Precision in Gas Measurement: Techniques and Tools
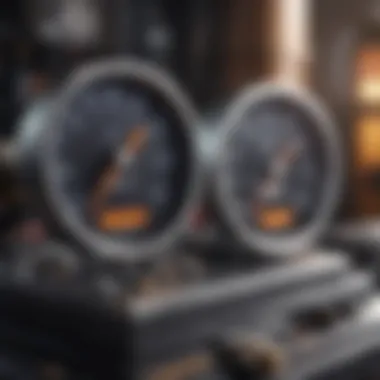
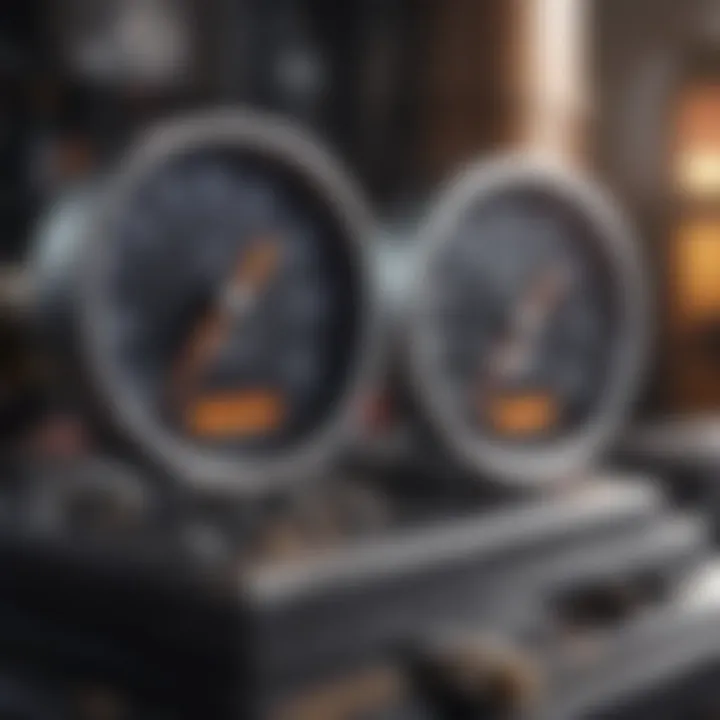
Intro
Measuring gas accurately is a crucial aspect in many fields such as science, industry, and daily life. The methods and tools used not only ensure compliance with safety and regulatory standards, but they also play a critical role in various research applications. Understanding these methods can help enhance the quality of research and the efficiency of industrial processes.
This article aims to provide a comprehensive overview of the different methods and tools available for measuring gas, while also delving into their applications across diverse settings. It will highlight the importance of precise measurements and how evolving technologies are shaping these practices.
Research Overview
In the following sections, we will explore the significance of accurate gas measurement methods, the context in which these measurements are utilized, and the various tools that facilitate the process.
Summary of Key Findings
- Precision is Integral: Accurate gas measurement is paramount for safety, compliance, and research outcomes.
- Diverse Methods: There are several methods to measure gas, including gravimetric, volumetric, and flow-based approaches.
- Technological Advances: New technologies have improved the accuracy and efficiency of gas measurement tools.
Background and Context
Gas measurement has evolved over time, influenced by industry requirements and scientific progress. Early methods relied on simple techniques, while modern measurement tools incorporate advanced technology, enhancing overall performance. Understanding this evolution provides insight into current practices and paves the way for future advancements.
Methodology
This section outlines the typical methodologies adopted in gas measurement, focusing on experimental designs and data collection techniques that ensure reliability.
Experimental Design
An effective experimental design in gas measurement often includes the following aspects:
- Control Variables: Maintaining constant temperature and pressure for accurate results.
- Sample Selection: Determining appropriate gas samples critical for the measurement experiment.
Data Collection Techniques
Data collection is crucial for gas measurement validity. Common techniques include:
- Direct Measurement: Utilizing devices such as gas chromatographs or infrared sensors to obtain direct readings.
- Indirect Measurement: Relying on calculated values derived from related measurements in some scenarios.
Prelims to Gas Measurement
Gas measurement is a crucial aspect in various sectors, including scientific research, industrial manufacturing, and environmental monitoring. Accurate gas measurement ensures safety and compliance with regulations, while also contributing to the understanding of processes that impact our environment. In this section, we will delve into the significance of gas measurement and its wide-ranging applications.
Importance of Gas Measurement
The importance of gas measurement lies primarily in its ability to provide reliable data. This data serves as the foundation for decision-making in multiple domains. For instance, in industrial settings, monitoring gas emissions helps in minimizing harmful effects on health and the environment. In laboratories, precise gas measurements are essential for accurate experimental outcomes. Moreover, regulatory agencies rely on gas measurement for enforcing environmental standards.
Accurate gas measurement is not merely a technical requirement; it is a fundamental element for ensuring public safety and environmental sustainability.
In addition, gas measurement plays an integral role in energy management. It enables businesses to track natural gas usage and optimize their consumption, leading to potential cost savings. Understanding gas quantities is also vital for processes like combustion, where efficiency depends on precise measurements. This technical aspect underscores the multi-faceted value of gas measurement in today's world.
Applications of Gas Measurement
Gas measurement finds applications across diverse fields. Some notable areas include:
- Environmental Monitoring: This involves tracking pollutants and greenhouse gases. Techniques used are essential for addressing climate change and air quality issues.
- Industrial Processes: Companies utilize gas measurement for quality control and safety. Ensuring the right gas concentrations can prevent accidents and enhance product quality.
- Healthcare: In medical settings, measuring anesthetic gases and carbon dioxide levels is vital for patient safety during surgical procedures.
- Energy Sector: Accurate gas measurement critically supports natural gas production, distribution, and consumption.
Through these applications, gas measurement showcases its importance across various sectors, allowing for safer environments and more efficient processes.
Fundamental Principles of Gas Measurement
Understanding the fundamental principles of gas measurement is essential for grasping the full scope of how we quantify gases accurately. The importance of these principles lies in their ability to provide a solid foundation upon which various measurement techniques and instruments are built. These principles encompass the behavior of gases under different conditions and the physics that govern their properties. This understanding allows for enhanced precision in varied applications, ranging from industrial processes to laboratory experiments.
Physical Properties of Gases
Gases exhibit distinct physical properties which play a vital role in their measurement. These properties include pressure, volume, temperature, and density. Each property influences how gases behave and, consequently, how they are measured. For instance, the pressure of a gas can change depending on its volume and temperature. Knowledge of these properties is crucial for successful gas measurement as it aids in predicting gas behavior under varying conditions.
- Pressure: The force exerted by gas molecules against the walls of its container. Measuring pressure accurately is crucial for many industrial applications.
- Volume: The space occupied by a gas, directly related to its pressure and temperature. Volume measurement often involves sophisticated equipment.
- Temperature: Refers to the degree of heat present in the gas. It affects gas density and pressure, making temperature control essential.
- Density: The mass per unit volume of the gas. Different gases have different densities, which can impact their handling and measurement.
Gas Laws Overview
Gas laws provide a mathematical approach to understanding the behaviors of gases. These laws establish relationships between pressure, volume, and temperature, serving as fundamental principles in gas measurement. The most significant gas laws include Boyle's Law, Charles's Law, and Avogadro's Law.
- Boyle’s Law: States that the pressure of a gas is inversely proportional to its volume at a constant temperature. This law is crucial in several engineering applications.
- Charles’s Law: Describes how gases expand when heated at constant pressure. This principle is important for understanding gas behavior in thermal applications.
- Avogadro’s Law: Indicates that the volume of gas at constant temperature and pressure is directly proportional to the number of moles. Understanding this helps in gas composition analysis.
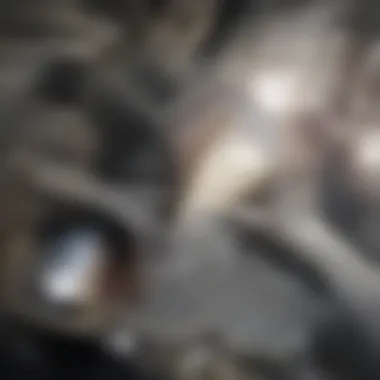
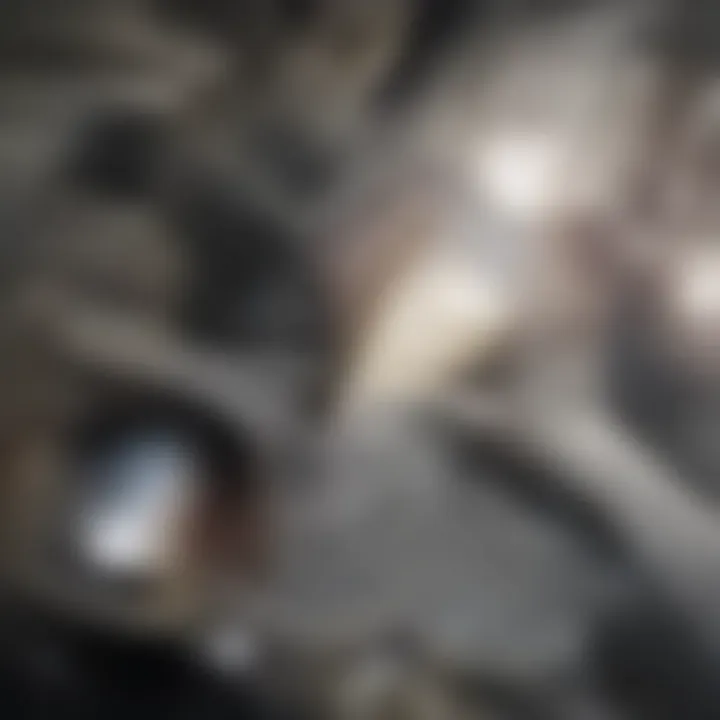
Knowledge of these laws not only enhances the accuracy of measurements but also facilitates the optimization of processes involving gases. Each of these principles and laws provides a framework that is essential for developing accurate measurement methods, improving safety protocols, and ensuring compliance within industry standards.
"Precision in gas measurement is not merely a technical requirement but a crucial determinant for safety and regulatory compliance."
In summary, the fundamental principles of gas measurement provide a crucial understanding that enables practitioners to measure gases accurately and efficiently. By delving into the physical properties of gases and the applicable gas laws, one lays the groundwork necessary for utilizing modern measurement techniques effectively. These principles also emphasize the importance of a rigorous approach to gas handling, transforming theoretical knowledge into practical applications.
Methods of Measuring Gas
Understanding the methods of measuring gas is crucial for ensuring accuracy and reliability in various applications. These methods are broadly divided into direct and indirect approaches. Each method's precision affects safety, compliance, and efficient operation in industrial and residential environments. Knowing these methods helps professionals select the right technique based on specific needs.
Direct Methods
Direct methods provide a clear measurement of gas quantities. These techniques are often favored for their straightforward application and reliability.
Volume Measurement
Volume measurement is a fundamental direct method that determines the space occupied by gas. This approach is crucial in industries like chemical manufacturing, where precise gas volumes can affect reaction outcomes.
The key characteristic of volume measurement is its simplicity. It often involves using devices such as flow meters, which allow for real-time monitoring. This makes it a popular choice in settings requiring immediate feedback on gas usage or production. The unique feature of volume measurement lies in its ability to provide measurable data under various conditions.
However, advantages come with challenges. Volume measurements can vary due to pressure and temperature changes, making calibration essential. Therefore, while beneficial, it requires careful consideration of environmental factors to maintain accuracy.
Mass Measurement
Mass measurement focuses on calculating the mass of gas instead of its volume. This technique is important for applications that require understanding gas density and mass flow rates. It is often employed in process industries and laboratories.
The primary characteristic of mass measurement is its reliance on weighing gas under controlled conditions. This attribute makes it a reliable option when exact quantities matter, ensuring accurate formulations and compliance with regulations.
A unique feature of mass measurement is the use of correlative equations that link mass to other properties like volume. This method does have downsides, such as needing advanced equipment and additional calculations to derive accurate readings, which can complicate processes in certain situations.
Indirect Methods
Indirect methods are valuable when direct measurements are not feasible. These techniques infer measurements based on related parameters, often encasing various environmental factors.
Pressure Measurement
Pressure measurement assesses the force exerted by gas within a system. It is essential for understanding gas behavior in processes where pressure changes occur frequently. Industries such as oil and gas utilize this method to ensure system integrity and safety.
The key characteristic is its ability to monitor gas without direct contact with the gas itself, reducing contamination risks. This makes pressure measurement an appealing option for sensitive applications. A distinctive aspect is how pressure readings can suggest the associated volume or flow rate through known equations, thus providing useful data.
However, dependent on the environment, pressure measurement can be influenced by temperature fluctuations, thus requiring regular calibration and vigilant monitoring.
Temperature Measurement
Temperature measurement examines how gas responds to heat changes. This method is vital for processes where temperature control dictates gas behavior, such as in HVAC systems or chemical reactors.
A significant attribute of temperature measurement is its role in optimizing system efficiency and safety. Understanding how temperature affects gas can help in maintaining conditions ideal for operation.
Unique to temperature measurement is its ubiquitous nature across various industries. While it has its advantages, like ensuring proper thermal management, temperature effects can complicate other measurement methods, requiring careful integration of data from multiple sources.
A thorough understanding of these methods gives insights into gas behavior, guiding professionals as they implement best measurement practices in their fields. Each method presents unique benefits and challenges tailored to the needs of various applications.
Tools for Measuring Gas
In the realm of gas measurement, selecting the appropriate tools is paramount for ensuring accurate results. These tools are designed to assess various properties of gases, ranging from flow rates to composition. Each category of tool serves a distinct purpose and influences measurement outcomes significantly. Their relevance extends across numerous sectors including manufacturing, laboratory research, and environmental monitoring.
Gas Flow Meters
Gas flow meters are essential instruments for measuring the flow of gases in a pipeline. They function by determining the volume or mass of gas being transported over a defined period. These devices can be categorized into several types such as vortex flow meters, thermal mass flow meters, and rotary positive displacement meters. The choice of flow meter often depends on the specific application, gas type, and required measurement accuracy.
The benefits of gas flow meters include real-time monitoring, which supports efficient operational control and resource management. They provide critical data that can enhance safety by preventing hazardous situations caused by gas leaks or overpressurization. Furthermore, accurate flow measurements are vital for compliance with regulations and optimization of processes, thereby illustrating the importance of these tools in various settings.
Gas Analyzers
Gas analyzers play a pivotal role in determining the composition of gases within a mixture. These devices are used to identify specific gas constituents, such as carbon dioxide, nitrogen, and oxygen. Various techniques are employed in gas analyzers, including infrared spectroscopy, gas chromatography, and electrochemical sensors.
Utilizing gas analyzers allows for precise monitoring of air quality, emission controls, and industrial processes. The insights gained aid in environmental assessments and compliance with health and safety regulations. Moreover, advances in gas analysis technology facilitate real-time data collection, which is increasingly crucial in industrial operations and scientific research. Understanding the gas composition can lead to improved efficiency and reduced environmental impact.
Calorimeters
Calorimeters measure the heat of reaction or combustion, providing insights into the energy content of fuels and gases. This tool is especially useful in energy production and material testing. There are different types of calorimeters, including bomb calorimeters and differential scanning calorimeters, each suited for particular applications.
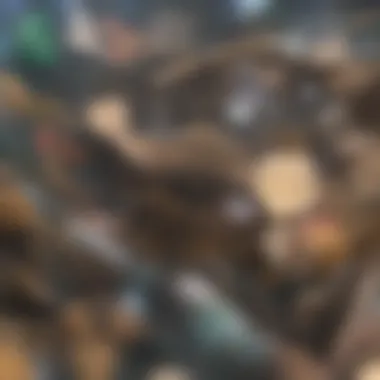
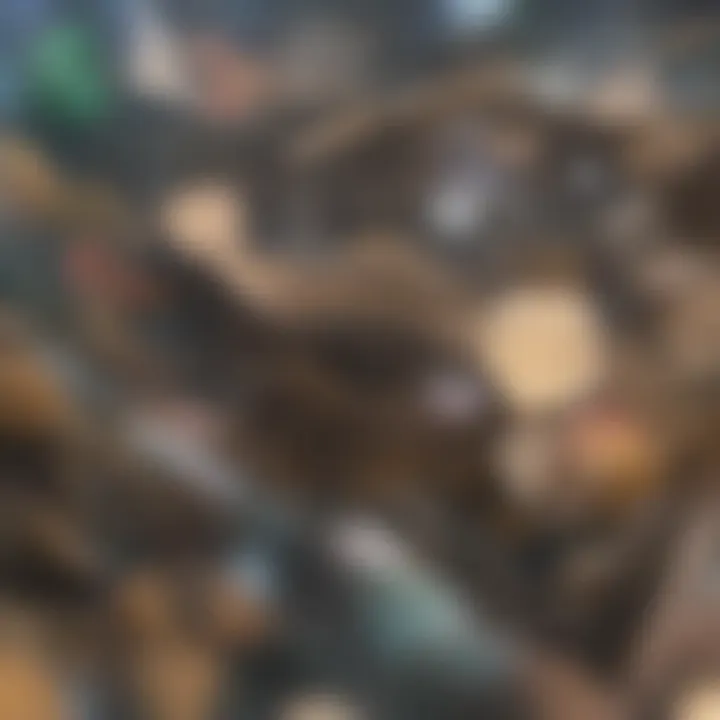
The significance of calorimeters extends to regulatory compliance and energy efficiency assessment in various industries. By measuring thermal properties, organizations can optimize fuel usage and reduce costs. Additionally, calorimetry can enhance safety measures by monitoring the calorific value of gases used in industrial processes or residential heating. Regular use of calorimeters contributes to effective energy management and environmental stewardship.
Types of Gases and Their Measurement Challenges
Understanding the types of gases and the challenges associated with their measurement is crucial for effective gas measurement practices. Different gases behave differently under varying conditions, which can affect the precision and accuracy of measurement instruments. Recognizing these differences is essential for industries and research where gas measurement plays a significant role in ensuring safety, compliance, and operational efficiency.
Gaseous Mixtures
Gaseous mixtures present unique challenges for measurement techniques. A gas mixture refers to a combination of two or more gases where each gas retains its individual properties. This can complicate the measurement process due to several factors. The presence of multiple components can affect the overall density, pressure, and temperature of the mixture.
One important consideration in measuring gaseous mixtures is the partial pressure of each component gas. According to Dalton's Law, each gas in a mixture exerts pressure independently of others. Thus, accurate measurement requires knowledge of the composition of the mixture. Instruments must be calibrated to account for the varying properties of each gas.
"Understanding the behavior of each component gas is vital for effective measurement of gaseous mixtures."
Another challenge is the potential for chemical interactions among the gases. Some mixtures may contain reactive components that can alter the composition or properties under certain conditions. For example, if water vapor is present in a gas mixture, it may condense and affect the volume and mass readings. Therefore, gas analyzers must be selected carefully to ensure compatibility with the specific gases in a mixture.
In practical applications, advanced techniques such as gas chromatography can be employed for mixture analysis. Gas chromatography separates components based on their interaction with a stationary phase, enabling precise measurement of individual gases within the mixture. This method is particularly valuable in industries like environmental monitoring and chemical manufacturing.
Reactive Gases
Reactive gases pose another layer of complexity in measurement. These gases can undergo chemical reactions that may alter their concentration or properties while being measured. Gases such as hydrogen, chlorine, and ammonia are examples of reactive gases that can significantly impact measurement accuracy.
When measuring reactive gases, it is vital to consider the time factor. The duration of exposure to other substances can result in unexpected reactions that change the composition of the sample. This is especially critical in real-time monitoring situations where immediate measurement is required for safety purposes.
Instruments designed to measure reactive gases often incorporate specific design features. For instance, some analyzers use inert materials to minimize reactions during measurement. Furthermore, they may be equipped with safety mechanisms to handle the release of reactive gases safely.
Calibration and Validation of Measurement Instruments
Calibration and validation of measurement instruments is a crucial aspect in the field of gas measurement. Precision is paramount when measuring gas, as even small inaccuracies can lead to significant safety hazards and incorrect conclusions in scientific research. The reliability of data produced by measurement instruments directly affects decision making in various applications, including environmental monitoring, industrial processes, and medical diagnostics.
Calibration refers to the process of adjusting the measurement instruments to ensure that they provide accurate readings. This involves comparing the measurements taken by the instrument against a known standard. Validation, on the other hand, ensures that the measurement system consistently produces results that meet the required specifications. Both processes are vital for maintaining the trustworthiness of gas measurement data.
Calibration Standards
Calibration standards are predefined benchmarks that provide reference points for instrument accuracy. These standards are often established by national and international organizations, ensuring compliance and uniformity across different measurement tools. Examples include the National Institute of Standards and Technology (NIST) in the United States and the International Organization for Standardization (ISO).
Using calibrated standards serves multiple purposes:
- Accuracy: Ensures that measurement instruments provide true measurements of gas concentrations.
- Interoperability: Facilitates consistent measurements across various laboratories and industries.
- Compliance: Assists organizations in meeting regulations and safety standards that govern gas measurements.
To maintain accuracy, users must document the calibration process and schedule regular calibration sessions. The calibration standards chosen should match the specific requirements of the application, considering factors such as gas type and measurement range.
Importance of Regular Validation
Regular validation of measurement instruments is imperative for ensuring continued accuracy over time. Environmental factors, wear and tear, and operational conditions can affect the performance of measuring devices. Thus, a once-off calibration is insufficient for long-term accuracy. Monthly or quarterly validation checks help to identify any discrepancies early, allowing for adjustments before they lead to serious issues.
The key benefits of regular validation include:
- Reliability: Frequent checks ensure that instruments produce consistent results, boosting overall confidence in measurements.
- Quality Control: Regular validation is integral for maintaining high quality in measurement practices, essential in industries like pharmaceuticals or food production.
- Risk Management: By continuously validating instruments, organizations can mitigate risks associated with false readings, which could result in regulatory penalties or safety incidents.
"A minor calibration error can escalate to major consequences. Regular validation is not just good practice; it’s a requirement for safety and compliance."
Impact of Environmental Factors on Gas Measurement
Understanding the influence of environmental factors on gas measurement is essential for ensuring accuracy and reliability. This section focuses on two primary aspects: temperature and humidity. Each plays a significant role in how gas behaves and how measurements are interpreted.
Temperature Effects
Temperature is a critical variable in gas measurements. Changes in temperature can alter the volume and pressure of gases, leading to potential inaccuracies. When conducting experiments or industrial processes, it is vital to monitor temperatures consistently. This holds true especially in processes where precision is paramount, such as in laboratories and manufacturing.
Effects of temperature on gas behavior include:
- Volume changes: Gases expand when heated and contract when cooled, affecting the readings.
- Pressure variations: According to the ideal gas law, increasing temperature raises pressure if the volume is kept constant.
- Measurement instrument calibration: Instruments must often be calibrated for specific temperature ranges to maintain accuracy.
To mitigate these effects, maintaining a stable temperature environment is advised. This can involve using temperature-controlled settings or compensating for temperature variations in calculations. Additionally, instrument manufacturers usually specify the operational temperature range for their products, which should be strictly adhered to in any serious application.
"Precision in gas measurement requires attention to environmental variables, with temperature being one of the most influential factors."
Humidity Effects
Humidity, or the amount of water vapor in the air, also significantly impacts gas measurements. Gases can react differently based on humidity levels, which can lead to discrepancies in measurements. High humidity might cause gases to dissolve in water or form droplets, complicating measurement precision.
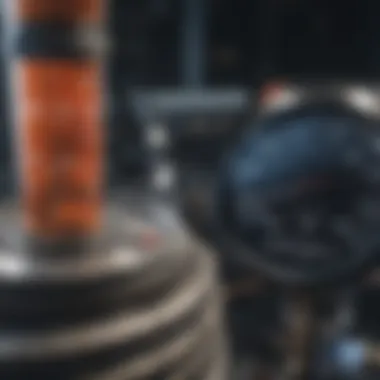
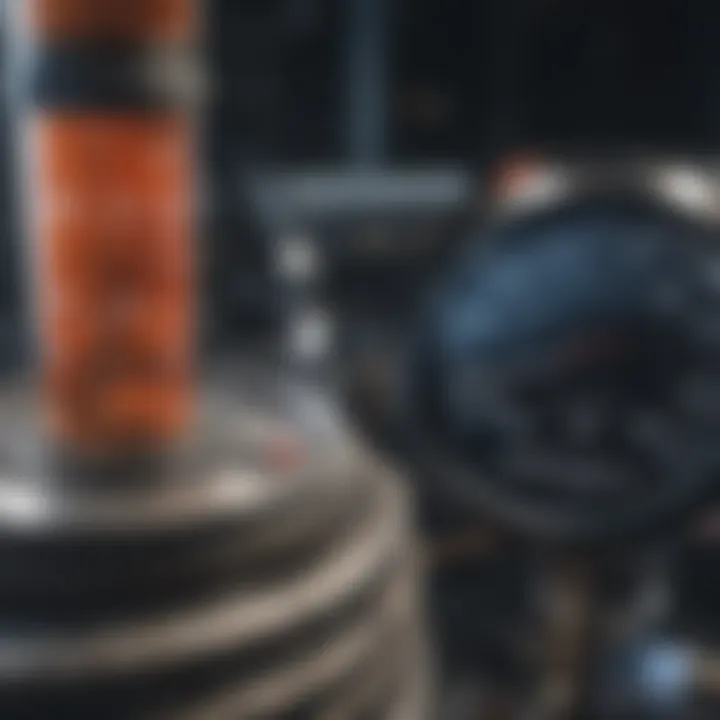
Key considerations regarding humidity include:
- Instrument performance: Some gas measuring devices, such as analyzers, may give faulty readings in high humidity.
- Sample condensation: Humid environments can lead to condensation in gas samples, distorting results.
- Calibration challenges: Like temperature, humidity levels need to be accounted for during calibration of measuring devices.
To address these challenges, it is crucial to ensure that gas samples are conditioned appropriately for analyses. This may involve drying gas samples or using dehumidifiers in workspaces to maintain controlled humidity levels. Researchers should also be aware of the local environment, as variations can lead to different baseline measurements over time.
Technological Advances in Gas Measurement
Technological advancements in gas measurement are at the forefront of improving accuracy, efficiency, and reliability in various applications. With the ever-increasing demand for precise gas measurement in industries such as oil and gas, environmental monitoring, and healthcare, understanding these advances is vital for stakeholders. New technologies not only enhance measurement capabilities but also influence regulatory compliance and safety protocols.
These innovations provide solutions to long-standing challenges. For instance, emerging technologies in sensors and data analytics significantly reduce downtime and increase the efficiency of operations. This is crucial for industries where safety and precision are paramount. Additionally, the integration of real-time data processing allows for immediate corrective actions, promoting proactive measures in managing gas flow and quality.
Emerging Technologies
Emerging technologies are transforming gas measurement through novel sensor designs and advanced analytics.
- Microelectromechanical Systems (MEMS): These sensors are compact and offer high sensitivity. They can detect gas concentrations at very low levels, making them essential for environmental monitoring and industrial safety.
- Optical Gas Imaging: This technology utilizes infrared cameras to visually detect leaking gases. It offers rapid assessment and is non-invasive. Such methods can be incredibly effective for industries needing regular inspections without disrupting operations.
- Smart Gas Meters: These devices incorporate IoT technology, allowing for remote monitoring of gas usage and leakage detection. They provide data in real time, enabling better decision-making and predictive maintenance.
The synergy of these technologies results in improved accuracy and responsiveness, crucial for today’s fast-paced industrial environments.
Automation and Remote Measurement
Automation and remote measurement techniques are gaining traction in the field of gas measurement. These innovations streamline operations and enhance data collection processes. Remote measurement eliminates the need for manual checks, reducing human error and operational costs.
- Telemetry Systems: These are instrumental in automating data collection. Sensors installed in various locations can communicate with a central system, delivering data instantaneously. This feature allows for continuous monitoring and immediate alerts when anomalies are detected.
- Predictive Maintenance: Automated systems can analyze data trends over time. This predictive capability prevents unforeseen breakdowns in measurement equipment, enhancing reliability.
- Remote Sensing Technologies: These technologies can monitor gas emissions from significant distances, mitigating the risks associated with on-site inspections.
With these advancements, the landscape of gas measurement is shifting, providing enhanced capabilities for current and future industry demands.
Legislative and Regulatory Aspects of Gas Measurement
The legislative and regulatory aspects of gas measurement are crucial to ensuring safety, compliance, and accuracy in various sectors. This area shapes how measurements are taken and assessed, affecting not just the industries involved but also the public and the environment.
Effective regulations provide a framework within which gas measurement must operate. Such regulations ensure that measurement practices meet certain standards, thus supporting reliability and integrity in different applications. Without these guidelines, inconsistencies could arise, leading to potentially hazardous situations in industries where gas levels are critical.
Standards and Compliance
Standards are essential in the field of gas measurement. They set the benchmarks for accuracy and reliability, helping ensure that different measurement tools and methods perform optimally. Compliance with these standards is not just a matter of legal obligation; it is also about fostering trust with stakeholders and customers.
Key advantages of adhering to established standards include:
- Increased Safety: Standardized measurement reduces risks associated with gas leaks and other hazardous conditions.
- Enhanced Accuracy: Compliance with recognized standards ensures that measurement instruments yield precise results.
- Improved Accountability: Adhering to regulations allows for better tracking of measurements, fostering responsibility among operators.
Organizations such as ASTM International and the International Organization for Standardization (ISO) provide guidelines that help businesses align with the best practices in gas measurement. These standards encompass various aspects, including calibration methods, maintenance, and operational procedures.
Impact on Industry Practices
The impact of legislative and regulatory frameworks on industry practices cannot be overstated. Regulations often dictate how various sectors approach gas measurement, influencing everything from equipment selection to employee training.
Industries such as oil and gas, healthcare, and manufacturing are particularly sensitive to these regulations. Practicing adherence to regulations can facilitate:
- Innovation: Compliance can drive companies to maintain updated or advanced measurement technologies to meet evolving standards.
- Operational Efficiency: Companies that align with regulations often see improvements in workflow and resource management.
- Risk Mitigation: Implementing regulated measurement practices decreases the likelihood of gas-related incidents.
"Regulatory compliance is not merely a tick box; it represents a commitment to stakeholder safety and trust."
For more information on standards and compliance related to gas measurement, you can explore resources such as Wikipedia and Britannica.
Future Directions in Gas Measurement
The field of gas measurement is constantly evolving. This evolution is crucial for several reasons. First, as global industries expand, the need for precise and reliable gas measurement becomes more significant. Technologies that improve measurement accuracy can enhance safety, compliance, and operational efficiency. Second, gas measurement plays a vital role in addressing environmental concerns and energy management, making it essential for sustainability.
New developments in this field promise to reshape how gas measurements are conducted across various environments, from industrial to residential settings. Understanding future directions is important for stakeholders, including policymakers, researchers, and industry professionals.
Innovations on the Horizon
Innovations in gas measurement technology are paving the way for more efficient and accurate measurements. Some key trends shaping this future include:
- Miniaturization of Sensors: Smaller and more portable sensors are enabling real-time measurements in diverse environments, enhancing decision-making processes.
- Smart Sensors: These devices utilize connectivity and software to provide more detailed data analysis and trends in gas behaviors, helping users to act rapidly and accurately.
- Remote Sensing Technologies: Advancements in remote sensing allow measurements in locations that are hard to access. These systems can provide data from wide areas, crucial for monitoring environmental changes.
- AI and Machine Learning: Integrating artificial intelligence in measurements can improve the precision of data interpretation. This means quicker responses to gas leaks or changes in chemical composition.
These innovations not only enhance the accuracy of gas measurement but also reduce risks associated with human errors. The ongoing development of these technologies suggests that the future of gas measurement may see the implementation of integrated systems capable of multitasking.
Challenges Ahead
While the future of gas measurement looks promising, several challenges need to be addressed. Key areas that require attention include:
- Data Security: With the rise of smart and connected devices, there is an increased risk of data breaches. Ensuring secure measurement data handling is vital.
- Implementation Costs: The costs of innovative technologies can be high. Industries must consider whether the benefits outweigh these initial investments.
- Standardization: As technologies evolve, the lack of standardized practices can lead to inconsistencies in measurement techniques across industries.
- Training and Expertise: New technologies require specialized knowledge. Industries may face a skills gap, making it difficult to implement and maintain advanced measurement systems effectively.
Addressing these challenges is essential for maximizing the potential benefits that new technologies can offer in gas measurement.