical for understanding how this versatile material will evolve to meet the needs of various industries. As technology advances and environmental concerns grow, the focus on nitrile rubber compounds will likely shift towards innovation in formulation and sustainable practices.
Innovations in Compound Formulations
Recent research and development in compound formulations show promising advancements in the properties of nitrile rubber. These innovations often aim to enhance the fundamental characteristics of nitrile rubber, such as its oil and chemical resistance, flexibility, and durability.
Key Innovations Include:
- Bio-based Chemicals: There is a strong push towards incorporating bio-based materials into compound formulations. This will not only preserve the performance of nitrile rubber but will also reduce its reliance on petroleum-based resources.
- Improved Polymer Blends: Researchers are experimenting with blending nitrile rubber with other materials to optimize various properties. For instance, combining it with thermoplastic elastomers can impart easier processing capabilities while maintaining robustness.
- Additive Technologies: The use of nanomaterials as additives could significantly improve mechanical properties and enhance resistance to wear and tear, making nitrile rubber even more robust for high-demand applications.
Adopting these innovations can substantially increase the market competitiveness of nitrile rubber products and offer substantial benefits to manufacturers aiming to meet stricter regulatory standards.
Emerging Market Demands
The market landscape for nitrile rubber is shifting.A variety of sectors are heightening demand for nitrile rubber compounds, including automotive, aerospace, medical, and consumer goods.
Trends Driving Demand:
- Electric Vehicles: The ramp-up in electric vehicle production is requiring advanced materials that can handle higher temperatures and various chemicals, which nitrile rubber compounds are well-equipped to provide.
- Medical Device Innovation: The ongoing design and development in medical devices, especially in response to recent health crises, emphasize materials that are not only durable but also biocompatible. Nitrile’s adaptability makes it suitable for these applications.
- Sustainability Requirements: Industries are increasingly focusing on sustainability, prompting a call for environmentally friendly materials. Nitrile rubber manufacturers are expected to adopt greener practices and develop recyclable products, resonating well with market trends towards sustainability.
As industries pivot towards advanced sustainable solutions, the evolution of nitrile rubber compounds will play a vital role in meeting those demands and expectations.
The End
In wrapping up this exploration of nitrile rubber compounds, it becomes clear how crucial these materials are in today’s diverse industrial landscape. Nitrile rubber isn’t just another synthetic rubber; it stands out due to its remarkable resistance to a range of elements like oils and heat, which makes it a preferred choice for many applications across various sectors. Understanding these properties is not merely academic; it drives innovation and efficiency in manufacturing processes and product performance.
Recap of Key Points
To distill the vast information presented, let’s highlight some of the key points:
- Chemical Structure: Nitrile rubber is predominantly made from a copolymer of acrylonitrile and butadiene, which confers its chemical resistance and mechanical strength.
- Properties: Its unique characteristics include superior elasticity, thermal stability, and robust resistance to fuel and chemicals, making it essential in demanding environments.
- Applications: From automotive seals to medical devices, the adaptability of nitrile rubber compounds serves critical functions, underscoring their importance in modern manufacturing.
- Environmental Considerations: Sustainability and efficient recycling methods are increasingly becoming part of the discourse around nitrile rubber, indicating a shift toward eco-friendlier practices in its production and disposal.
Implications for Future Research
The future of nitrile rubber compounds looks promising but also presents challenges that warrant further inquiry. Some of the areas that could benefit from thorough investigation include:
- Advanced Formulations: Research into new compound formulations can lead to enhancements in performance, extending the lifespan and applications of nitrile rubber in specialized areas.
- Sustainability Practices: Ongoing studies on how to improve the recycling process for nitrile products could lead to significant strides in reducing waste and promoting circular economy practices.
- Market Demands: As industries evolve, understanding emerging market needs can guide the development of nitrile rubber compounds that are tailored for the next generation of products.
"The exploration of nitrile rubber compounds is not an isolated academic endeavor but a gateway to innovations that influence everyday products and operations in various industries."
In summary, nitrile rubber is much more that meets the eye, demanding our attention for continuous exploration, adaptation, and advancement.