Roughness Calculation: Advanced Methods & Applications
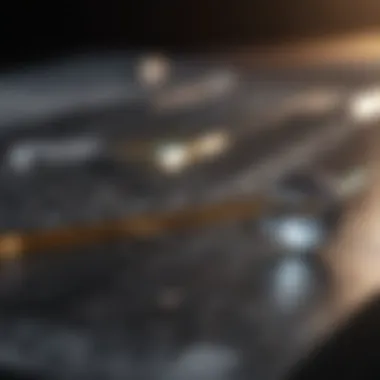
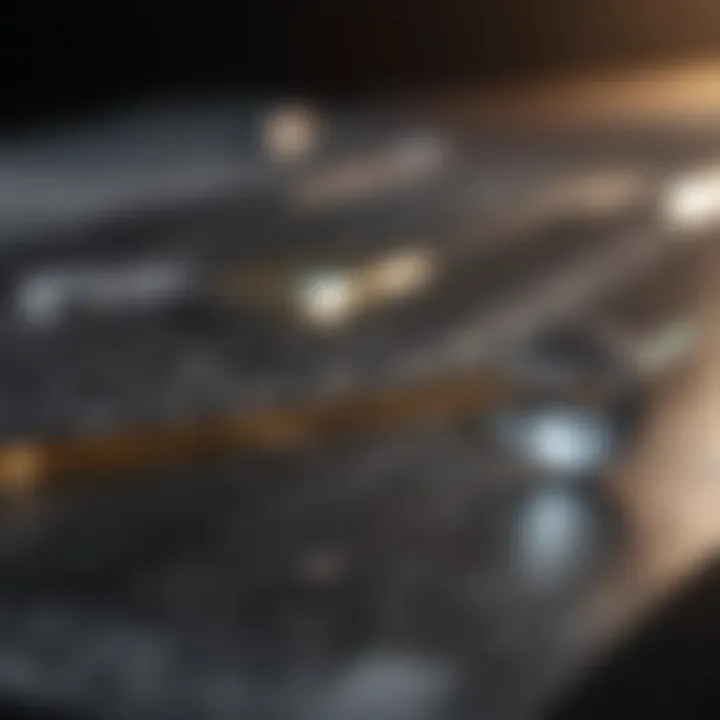
Intro
Roughness calculation is integral to understanding surface properties in various scientific inquiries. Recognizing the roughness of a surface influences its behavior in multiple contexts such as friction, adhesion, and fluid dynamics. This section outlines the significance of accurately quantifying surface roughness and introduces the key aspects to be discussed in the thorough exploration of this subject.
Roughness metrics play a crucial role in numerous fields, including engineering and material science. By assessing surface characteristics, researchers can predict how materials will behave under operational conditions. Furthermore, advances in technology continually reshape the methodologies employed in these calculations, leading to more precise and efficient analysis.
The subsequent sections will elaborate on key findings, methodologies, and emerging trends in roughness calculation. This in-depth exploration aims to equip students, researchers, and professionals with crucial insights to enhance their work and decision-making processes.
Preamble to Roughness Calculation
Roughness calculation plays a crucial role in various fields, including material science, engineering, and nanotechnology. Understanding the texture of a surface provides insights about its behavior, performance, and suitability for different applications. Accurate roughness measurements can lead to enhanced product quality and reliability. It builds the foundation for analyses involving friction, wear, coating adhesion, and even electrical conductivity.
In this section, we will unpack the definition and importance of surface roughness. A clear understanding is essential for researchers, students, and professionals alike. It guides the selection of measurement techniques and interpretation of results, ensuring that the insights gleaned from roughness data contribute meaningfully to scientific and practical advancements.
Definition of Surface Roughness
Surface roughness is a key parameter that quantifies the texture of a surface. It reflects the minor irregularities from an ideal flat surface. These irregularities arise from various processes, such as manufacturing and material treatment. The measurement of roughness can be expressed in different forms, primarily through roughness averages like Ra, Rz, and Rq. Each parameter captures specific aspects of surface texture and can impact how a material interacts in real-world scenarios.
By measuring surface roughness, one can assess how smooth or rough a surface is. It is important in applications like aerodynamics, where surface texture influences fluid flow around objects. In manufacturing, roughness can dictate how coatings adhere to surfaces or affect friction between moving parts.
Importance in Scientific Research
Surface roughness is fundamental for advancing knowledge across various scientific disciplines. Its importance can be highlighted through several key considerations:
- Predicting Performance: Roughness data supports predictions about material performance in real-world applications. This predictive capability is vital for developing materials tailored for specific uses.
- Enhancing Product Quality: In manufacturing, controlling surface roughness leads to improved product quality. Products that meet specific roughness criteria often perform better in terms of durability and functionality.
- Facilitating Research and Development: Understanding how surface texture interacts with other material properties drives innovation, especially in materials science and engineering.
"Surface roughness can significantly influence material properties, making accurate measurement essential for innovation and quality assurance."
Historical Context of Roughness Measurement
Understanding the historical context of roughness measurement is essential for grasping its importance in both scientific research and industry applications. The journey of roughness metrics and measurement techniques has evolved considerably over the last century. By examining how these methodologies developed, we can appreciate their role in current practices and future advancements.
Development of Roughness Metrics
The inception of surface roughness metrics begins in the early 20th century. Initially, roughness was assessed qualitatively, relying on visual inspections and rudimentary touch-based techniques. However, as materials science advanced, a systematic approach became necessary. The introduction of quantifiable metrics like Ra (Arithmetic Average Roughness) and Rz (Average Maximum Height) marked a significant shift.
The formulation of these metrics provided a consistent way to express surface irregularities. Researchers, such as Dr. R. S. A. K. Ray and others, made substantial contributions toward standardized methods that could be universally applied across various fields. Consequently, materials scientists, engineers, and manufacturers could communicate more clearly about surface properties, which enhanced collaboration and innovation.
Evolution of Measurement Techniques
The evolution of measurement techniques reflects advancements in technology and materials science. Early methodologies like stylus profiling gained prominence in the mid-20th century. This technique involved dragging a stylus across the surface to record deviations, which provided valuable data on surface roughness. However, it was limited by its inability to capture very small features or complex geometries.
With the introduction of technologies such as Atomic Force Microscopy (AFM) and Scanning Electron Microscopy (SEM), the precision and scope of roughness measurement expanded dramatically. These techniques allowed for the characterization of nanostructures and very fine features in materials. As a result, they opened new avenues for research and applications in fields like semiconductor manufacturing and biomedical engineering.
Each advancement in roughness measurement techniques not only improved the accuracy of the results but also broadened the range of applications. Researchers could now analyze surfaces at different scales, leading to better quality control in manufacturing processes. Furthermore, understanding surface roughness became crucial for predicting material behavior in practical applications, from friction to adhesion.
"The evolution of both metrics and techniques reveals a progressive understanding of how surface characteristics impact material performance and application."
In summary, the historical context of roughness measurement highlights the importance of progressing from qualitative assessments to quantitative metrics and sophisticated measurement techniques. This evolution fosters a deeper understanding of materials, aiding both research and practical applications in various industries. As we move forward, staying updated with these advancements will be key for researchers and professionals alike.
Mathematical Foundations of Roughness
Understanding the mathematical foundations of roughness is essential in conducting accurate surface analysis. This knowledge allows scientists and engineers to quantify surface characteristics, leading to enhanced performance in various applications. By applying mathematical principles, researchers can derive meaningful insights from roughness measurements that inform both design and manufacturing processes.
Geometric Parameters of Surface Roughness
In surface metrology, geometric parameters play a crucial role in defining the characteristics of roughness. The most widely used geometric parameters include:
- Arithmetic Average Roughness (Ra): This is the average of the absolute heights of the profile irregularities over a specified surface length. Ra is typically easy to measure and provides a quick indication of overall roughness.
- Peak-to-Valley Height (Rz): This measures the vertical distance between the highest peak and the lowest valley in the surface profile. Rz is particularly notable when assessing surfaces that require specific threshold tolerances.
- Root Mean Square Roughness (Rq): This parameter reflects the root mean square value of the height deviations from the mean line. Rq tends to be more sensitive than Ra and is useful for deeper insights into the surface texture.
The selection of these geometric parameters should align with the intended application. For instance, in semiconductor manufacturing, a low Ra value is critical for establishing optimal adhesion and performance. On the other hand, Rz might be prioritized in tribological applications where friction and wear are the main concerns.
Statistical Methods in Analysis
Statistical methods are indispensable for analyzing roughness data effectively. They provide tools to interpret data sets and to assess the variability inherent in surface measurements.
Some key statistical techniques include:
- Mean and Median Calculation: These simple measures assist in understanding the central tendency of the roughness values.
- Standard Deviation: This metric evaluates the spread of the roughness measurements, supplying insights into the consistency of the surface texture.
- Histograms: A graphical representation of roughness data, histograms can be used to visualize the distribution of surface heights, assisting researchers in identifying patterns or anomalies.
Additionally, with advancements in technology, statistical analysis also incorporates software tools that can conduct complex calculations and simulations. This not only enhances precision but also makes data interpretation more accessible to researchers and practitioners alike.
"Mathematical principles are the backbone of effective surface roughness analysis, enabling definitive conclusions drawn from empirical data."
Common Roughness Parameters
Common roughness parameters serve as fundamental metrics to evaluate and quantify surface texture. Understanding these parameters is crucial in many fields, including material science, engineering, and manufacturing. Each parameter provides meaningful insights that can inform production processes and quality control measures. They help in assessing how surfaces interact in applications ranging from mechanical systems to electronic devices.
Roughness parameters not only offer a method for consistent quantification but also enable comparisons across different materials and surfaces. They ensure that products meet required specifications and performance criteria. Let's examine some of the most recognized roughness parameters: Ra, Rz, and Rq.
Ra (Arithmetic Average Roughness)
Ra, or arithmetic average roughness, is one of the most widely used indices for surface texture assessment. It represents the average deviations of the surface profile from the mean line over a certain sampling length. The calculation is straightforward: sum the absolute values of the deviations and divide by the number of sample points. This parameter is widely used due to its simplicity and effectiveness in capturing general roughness, making it a reliable choice in many engineering contexts.
However, while Ra is useful, it may not fully represent all surface irregularities, especially in highly textured surfaces where peaks and valleys are pronounced. Thus, it should be considered alongside other roughness parameters for a more comprehensive analysis.
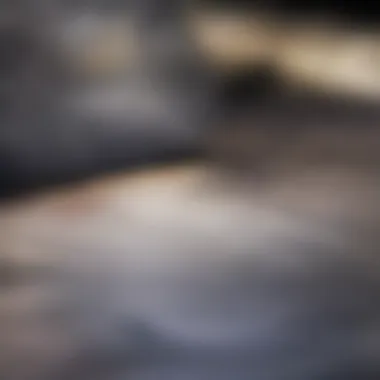
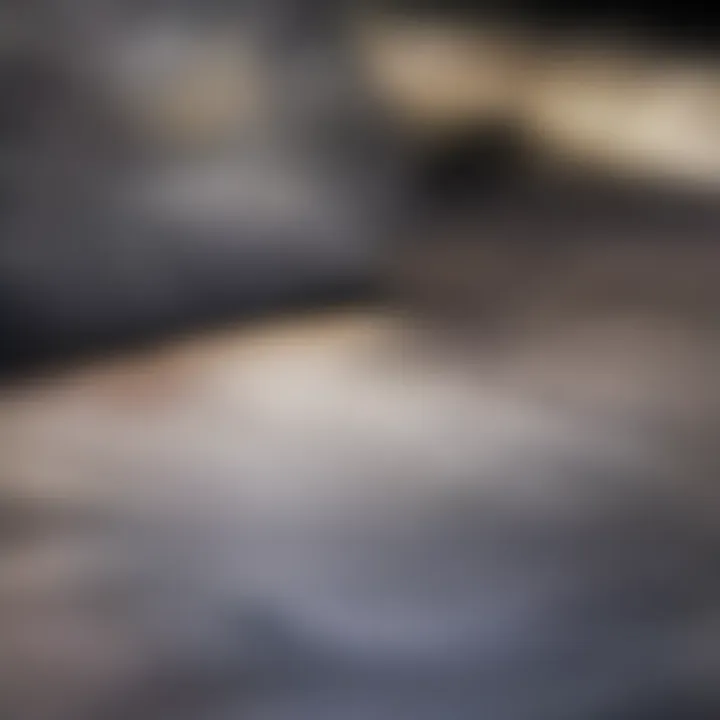
Rz (Average Maximum Height)
Rz calculates the average maximum height of the profile from the highest peak to the lowest valley within a specified sampling length. This measurement gives a more significant representation of the overall roughness than Ra. Rz is beneficial in scenarios where extreme values are of greater concern, such as in wear and friction applications.
By emphasizing the extremes of the surface profile, Rz helps in applications where surface contact quality or load-bearing capacity is critical. Despite its strengths, this parameter can also be influenced by outliers, which may skew the insights it offers.
Rq (Root Mean Square Roughness)
Rq, or root mean square roughness, is another important metric used to assess surface texture. Unlike Ra, Rq takes into account the square of the deviations from the mean line, which means it gives more weight to larger deviations. This characteristic makes Rq a valuable parameter when evaluating surfaces that require fine precision and where larger surface features can dramatically affect performance.
The formula for Rq provides a deeper view of the surfaceβs characteristics, thus enhancing the accuracy of roughness evaluations. However, similar to Ra and Rz, it has its limitations, and practitioners often utilize Rq in conjunction with other parameters to achieve the most accurate characterization of surface roughness.
Understanding these roughness parameters helps engineers and researchers optimize materials for specific applications, influencing product performance and longevity.
Measurement Techniques
Measurement techniques play a pivotal role in the quantification of surface roughness. These methods not only define the effectiveness of measurements but also impact the accuracy and reliability of the data collected. Different techniques suit various materials and applications, making the choice of methodology crucial. The importance of measurement techniques lies in their ability to provide insights and enhance understanding of material behavior under different conditions.
Contact Profilometry
Contact profilometry is a traditional method of measuring surface roughness. In this technique, a stylus moves across the surface, tracing its topography. As the stylus traverses, it records the vertical displacements, allowing for a detailed analysis of surface variations.
Benefits of contact profilometry include:
- High accuracy and resolution.
- Ability to measure various types of surfaces, including soft materials.
However, there are considerations to keep in mind. Contact profilometry may not be suitable for delicate surfaces, as the pressure applied by the stylus could deform or damage the material. Additionally, this method can be relatively slow compared to non-contact techniques.
Non-Contact Profilometry
Non-contact profilometry employs optical or laser-based techniques to measure surface roughness without physical contact. This method is advantageous for assessing delicate or soft materials where contact might cause damage. Non-contact systems use light reflection or scanning lasers to capture surface profiles.
Advantages include:
- No risk of surface damage.
- Faster data acquisition.
- Capability to gather data over large areas.
Despite these benefits, non-contact methods may be influenced by surface conditions, such as reflectivity and transparency. Thus, proper calibration is necessary to obtain reliable results.
Atomic Force Microscopy (AFM)
Atomic Force Microscopy offers high-resolution imaging and surface analysis at the nanoscale. AFM uses a cantilever with a sharp tip that senses forces between the tip and the surface atoms, providing topographic information with exceptional precision.
The primary strengths of AFM include:
- Ability to measure roughness at the atomic level.
- Functionality in various environments, including liquid and air.
- Capability to study a wide range of materials.
Nonetheless, the complexity of AFM techniques requires skilled operation and interpretation of results, making it more suitable for specialized applications.
Optical Techniques
Optical techniques for measuring surface roughness utilize principles of light, such as interferometry and reflectometry. These approaches analyze light waves reflected from a surface to determine roughness parameters accurately.
Key advantages of optical techniques include:
- Non-invasive nature, preventing any surface alteration.
- High-speed measurements suitable for large-area assessment.
- Ability to gather comprehensive data regarding surface features.
However, optical methods may be limited by conditions such as surface cleanliness and geometry, which can interfere with light paths and affect measurement accuracy. Ensuring adequate surface conditions is essential for reliable data acquisition.
In summary, each measurement technique offers unique benefits while posing specific challenges. Understanding these aspects is vital for selecting the appropriate method to achieve accurate roughness calculations.
Applications of Roughness Calculation
Understanding surface roughness is vital across various domains. The analysis of roughness has multiple applications that influence both research and practicality in many fields. This section elucidates the significance of roughness calculation, focusing on material science, tribology, and semiconductor manufacturing.
Material Science and Engineering
In material science, surface roughness plays a pivotal role. Rough surfaces can significantly affect material properties such as adhesion, friction, and wear resistance. For instance, roughness influences how coatings adhere to substrates. A surface with high roughness may improve bonding but could also lead to weak points where the coating may peel or chip.
Moreover, in engineering applications, understanding roughness is crucial when predicting the performance and lifespan of components. Rougher surfaces may lead to increased wear in mechanical assemblies. It is essential to balance roughness to achieve desired performance outcomes while maintaining durability.
Advancements in materials often require precise control over surface characteristics. Researchers regularly explore surfaces at micro and nano levels to understand better how these features affect overall material behavior. This investigation helps drive innovation in engineering solutions.
Tribology and Wear Analysis
Tribology, the study of friction, lubrication, and wear, significantly relies on accurate roughness measurements. The interaction between surfaces during contact can greatly influence frictional forces. Specifically, the roughness of surfaces can cause variations in friction behavior that are critical to predict.
Wear analysis involves studying how surfaces deteriorate during operational conditions. Substantial roughness can enhance wear, impacting operational efficiency and leading to increased maintenance costs. Understanding the roughness profile assists in predicting how materials will behave under specific load conditions. It also helps design components that utilize lubrication more effectively, which can reduce wear and extend their lifespan.
For example, in testing lubricants, the roughness of the tested surfaces plays a crucial role in determining the effectiveness of the fluid. Efficient analysis allows for optimizing lubricant formulations to match surface characteristics, giving a performance edge.
Semiconductor Manufacturing
In semiconductor manufacturing, surface roughness directly affects the functional properties of electronic devices. As device components get smaller, surface irregularities become critical. Excessive roughness can lead to problems in device performance, causing issues such as electrical resistance and reliability.
Precision in roughness measurements during the manufacturing process allows for better control over the final product quality. Engineers and scientists focus on maintaining optimal roughness levels to ensure the performance meets stringent requirements.
Features on semiconductor wafers must often be in the nanometer range. Any irregularities can severely impact the functioning of transistors and other microelectronic devices. Thus, thorough roughness calculations and surface analysis methods are indispensable in the development of next-generation semiconductors.
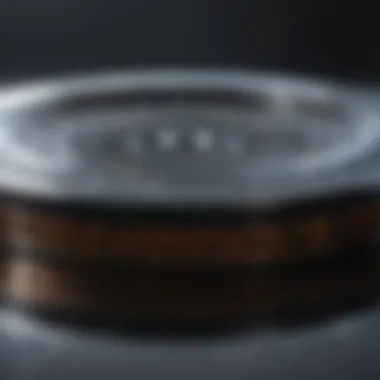
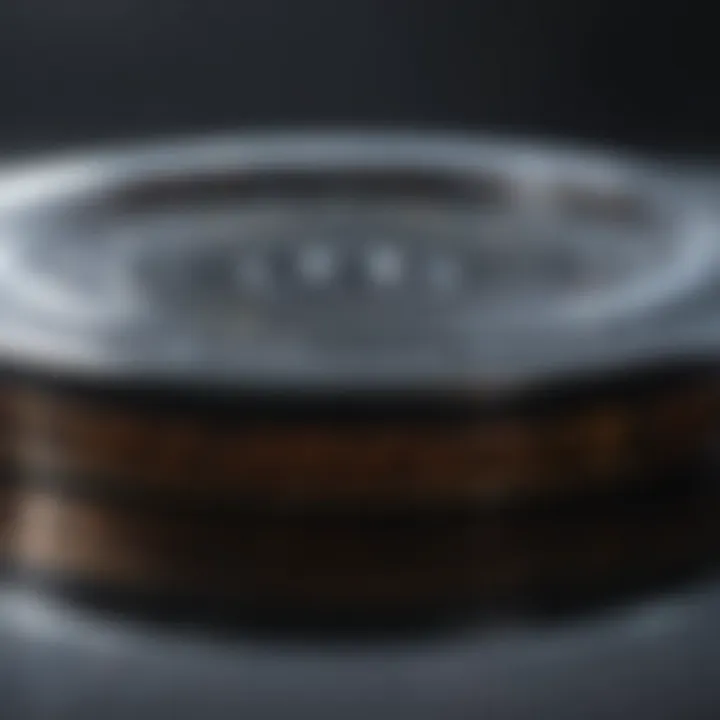
In summary, applications of roughness calculation span crucial fields like material science, tribology, and semiconductor manufacturing. Understanding and controlling surface roughness is essential for enhancing performance, reliability, and longevity across various technologies.
Standardization and Best Practices
Standardization and best practices in roughness calculation play a crucial role in ensuring the accuracy, reliability, and consistency of measurement results. The variability in surface roughness across industries necessitates clear guidelines that practitioners can follow. Such standardization helps harmonize methods and contributes to better communication of results among researchers and professionals. It further reduces potential errors, allowing for seamless comparisons in the scientific and engineering communities.
One of the main benefits of adopting standard practices is improved quality control. Industries that rely on precise surface characteristics, such as aerospace and semiconductor manufacturing, benefit significantly from following established standards. Consistent measurements can directly impact product performance. For instance, in tribology, the wear and friction properties of surfaces can vary widely with roughness parameters, making standardization imperative for predictability in material behavior.
Moreover, organizations can achieve compliance with international quality standards, thereby enhancing their global competitiveness. Key points to consider about standardization in this field include:
- Clarity in communication regarding surface characteristics.
- Reduction of discrepancies in measuring techniques across different laboratories.
- Enhancement of product reliability through known roughness specifications.
- Facilitation of cross-industry collaborations and partnerships.
- Supporting regulatory compliance aimed at public safety and product quality.
ISO Standards on Surface Roughness
The International Organization for Standardization (ISO) has established a range of standards that pertain specifically to surface roughness measurement. ISO 4287 and ISO 4288 are foundational documents that offer guidelines for roughness parameters and their assessment. These standards provide definitions and methods for measuring roughness, ensuring that practitioners are equipped with a consistent framework for conducting their analyses.
Understanding these ISO standards is essential for anyone involved in surface measurement as they dictate the terminologies and methodologies used globally. They set benchmarks for roughness evaluation, which can help in conducting meaningful comparisons between studies or products. By following these standards, those in research and industry can ensure that their findings are credible and recognized across different disciplines.
Some key elements of the ISO standards include:
- Specific parameters to measure, such as Ra, Rz, and Rq.
- Guidelines for the setup and calibration of measuring equipment.
- Recommendations for sample preparation to minimize variabilities.
Quality Control in Production
In the context of production, quality control plays an integral role in maintaining product standards, particularly in industries where surface texture is paramount. Uncontrolled surface roughness can lead to defects in products, resulting in a high rate of rejection and increased costs. By implementing rigorous quality control measures that adhere to standard practices, manufacturers can effectively minimize these risks.
Quality control in roughness measurement often involves:
- Periodic audits of measurement processes to ensure compliance with ISO standards.
- Essential calibrations and maintenance check-ups of measurement instruments.
- Training for operators to understand the significance of accurate roughness data.
Effective quality control can lead to improved customer satisfaction, as products meet the desired specifications consistently. Moreover, it allows industries to develop a clear understanding of how surface roughness affects performance factors like friction and wear, ultimately aiding in the creation of more performant materials.
Regular audits and adherence to ISO standards are not just best practices; they are essential for maintaining product integrity and customer trust in today's competitive market.
Implementing these techniques and standards is crucial not only for the mechanical performance of components but also for the longevity and reliability of the materials used in various applications.
Challenges in Roughness Calculation
Roughness calculation presents several challenges that researchers and professionals must navigate to ensure accurate measurements. These challenges are critical in understanding surface characteristics and play an essential role in various fields such as material science, engineering, and manufacturing. Accurate roughness calculations not only affect product quality but also influence performance and longevity of materials in applications. Addressing these hurdles is necessary for achieving reliable results and improving methodologies.
Measurement Uncertainties
Measurement uncertainties are a significant concern in roughness calculation. Various factors contribute to these uncertainties, such as the choice of measurement technique, the condition of the measuring instrument, and environmental influences. For instance, instruments like contact profilometers might suffer from wear or calibration issues leading to deviations in readings. Consequently, this can result in inconsistent roughness values, hindering the interplay between design and production processes.
In addition, the surface conditions themselves can impact measurements. Dust, oil, or other contaminations on a surface can alter its expected roughness profile. It is crucial to maintain a clean environment and proper surface treatment before conducting measurements. Real-time monitoring systems, along with robust calibration procedures, may mitigate these uncertainties, leading to improved data reliability.
"Consistent measurement techniques are essential in mitigating uncertainties."
Implementing precise protocols helps establish confidence in roughness data. This ultimately supports quality control measures in industrial settings. It will also allow researchers to refine experimental design and data interpretation. Thus, understanding and addressing measurement uncertainties is vital.
Surface Anisotropy Issues
Surface anisotropy issues further complicate roughness calculations. Anisotropy refers to the directional dependence of a surface's texture. Different measurements along various axes may yield different roughness parameters, making it challenging to derive a single representative value. Materials often exhibit different characteristics based on how they were processed or finished, adding layers of complexity to analysis.
Additionally, for applications requiring precision, such as semiconductor manufacturing, ignoring surface anisotropy can lead to performance failures in the final product. Traditional metrics like Ra (arithmetic average roughness) do not account for these directional differences adequately. Therefore, it is vital to adopt advanced metrics to capture the true nature of the surface.
Researchers may employ techniques such as 3D surface topography analysis to evaluate anisotropy more effectively. Various software tools are available to assist in analyzing and interpreting complex surface profiles. By taking into account surface anisotropy, one can achieve a more profound understanding of how surface texture influences the overall performance of a material.
In summary, both measurement uncertainties and surface anisotropy are challenges that require thoughtful approaches and careful methodologies in roughness calculations. Through addressing these factors, industries and researchers can secure more reliable results, enhancing the reliability and performance of materials across applications.
Advanced Techniques in Surface Analysis
Advanced techniques in surface analysis provide deeper insights into surface characteristics that traditional methods may overlook. These techniques significantly enhance the understanding of surface roughness by offering greater precision and detail. They are crucial for applications in fields such as material science, engineering, and semiconductor manufacturing, where the performance of surfaces can profoundly impact overall functionality and durability.
Adopting advanced methods allows researchers and practitioners to observe surface features at the micro and nano scales. With the rise of technologies like laser scanning confocal microscopy and scanning electron microscopy, accurate characterization of surfaces becomes more feasible. Furthermore, these techniques often reveal not only the topographical details but also other physical attributes, such as chemical composition or material properties.
However, challenges remain. The complexity of these methods often requires specialized training and equipment, which might not be accessible to all. Additionally, the interpretation of data obtained from these analyses can demand sophisticated modeling and expertise. Despite these considerations, the benefits of using advanced techniques outweigh the drawbacks, hence their growing importance in contemporary research and practical applications.
Laser Scanning Confocal Microscopy
Laser scanning confocal microscopy (LSCM) is a powerful imaging technique that utilizes laser light to scan surface features. By focusing on a particular point on the surface and collecting emitted light, LSCM generates high-resolution 3D images of surfaces. This capacity is vital in measuring surface roughness as it offers precise depth control and minimizes optical aberrations common in conventional microscopy.
Key advantages of LSCM include:
- High Resolution: Capable of imaging down to the nanometer scale.
- Non-Destructive: The method does not alter or damage surfaces during analysis.
- 3D Imaging: Allows visualizing surface morphology in three dimensions, providing a clearer understanding of roughness profiles.
In applications like biology or materials science, LSCM serves an essential role in surface topography studies. It enables detailed exploration of cellular structures, thin films, and coatings, illustrating its versatile nature.
Scanning Electron Microscopy (SEM)
Scanning electron microscopy (SEM) is another advanced technique pivotal for surface analysis. It utilizes focused beams of electrons to scan a specimen, producing detailed images based on electron interactions. SEMβs high magnification capabilities grant a unique perspective on surface features, which can be critical when evaluating material properties.
Benefits of SEM include:
- Magnification: Offers up to 1,000,000x magnification, revealing intricate surface details.
- Elemental Analysis: Coupled with energy-dispersive X-ray spectroscopy, it can provide chemical composition information.
- Surface Imaging: Capable of recognizing surface textures and defects, assisting in quality control in manufacturing.
This technique is extensively used in semiconductor manufacturing, material failure analysis, and nanotechnology research. SEM can reveal information that supports development and refinement of processes and products.
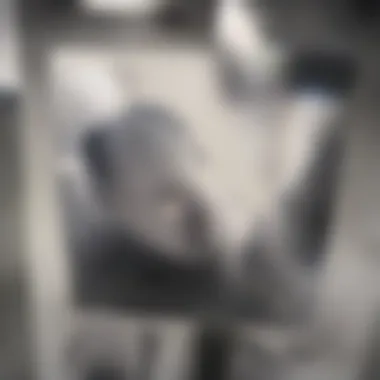
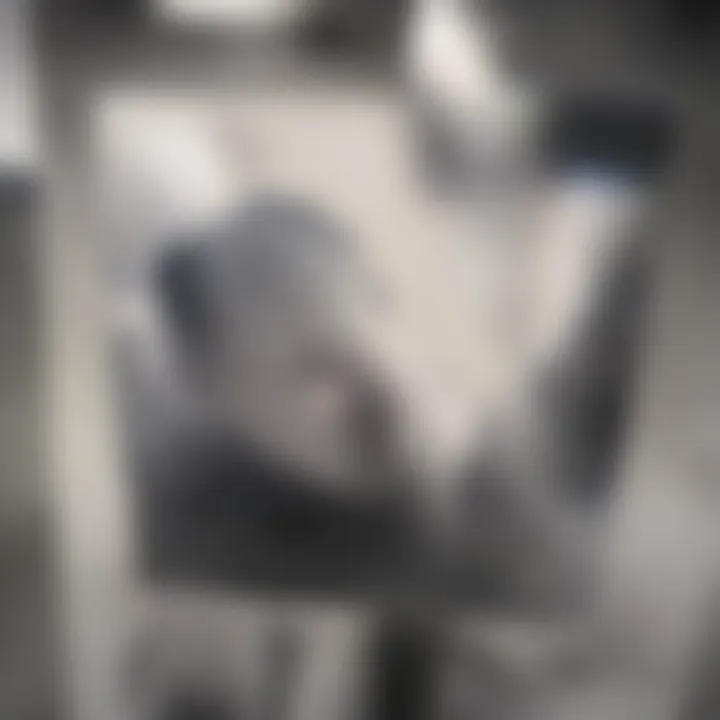
"Advanced techniques such as LSCM and SEM are reshaping our understanding and manipulation of materials at a fundamental level."
Embracing these methods in surface analysis allows scientists and engineers to achieve unprecedented levels of detail and accuracy. Understanding the nuances of surface roughness becomes less of a mystery and more of a clear pathway toward innovation.
Emerging Trends in Roughness Measurement
Emerging trends in roughness measurement highlight the dynamic nature of surface analysis. Understanding these trends is critical as they serve to enhance accuracy and efficiency in various fields such as material science, automotive, and aerospace industries. The integration of new technologies and methodologies into roughness measurement represents a significant shift in how properties of surfaces are quantified. As these innovations unfold, they present both benefits and considerations.
Integration of AI and Machine Learning
Artificial Intelligence (AI) and machine learning are revolutionizing roughness measurement. The application of these technologies allows for the analysis of large datasets, uncovering complex patterns that traditional methods might overlook. By utilizing machine learning algorithms, researchers can enhance predictive models, improving the accuracy of roughness assessments.
- Data Analysis: AI can process vast amounts of data quickly, providing insights into surface characteristics that can lead to better material formulations.
- Predictive Modeling: Machine learning aids in developing predictive models based on historical roughness data, allowing for informed decision-making.
- Automation: The automation of roughness measurement processes reduces human error and increases reproducibility in results.
The benefits of integrating AI and machine learning extend beyond efficiency. They also promote innovation in how roughness metrics are defined and utilized, encouraging the exploration of new metrics that reflect the nuances of surface characteristics.
Real-Time Surface Characterization
Real-time surface characterization represents another significant trend in roughness measurement. The ability to assess surface properties as they are being fabricated reduces delays in production and increases the overall quality of the finished product.
- Immediate Feedback: Real-time data allows for immediate adjustments during manufacturing processes, reducing defects related to surface imperfections.
- Improved Processes: Continuous monitoring helps identify issues early, leading to improvements in workflow and productivity.
- Enhanced Quality Control: Incorporating real-time measurements supports enhanced quality control measures, which is crucial for industries that demand tight tolerances, such as semiconductor manufacturing.
Real-time characterization in the manufacturing process not only enhances quality but also sets a new benchmark for efficiency in production cycles.
These emerging trends in roughness measurement reflect the evolving landscape of technology and its application in surface science. As advancements continue, it is essential to stay informed on how these changes can lead to more robust analysis methods and improved outcomes in research and practical applications.
Case Studies and Practical Examples
Case studies serve as vital components in understanding the practical applications of roughness calculation across various industries. They provide concrete instances that demonstrate how theoretical principles are applied in real-world situations. By analyzing these examples, students, researchers, educators, and professionals can grasp the complexities and nuances involved in surface roughness measurement. Case studies not only illustrate the methods employed but also highlight the outcomes achieved, limitations encountered, and lessons learned. Each example offers unique insights that can contribute to improving measurement techniques and application strategies.
The benefits of case studies in this context are manifold:
- Demonstration of Real-World Applications: They show how roughness calculations influence design and manufacturing decisions, particularly in high-stakes industries like aerospace and automotive.
- Insight Into Challenges and Solutions: They outline specific challenges associated with surface roughness and how they have been addressed, providing a learning opportunity for others in the field.
- Evidence-Based Learning: Case studies support evidence-based conclusions about the effectiveness of different roughness measurement techniques and metrics.
Considering these elements, a closer examination of prominent case studies in both aerospace and automotive industries will shed light on the valuable role of roughness calculation in these fields.
Case Study in Aerospace Applications
The aerospace industry has stringent requirements for surface quality, where even minor deviations can affect the performance and safety of aircraft. A notable case study involved the analysis of turbine blades used in jet engines. In this area, roughness measurements are critical for ensuring optimal aerodynamic performance and fuel efficiency.
Using advanced techniques such as Laser Scanning Confocal Microscopy, the roughness of the blade surfaces was meticulously measured. The focus was on parameters like Ra, Rz, and Rq which revealed insights into material wear over time. An important finding from the study indicated that a lower roughness profile directly correlated with increased turbine efficiency.
Moreover, the study highlighted challenges such as environmental factors affecting surface characteristics during the manufacturing and testing phases.
Automotive Industry Insights
Similarly, the automotive industry frequently assesses surface roughness for various components, including bearings and engine parts. A specific case study concerning critical engine components revealed how precise roughness calculations contribute to reducing wear and improving performance.
By utilizing Contact Profilometry, engineers obtained detailed roughness profiles of engine cylinder liners. This meticulous analysis helped to recognize the manufacturing inconsistencies that could lead to premature engine failure. The study emphasized the necessity of adhering to stringent ISO standards for surface measurement in production processes.
In terms of impact, the results of this case indicated that regulating surface roughness not only enhanced operational efficiency but also extended product longevity.
In summary, case studies in aerospace and automotive sectors underscore the profound implications of roughness calculation on both performance and reliability. They serve as powerful examples for industry professionals, demonstrating the effectiveness of meticulous surface analysis and encouraging ongoing improvements in measurement practices.
Future Directions in Roughness Research
Understanding future directions in roughness research is critical, as it shapes the trajectory of surface analysis. The advancements in measurement techniques and evolving metrics can lead to improved precision in various applications, from materials science to manufacturing. This section highlights these innovations and explores the potential impact they may have.
Potential Innovations in Measurement Techniques
Advancements in technology continue to redefine how surface roughness is measured. Current techniques, while effective, often come with limitations in terms of resolution and reliability. Future innovations might integrate the use of advanced sensors and high-resolution imaging systems, which promise to enhance measurement accuracy.
- 3D Surface Profiling: Innovations focusing on three-dimensional surface profiling could allow for more detailed analyses. Traditional methods often rely on two-dimensional measurements, lacking depth information.
- Nanotechnology Applications: Employing nanotechnology can potentially revolutionize roughness measurement. Nanoscale sensors may provide high precision and sensitivity, surpassing current topographical mapping techniques.
- Real-Time Monitoring: The integration of smart technologies like IoT could enable real-time surface analysis, allowing for immediate adjustments during manufacturing processes.
- Machine Learning Enhancements: Machine learning algorithms can analyze complex datasets quicker than manual processing. They can improve the identification of patterns in surface roughness data, facilitating better predictions and quality control.
These innovations mark a trend towards higher efficiency and accuracy in roughness calculations, emphasizing the need for continuous development in measurement techniques.
Exploration of New Roughness Metrics
As the field of surface analysis evolves, so does the necessity for novel roughness metrics. Existing parameters may not capture the full complexity of surface textures, highlighting the need for fresh perspectives in quantifying roughness.
- Multi-Scale Measurements: Developing metrics that can evaluate roughness across multiple scales may provide a more comprehensive understanding of surface characteristics. This can be particularly beneficial in industries where minute details significantly impact performance.
- Dynamic Metrics: New metrics could focus on dynamic changes in surface roughness under various conditions. Evaluating how surfaces behave under stress, pressure, or temperature variations adds another layer of understanding.
- Customized Metrics for Specific Applications: Tailoring roughness metrics to suit specific applications could enhance their efficacy. For instance, metrics designed exclusively for aerospace could provide insights more relevant to that industry, boosting performance evaluations.
- Integrating Data from Different Techniques: A holistic approach to roughness metrics might involve integrating data from various measurement techniques to develop a unified metric. This could enhance accuracy and provide a multidimensional perspective on surface roughness.
"The future of roughness measurement lies in the blend of advanced technologies and novel metrics, guiding us towards unprecedented precision in surface analysis."
End
In the context of this article, the conclusion serves as a vital synthesis of the discussions held throughout the various sections. It encapsulates the essence of roughness calculation as a fundamental aspect of surface analysis, reinforcing its relevance across multiple disciplines. The significance of this topic extends beyond mere measurement; it influences the understanding of material properties, manufacturing processes, and technological innovations.
The benefits of a thorough comprehension of roughness calculation are manifold. For researchers, it provides a robust framework for exploring new materials and their applications. Understanding the nuances of surface roughness can lead to optimization in diverse fields such as material science, semiconductor manufacturing, and tribology, thereby increasing efficiency and enhancing product performance. Moreover, standardized approaches to roughness measurement aid in quality control and assurance, ensuring that the products meet expected specifications.
Furthermore, the conclusion invites ongoing consideration of future implications in the field of roughness research. To truly grasp its potential, continued exploration into evolving techniques and metrics is essential. As technology advances, so will the ability to analyze and interpret roughness in ways that were previously unimagined, providing fertile ground for innovative research.
Summary of Key Points
- Roughness calculation is crucial in various scientific fields, including material science and engineering.
- Different methods such as contact and non-contact profilometry, and atomic force microscopy, offer unique insights into surface characteristics.
- Understanding parameters like Ra, Rz, and Rq is essential for accurate surface analysis.
- Standardized practices and ISO standards play a significant role in quality control.
- Emerging technologies, including AI and machine learning, are set to revolutionize the approach to surface roughness measurement.
Implications for Future Research
As we look to the future, the implications of roughness research become increasingly compelling. There are several areas for potential growth:
- Innovative Measurement Techniques: The exploration of advanced tools and methodologies can lead to more precise surface analysis.
- New Roughness Metrics: Developing new metrics for characterizing surface textures can enhance our understanding and application of materials in practical scenarios.
- Interdisciplinary Collaborations: Engaging with diverse scientific fields can provide richer data and insights, fostering advancements in technology and material design.
- Continued Integration of AI: Leveraging artificial intelligence can optimize measurement processes and data interpretation, leading to faster advancements in surface analysis.
In summary, the exploration of roughness calculation will undoubtedly continue to evolve, making it essential for academics, practitioners, and industry leaders to stay informed and engaged with these developments.