Thin Film Adhesion: Comprehensive Analysis and Insights
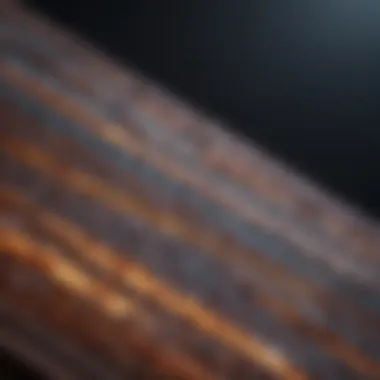
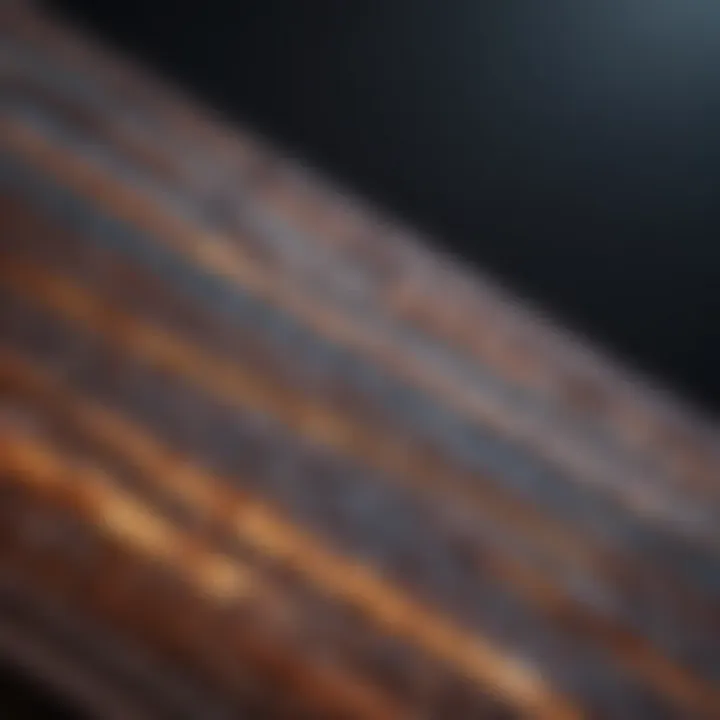
Intro
In the intricate world of materials science, the adhesion of thin films plays a pivotal role in numerous applications—from semiconductor devices to optical coatings. Understanding the mechanisms that govern how these films bond to their substrates is no trivial task. Just as glue does more than simply hold two objects together, thin film adhesion involves a delicate interplay of physical forces, chemical compositions, and microscopic structures.
Acquiring a solid grasp of thin film adhesion means stepping into a zone where physics meets engineering. This is not just about sticking materials together; it's a fundamental aspect of material performance in real-world applications. As industries demand more efficient and effective materials, the significance of adhesion cannot be overstated. Each of the myriad applications, whether in electronics, coatings, or nanotechnology, relies heavily on how well those thin films adhere.
In this article, we delve further into the complexities of thin film adhesion. By breaking down key findings, exploring methods of analysis, and assessing practical implications, we aim to equip both novices and seasoned professionals with a thorough understanding of this critical area of study.
Prelims to Thin Film Adhesion
Thin film adhesion is a crucial aspect of material science that significantly impacts various industries, including electronics, coatings, and energy systems. Understanding how thin films adhere to substrates not only enhances product reliability but also expands the potential for innovative applications. The discussion around thin film adhesion encompasses multiple fields, blending physics, chemistry, and engineering principles. This intersection creates potent opportunities for advancements in technology, driving both academic research and industrial applications.
Evaluating the adhesion properties of thin films involves understanding the forces at play and the mechanisms that ensure a robust bond between materials. As the demand for lighter, more efficient products grows, proper adhesion becomes paramount. Enhanced adhesion can lead to improvements in performance, longevity, and overall functionality of various devices.
This article dives deep into the nuances of thin film adhesion, offering insights that address both fundamental theories and practical applications. It serves as a vital resource for students, researchers, and professionals alike, facilitating a richer comprehension of this complex topic. By delving into the fundamental concepts and practical implications, we aim to enhance knowledge among our target audience, ensuring a thorough understanding of why this field is not just academic but crucial for modern technological advancements.
Defining Thin Film and Adhesion
Thin films are layers of material ranging from fractions of a nanometer to several micrometers in thickness. They are applied to substrates for various reasons, including enhancing surface properties, altering optical or electrical characteristics, or providing protective barriers. Thin films can be composed of metals, oxides, polymers, and other materials, each offering unique properties based on their composition and structure.
Adhesion, on the other hand, refers to the tendency of dissimilar particles or surfaces to remain in contact with each other. The strength of adhesion can be affected by various factors, including surface cleanliness, roughness, and the chemical nature of the substrates. A robust adhesion mechanism ensures that thin films perform as intended without delaminating or failing under stress.
Understanding the principles of thin film and adhesion involves examining the molecular and atomic interactions at interfaces. This holistic perspective not only helps in selecting appropriate materials for specific applications but also in predicting their behavior under different conditions.
Historical Context of Thin Film Applications
The journey of thin films began centuries ago, with the exploration of materials that could control optical properties, such as iridescence in soap bubbles. As technology advanced, the development of thin films gained significant momentum, particularly in the 20th century when vacuum deposition methods and chemical vapor deposition (CVD) were perfected. These innovations expanded the applications of thin films from decorative and optical uses to electronics and protective coatings.
In electronics, the advent of integrated circuits in the 1960s marked a turning point. Thin films enabled miniaturization, paving the way for the modern computing era. Similarly, protective coatings have evolved with advancements in material science, providing enhanced moisture resistance and durability for various applications.
Throughout history, the development and application of thin films have mirrored technological advancements and societal needs. From initial decorative uses to essential components in modern electronics and material solutions, the field of thin film adhesion reflects a blend of creativity, engineering, and science that continues to evolve.
"The application of thin films has transformed industries, highlighting the intricate balance between materials science and practical engineering solutions."
This section sets the stage for a deeper dive into the fundamental concepts, materials, and testing methods necessary to understand thin film adhesion comprehensively.
Fundamental Concepts
The study of thin film adhesion revolves around certain key concepts that lay the groundwork for understanding how and why materials stick together at the microscopic level. These concepts are not just trivial; they inform the engineering designs and applications of thin films across a range of industries. Knowing these principles helps in making informed decisions about material choices, ensuring successful outcomes in real-world applications.
Physical Principles of Adhesion
Adhesion itself is a complex phenomenon influenced by various physical interactions. This section elaborates on the main principles that govern adhesion in thin films:
Mechanical Interlocking
Mechanical interlocking occurs when the surface roughness of a substrate creates physical bond points for the adhesive layer. This type of adhesion plays a significant role in applications where solid holds are paramount. The ability of an adhesive to grip onto tiny indentations or protrusions contributes directly to the strength of the bond.
One critical aspect of mechanical interlocking is the disparity in surface profiles. Surfaces that are rough can substantially outperform smooth surfaces when it comes to obtaining a strong hold. Think of it as how a hand grabs onto a crumpled piece of paper more effectively than onto a flat piece; the nuances in texture provide grip in ways that smooth contact simply cannot.
However, there are some drawbacks. For instance, the initial surface preparation costs can be high due to the need for specialized treatments to achieve the necessary roughness.
Chemical Bonding
Chemical bonding refers to the formation of chemical attachments between the thin film and the substrate. This type of adhesion is pivotal in various high-tech applications and provides remarkable bond strength that mechanical interlocking may not achieve on its own.
A key characteristic of chemical bonding is that it translates into much stronger overall adhesion. Unlike merely interlocking surfaces, chemical bonds can create a much more enduring connection through underlying molecular interactions. For instance, silane coupling agents are often used in coating applications, bridging the gap between inorganic surfaces and organic coatings.
But like any method, there are trade-offs too. The conditions under which chemical bonds form, like temperature and humidity, can make a significant difference.
Van der Waals Forces
Van der Waals forces constitute a different yet equally important mechanism of adhesion. These are weak intermolecular forces that, while not producing the same strength as chemical bonds, can still be crucial for thin film applications. They arise from transient dipoles that result in small but pervasive attractions between molecules.
The unique feature of Van der Waals forces is their ubiquity in nature. They are present in almost all materials and environments, making them relevant across a wide range of applications. This means that even a relatively smooth surface can still achieve some level of adhesion by van der Waals attractions.
Yet, the strength of these forces can also be a double-edged sword. For some applications, relying on Van der Waals forces alone may present challenges in terms of long-term durability.
Types of Thin Films
Thin films come in various forms, each tailored for specific functions. Understanding the differences between thin film types is crucial for selecting the best option for a intended application:
Metallization Films
Metallization films address the need for electrical conductivity in devices. These films enable the efficient transfer of electrical signals and provide a conducive path for current to travel. Typically, metals like aluminum or copper are used because of their superior conductivity.
The standout characteristic of metallization films is their ease of deposition on substrates. Processes like physical vapor deposition (PVD) can create a uniform metal layer quickly and efficiently. However, these films often need to be carefully managed, as they can be quite sensitive to oxidation, which can degrade their properties over time.
Dielectric Coatings
Dielectric coatings serve a contrasting purpose by providing insulating properties. They are used primarily to thwart electrical conduction while maintaining transparency in applications like capacitors and insulators. Materials such as silicon dioxide are common choices for these coatings.
Their significant characteristic is high dielectric strength, which is essential in high-voltage environments. However, while offering insulation, these materials can be brittle and prone to mechanical failure under stress.
Polymeric Layers
These layers come into play when flexibility and resilience are needed. Polymeric thin films can be tailored for a range of applications from protective coatings to flexible electronics. They are often more forgiving than metallic or dielectric thin films, offering advantages in terms of shock absorption and impact resistance.
However, their temperature sensitivity may present limitations. Polymeric films can deteriorate under high temperatures, affecting adhesion and overall product longevity.
In summary, understanding fundamental concepts related to thin film adhesion not only enables better material choices but also informs better engineering techniques in various applications. Each type of adhesion mechanism and thin film serves its own purpose, contributing uniquely to performance and reliability in technology.
Materials Used in Thin Films
Understanding the materials utilized in thin films is fundamental to grasping the broader complexities of adhesion phenomena. Thin films are integral to an array of modern applications, spanning electronics to coatings and energy devices. The selection of appropriate materials not only influences adhesion strength but also the overall performance of the final product. Various factors must be considered, such as mechanical resilience, thermal stability, and compatibility with substrates. Thus, dissecting the materials provides insights into their specific roles, benefits, and the considerations necessary for optimized use in thin film technologies.
Common Substrates for Thin Films
Silicon
Silicon is often regarded as the backbone of the semiconductor industry. Its semiconductive properties make it a popular choice in electronics, where thin films are applied to create integrated circuits and various microelectronic devices. A standout characteristic of silicon is its natural oxide layer, which provides excellent adhesion for subsequent films. This unique feature advantages silicon by enhancing stability while allowing for effective electrical performance in many applications. However, one must note that silicon's thermal expansion coefficient may pose challenges, particularly under varying temperature conditions, leading to potential stress in multilayer systems.
Glass
In the world of optics and display technologies, glass frequently takes center stage as a thin film substrate. Its transparency and chemical inertness make it highly suitable for optical coatings, allowing for high-performance outcomes in devices like screens and lenses. An essential characteristic of glass is its smooth surface, enhancing adhesion properties for films applied on top. This smoothness facilitates a stronger bond, leading to exceptional durability. However, the brittleness of glass is a concern when it comes to handling and potential impacts, necessitating careful application in sensitive environments.
Metals
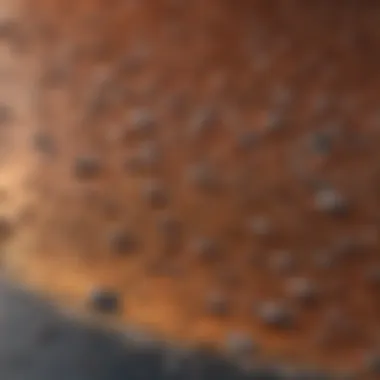
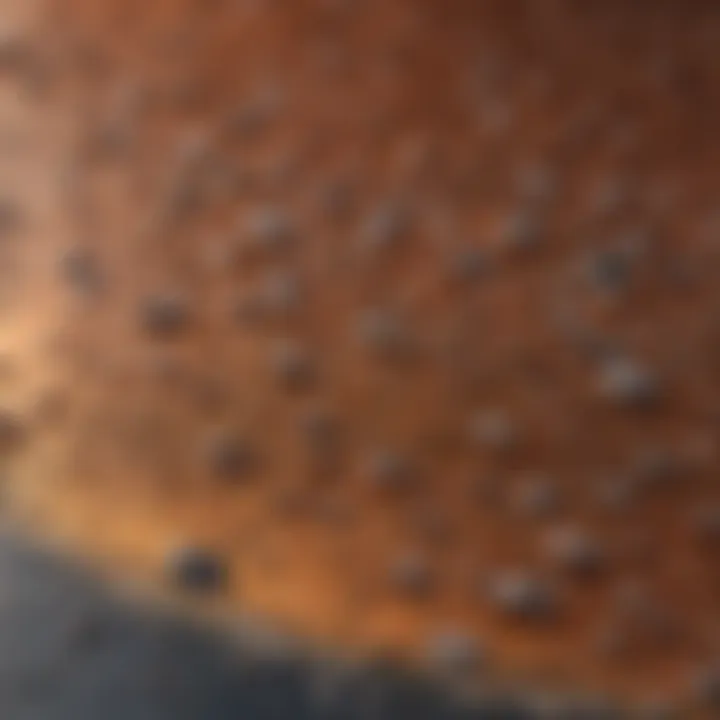
Metals serve as a robust substrate choice, particularly in protective and functional coatings. Their high thermal and electrical conductivity plays a crucial role in applications where thermal management is important. Metals can also provide a dense substrate for films, significantly contributing to adhesion through mechanical interlocking. Among the various metals, stainless steel and aluminum stand out for their favorable chemical and mechanical properties. However, one must consider the increased risk of oxidation in metals, which can lead to compromised adhesion, potentially undermining performance in long-term applications.
Thin Film Material Composition
The composition of thin films represents a critical aspect that dictates their performance and applicability in various domains. An understanding of material types is essential for developing coatings and films that align with desired outcomes in adhesion and functionality.
Inorganic Materials
Inorganic materials, such as ceramics and metals, provide several advantageous properties for thin films. Their high thermal resistance and mechanical strength make them suitable for applications requiring robust performance, like protective coatings on tools or in aerospace. An interesting feature of inorganic materials is their ability to form strong chemical bonds, which enhances adhesion significantly. Despite these benefits, the rigidity of these materials may lead to brittleness, requiring careful handling during application and end-use.
Organic Compounds
Organic compounds gain traction in thin film applications, especially for optoelectronic devices and flexible displays. They are celebrated for their lightweight nature and easy processing, making them favorable for low-cost manufacturing. A key characteristic of organic thin films is their flexibility, which allows them to conform to varied surfaces and withstand mechanical stress without failure. However, their sensitivity to environmental conditions, like moisture and temperature, can affect durability and long-term performance, posing challenges that need to be addressed in design and application.
Hybrid Materials
Hybrid materials blend the best of inorganic and organic properties, paving the way for innovative applications. Their versatile characteristics often lead to improved adhesion and performance in devices needing both strength and flexibility. For example, these materials can offer the mechanical robustness of inorganics while maintaining the lightweight aspect of organics. Nevertheless, the complexity in material processing may introduce additional variables to control during production, which can complicate the manufacturing process.
"The right choice of materials is not merely about performance; it is also about creating a seamless interaction between the thin film and its substrate."
Through careful consideration of these materials, one can optimize thin film adhesion and unlock advancements across various industries.
Adhesion Mechanisms
In the realm of thin film technologies, understanding the mechanisms of adhesion is paramount. Adhesion mechanisms are the processes that dictate how films bond to substrates, influencing not only the durability of the films but also their performance in various applications. Recognition of these mechanisms allows researchers and engineers to design films with enhanced properties, ensuring they meet specific functional requirements across diverse industries. Without a solid understanding of adhesion mechanisms, one might as well be trying to catch smoke with their bare hands.
Interfacial Phenomena
Interfacial phenomena refer to the unique interactions that occur at the boundaries between different materials. These phenomena are central to the overall adhesion strength of thin films. In this section, we will shine a light on three critical elements: surface roughness effects, molecular interaction dynamics, and the influence of temperature.
Surface Roughness Effects
Surface roughness plays a vital role in the adhesion of thin films. When one considers the layers involved, it's the minute textures of surfaces that often dictate how effectively two materials cling. A rough surface can increase mechanical interlocking, creating numerous points of contact compared to a flat surface. This characteristic makes rough surfaces a popular choice in applications where enhanced bond strength is needed, such as in protective coatings.
Interestingly, while increased roughness can lead to better adhesion, excessive roughness may introduce difficulties in achieving uniform film deposition, potentially resulting in defects. Thus, surfac roughness stands as a double-edged sword, offering both benefits and challenges.
Molecular Interaction Dynamics
The dynamics of molecular interactions—think of it like a dance between molecules—directly influence adhesion quality. When molecules on the surface of a film bond with those of a substrate, it can enhance the overall strength of the bond. Key interactions include hydrogen bonding and van der Waals forces that govern how surfacial elements engage with one another. This concept is particularly significant in organic thin films, where such interactions are more pronounced.
However, relying solely on molecular interactions can sometimes be misleading. The environmental conditions, such as humidity and temperature, can disrupt these interactions. Hence, while understanding molecular dynamics can lead to improved adhesion strategies, one must also be mindful of external circumatances that could alter these behaviors.
Temperature Influence
Temperature has a unique influence on adhesion. During thermal treatments, the properties of materials can change significantly. At elevated temperatures, materials might expand, potentially leading to enhanced molecular mobility and improved interfacial bonding. This characteristic makes temperature manipulation a beneficial tool in thin film processing.
However, it can be a double-edged sword once again. High temperatures can also lead to unwanted stress or phase changes in materials, which could compromise bond strength. Thus, managing temperature effectively is crucial when considering the adhesion of thin films.
Role of Surface Energy
Surface energy is a critical parameter in the adhesion landscape of thin films. Understanding this concept is essential for anyone looking to enhance or manipulate adhesion in practical applications. Variations in surface energy can dramatically affect how materials interact; higher surface energy generally promotes better adhesion due to increased molecular interactions.
Defining Surface Energy
Surface energy can be viewed as a measure of how much energy is required to create a new surface. A key characteristic of this concept is that it dictates the wettability of a surface. In the context of thin films, surfaces with low energy may repel incoming materials, resulting in poor adhesion properties. Hence, understanding surface energy is crucial for selecting materials and treatment processes in this article.
The unique feature of surface energy is that it can be modified through treatments such as plasma activation or coatings, offering potential advantages in engineering applications. However, there's always a trade-off; for example, treatments can sometimes alter the primary characteristics of materials unexpectedly.
Impact on Adhesion Strength
Surface energy also has direct implications on adhesion strength. When adhesion increases, usually due to improved molecular wetting, performance in applications like electronics and coatings can see a significant boost. This makes it a popular focus in current research.
However, it's crucial to remember that while enhancing surface energy can lead to better performance, it is often accompanied by increased susceptibility to contamination or environmental changes, thus requiring careful handling and processing.
Measurement Techniques
Finally, understanding how to accurately measure surface energy is pivotal for any assessment of thin film adhesion. There are several methods, including contact angle goniometry and the use of tensiometric methods. Each of these techniques provides insights into how well a material may adhere under specific conditions.
The distinct feature of these measurement techniques is their ability to offer real-time assessments, giving researchers valuable data to optimize adhesion strategies. On the downside, intricate setups and measurements can introduce variability, requiring meticulous calibration to ensure accuracy.
Understanding adhesion mechanisms enables scientists to not only predict the success of materials in specific applications but also to engineer innovative solutions in technology and materials science.
Testing and Measurement Methods
Testing and measurement methods are critical in understanding thin film adhesion, as they provide insight into how well a thin film adheres to its substrate. This section dives into various testing methodologies that can assess the effectiveness of adhesion in thin films. Employing precise techniques not only highlights adhesion strength but also facilitates improvements in material selection and application processes. The reliability and accuracy of these methods are pivotal since they determine the durability and integrity of thin films in real-world scenarios.
Mechanical Testing Approaches
Mechanical testing methods are essential in evaluating the adhesion properties of thin films. They simulate mechanical stresses that may occur in practical environments, allowing researchers to gauge how materials will behave under varying conditions.
Peel Test
The peel test is cornerstone in mechanical testing approaches. It measures the force required to peel a thin film away from a substrate at a specific angle. This method stands out for its simplicity and is frequently favored in the industry for assessing adhesion in tape products and laminates.
A key characteristic of the peel test is its straightforward setup, making it an accessible choice for both research and quality control processes. When conducted properly, the peel test provides accurate readings of adhesion forces, offering crucial data for evaluating adhesive strategies.
However, its unique feature lies in how it reveals the failure mode of the adhesive bond. A weakness in the bond is usually evident from the manner in which the film separates—be it cohesive failure (within the film) or adhesive failure (with the substrate).
Advantages of the peel test include ease of implementation and the ability to simulate practical applications directly. Nevertheless, the disadvantages may include its inability to provide comprehensive data on adhesion performance under dynamic conditions or varying environmental influences.
Shear Test
The shear test measures the force required to slide one material over another, which is significant in evaluating adhesion under lateral stress. It is a preferred method for assessing adhesion in coatings and bonded materials, especially where shear forces are prevalent in service conditions.
One prominent characteristic of the shear test is its capacity to reflect real-world applications where lateral forces act. It gives a more rounded understanding of how a material interacts under different stress conditions, which is particularly beneficial for end-user applications.
Moreover, the unique feature of the shear test is its ability to determine the point of failure and the mode thereof, whether it's adhesive or cohesive. This lends insight into the durability of the thin film under challenging conditions.
The advantages here include its direct relevance to many applications and the robust data it generates about shear strength. However, a notable disadvantage can be its complexity; the test may require equipment set up precisely, which demands some expertise.
Scratch Test
Scratch testing provides an interesting way to assess adhesion by measuring a material's resistance to localized mechanical stress. It typically involves scratching the surface of the thin film with a specified force or object, thereby evaluating how well the film adheres to its underlying substrate.
A critical aspect of the scratch test is that it can simulate damage that occurs in real-world settings, like wear or abrasion. This makes it particularly valuable for materials subjected to frequent or harsh contact.
The unique feature of this test lies in its sensitivity to failing adhesion, as small scratches often result in visible damage indicating bond weakness.
The key advantages of utilizing the scratch test are its replicability and direct correlation to user-oriented stress conditions. On the flip side, one disadvantage is that it may not cover all aspects of adhesion; for instance, it does not always account for the effects of thermal stresses on adhesion performance.
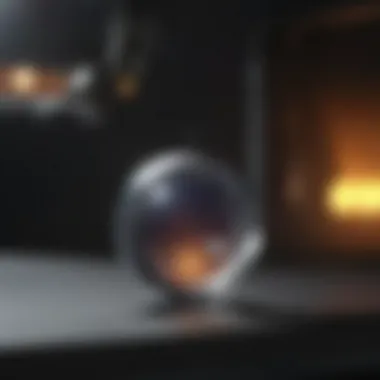
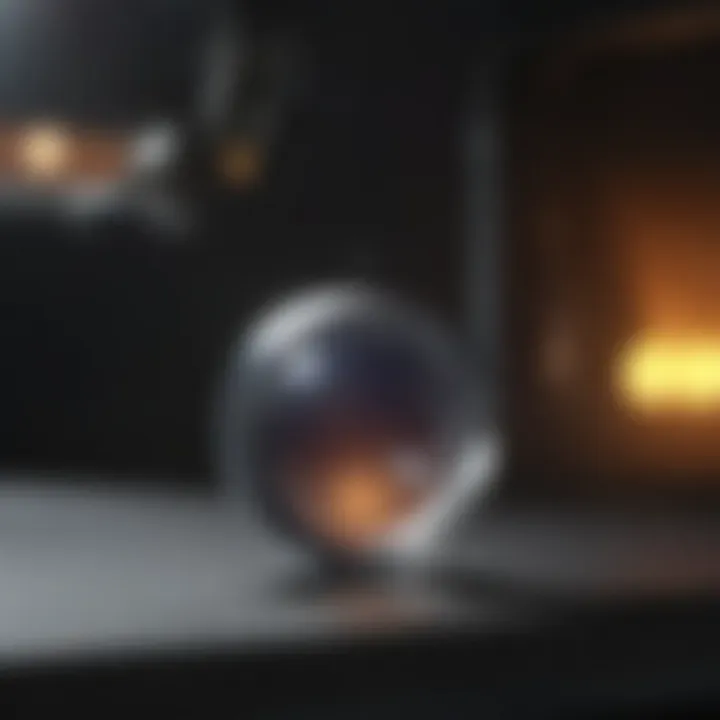
Characterization Techniques
Characterization techniques are necessary for delving deeper into the microstructural properties and interactions at the interfaces. In the arena of thin film adhesion, these sophisticated methodologies can unveil the physical and chemical characteristics influencing adhesion performance in various applications.
Atomic Force Microscopy (AFM)
Atomic Force Microscopy is a powerful imaging technique that provides topographical maps of surfaces at the nano-level. In the context of thin film adhesion, AFM allows for detailed visualization of surface roughness and features that play a significant role in adhesion mechanisms.
A key characteristic of AFM is its capacity to operate in different environments, making it versatile for capturing changes in adhesion properties under varying conditions. It measures forces between a sharp tip and the sample, allowing researchers to understand the intermolecular interactions that define adhesion strength.
The unique feature of AFM lies in its ability to achieve high-resolution data, making it invaluable in very precise applications. However, its advantages come with disadvantages such as operating costs and the need for skilled interpretation of data, which can present challenges in broader applications.
Scanning Electron Microscopy (SEM)
Scanning Electron Microscopy takes the examination of surface topography a step further by allowing scientists to visualize the surfaces of thin films in high detail. In analyzing adhesion, SEM can reveal interfaces and failure modes with remarkable clarity.
One interesting characteristic of SEM is its ability to analyze samples at different magnifications, making it suitable for a range of materials and applications.
The unique feature lies in its potent imaging capabilities that can even allow for elemental analysis. This provides valuable chemical information alongside structural data that is crucial for understanding adhesion properties. Yet, while the advantages of SEM include extensive insight into surface interactions, its disadvantages typically involve high costs and the need for sample preparation that may alter the actual material properties.
X-ray Photoelectron Spectroscopy (XPS)
X-ray Photoelectron Spectroscopy is instrumental in investigating the elemental and chemical state of materials. For thin film adhesion, it offers insights into surface chemistry, which is vital since chemical interactions can significantly affect adhesion strength.
A key characteristic of XPS is its surface sensitivity, making it ideal for thin films where understanding outer layers is critical. It can effectively measure the elemental composition and identify different oxidation states in materials, providing insights into potential bonding mechanisms at work.
The unique feature of XPS is its non-destructive nature, allowing for analysis without compromising the sample. Its advantages include depth profiling and the ability to gather chemical information, while disadvantages might include complexity in operating the device and interpreting results.
Challenges in Thin Film Adhesion
Understanding the intricacies of thin film adhesion necessitates a closer look at the challenges that accompany it. These hurdles can significantly impact the performance and longevity of thin films in various applications. Addressing these challenges is not just academic; it's crucial for ensuring the effectiveness of thin film technologies in real-world situations, especially in sectors like electronics, medicine, and renewable energy.
Common Failure Modes
Delamination
Delamination occurs when layers of material separate at the interface, compromising adhesion. It acts like a double-edged sword in thin film applications—the very qualities that make multilayer systems useful can also render them susceptible to delamination. Commonly arising due to mechanical stress or thermal cycling, delamination serves as a key indicator of the battle between adhesion and material instability.
A notable characteristic of delamination is its tendency to manifest in ways that are not immediately detectable, sometimes only revealing itself after significant performance loss. While it can serve as a cautionary tale, its prevalence in the industry makes delamination a popular subject of study in this article. Understanding the mechanics behind delamination helps researchers design better adhesives and select materials more judiciously.
The challenge, however, lies in the difficulty of predicting when and how delamination will happen. Factors such as inconsistent surface preparation or improper curing can contribute to its onset, emphasizing the need for rigorous control systems in manufacturing processes.
Blistering
Blistering, on the other hand, refers to the formation of bubbles or raised areas in thin films, typically due to trapped moisture or gas. Its emergence can be likened to an unexpected pop during a smooth performance—one moment everything looks fine, the next you're facing a serious issue. It highlights the sensitivity of thin films to their environments.
The key characteristic of blistering is its rapid propagation. Once initiated, it can lead to extensive damage, making it a critical factor to consider. The good news? Knowing the conditions that foster blistering enables engineers to implement pre-emptive measures, such as improving sealing techniques to mitigate moisture intrusion.
Nonetheless, while it’s vital to understand how to prevent blistering, its potential to significantly malfunction products adds another layer of complexity to thin film adhesion.
Cracking
Cracking represents yet another common failure mode and can be the straw that breaks the camel's back for many thin films. This phenomenon arises under stress or environmental conditions that push materials beyond their limits. The journey of a cracking thin film is often a gradual one, triggered by the interplay of mechanical and thermal stresses.
A standout feature of cracking is its irreversibility. Once a crack forms, it usually leads to complete failure of the thin film, which reinforces the seriousness with which researchers must give consideration to this issue. Cracks can open doors to further degradation, and much like the old saying goes, an ounce of prevention is worth a pound of cure. Understanding the underlying causes of cracking can help mitigate its impact, providing researchers with valuable insights into enhancing durability.
Influential Factors
In addition to failure modes, various factors play a significant role in influencing the adhesion of thin films. Grasping these elements not only enriches our understanding but equips researchers and engineers with the tools needed to tackle adhesion challenges effectively.
Thermal Stresses
Thermal stresses arise due to temperature fluctuations during fabricating or operating thin films. They are often underestimated yet carry substantial weight in determining adhesion quality. The unique characteristic of thermal stresses is their ability to induce strain within materials, which can lead to separation at the interfaces and ultimately affect the film's performance.
The embedded implications of thermal stresses make them a critical point of discussion in this article. Understanding how temperature gradients can create adverse conditions opens avenues for improved material selection or optimized thermal management strategies.
However, the challenge lies not only in quantifying these stresses but also in developing materials that can withstand them without compromising structural integrity.
Environmental Influences
Environmental conditions play a pivotal role in determining the adhesive performance of thin films. Factors such as humidity, temperature, and ambient chemicals can weaken the adhesion over time. Environmental influences are often the silent contributors to failure, gradually wearing down the interfaces without immediate symptoms.
The key advantage in understanding these factors is the opportunity for tailored strategies to mitigate their effects, allowing companies to ensure longer-lasting products. Yet, the variability of environmental conditions can pose significant challenges, making it difficult to create universal solutions applicable across different scenarios or applications.
Aging Process
Lastly, the aging process of materials presents its own set of challenges. Over time, changes in the chemical and physical structure of thin films can lead to a decline in adhesion strength. This phenomenon can be especially concerning for long-term applications like solar cells or medical devices, where sustained performance is critical.
The unique property of aging is that it can be slow and insidious, often going unnoticed until it has reached a critical level. It calls for continuous monitoring and assessment throughout a thin film's lifecycle, creating a demand for innovative testing methods and materials that can withstand the test of time.
In summary, the challenges surrounding thin film adhesion are multifaceted, encompassing common failure modes and influential environmental factors. Understanding these challenges equips stakeholders with knowledge that is crucial for advancing thin film technologies and their applications.
Surface Treatments and Enhancements
Surface treatments and enhancements are critical steps in the thin film adhesion process. They serve as the backbone for ensuring that thin films not only adhere well but also maintain their integrity and functionality over time. The selection of appropriate treatments can significantly affect adhesion properties, performance longevity, and structural stability, especially in demanding environments. These treatments can therefore lead to improvements in durability, effectiveness, and user satisfaction, making it a focal point in thin film applications.
Surface Preparation Techniques
Cleaning Protocols
Cleaning protocols play a vital role in preparing surfaces for thin film applications. The objective of these protocols is to remove contaminants such as dust, grease, or oxides that could undermine adhesion. By ensuring a pristine substrate, the potential for a strong bond increases considerably. One of the key characteristics of cleaning protocols is their adaptability; they can incorporate techniques like solvent cleaning, ultrasonic cleaning, and even laser ablation. This adaptability makes them a popular choice within the field of thin films.
Cleaning protocols often utilize unique features like solvent combinations that account for the surface chemistry of the substrate. For instance, isopropyl alcohol is often used for its effectiveness in removing organic contaminants.
While cleaning protocols provide significant advantages—like improved adhesion and consistency—they can also have drawbacks. Over-cleaning or using aggressive solvents may lead to substrate damage or unwanted chemical alterations at the surface, which could negatively influence the performance of the thin film.
Surface Roughness Alteration
Surface roughness alteration involves physically manipulating the surface texture to enhance adhesion. This technique often utilizes methods such as sandblasting or chemical etching. The primary advantage of altering surface roughness is the increased surface area for bonding, which allows for mechanical interlocking between the thin film and the substrate. This aspect is fundamentally beneficial in promoting stronger adhesion.
An important characteristic of surface roughness alteration is its ability to create microstructures that can significantly improve adhesion properties. Enhanced friction and interfacial surface area lead to more robust bonding. However, it comes with trade-offs. Excessive roughness can result in defects in the thin film itself or create zones that are difficult to coat uniformly, potentially leading to uneven film thickness and compromised functionality.
Plasma Treatment
Plasma treatment is a sophisticated surface modification technique that employs ionized gases to modify the surface properties of substrates. This method is gaining popularity due to its effectiveness in cleaning and activating surfaces in one step. A significant characteristic of plasma treatment is its versatility, providing exceptional control over modifications to the chemical composition and roughness of surfaces.
Plasma treatment uniquely enables a high degree of specificity; depending on the gas used—such as oxygen or nitrogen—it can enhance surface energy or introduce functional groups that promote chemical bonding. This leads to better adhesion and performance in various applications, particularly in the realm of electronics and coatings.
Nevertheless, plasma treatment is not without its challenges. The method can be complex, requiring specialized equipment and trained personnel. Furthermore, the effects of the treatment can also be transient, necessitating careful consideration of the timing between treatment and application of the thin film to ensure maximum adhesion.
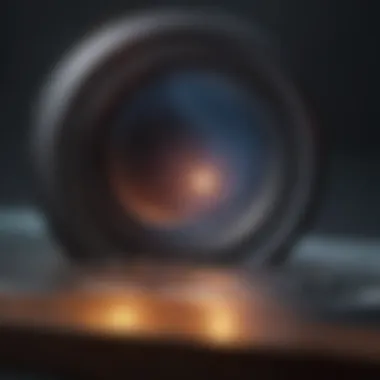
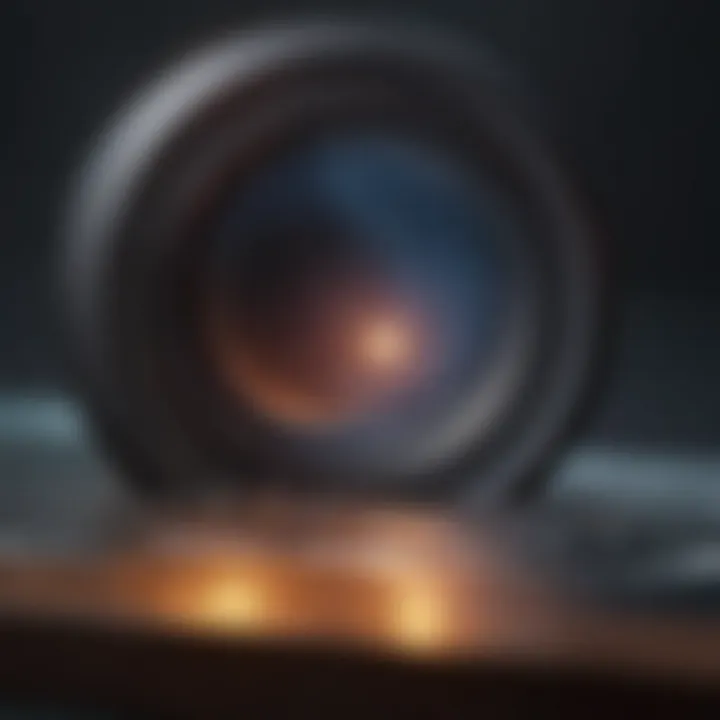
Coating Improvements
Coating improvements are an integral part of enhancing thin film adhesion by modifying the characteristics of the coatings themselves. These enhancements can include the use of various additives and alternative materials that effectively improve bonding properties and durability.
Adhesion Promoters
Adhesion promoters are specific compounds added to coatings to enhance their ability to bond with substrates. They are particularly useful in systems where traditional bonding might fail. One key aspect of adhesion promoters is their ability to modify interfacial energies, making the surface more amenable to bonding. This character makes them extremely valuable in applications where high adhesion strength is crucial.
Promoters can vary widely in chemical structure and functionality. One unique feature is their ability to react with both the substrate and the coating, creating a chemical bridge that solidifies the bond. However, the downside is that improper use or selection of an adhesion promoter could lead to adverse chemical reactions, possibly compromising the overall film integrity.
Hybrid Coatings
Hybrid coatings blend different materials to tap into the benefits of each, effectively creating coatings that are both versatile and robust. The hallmark of hybrid coatings is their multifunctionality; they can provide strength, flexibility, and resistance to both chemical and environmental degradation.
Hybrid coatings often contain a mix of organic and inorganic components. For example, combining polymers with silica can yield a coating that excels in both mechanical and thermal properties. One downside noted in using hybrid coatings is their complexity; designing a hybrid system requires extensive knowledge to balance compatibility and performance. Failure to do so can lead to issues like phase separation or reduced mechanical properties.
Polymeric Modifiers
Polymeric modifiers are used to enhance the mechanical and adhesion properties of films. These modifiers can be incorporated into coatings to improve flexibility and impact resistance. A defining characteristic is that they can help balance performance and ease of application, allowing coatings to be more robust without complicating the application process.
The unique advantage of polymeric modifiers is that they can adjust properties, such as elasticity and tensile strength, tailored for specific applications. However, too much modification can lead to increased viscosity, complicating application processes and potentially leading to defects in the film during production.
In the ever-evolving landscape of thin film technology, adopting meticulous surface treatments and enhancements can make all the difference. As challenges in adhesion are addressed through careful considerations of the methods and materials involved, researchers and practitioners can achieve greater reliability and functionality in their applications.
Applications of Thin Film Adhesion
Thin film adhesion holds significant value across various industries, acting as a core concept that influences both functionality and durability. From the precision required in electronics to the diverse application in coatings, thin film adhesion is pivotal. This section explores its roles in essential sectors, showcasing how the different applications impact the overall landscape of technology and innovation.
In Electronics
Integrated Circuits
Integrated circuits, a cornerstone of modern electronics, rely heavily on robust thin film adhesion. The specific aspect of adhesion here is related to how well different layers, such as semiconductors and insulation materials, bond together without delaminating. A key characteristic of integrated circuits is their compact design, which necessitates precise and reliable adhesion to maintain functionality over time. This aspect makes them a popular choice in the realm of electronics, as even the slightest failure in adhesion can lead to performance inefficiencies or complete system failures.
Moreover, integrated circuits often incorporate multilayer structures, benefitting from advances in adhesive technologies, which enhance reliability and longevity but may introduce complexities in manufacturing processes.
Optoelectronic Devices
Optoelectronic devices, which combine optics and electronics, also showcase the critical nature of thin film adhesion. The specific aspect of adhesion in this context pertains to light transmission efficiency and operational stability. Optoelectronic devices are favoured because they are both versatile and essential for applications ranging from telecommunications to healthcare imaging. Their unique feature is that they rarely operate independently—during design, ensuring that the film layers adhere properly is crucial for optimal performance. While the adhesion can improve functionality, the complexity of integrating various materials introduces challenges that must be addressed for reliable operation.
Flexible Electronics
Flexible electronics present another angle on the application of thin film adhesion. This sector focuses on the ability to create gadgets that can bend, twist, or stretch without compromising functionality. The key characteristic here is the incorporation of thin films on flexible substrates, allowing devices to adapt to various shapes and forms. This makes flexible electronics a beneficial choice for modern consumer products, such as smartwatches and wearable health monitors. The unique feature of these devices lies in their capacity to maintain performance during mechanical stress. However, the challenges of ensuring durable adhesion under such varied conditions are significant, requiring continuous innovations in materials science.
In Coatings
Protective Coatings
Protective coatings are vital in extending the service life of materials. These coatings rely on effective thin film adhesion to shield underlying surfaces from environmental factors like corrosion or abrasion. A key characteristic of protective coatings is their robustness, often designed to withstand harsh conditions. This makes them a beneficial choice in industries such as construction and aerospace. The unique feature of these coatings is their ability to minimize wear and tear on the base material. However, ensuring longevity can sometimes lead to complications in application techniques and material compatibility.
Decorative Films
Decorative films add both aesthetic value and functional benefits to products. They are widely used to enhance the visual appeal of items, but they also necessitate strong adhesion to perform effectively. The key characteristic of decorative films is that they provide a high level of versatility in design while being relatively easy to apply. This duality makes them a popular choice in various markets, from automotive to consumer goods. However, achieving an optimal bond often requires careful selection of both the film materials and the surfaces to which they are applied, making this process more art than a science.
Functional Coatings
Functional coatings go beyond mere appearance, offering specific benefits such as anti-reflective properties or hydrophobic surfaces. The specific aspect of thin film adhesion relates to how these coatings interact with a myriad of surface types. They are often recognized for their remarkable adaptability, which positions them as a benefit to both new and existing products that need to meet varying technical specifications. The unique feature of functional coatings lies in their ability to provide dual functionality—enhanced durability alongside performance. Nevertheless, careful considerations regarding adhesion techniques and surface preparation become essential to ensure longevity and efficacy.
In Energy Harvesting
Solar Cells
In the energy harvesting sector, solar cells epitomize the necessity for effective thin film adhesion. A critical aspect here involves how well the film layers bond, directly influencing the overall efficiency of energy conversion. Solar cells are a beneficial choice in renewable energy pursuits due to their capacity for reducing dependency on fossil fuels. The unique feature of solar cells is that they must perform reliably in a variety of environmental conditions. Factors such as temperature fluctuations can complicate adhesion, requiring ongoing research to develop more resilient materials and bonding techniques.
Fuel Cells
Fuel cells are another area of focus, relying on effective thin film adhesion to maintain operational integrity. The specific aspect within slim films relates to their ability to ensure proper ion transport and fuel flow, which is paramount for efficiency. Fuel cells represent a promising solution for sustainable energy, particularly in transportation. Their unique feature is the need for an intricate balance between conductivity and adhesion stability. However, challenges arise when considering long-term durability, necessitating advancements in materials technology.
Thermoelectric Devices
Lastly, thermoelectric devices transform temperature differences into electric energy, and their efficiency is heavily reliant on thin film adhesion. The key characteristic of these devices is their dual function in power generation and cooling applications. This versatility makes them valuable in various applications like waste heat recovery. A notable unique feature is their dependence on maintaining optimal adhesion to ensure consistent performance, making ongoing research into adhesive technologies crucial.
As the landscape of technology evolves, the importance of understanding thin film adhesion only increases, especially as applications continue to diversify and integrate into everyday life.
Future Directions in Thin Film Research
The quest for advancements in the field of thin film adhesion is akin to navigating through a maze, where every turn leads to potentials yet to be discovered. Understanding where the future is headed helps not only in developing smarter technologies but also in pushing the boundaries of what is possible in various industries.
Emerging Materials
Optimizing thin film adhesion largely relies on the adoption and integration of new materials. As the phrase goes, "new blood brings rejuvenation," and this is particularly relevant in the domain of thin films. Each novel material can reshape expectations and standards.
Nanomaterials
One of the most exciting developments in thin film research is the rich field of nanomaterials. These materials are often less than 100 nanometers in size, and their unique properties stem from their reduced dimensions. The key characteristic of nanomaterials includes their significant surface area to volume ratio, which contributes to enhanced mechanical properties and improved chemical reactivity.
A notable aspect of nanomaterials is their ability to strengthen adhesion through better interaction at the molecular level. For example, graphene, a single layer of carbon atoms, exhibits remarkable strength and conductivity, making it a popular choice in advanced thin film applications. However, the disadvantages cannot be ignored; they often face challenges concerning scalability and uniformity during production, making widespread application trickier than it seems.
2D Materials
As we take a closer look, another frontier appears: 2D materials. These substances, like graphene and transition metal dichalcogenides (TMDs), have gained traction due to their incredible electronic properties and thin-film configurations.
The beneficial aspect of these materials lies in their exceptional flexibility and strength combined with low weight. Such characteristics make them attractive for supporting applications where conventional materials may falter. A standout feature is their unparalleled conductivity, which can revolutionize electronics, yet various processing methods to integrate them seamlessly into existing technologies can be a hurdle.
Biomaterials
Then there’s the realm of biomaterials. The demand for eco-friendly and biocompatible solutions is on the rise. Biomaterials are derived from natural sources and exhibit favorable interactions with biological systems. They are pivotal in applications ranging from medical devices to sustainable energy systems.
The key feature of biomaterials is their bioactivity, meaning they can integrate well with living tissues. This makes them a prime candidate in fields such as tissue engineering or drug delivery. However, the trade-offs often involve variability in how they react under different conditions, leading to unpredictable performance.
Innovative Applications
The innovations flowing from the research of thin films aren’t merely academic—they hold promise for transformative changes in real-world applications. Every advance leads to potential breakthroughs in functionality and efficiency.
Smart Coatings
One of the shining stars in current development is smart coatings. These coatings can change their properties in response to environmental stimuli such as temperature or light. Their adaptive ability makes them particularly valuable in fields like construction and healthcare. The ability to respond dynamically leads to improved durability and efficacy. However, complex design and potentially higher costs are challenges that manufacturers need to address.
Biocompatible Films
Moving into the medical realm, biocompatible films are paving the path forward. These films find significant use in applications like drug delivery systems and surgical devices. Their crucial characteristic is that they are designed to interact favorably with biological tissues without inducing an adverse reaction. This is a major plus, especially in sensitive and critical applications, but issues such as degradation rate and processing require careful consideration in each specific context.
Advanced Energy Solutions
Finally, there are advanced energy solutions, which revolutionize how energy is harvested and utilized. These solutions focus on improving the efficiency of devices like solar panels and batteries through enhanced thin film technologies. A defining quality here is their capacity to optimize energy conversion rates, making them increasingly relevant in today’s energy discourse. However, integrating these solutions into existing systems can be technically challenging and may involve high initial costs.
The future of thin film research is not just about material advances; it’s about rethinking how we apply these materials in our daily lives.