Understanding Cold Forging: An In-Depth Exploration
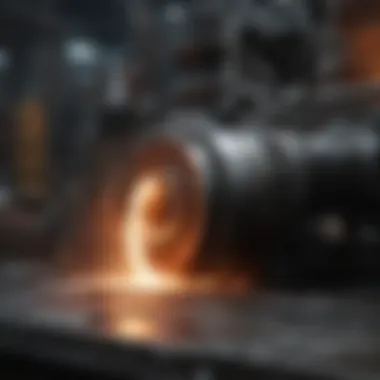
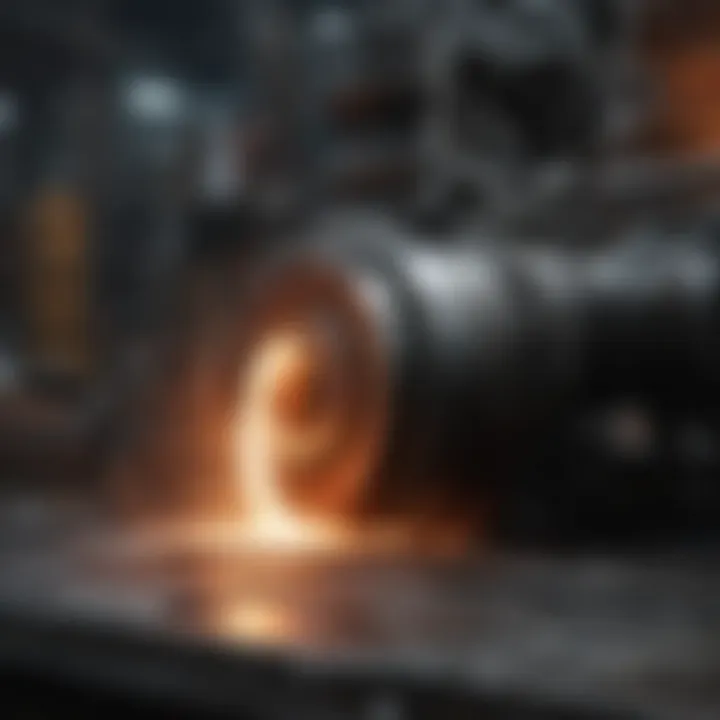
Intro
Cold forging is a metalworking process that shapes metal at or near room temperature. This process, unlike hot forging, preserves the material's strength and grain structure, leading to significant advantages in both mechanical properties and product quality. Cold forging has gained attention in various industries, from automotive to aerospace, as it offers both efficiency and precision. The objective of this article is to explore the underlying mechanisms of cold forging, study its benefits and limitations, and assess its role in modern manufacturing practices.
Research Overview
Summary of Key Findings
- Cold forging enhances material strength and durability due to work hardening.
- The method is energy-efficient and produces minimal waste compared to traditional metal shaping processes.
- It offers high precision, allowing for tighter tolerances in finished products.
- There are limitations in terms of the types of metals and sizes which can be effectively forged.
Background and Context
Cold forging has historical roots that trace back centuries, but it has evolved significantly with advancements in technology. As industries demand higher performance from components, cold forging has transitioned from a niche application to a mainstream manufacturing technique. Understanding its operational principles and applications can provide valuable insights for professionals aiming to innovate in their respective fields.
Methodology
Experimental Design
In examining cold forging, various case studies from the automotive industry illustrate how different processes are integrated. The effectiveness of cold forging can be measured against hot forging and machining processes in a controlled environment to highlight key differences in output and quality.
Data Collection Techniques
Data was gathered through a combination of literature review and empirical testing. Key metrics include:
- Mechanical properties post-forging
- Energy consumption during the process
- Surface finish and dimensional accuracy
- Yield and waste during production
This systematic approach reveals the significant advantages and some limitations present in cold forging processes.
Preamble to Cold Forging
Cold forging presents a method of metal shaping that has distinct advantages in manufacturing. Its significance cannot be overstated, as it plays a major role in producing strong and durable components found across various industries. In this section, we outline the critical aspects surrounding cold forging, specifically exploring its definition, historical evolution, and the benefits that set it apart from other methods.
Definition and Overview
Cold forging is a process where metals are shaped at room temperature, applying high pressure to create desired forms. Unlike hot forging, which involves heating metals to extreme temperatures, cold forging retains the material's original properties. This process typically results in improved mechanical properties, specifically increased strength and hardness due to strain hardening. Products manufactured through cold forging often require less finishing work because of the fine surface finish achieved.
Key techniques include open die forging and closed die forging, which enable a range of shapes and sizes to be produced, from simple fasteners to complex aerospace components. The versatility of cold forging is coupled with efficiency, making it an attractive alternative in modern manufacturing environments.
Historical Context
Cold forging has roots dating back centuries, with evidence suggesting that ancient societies utilized rudimentary forms of metal shaping. The technology, however, has evolved significantly. During the mid-20th century, with advancements in machinery and material science, the effectiveness of cold forging processes increased. The industrial revolution catalyzed its adoption, as mass production demanded streamlined methods that maintained stringent quality standards.
Currently, cold forging is pivotal in sectors such as automotive and aerospace, where weight reduction and high strength are crucial. Research continues to foster innovations in cold forging techniques and materials, ensuring this process remains relevant in addressing modern manufacturing challenges.
"Cold forging is a fundamental process that remains one of the most effective ways to produce high-performance components in various industries."
In summary, understanding cold forging sets the stage for exploring the detailed processes, materials, and applications that define this critical manufacturing technique.
The Cold Forging Process
The cold forging process plays a central role in the broader context of cold forming. Understanding this process is essential, as it encompasses specific techniques that enhance the properties of metals while maintaining their integrity. This section will detail the fundamental principles underlying cold forging, the necessary equipment, as well as the variations in techniques employed in the industry. Knowing these aspects gives insights into the overall efficiency, effectiveness, and adaptability of this manufacturing method.
Basic Principles
Cold forging is characterized by shaping metals without applying heat. The benefits of this approach include increased strength and superior surface finish. During this process, metals are subjected to high pressure, which causes them to deform. This deformation results in grain structure refinement and improved mechanical properties. Furthermore, lesser energy is consumed compared to hot forging, making it an environmentally sustainable choice. In summary, cold forging relies on mechanical methods to shape material efficiently, preserving its original properties while enhancing performance.
Equipment Used
Forging Machines
Forging machines are critical in the cold forging process. They serve as the primary means of applying mechanical pressure to the materials being shaped. Hydraulics or mechanical force generators are often involved in these machines. The key characteristic of forging machines is their ability to exert consistent force, achieving high accuracy in the deformation of materials. This technology's popularity stems from its reliability and efficiency in producing parts with complex geometries. One unique feature of these machines is their adaptability to various production needs, though their initial investment can be significant.
Dies and Tools
Dies and tools form the core components of the cold forging setup. These tools guide the flow of material during the forging process. Dies specifically are custom-made to fit the part being produced, which ensures precision. A significant advantage of using dedicated dies is that they facilitate production at higher rates and with fewer defects. However, the custom nature of dies can lead to longer lead times and higher costs during the initial setup phase. They are crucial for achieving consistent results in part production.
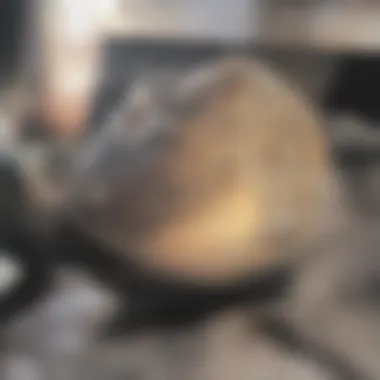
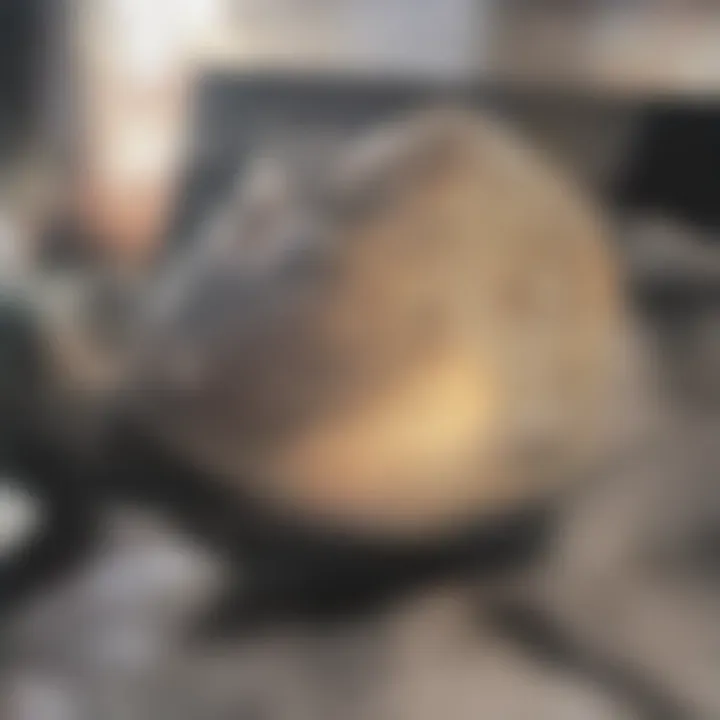
Material Handling Equipment
Material handling equipment is essential for transporting materials within the forging environment. This equipment includes conveyors, forklifts, and storage systems. The main characteristic of material handling equipment is its ability to ensure that the workpieces move seamlessly through various production stages. Effective handling minimizes the risk of damage or defects, emphasizing the need for proper logistics in the cold forging process. However, maintaining and operating this equipment demands careful planning and resources, which can be a limitation for some operations.
Technique Variations
Understanding the variations in cold forging techniques is important as it directly impacts the end product. Different methods can be employed based on material type, desired shape, and production volume.
Open Die Forging
Open die forging is characterized by the absence of a confined space, allowing for more complex shapes. This method permits considerable metal flow and is often used for larger parts. A key characteristic of open die forging is its versatility. It is suitable for various metals and dimensions. While it offers advantages in terms of the size and flexibility of the pieces produced, it typically has longer cycle times compared to closed die forging.
Closed Die Forging
Closed die forging employs a die that fully encloses the workpiece, shaping it precisely. This technique is highly effective for producing intricate shapes, thus presenting greater precision. The main advantage is the reduced waste and improved surface finish, making it a popular choice in industries where detail is vital. However, the complexity of the dies can increase production costs and extend lead times.
Upset Forging
Upset forging focuses on increasing the cross-sectional area, typically at one end of the workpiece. This technique is effective for producing specific shapes and is often used in applications that require a strong, thickened end, such as bolt manufacturing. A key characteristic of upset forging is its capability to create strong, durable components. The downside can be the limitations on the range of shapes that can be produced, alongside the stress concentrations that may arise from design choices.
Understanding these variations aids manufacturers in selecting the most applicable methods for their needs, enhancing production efficiency and product quality.
The detailed exploration of the cold forging process reveals its importance in modern manufacturing contexts. Each principle, piece of equipment, and technique variation contributes significantly to the capabilities afforded by cold forging.
Materials Suitable for Cold Forging
Cold forging requires specific materials that can withstand the demands of the process while achieving desired performance characteristics. The selection of suitable materials is crucial as it directly affects the strength, durability, and cost-effectiveness of the final products. Various metals exhibit properties that align well with the requirements of cold forging, each contributing uniquely to the manufacturing outcomes.
Common Metals Used
Steel
Steel is often regarded as the most popular choice for cold forging. Its strength-to-weight ratio is excellent, making it suitable for applications requiring exceptional durability. One key characteristic of steel is its ability to undergo strain hardening, which enhances its strength during the forging process. This characteristic is beneficial as it leads to parts that are robust and capable of withstanding heavy loads.
The unique feature of steel is its versatility; it can be alloyed with elements like chromium, nickel, or molybdenum to tailor its properties for specific applications. However, it is worth noting that steel's susceptibility to corrosion can be a disadvantage, requiring additional treatment to improve longevity.
Aluminum
Aluminum ranks high on the list for cold forging due to its lightweight nature and excellent corrosion resistance. Its key characteristic is its low density, which translates into lighter parts without sacrificing structural integrity. This makes aluminum a favorable material for industries such as aerospace, where every gram counts.
Aluminum’s unique feature is its ease of fabrication. It can be easily shaped and formed, even at low temperatures, which is a significant advantage in the cold forging process. Nonetheless, aluminum has a lower tensile strength compared to steel, which limits its use in some high-stress applications.
Copper
Copper finds its niche in cold forging thanks to its excellent electrical conductivity. The specific aspect of copper is its malleability, which allows for complex shapes to be forged with relative ease. This is particularly relevant in industries where electrical components are essential, such as electronics and telecommunications.
A key characteristic of copper is its inherent resistance to corrosion, contributing to its reliability in various environments. The unique feature of copper also extends to its high thermal conductivity, making it suitable for applications requiring heat dissipation. On the downside, copper is more expensive than steel and aluminum, which can be a consideration for large-scale production.
Material Properties
When selecting materials for cold forging, understanding the material properties is essential. Factors such as yield strength, ductility, and fatigue resistance directly influence the performance of the forged components. Cold forging processes often demand materials that can not only endure deformation without cracking but also retain their mechanical properties after processing.
The energy efficiency of the cold forging process also ties back to material selection; materials that are easier to forge can lower energy costs, thus making the operation more sustainable. Ultimately, the right choice of metals ensures that the products meet industry standards and client specifications.
Advantages of Cold Forging
The advantages of cold forging are significant for various industries. Understanding these benefits is crucial to appreciating the relevance of cold forging in modern manufacturing. This section elaborates on three main advantages: increased strength and durability, cost-effectiveness, and surface finish quality.
Increased Strength and Durability
Cold forging enhances the physical properties of metals, particularly their strength and durability. By working the metal at room temperature, the process encourages strain hardening. As the material is deformed, dislocations in the metal’s crystal structure increase, resulting in greater strength. Engineers and manufacturers take advantage of this phenomenon, as finished products require fewer resources to maintain their integrity over time.
Additionally, items produced through cold forging often display superior resistance to fatigue. This is essential in critical applications, such as automotive or aerospace components, where failure is not an option. Therefore, the choice of cold forging not only improves performance but also extends the lifespan of products subjected to high stresses.
Cost-Effectiveness
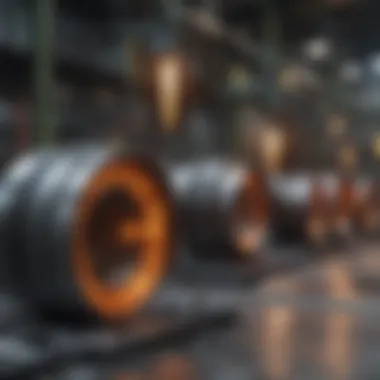
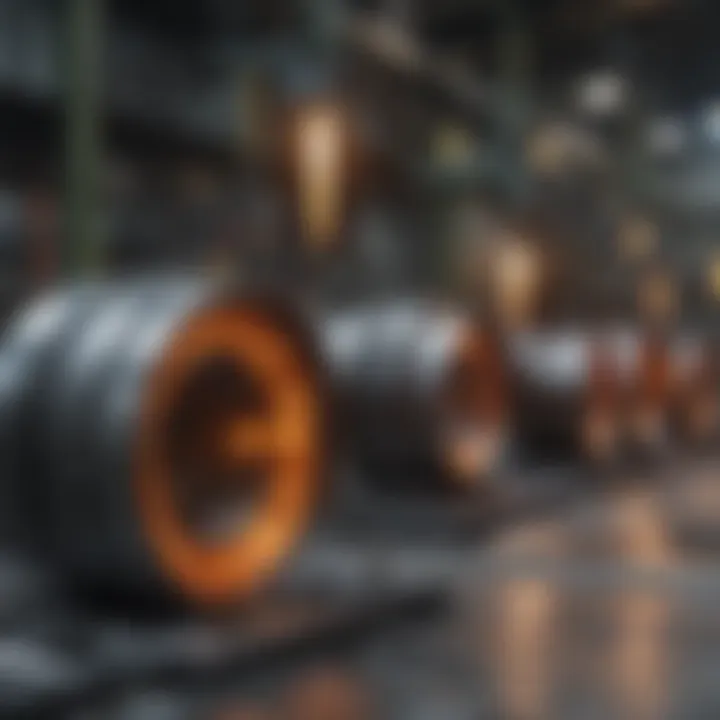
Another compelling advantage of cold forging is its cost-effectiveness. This term encompasses several factors that reduce overall production expenses. First, cold forging processes typically allow for a higher rate of production compared to other methods. This efficiency translates into lower labor costs per unit produced. Moreover, because the material is shaped close to final dimensions, there is less waste during production.
The initial investment in equipment may seem high. However, the longevity and durability of cold forged parts can offset this cost. Maintenance and replacement are less frequent, contributing to savings on long-term operational expenses. Ultimately, businesses can achieve a better return on investment through careful selection of cold forging for their manufacturing needs.
Surface Finish Quality
Cold forging tends to produce superior surface finish quality. Parts forged using this method require less machining or secondary processing. This is particularly important as it leads to reduced production times and costs. Cold-forged components naturally exhibit a smoother surface when compared to those produced by hot forging methods, which often leave thicker oxides or scale.
Furthermore, this high-quality finish can be critical in applications where tolerances are tight, such as in the production of medical devices or precision instruments. Manufacturers benefit from reduced finishing work, which translates to both time savings and enhanced overall product performance.
In summary, cold forging provides distinct advantages that bolster the production of durable, cost-effective, and high-quality components across various sectors.
Disadvantages of Cold Forging
Cold forging, while advantageous in many respects, does come with certain disadvantages that are worth thorough examination. Understanding these drawbacks is crucial for anyone involved in manufacturing or engineering. This section focuses on two specific challenges frequently associated with cold forging.
Limitations on Size and Complexity
Cold forging is inherently limited when it comes to the size and complexity of parts that can be produced. The process relies on the ability to shape metal at room temperature, a characteristic that imposes restrictions on the geometry of the items being forged. Large or excessively intricate designs may not be feasible due to the mechanical constraints of equipment and tooling.
Additionally, cold forging often requires significant material flow to achieve the desired shape. This flow can be difficult to manage with larger parts, potentially leading to issues such as material waste or weak points in the final product. Thus, manufacturers may need to consider alternative forming processes or utilize multiple operations to achieve complexity, increasing both production time and costs.
Initial Equipment Costs
Another important drawback of cold forging is the high initial investment required for equipment. The machinery and tools specific to cold forging can be quite expensive. This can be a significant barrier for small manufacturers or startups looking to enter the market. Furthermore, specialized dies and tools must be designed and manufactured for each specific part type, which adds to the upfront costs.
While cold forging can indeed yield cost savings over the long term through efficiencies in production, the initial financial outlay can be daunting. Companies must weigh these costs against potential benefits when considering if cold forging is a suitable method for their products.
"The upfront investment in cold forging equipment can often deter manufacturers, especially those new to the market, from adopting this method."
To summarize, while cold forging offers clear advantages, it does not come without limitations. Understanding these disadvantages is essential for making informed decisions about manufacturing processes. Awareness of size and complexity constraints, along with initial equipment costs, ensures that organizations can strategically plan their production capabilities.
Applications of Cold Forging
Cold forging has significant applications across various industries. This method of manufacturing offers practical benefits, including improved material properties and cost savings. Understanding these applications is essential for grasping the full impact of cold forging in modern manufacturing.
Automotive Industry
The automotive industry is one of the leading sectors that utilizes cold forging extensively. Components such as gears, shafts, and connectors are crafted using this process. Cold forging allows for the production of parts with enhanced strength and precision. Additionally, the weight reduction in parts produced through cold forging contributes to fuel efficiency in vehicles. Common materials like steel and aluminum are often used due to their favorable mechanical properties when cold forged.
Aerospace Sector
In the aerospace sector, cold forging plays a critical role in manufacturing lightweight yet strong components. Parts such as fasteners and structural elements are often produced via this method. The aerospace industry demands high reliability and performance from its components, which cold forging provides through its ability to create uniform grain structures in metals. This method also meets stringent regulations while optimizing production cost, making it ideal for aerospace applications.
Medical Devices
Cold forging finds applications in the production of medical devices, where precision and quality are paramount. Components like surgical instruments and implants benefit from the superior mechanical properties afforded by cold forging. The process also enables high levels of cleanliness and minimizes waste, aligning with the industry’s standards for safety. Using cold-forged parts allows manufacturers to maintain consistency in performance critical to patient care.
Construction and Infrastructure
The construction and infrastructure sectors also leverage cold forging for various applications. Structural components, connectors, and specialty fasteners are some examples. The high strength-to-weight ratio achieved through cold forging makes it an attractive choice for engineers. Furthermore, the enhanced durability of cold-forged components translates to longevity in structures, reducing the need for replacements. This advantage makes cold forging a valuable manufacturing technique in building infrastructure.
Cold forging enhances performance and reliability across several sectors by producing parts that are strong, lightweight, and cost-effective.
The diverse applications of cold forging highlight its critical role in multiple industries. As the demand for efficient manufacturing methods grows, cold forging is likely to see increased utilization and innovation.
Technological Advancements in Cold Forging
Technological advancements play a vital role in the evolution of cold forging. Innovations enhance the efficiency, precision, and overall effectiveness of the cold forging process. These advancements not only streamline operations but also improve the quality of the final products. To stay competitive, industries must adapt to these new technologies, which bring numerous benefits.
Automation and Robotics
The integration of automation and robotics into cold forging represents a significant leap forward. Automated systems enable higher production rates and consistent quality, minimizing human error. Robotics can perform repetitive tasks, which increases productivity and reduces labor costs. Moreover, automation reduces workplace accidents by taking on dangerous duties.
Robotic arms are now used for various operations like loading materials, adjusting forging machines, and quality inspections. This level of technological integration allows for more intricate designs and faster turnaround times. The efficiency gained through automation also translates into lower operational costs, which is critical in a competitive market.
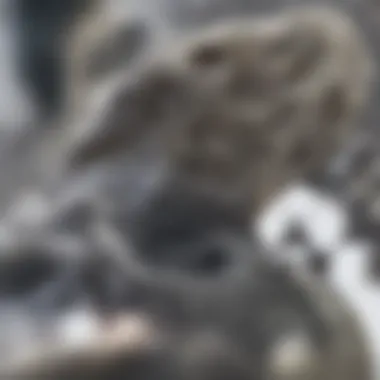
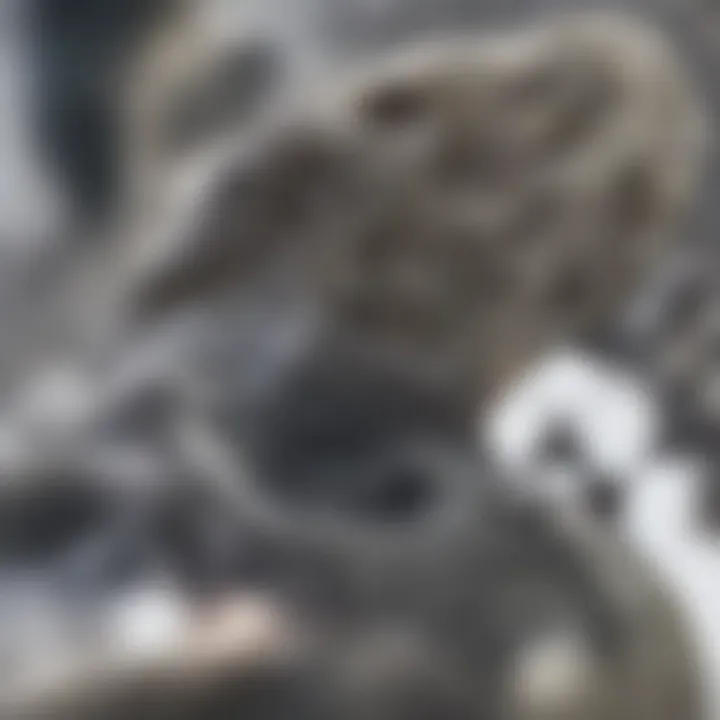
"Investing in automation is no longer an option, but a necessity to meet the growing demands and quality standards in manufacturing."
Advanced Materials Research
Advanced materials research is another key driver of progress in cold forging. The development of stronger, lighter, and more versatile materials expands the potential applications of cold forging. Researchers are exploring composite materials and alloys that improve performance characteristics while reducing weight.
Novel treatments and processes are also being researched to enhance the mechanical properties of conventional materials. For instance, the use of nanomaterials can improve strength without adding significant weight. These enhancements can lead to better fuel efficiency in automotive applications and improved performance in aerospace components.
The synergy between advanced materials and cold forging technology allows for products that meet high-performance requirements while also being cost-effective. As further research continues, cold forging is likely to benefit from new material innovations that will shape its future.
In summary, technological advancements in automation and materials science are transforming the landscape of cold forging. These elements play a crucial role in enhancing productivity, ensuring quality, and paving the way for future innovations.
Environmental Considerations
Cold forging is not just a technical process; it influences the environment significantly. Recognizing its environmental impact is essential for promoting sustainable manufacturing practices. This section explores two vital aspects of environmental considerations: energy consumption and material efficiency.
Energy Consumption Analysis
Energy consumption is a critical factor in cold forging operations. Unlike hot forging, which requires heating metals to high temperatures, cold forging operates at room temperature. This fundamental difference translates to lower energy usage. Cold forging can lead to significant energy savings when compared with traditional forging methods.
In cold forging, energy is primarily used in the machinery and the initial processing of raw materials. Efficient machinery can reduce overall energy consumption drastically, enabling manufacturers to optimize their production processes. The adoption of energy-efficient forging machines is thus critical to minimizing environmental impacts.
Consider implementing practices such as:
- Regular maintenance of machinery to ensure optimal performance.
- Upgrading equipment to more energy-efficient models.
- Analyzing the production process to identify areas for energy reduction.
These strategies not only benefit the environment but also reduce operational costs associated with energy consumption.
Recycling and Material Efficiency
Material efficiency plays a vital role in the sustainability of cold forging. The process inherently generates less scrap compared to other metalworking techniques. This reduced waste means that manufacturers can maximize the use of raw materials. Furthermore, utilizing recyclable materials in cold forging enhances sustainability.
Emphasizing the recycling aspects is crucial. For example, manufacturers can:
- Source raw materials that are made from recycled content.
- Reintroduce scrap metal into the production cycle.
- Collaborate with recycling partners to ensure responsible disposal of materials.
These practices contribute to a circular economy, where materials are continuously reused and recycled. The result is a smaller ecological footprint for the cold forging industry, aligning with global sustainability goals.
"Technology can provide solutions that are both economical and environmentally friendly when it comes to manufacturing practices."
Future Trends in Cold Forging
Cold forging is at a critical juncture, with emerging technologies and shifting market dynamics shaping its future. This section explores how innovation is influencing the cold forging landscape and what trends professionals should monitor.
Emerging Technologies
Innovations in cold forging technology are primarily driven by advances in automation and digital manufacturing.
- Automation: The integration of robotics in cold forging processes enhances efficiency. Automated systems can perform repetitive tasks with precision, reducing human error. This allows manufacturers to scale production without compromising quality.
- Digital twin technology: Manufacturers now create virtual models of forging processes. This technology assists in optimizing production by simulating different parameters, which helps identify the most efficient methods.
- Advanced sensors: The implementation of sensors in forging machines allows for real-time data collection. This data can inform maintenance schedules and predict failures, reducing downtime. Furthermore, it enables a more precise control of the forging process, leading to improved quality of the final products.
- Sustainable practices: Innovations focus on reducing waste and energy consumption. Techniques like warm forging, often seen as a hybrid between cold and hot forging, can enhance material properties while lowering energy demands.
These emerging technologies collectively contribute to a more efficient, cost-effective, and sustainable cold forging process. They present significant benefits for industries relying on precision components.
Global Market Outlook
The global market for cold forging is expected to expand steadily, driven by the increasing demand for precision parts in various sectors such as automotive, aerospace, and manufacturing.
- Market Growth: Various industry reports forecast a compound annual growth rate (CAGR) in the forthcoming years. A significant push in electric and hybrid vehicle production heightens the demand for lightweight and durable components that cold forging can provide.
- Geographical Trends: Asia-Pacific stands out as a leader in cold forging due to its massive automobile industry and increasing manufacturing capabilities. Countries like China and Japan are expected to dominate market share.
- Consumer Preferences: There is a growing emphasis on lightweight and energy-efficient products. Cold forging meets these requirements, making it an attractive option for manufacturers aiming to create sustainable products.
- Investment and R&D: Increased investment in research and development enables businesses to innovate cold forging technologies. This trend will likely include collaborations between manufacturers and tech firms to foster new solutions in production processes.
Culminations
The conclusion section serves as a crucial summation of the insights discussed throughout the article. It consolidates the core concepts of cold forging, reinforcing their significance in modern manufacturing. This part is vital not only for recapping the advantages and disadvantages of the process but also for connecting theoretical knowledge to practical applications. Understanding these elements helps industry professionals, scholars, and students appreciate the multifaceted nature of cold forging.
Summary of Key Points
- Definition and Overview: Cold forging is a metalworking process that shapes metals at ambient temperature, enhancing their mechanical properties.
- Process and Equipment: The methodology involves various specialized machines, such as forging presses and dies, designed for specific outcomes.
- Material Usage: Metals like steel, aluminum, and copper are commonly employed due to their favorable properties when subjected to cold forging techniques.
- Advantages: Key benefits include increased strength, cost-effectiveness, and excellently finished surfaces, which are essential for high-quality manufacturing.
- Limitations: Constraints are noted in terms of size and complexity of the finished products, along with initial tooling and equipment costs.
- Applications: The sectors benefiting from cold forging span automotive, aerospace, medical devices, and construction, showcasing its versatility.
- Innovation and Future Trends: Emerging technologies and a global market outlook indicate a promising future for cold forging, with automation and materials research driving progress.
Final Thoughts on Cold Forging
In light of the discussion, cold forging emerges as a process not only fundamental to various industries but also one that holds potential for significant advancements. Factors such as technological developments and environmental considerations will shape its trajectory in the coming years. Cold forging's ability to produce robust and precise components makes it a valuable method in the realms of manufacturing and engineering.
Investors, engineers, and educators alike must remain attentive to the evolving landscape of this critical process. The importance of continuous research and adaptation cannot be overstated, as the metalworking industry seeks more sustainable and efficient methods to meet global demands. For further reading on this topic, consult resources such as Wikipedia and Britannica.
"Cold forging is not merely a method; it is a cornerstone of modern engineering, offering strength and precision where needed most."