Understanding Powder Flow Testing: Key Insights
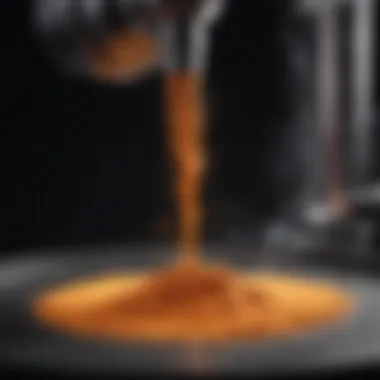

Intro
The powder flow test serves as a vital tool in assessing the flow behavior of powders across various industries. Understanding how powders flow is essential for optimizing production processes, ensuring quality in end products, and meeting safety regulations. By evaluating the flowability of powders, industries can predict how they will behave during handling, mixing, and processing. This understanding has significant implications in sectors like pharmaceuticals, food production, and materials science.
The methodologies employed in powder testing range from basic to advanced, focusing on different physical characteristics and flow properties. The results of these tests inform material selection, equipment design, and product formulation. As such, a comprehensive exploration of powder flow testing methodologies and their implications contributes to more effective industrial applications.
Research Overview
Summary of Key Findings
Powder flow tests reveal critical insights regarding the behavior of powders. Key findings indicate that:
- Flow Rate: Affects production speed and efficiency.
- Cohesion: Strongly influences packing and handling.
- Particle Size and Shape: Directly correlate with flow characteristics.
- Moisture Content: Alters flow behavior, which is vital during process formulation.
These elements highlight the necessity of proper testing in achieving both performance and efficiency in powder handling.
Background and Context
Historically, the study of powder flow began in response to the challenges faced in industries requiring bulk powder movements. Early techniques were rudimentary, yet as technology advanced, the methodologies became sophisticated. Today, modern tests utilize equipment such as the FT4 Powder Flow Tester or the Hausner Ratio method to provide concrete data. These tests have become part of standard practice, especially in pharmaceutical production, where they ensure that powders meet specific requirements for effective drug delivery.
Methodology
Experimental Design
Experimental design for powder flow testing typically involves various setups depending on the material being analyzed. Major aspects to consider include:
- Selection of Powders: Different types will yield different results.
- Testing Environment: Humidity and temperature must be controlled.
- Measurement Techniques: This may include shear cell testing or bulk density measurement.
Data Collection Techniques
Data collection in powder flow testing involves precise measurement of various parameters. The techniques commonly used include:
- Jenike Shear Test: Evaluates the cohesive strength of powders under different stress conditions.
- Bradford Tester: Measures the compressibility and flow properties.
- Cohesion Tests: Determine how well powders will flow under pressure.
Comprehensive analysis of the results helps to elucidate flow behavior, which can then be correlated with processing performance. This data becomes critical in product formulation and development, ensuring that qualities align with desired outcomes.
Foreword to Powder Flow Testing
Powder flow testing is a fundamental aspect in various fields, such as pharmaceuticals, food processing, and metallurgy. The ability to accurately assess the flow characteristics of powders directly influences processing efficiency and the quality of end products. Understanding this area opens pathways to enhance material performance and predict behavior during manufacturing processes.
Definition and Importance
Powder flow testing refers to the assessment of how powders behave under different conditions. This includes their ability to move through equipment, their interaction with other substances, and their response to external forces. The importance of this testing lies in several critical factors:
- Process Optimization: A thorough understanding of powder flow can lead to more efficient manufacturing processes. When powders flow well, they fill molds properly, ensuring uniform consistency in products.
- Quality Control: Assessing flow properties helps to maintain quality by reducing variability. Consistent powder behavior ensures that end products meet the desired specifications.
- Material Compatibility: Some powders do not behave similarly when mixed with others. Testing helps identify compatibility issues early in product development.
In essence, knowing how powders flow can significantly enhance productivity and product quality across various industries.
Historical Context
The study of powder flow characteristics is not new. Historically, the importance of powder properties has been recognized since ancient times, especially in areas such as metallurgy and pharmaceuticals. The evolution of powder characterization has followed advancements in material science, leading to the development of sophisticated testing methodologies.
Early experiments mainly relied on subjective assessments of powder behavior. As industrial processes became more complex, the need for standardized testing methods grew. Critical milestones include the establishment of ASTM D1895 and similar standards that provided guidelines on measuring flow attributes. Today, numerous instruments and methodologies are available to assess powder flow, representing a significant advancement in this field.
Through its historical context, it becomes clear that powder flow testing is not just a technical necessity; it is a pivotal aspect that has shaped modern practices in numerous industries. Leveraging this knowledge can lead to better innovations and improvements in processing methods.
Fundamentals of Powder Flow
Understanding the fundamentals of powder flow is crucial for anyone involved in the processing and application of powdered materials. This segment sheds light on the different physical characteristics and factors that directly influence flowability. Comprehending these elements is essential not only for optimizing formulations but also for ensuring consistent product performance across various industries.
The behavior of powders during processing can significantly affect the efficiency of manufacturing procedures. By analyzing the intrinsic characteristics of powders, professionals can draw clearer conclusions about how to handle materials efficiently. The implications of flow behavior are vast, affecting everything from product quality to safety during manufacturing processes.
Physical Characteristics of Powders
The physical characteristics of powders hold immense significance in determining how they behave during flow. Key attributes such as particle size, shape, and distribution directly impact their flowability. Understanding these properties allows engineers and product developers to tailor their materials to meet specific powder flow characteristics that are necessary for their applications.
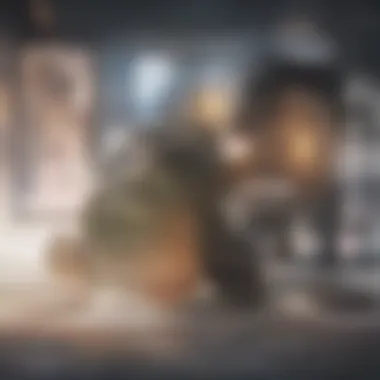

Factors Influencing Flowability
Flowability is influenced by a myriad of factors. Each factor interacts uniquely with the specific powder being used. A deeper dive into the primary characteristics shows how they can enhance or hinder powder flow.
Particle Size
The particle size of a powder is a fundamental aspect influencing its flowability. Smaller particles tend to have higher surface areas relative to their mass, which can lead to increased cohesion among particles. This can restrict flow. Conversely, larger particles may flow more freely but can also create segregation issues in mixtures.
The key characteristic of particle size's influence is how it affects the packing and movement of the powder in bulk. This is often a beneficial consideration in the design of processes relying on reliable flow characteristics. A unique feature is the relationship between size distribution and flow properties; more uniform distributions often enhance flowability, while broader distributions may introduce challenges.
Shape and Morphology
Shape and morphology play significant roles in defining how powders behave. Irregularly shaped particles may interlock better, which can enhance stability but also impede flow. In contrast, spherical particles tend to roll and slide over each other, reducing friction and enabling better flow.
The main characteristic of shape lies in its effect on packing density. Higher packing density can lead to increased flow resistance in certain formulations. Yet, this can be a beneficial feature when stability is required. A unique challenge lies in maintaining functionality while optimizing the shape of the powders used, particularly for specialized sectors such as pharmaceuticals.
Moisture Content
Moisture content is another critical factor impacting powder flow behavior. The presence of moisture can induce cohesion among particles, leading to clumping that obstructs flow. On the other hand, appropriate moisture levels may enhance flowability by reducing static charge and friction.
The key characteristic here is balance. An optimal moisture content is beneficial, helping to maintain flowability without compromising powder properties. The issue arises with variations in humidity, which can lead to unpredictable flow characteristics in environments where powders are stored or processed. Thus, understanding moisture content is essential for mitigating risks associated with flowability in dynamic conditions.
Understanding the fundamentals of powder flow is essential for professionals aiming to optimize their processes and improve product consistency across various industries.
Testing Methodologies
Testing methodologies for powder flow are essential for understanding how different powders behave during processing. These methodologies help determine the flow characteristics of various powders, which can significantly impact manufacturing processes, product formulation, and end-use performance. Analyzing the flow behavior of powders assists industries in optimizing their operations and achieving consistent product quality.
Cohesive and Free-Flowing Powders
Cohesive powders tend to clump together due to intermolecular forces. These powders often exhibit low flowability and can lead to challenges during processing. Examples include powders used in pharmaceuticals, where compactness and uniformity are crucial.
On the other hand, free-flowing powders, such as granulated sugar or flour, flow smoothly and easily through processing equipment. Understanding the distinction between these two types is vital for selecting the appropriate testing methodologies. It also helps industries to choose the right additives or processing techniques to improve flow properties.
Commonly Used Instruments
Several instruments are popular in powder flow testing, each with unique features and characteristics.
Carr Assessment
The Carr Assessment, also known as the Carr Index, is a widely used method to evaluate powder flow behavior. It focuses on measuring the powder's density and cohesion through both tapped and bulk density measurements. This method is a popular choice due to its simplicity and effectiveness in providing insights into flowability.
A key characteristic of the Carr Assessment is its ability to quantify cohesiveness through the Carr Index, which is derived from the ratio of tapped density to bulk density. This quantification allows scientists and engineers to predict how the powder will behave in specific workflows.
However, the Carr Assessment has limitations. It may not provide enough detail about critical factors such as particle shape or size distribution. While it efficiently assesses flowability, it should ideally be used in conjunction with other methodologies for comprehensive analysis.
Hall Flow Test
The Hall Flow Test measures the time taken for a specific volume of powder to flow through an orifice. This method is beneficial for understanding the flow properties of powders that may not be cohesive.
Key aspects of the Hall Flow Test include its straightforward setup and the ability to provide quick results. This method is particularly beneficial when assessing free-flowing powders. The Hall Flow rate is indicative of how well a powder will flow under gravity, making it a useful tool in various industries including food and pharmaceuticals.
A unique feature of the Hall test is its ability to discern the flow rate based on different mass scales and profiles. However, it may overlook the interactive effects of moisture content or particle morphology, which are important factors in powder flow behavior.
Bulk Density Measurement
Bulk density measurement involves calculating the mass of a powder divided by its volume, including void spaces. This method provides insights into the powder's packing characteristics and is valuable in predicting how powders will behave in storage and during processing.
The key characteristic of bulk density measurement is its ability to highlight differences in flow properties caused by variations in particle size, shape, and the presence of air pockets. The beneficial nature of this technique lies in its simplicity and fundamental approach to quantifying powder behavior.
One drawback is that bulk density alone may not reflect the complexities of powder interactions and flow dynamics in real processing environments. For thorough analysis, bulk density should be part of a multimodal testing strategy that includes other relevant assessments.
In powder flow testing, multiple methodologies are often necessary to form a complete picture of material behavior.
Selecting the right testing methodology requires careful consideration of the powder type, desired outcomes, and specific processing conditions. A nuanced understanding of cohesive and free-flowing powers, along with the instruments available for testing, enhances the ability to produce high-quality products efficiently.
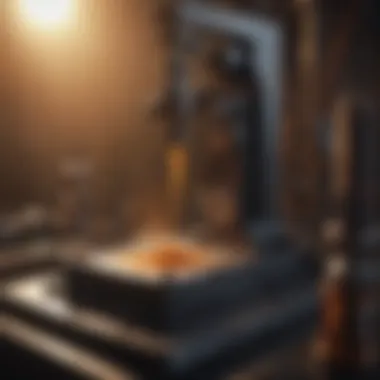

Key Testing Standards
Testing standards play a crucial role in powder flow assessments. They provide guidelines that ensure consistency, reliability, and comparability of results across different laboratories and applications. Understanding these standards helps industries adopt best practices, leading to improved product performance and process efficiency.
Standards such as ASTM and ISO establish methods for evaluating flow properties of powders. They define specific procedures and equipment needed for accurate testing, which is essential for industries relying on powder handling. The benefits of adhering to these standards are significant. They promote uniformity in testing, enhance reproducibility of results, and facilitate communication across stakeholders.
When industry professionals apply these standards, they gain confidence in their results. This trust is vital for quality control and assurance processes. Also, organizations that follow recognized standards often achieve better regulatory compliance, which can lead to reduced risks during production.
ASTM Standards
ASTM D1895
ASTM D1895 focuses on measuring the particle size distribution and shape of powders. This standard is significant as it provides a clear framework for understanding how these factors influence flowability. A key characteristic of ASTM D1895 is its ability to assess the flow properties under controlled conditions. This precision allows for detailed analysis of powder behavior, essential for consistent quality in production.
One unique feature of ASTM D1895 is its inclusion of both bulk and tapped density measurements. These offer insights into how powders will behave when stored or transported. The advantages include its widespread acceptance and ease of use, making it a popular choice for many industries, such as pharmaceuticals and food processing. However, it does have limitations. For instance, it may not account for certain cohesive powders adequately, leading to potential misinterpretations of flow characteristics.
ASTM D4179
ASTM D4179 deals with the assessment of the flowability of free-flowing powders. Its main contribution to this field lies in its detailed methodology for evaluating powder behavior during processing. A key characteristic of ASTM D4179 is the emphasis on understanding how powders resist flow under various conditions, which is crucial for optimizing manufacturing processes.
This standard is well regarded for its balance of simplicity and robustness, making it accessible for various applications. One unique feature of ASTM D4179 is its focus on the measurement of flow through orifices, helping predict how a material behaves during bulk handling. This can be beneficial when designing equipment or storage solutions. However, one drawback is that it may not fully encompass the complexities of all powder types, particularly those with high cohesiveness.
ISO Standards
ISO standards for powder flow testing provide an additional layer of guidelines applicable on an international scale. They aim to harmonize testing methods worldwide, ensuring that results from different sources can be compared and validated effectively. Buffered by the global nature of many industries, ISO standards are instrumental in establishing a baseline for flow testing.
These standards promote best practices in powder handling and processing, making them an essential reference for companies engaged in international trade or collaborations. Moreover, the thoroughness of ISO standards supports quality assurance procedures, ultimately benefiting product consistency and safety.
Interpreting Powder Flow Test Results
Interpreting powder flow test results is a critical step in understanding how powders behave during processing and application. It provides insights into flowability metrics, which are essential for industries that handle bulk materials. The outcome of these tests can significantly affect product quality, efficiency of processing, and ultimately the success of industrial operations.
Proper interpretation allows professionals to make informed decisions. For instance, it can influence process settings, ensure consistency in production, and enhance product development. Understanding the results also unveils the relationship between the physical characteristics of the powder and its performance in various applications. This understanding is paramount in industries such as pharmaceuticals, food processing, and metallurgy where material behavior is crucial.
Understanding Flowability Metrics
Flowability metrics help quantify how easily a powder can flow under specific conditions. Common metrics include:
- Cohesion: Relates to the internal forces between particles. High cohesion may lead to clumping, which affects flow.
- Angle of Repose: Indicates the maximum angle at which a powder remains stable. A lower angle suggests better flowability.
- Compressibility: This metric describes how much a powder decreases in volume under pressure. Greater compressibility can indicate issues in processing.
These metrics provide a benchmark for comparing various powders. They assist researchers and engineers in selecting appropriate materials for specific applications, ultimately enhancing product reliability and performance.
Common Pitfalls in Interpretation
Interpreting results requires careful consideration. Several pitfalls can compromise the accuracy and applicability of conclusions. Key challenges include:
- Ignoring Environmental Factors: Temperature and humidity can alter flow characteristics. Failing to control or report these conditions leads to skewed results.
- Overgeneralizing Results: Each powder behaves differently; results from one type cannot universally apply to another without validation.
- Inadequate Data: Not taking enough measurements can cause significant variability in results. It is essential to have a robust dataset for reliable interpretation.
Proper awareness of these pitfalls is vital. A comprehensive understanding can aid in making better operational choices and achieving optimal results in product formulation.
"The ability to interpret powder flow test results accurately is not just an academic exercise; it is a practical necessity for ensuring product consistency and reliability in advanced material applications."
By avoiding these common mistakes and focusing on accurate data collection and analysis, professionals can significantly enhance the effectiveness of their powder processing techniques. The consequences of correct interpretations are profound, affecting everything from manufacturing processes to quality assurance in final products.
Applications in Industry
The applications of powder flow testing are vast and significant in various industries. This testing is critical as it assesses how powders behave during processing and ultimately influences product quality. Understanding the flow characteristics of powders helps industries optimize their processes, reduce waste, and enhance product consistency. Each sector benefits differently, but all share a common goal of improving efficiency and maintaining high standards.
Pharmaceutical Sector
In the pharmaceutical industry, the quality of drug formulation is paramount. Powder flow testing helps in ensuring consistent dosing and uniformity in drug composition. For instance, if a powder exhibits poor flowability, it may lead to variations in tablet weight or active ingredient concentration, which can affect product efficacy and safety.
Pharmaceutical companies often use flow testers to assess the cohesiveness of their powders. Products like Carr Assessment and Hall Flow Tests provide insight into how powders will behave in large-scale manufacturing. It becomes crucial when considering excipients, which can enhance or inhibit flow. Thus, knowing the flow properties helps formulators make informed choices about processing methods and machinery, leading to better end products.
Food Processing
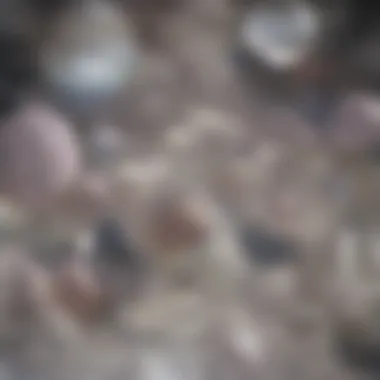

Food processing industries heavily rely on powder flow testing to ensure that ingredients mix well and maintain consistent quality. The behavior of powdered food ingredients during mixing, transportation, and storage can affect texture, taste, and nutritional value. For example, variations in flowability can result in inconsistent flavor distribution in powdered mixes.
Heavy reliance on powders, such as flour and spices, means that understanding their flow properties is essential. Good flowability ensures efficient manufacturing processesโfrom blending to packaging. Moreover, food safety standards necessitate rigorous testing of ingredients, thus establishing the importance of powder flow tests in this field.
Powder Metallurgy
Powder metallurgy is another industry where powder flow tests are critical. In this process, metal powders are shaped and sintered to create solid components. The ability to predict how uniformly the powder flows during pressing determines the quality and strength of the finished product. Poor flow can result in inadequate density and dimensional consistency, leading to mechanical failures.
Specific flow tests help determine the suitability of metal powders for different applications. For instance, the ability of metal powders to flow influences the choice of dies and the parameters of the sintering process. Therefore, understanding powder flow becomes essential for achieving specified mechanical properties.
"Understanding powder flow behavior is fundamental to improving industrial processes that rely on powder materials."
Overall, a thorough grasp of powder flow testing aids industries in not just optimizing production but also in ensuring compliance with industry standards. Each sector has specific considerations, but all can leverage these methodologies for better performance and product quality.
Case Studies
Case studies are pivotal in emphasizing the real-world application of powder flow tests across various industries. They provide practitioners and researchers with tangible examples of how theoretical knowledge translates into practical outcomes. By analyzing specific instances, one can appreciate the complexities involved in powder behavior and the implications of flow tests on product development and processing efficiency.
In this article, two key sectors will be explored through the lens of case studies. These sectors are pharmaceutical formulations and food product consistency. Each case study will reveal critical insights about the role of powder flow tests and illustrate their importance in maintaining quality and performance.
Pharmaceutical Formulations
Pharmaceutical formulations require precise and consistent powder flow properties to ensure uniformity in drug doses. An example can be drawn from a case study involving the formulation of a powdered medication. In this instance, the flowability of the active pharmaceutical ingredient (API) was tested using the Carr Assessment. The results indicated that variations in particle size distribution adversely affected flow characteristics.
Such findings are significant. They guided the formulation team to adjust the milling process in order to achieve a more uniform particle size. This adaptation ultimately allowed for enhanced dosing accuracy and reproducibility of the final product.
Continuous monitoring using powder flow tests will help in identifying potential issues before they lead to larger production problems, thereby safeguarding patient safety and product efficacy.
Food Product Consistency
The food industry also illustrates the relevance of powder flow tests through a notable case study on flour consistency in baking products. In this situation, the Hall Flow Test was used to assess the flowability of various flour samples. The results revealed inconsistencies that could potentially affect the texture and quality of baked goods.
Bakers can use these insights to modify processing parameters, like improving storage conditions to reduce humidity. This intervention helps stabilize the flowability of flour, ensuring consistent performance during production.
Understanding the flow behavior of food powders is essential in achieving desired product features. This is paramount not just during production, but also in maintaining the high standards expected in finished goods.
Through these case studies, the relevance of powder flow testing methodologies becomes clear. They provide a framework for understanding practical implications, ultimately enhancing both product quality and process efficiency.
Future Trends in Powder Flow Testing
The landscape of powder flow testing continues to evolve with significant advancements in technology and methodologies. Understanding these trends is essential for industries that rely on the efficient handling and processing of powdered materials. As industries such as pharmaceuticals, food processing, and powder metallurgy increasingly demand precision and efficiency, the role of innovative powder flow testing methodologies becomes critically important.
Technological Advancements
Technological advancements in powder flow testing are vital for improving accuracy and reliability. Modern testing devices now include sophisticated features like real-time monitoring and enhanced data analysis capabilities. For instance, instruments such as the Freeman Technology FT4 Powder Rheometer provide comprehensive flowability metrics that were previously unattainable. These advancements allow for a more precise understanding of powder behavior under various conditions.
Moreover, the integration of digital technologies, such as machine learning algorithms, enables predictive modeling of powder behavior. This approach not only enhances the understanding of material properties but also supports decision-making related to formulation and production processes. Recognizing and adapting to these technological changes can provide competitive advantages in the marketplace.
Integration with Automation
The integration of automation in powder flow testing represents another significant trend. Automated systems can streamline the testing process, reduce human error, and increase the throughput of tests. In automated settings, sensors and control systems monitor parameters and adjust processes in real time, ensuring consistent and reliable results. This is especially beneficial in large-scale manufacturing environments, where time and accuracy are paramount.
Furthermore, automation facilitates the implementation of quality control measures at various production stages, ensuring that powders meet the required specifications. The ability to continuously monitor flow characteristics not only enhances operational efficiency but also improves product consistency.
"The future of powder flow testing lies in seamlessly integrating advanced technologies and automation into processes to elevate both precision and efficiency."
As industry demands continue to rise for swift and reliable results, staying informed about these trends will be essential for professionals in the field. Well-informed adaptations to testing methodologies will lead to more effective product formulations and better overall material performance.
Finale
In the realm of material science, understanding powder flow testing is of utmost importance. This conclusion synthesizes the essential elements covered in the article, highlighting the significance of powder flow testing methodologies and their implications for various industries. The insights gained from powder flow tests not only inform material selection but also optimize processes across sectors like pharmaceuticals, food processing, and powder metallurgy.
Summary of Findings
The findings throughout this article underscore the critical role that powder flow testing plays in evaluating the flow characteristics of powders. Key points include:
- Definition and Relevance: Powder flow testing evaluates how powders behave under specific conditions, which can affect processing efficiency.
- Methodological Diversity: Various testing methodologies, such as the Carr Assessment and Hall Flow Test, provide a range of insights depending on powder behavior.
- Industry Standards: Adhering to established standards like ASTM D1895 and ASTM D4179 is vital for ensuring test accuracy and consistency.
- Applications: Understanding powder flow can dramatically improve formulations in pharmaceuticals, ensure product consistency in food processing, and enhance production in powder metallurgy.
Final Thoughts
Reflecting on the information presented, it is clear that mastering powder flow testing methodologies is essential for professionals engaged in material science. The implications of powder flow behavior extend beyond mere academic interest. Industry practitioners must grasp these concepts to optimize their processes effectively. As advancements in technology continue to remodel testing frameworks, integrating these methodologies into everyday practice enhances operational efficacy and product quality. Continuous education and adaptation will remain crucial as industries evolve. The future of powder flow testing will likely see increased reliance on automated systems, providing comprehensive insights into powder behavior. Thus, staying informed and adaptable ensures that industries can harness the full potential of their powder handling processes.