Understanding Rapid Mix: Importance and Applications
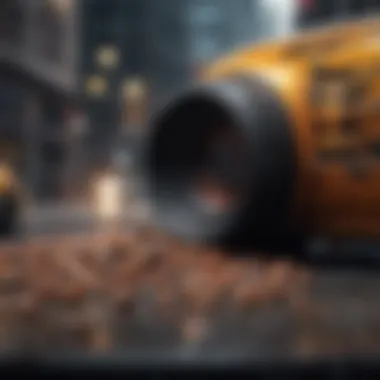
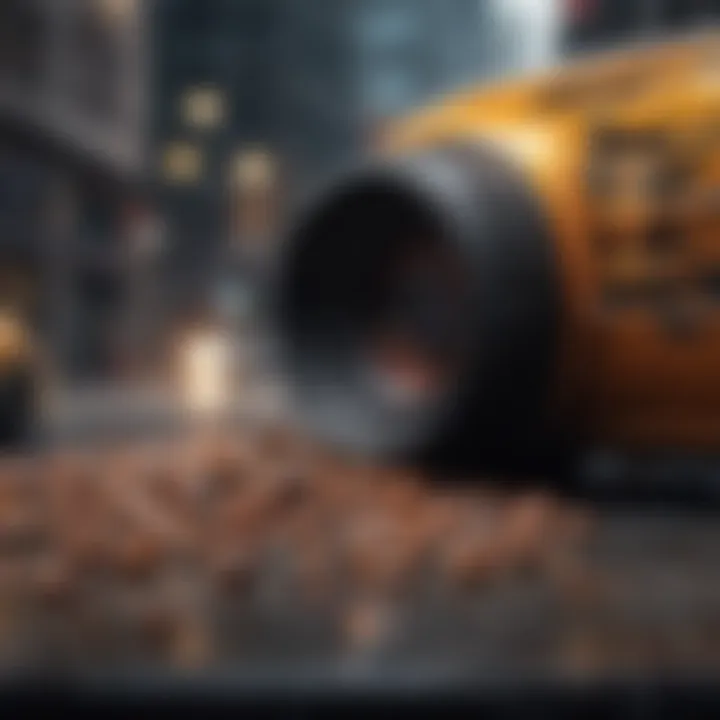
Intro
The realm of mixing processes plays a crucial role in numerous scientific and industrial applications, yet often slips under the radar. At the heart of these processes is rapid mix, a concept that ensures optimal interactions between materials, facilitating everything from the development of pharmaceuticals to enhancing environmental solutions. Given its broad implications, understanding the intricacies of rapid mixing can elevate both academic inquiry and practical implementation.
In this exploration, we will set the stage by peeking into why rapid mix matters. Understanding its mechanics not only aids in the efficiency of reactions and formulations but is also pivotal in tackling contemporary challenges in material science and environmental sustainability. Through a cohesive narrative, we’ll journey through fundamental theories, methodologies applicable in various scenarios, and investigate innovative techniques to push the boundaries of conventional mixing.
The significance of rapid mix cannot be overstated—it forms the backbone of numerous processes that shape our modern society. The purpose of this article is to bridge theoretical insights with practical implications, helping students, researchers, and professionals alike gain a comprehensive view of this essential topic.
Research Overview
Summary of Key Findings
A thorough examination of existing literature reveals several critical insights about rapid mix:
- Efficiency of Mixing: Effective mixing significantly improves reaction rates and product uniformity. Studies show that optimizing mixing parameters can lead to a range of outcomes from better yields in chemical production to enhanced material properties.
- Impact on Chemical Reactions: Rapid mixing can affect not only the kinetics of reactions but also the thermodynamics. When mixing times are minimized, reactions that might otherwise proceed sluggishly become feasible.
- Application Diversity: The principles of rapid mixing extend beyond chemistry into fields such as food technology, environmental engineering, and even biomedical applications. Each domain benefits uniquely from enhanced mixing techniques.
Background and Context
To truly appreciate the evolution of rapid mixing, it’s important to delve into its historical backdrop. The concept has roots tracing back to early chemical engineering practices but has expanded significantly over decades due to advancements in technology.
Today, methods such as high-shear mixers, static mixers, and impingement mixers exemplify technical growth. Furthermore, as industries transition toward more sustainable practices, the need for efficient mixing processes becomes increasingly pressing. That's becasue it directly correlates with resource utilization and waste reduction—an essential aspect in the fight against climate change.
"Innovations in rapid mixing technologies not only enhance productivity but also contribute to more sustainable industrial practices."
Understanding the nuances of these developments is key for anyone in the scientific community. Grasping historical contexts enables professionals to better project future trends in rapid mix applications. This foundational knowledge serves as a building block as we explore specific methodologies
Methodology
Experimental Design
In the sphere of rapid mixing research, the experimental design often focuses on comparing various mixing techniques. Researchers employ both qualitative and quantitative approaches to assess mixing efficiency. For example, a common method is to employ tracer studies—using a dye or marker that allows scientists to visually observe the mixing process and measure how quickly homogeneous mixtures are achieved.
Data Collection Techniques
Data collection for understanding rapid mixing typically involves:
- Viscosity Measurements: Measuring the fluid's resistance to flow helps evaluate the impact of mixing on rheology.
- Reaction Kinetics: Through monitoring the rates of chemical reactions over time, researchers can draw connections between mixing conditions and outcomes.
- Particle Size Analysis: This technique assists in determining the distribution of solid particles in a mixture, which is directly affected by how well substances are mixed.
These methodologies lay the groundwork for innovative studies aimed at optimizing rapid mixing processes across various fields.
Defining Rapid Mix
In the realm of science and engineering, the term rapid mix is more than just a buzzword; it represents a cornerstone concept that influences a wide variety of processes. Understanding what rapid mixing entails is crucial for anyone interested in chemical reactions, material synthesis, or environmental applications. At its core, rapid mixing refers to the swift and effective blending of substances to achieve homogeneity, often in a short span of time. This technique is not merely a matter of convenience but a necessity in various fields where consistency and uniformity are pivotal to the outcomes of experiments and industrial processes.
Basic Principles of Mixing
Having a grasp of the basic principles of mixing is essential in comprehending rapid mix. Fundamentally, mixing involves several physical and chemical phenomena that dictate how materials combine. Factors such as velocity, viscosity, and density play significant roles in determining how quickly and effectively two or more materials intermingle.
- Mechanical Agitation: Often achieved through stirring or shaking, mechanical agitation introduces energy into the system, promoting interaction between particles. The speed at which this energy is applied can greatly alter the efficiency of the mixing process.
- Diffusion: A slower process in comparison to mechanical agitation, diffusion is the movement of particles from areas of high concentration to low concentration. This natural tendency helps achieve a uniform distribution of materials over time.
- Turbulence: In certain applications, inducing turbulence can dramatically enhance mixing efficiency, ensuring that even the most stubborn materials find a way to blend.
Rapid mixing techniques exploit these principles to minimize time and maximize efficiency. By understanding these fundamentals, one can appreciate the intricate dance of molecules during mixing that affects everything from the final product’s texture to its chemical reactivity.
Importance in Scientific Research
The significance of rapid mixing in scientific research cannot be overstated. In research labs, where precision and accuracy are paramount, the method of mixing directly affects experimental outcomes. Poor mixing could lead to inconsistent results, which could skew data interpretations and conclusions. Here are a few ways rapid mixing stands out in scientific pursuits:
- Enhanced Reaction Rates: In chemical reactions, particularly those that are time-sensitive, effective mixing ensures that reactants come into contact quickly, facilitating swift reaction rates.
- Uniform Material Properties: For researchers in material science, consistent material properties are critical. Rapid mixing ensures that composite materials are free from defects caused by uneven distribution of components.
- Improved Safety: In processes involving toxic or hazardous materials, rapid mixing minimizes the risks associated with prolonged exposure or reaction time. Quick blending helps to reduce the chances of accidents by ensuring safer handling conditions.
"Effective mixing is the silent hero in achieving successful outcomes that scientists often take for granted."
As rapid mixing becomes more integrated into various fields, understanding its dimensions will empower both young students and seasoned professionals to harness its full potential in their work. This insight not only enlightens the research community but also lays the groundwork for future innovations in mixing technology.
Mechanisms of Rapid Mixing
Understanding the mechanisms behind rapid mixing is pivotal as it lays down the framework for optimizing processes across an array of scientific and industrial applications. As the intricacies of fluid behavior come into play, researchers and professionals alike are better equipped to enhance efficiency, improve outcomes, and innovate strategies in fields ranging from chemical engineering to environmental science.
Fluid Dynamics and Mixing
Fluid dynamics is at the heart of mixing processes, governing how different substances interact. When we think about mixing, we’re often referring to how fluids of various densities and viscosities come together to form a homogeneous solution. Concepts such as laminar flow and turbulent flow come to the forefront here.
In turbulent flow, for example, the chaotic and irregular motion of fluid particles enhances mixing effectiveness dramatically. This is particularly essential in processes where time is of the essence, like during chemical reactions that are highly temperature sensitive. The actual mechanics can be complex, but to keep it simple: ever seen a storm brewing? The swirling winds and swirling clouds are akin to how fluid dynamics can induce mixing on both a macro and micro scale.
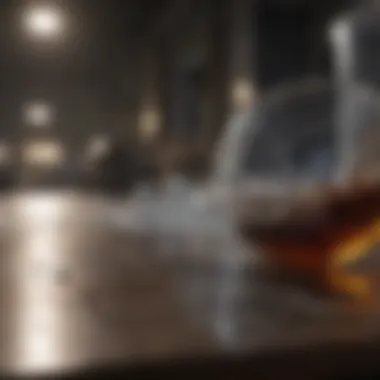
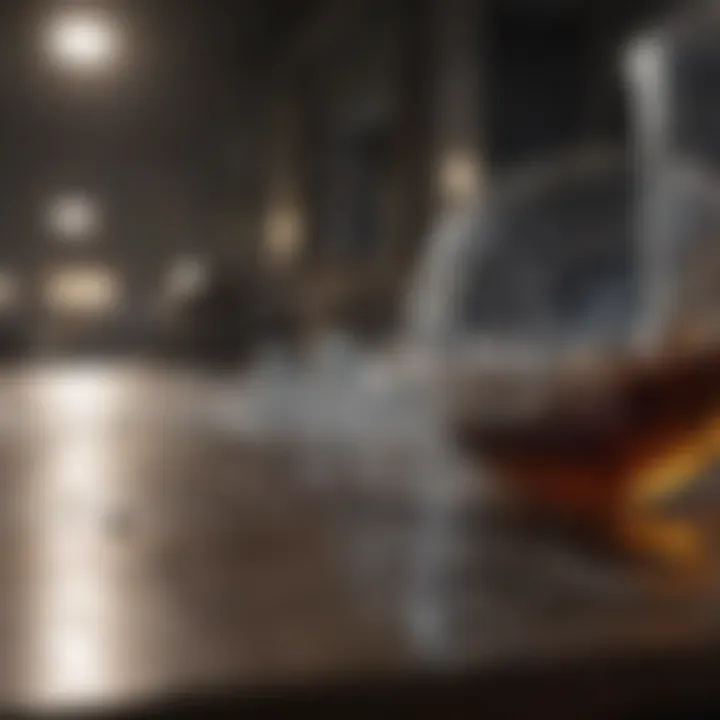
"Understanding flow dynamics is like grasping the pulse of a river; it tells you how fast, how deep, and how currents interact.
In practical applications, this principle can lead to robust designs for mixing systems that cater specifically to the unique flows of reactants, such as in a reactor where diverse chemicals converge. Consider a common kitchen scenario: whipping cream involves a lot of motion and fluid dynamics—the chaotic mixing creates a uniform product by incorporating air. Just as in cooking, precision in application often leads to a better result.
Mechanical Stirring vs. Hydrodynamic Mixing
When considering ways to mix fluids, two primary methods often come into discussion: mechanical stirring and hydrodynamic mixing. Each has its own place in various applications.
Mechanical stirring typically uses blades or paddles to induce mixing. It’s a straightforward approach—think about how a chef stirs soup with a ladle. This method is easily adaptable and, in some settings, it's the go-to option due to its simplicity and control. However, it can lead to localized mixing and uneven distribution if not monitored properly, which can be a downside in reactive processes where uniformity is critical.
On the flip side, you have hydrodynamic mixing, which harnesses the forces of fluid motion itself. This approach often leads to better mixing uniformity as it leverages natural flow dynamics. You could liken it to a waterfall that blends rainwater into a river; the water does not just combine at the surface but integrates through layers, ensuring a uniform mix. While hydrodynamic mixing can be more complex to set up, in many cases, it achieves results more efficiently.
In the grand scheme of things, the choice between mechanical stirring and hydrodynamic mixing hinges on specific project requirements—speed, efficiency, and the nature of the materials being mixed all play pivotal roles. As industrial applications are pushed to the limits of precision and efficiency, understanding these mechanisms is vital to streamline processes and enhance product quality.
Applications in Chemical Engineering
Chemical engineering is a field that thrives on understanding how different elements interact and react, often requiring precise control of processes. Rapid mixing plays a pivotal role in enhancing efficiency and effectiveness across various applications, making it a foundational topic in this discipline. The ability to mix materials quickly and uniformly not only optimizes reactions but also ensures consistent product quality. Let’s delve into two critical aspects of rapid mixing in chemical engineering: process optimization in reactor design and the integral role it serves in catalysis.
Process Optimization in Reactor Design
In the realm of reactor design, achieving the perfect mix is akin to hitting the bullseye in archery; it requires precision and a keen understanding of dynamics. Optimizing mixing within reactors can significantly influence outcome yields, energy consumption, and overall production rates. When materials are mixed effectively, reactions can occur uniformly, reducing hot spots or cold spots that might lead to incomplete reactions or even side reactions that could create unwanted byproducts.
- Factors Influencing Optimization: A couple factors influence the degree of effective mixing. These include fluid properties such as viscosity and density, as well as the reactor's geometry. A taller reactor might favor gravitational settling, while a wider design promotes lateral flow dynamics.
- Technological Considerations: Operators and engineers now employ sophisticated computational fluid dynamics (CFD) simulations to foresee how different designs will perform. These simulations allow for adjusting parameters like agitator speeds and mixing times, ensuring that the design choices align with the desired outcomes before physical implementation.
Additionally, well-optimized processes lead to sustainable practices. By maximizing the yield in existing setups, companies can defer costly expansions or reduce energy use, aligning their operations with global demand for sustainability.
Role of Rapid Mixing in Catalysis
Fast and efficient mixing is particularly important when it comes to catalytic processes. Catalysis involves enhancing the rate of a chemical reaction through a catalyst, which is often in a different phase than the reactants. This disparity can create challenges, as the catalyst must consistently come into contact with the reactants to ensure maximum efficiency.
In this context, rapid mixing helps to:
- Ensure that reactants quickly and uniformly distribute across the catalyst’s surface area, maximizing exposure.
- Minimize the time reactants spend before they interact with the catalyst, thus speeding up the overall reaction.
Moreover, integrating rapid mixing into catalytic processes can unveil new pathways for reaction intensification. When mixing is rapid and effective, it may lower the energy required for reactions, which can lead to cost savings in both energy and raw materials.
Combining state-of-the-art mixing technology with catalysis can even lead to the development of novel, more efficient reactions that were previously unconsidered. This synergy not only fosters innovation in the field but also promotes a broader understanding of reactant behavior and interaction under different conditions.
In the words of a renowned chemical engineer: "The art of mixing is every bit as vital as the science of chemistry itself. Without proper mixing, we would be grasping at straws in the fog of chaos.
The future of chemical engineering clearly leans heavily on effective rapid mixing techniques. As scientists continue to explore and refine these processes, the implications for both efficiency and sustainability will likely be profound.
Impact on Material Properties
In the realm of rapid mixing, understanding how this process influences material properties is pivotal. This facet reveals not merely the behavior of particles in suspension but also the overall outcome of industrial and experimental endeavors. By getting to the crux of material characteristics affected by mixing, researchers and practitioners can optimize processes for desired results. This section dives into two critical subcategories: the influence on particle size distribution and the effects on bulk density and moisture content.
Influence on Particle Size Distribution
Particle size distribution significantly impacts many processes in both chemical engineering and material science. When mixing happens rapidly, particles are forced to interact more efficiently. This interaction can lead to a narrower size distribution.
- Why is this significant? A narrower distribution often means that the product will have improved consistency in quality, essential in fields like pharmaceuticals and food processing. Uniform particle sizes help in achieving uniform reactivity and predictable dissolution rates.
In contrast, if mixing is inadequate, larger particles persist while smaller ones might agglomerate, leading to a wide size distribution. These changes can impair the desired characteristics in any final product.
Overall, understanding particle size distribution is crucial for:
- Enhancing product uniformity
- Optimizing reaction rates in chemical processes
- Ensuring proper functionality of ingredients in formulations
"A finely-tuned mixing process can be the difference between a successful formulation and a failure in production."
Effects on Bulk Density and Moisture Content
Another pivotal aspect influenced by rapid mixing is bulk density and moisture content. Bulk density refers to how much mass of material occupies a certain volume, affected by the arrangement of particles within a mixture. In scenarios of effective mixing, materials tend to achieve a more compact and homogenous structure, resulting in increased bulk density.
- Why does bulk density matter? Higher bulk density can lead to enhanced transportation efficiency and reduced costs in storage. Moreover, in construction and material design, precise bulk density ensures the reliability of structures and products.
Moisture content is equally critical, especially in sectors where products must retain certain levels of hydration, such as food and pharmaceuticals. Rapid mixing allows for more uniform distribution of moisture, ensuring that all components reach an optimal level. If mixing isn't done correctly, moisture may be unevenly distributed, leading to spoilage or compromised product quality.
Ultimately, understanding the interplay between rapid mixing and these often-overlooked material properties is key to optimizing performance across various industries. Ensuring proper sizing, density control, and moisture levels can lead to enhanced stability and longevity of the final product.
Environmental Relevance
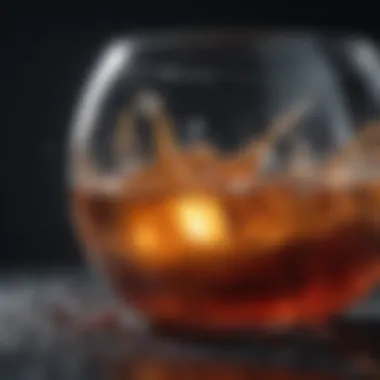
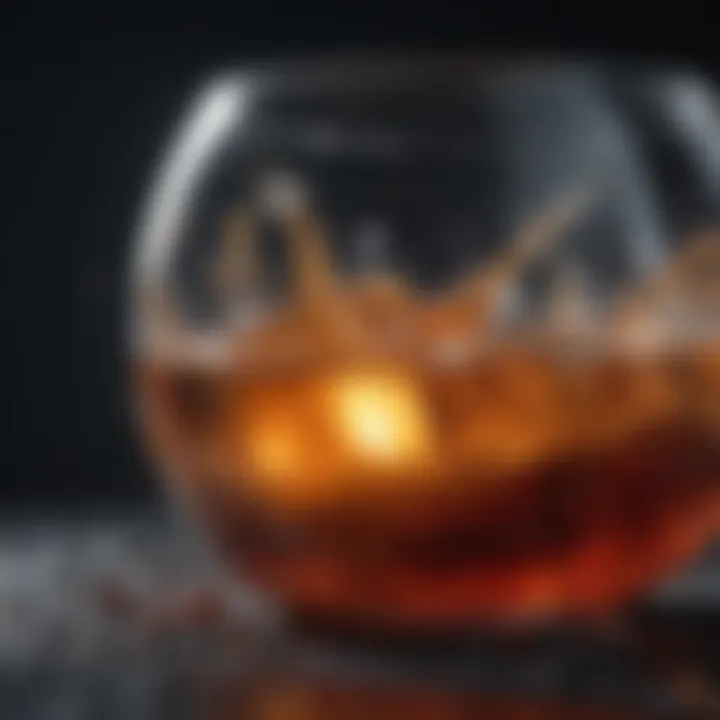
The significance of rapid mixing extends far beyond the confines of laboratory walls and industrial plants. It finds an essential place in environmental sciences, chiefly due to its role in improving various critical processes. Understanding the environmental relevance of rapid mixing unveils how it aids in tackling some pressing issues we face today, ranging from wastewater management to air quality improvements.
Rapid Mixing in Wastewater Treatment
Rapid mixing in wastewater treatment plants is crucial. When organic and inorganic pollutants enter water bodies, they can wreak havoc on ecosystems, not to mention public health. Rapid mixing ensures a homogenous mixture of wastewater and treatment chemicals, such as flocculants or coagulants, which simplifies the sedimentation process.
The benefits of employing rapid mixing techniques in such treatment processes are manifold:
- Rapid Reactions: Chemicals that are mixed quickly can react faster, leading to more effective pollutant removal. This helps in achieving regulatory compliance more efficiently.
- Reduced Final Treatment Times: Efficient mixing shortens the overall time a treatment batch requires, leading to increased throughput of wastewater.
- Improved Efficiency: Better mixing yields finer particles or flocs, enhancing the sedimentation characteristics in secondary clarifiers.
The challenges lie mainly in ensuring that energy consumption doesn’t spiral out of control, amidst calls for more sustainable practices.
"Effective management of wastewater is not just about treatment, it's about rejuvenating our shared water resources for future generations."
Role in Air Quality Improvement
Rapid mixing plays a significant role in air quality control as well. The relationship between mixing efficiency and pollutant dispersion is critical for mitigating the impacts of harmful emissions. In the context of industrial operations, rapid mixing systems in scrubbers or catalytic converters can greatly improve air quality.
The specific advantages are:
- Enhanced Gas Treatment: Rapidly mixing gases with absorbent or adsorbent materials maximizes contact, improving removal efficiency of pollutants like sulfur dioxides or nitrogen oxides.
- Prevention of Bad Odors: Through effective mixing, volatile organic compounds and other odorous substances can be neutralized before they escape into the atmosphere, thus improving overall air quality.
- Support for Compliance: Achieving stringent regulatory standards becomes more feasible when systems are designed for optimal mixing performance.
On the flip side, care must be taken to assess the chemical compatibility of materials used, as corrosion can be a factor for long-term applications.
Ultimately, recognizing and harnessing the environmental relevance of rapid mixing methods expands our toolkit for tackling ecological challenges, guiding us toward a cleaner, healthier future.
Innovative Techniques in Rapid Mixing
In the ever-evolving field of science and technology, the continuous pursuit of efficiency leads to significant innovations. Rapid mixing techniques play a vital role in enhancing processes across various domains. Understanding the innovative methods employed in rapid mixing is crucial for industries aiming to maximize yield while minimizing resource consumption. By exploring advanced technologies, we can appreciate how they contribute to better mixing outcomes, ultimately driving advancements in chemical reactions, materials development, and environmental solutions.
Advancements in Turbulence Inducing Devices
One of the cornerstones of rapid mixing lies in turbulence management. Turbulence-inducing devices have come a long way. These tools are designed to disrupt laminar flow and create chaotic, swirling currents within mixtures. This dynamic behavior enhances the interaction between different phases and ingredients, leading to quicker and more uniform blending. The advancement in design and materials of these devices is a game changer.
Benefits of Turbulence Induction:
- Improved Mixing Efficiency: By breaking down layers of fluid that resist blending, turbulence allows materials to mix faster than traditional methods.
- Reduced Processing Times: Quick mixing translates into shorter production cycles. This is critical for sectors like pharmaceuticals, where time could mean the difference between efficacy and obsolescence.
- Cost-Effectiveness: Enhanced efficiency often leads to lower energy consumption, thereby reducing operational costs.
However, it's essential to consider the challenges that come with these advancements. For instance, excessive turbulence may lead to shear-induced degradation of sensitive compounds. Thus, finding a sweet spot for operational parameters is key.
Nanotechnology in Mixing Processes
Nanotechnology, often hailed as the frontier of innovation, brings a novel approach to rapid mixing. At the nanoscale, the behavior of materials can drastically differ from their macro counterparts. Integrating nanotechnology into mixing practices allows for the manipulation and enhancement of properties that significantly affect performance.
What Nanotechnology Brings to the Table:
- Uniform Particle Distribution: By utilizing nanoparticles, blending becomes more precise, reducing the chances of large agglomerates that could disrupt processes.
- Enhanced Reactivity: Nanoparticles often possess higher surface area-to-volume ratios, making them more reactive. This characteristic is especially appealing in catalytic applications where rapid mixing occurs.
- Smarter Processes: Incorporating smart materials can lead to adaptive mixing systems that respond in real time to variations in the mixing environment,
Yet, the infusion of nanotechnology is not without its obstacles. Issues related to the high costs of developing and deploying these techs can hinder their widespread adoption. There's also the matter of safety and regulatory compliance that must be navigated.
"The integration of any new technology must always be balanced against potential repercussions to ensure sustainable and responsible innovation."
In summary, the exploration of turbulence-inducing devices and nanotechnology in rapid mixing techniques opens up exciting possibilities. By staying informed of these advancements, industries can harness the full potential of rapid mixing, transforming their processes for the better.
Measuring Mixing Efficiency
Measuring mixing efficiency is crucial in understanding how well different materials or substances combine in rapid mix processes. It goes beyond just touching the surface; it dives into how effective the mixing really is and the outcomes it generates. A precise evaluation of mixing efficiency can lead researchers and engineers to optimize processes, reduce waste, and improve end products.
Feedback Mechanisms in Mixing Evaluations
Feedback mechanisms are important for evaluating mixing efficiency. Without them, one might imagine that mixing is about simply stirring substances together, but it’s far more complex. These mechanisms allow for real-time assessment of how uniform the mixture is throughout the process. Examples of feedback mechanisms include sensors that can detect changes in properties such as viscosity or temperature, giving immediate data about how well the mixing is going.
- Real-Time Monitoring: Employing tools like ultrasonic sensors can provide immediate feedback on the state of the mix.
- Automated Control: Automated systems can adjust the mixing parameters in real-time based on feedback, making the process more responsive.
- Data Analysis: Gathering data continuously can lead to insightful patterns, helping researchers understand how different factors affect mixing efficiency over time.
Through these feedback systems, you can catch issues before they escalate, catching problems like clumping or ineffective mixing while there’s still time to correct them.
Utilization of Digital Imaging Techniques
Digital imaging has emerged as a game-changer in the realm of mixing evaluations. It provides an intricate view into the mixing process that was previously tough to achieve. By capturing high-resolution images of the mixing in action, researchers can analyze particle distribution and flow dynamics in a non-invasive manner. The application of this technique can be profound, particularly in settings where traditional methods fall short.
- Particle Tracking: With digital imaging, it’s possible to track individual particles. This helps in understanding how materials interact at a microscopic level.
- 3D Reconstruction: Some advanced image processing techniques can create three-dimensional models of the mixing phenomena, providing greater insights into the behavior of different materials during the process.
- Combining Techniques: When combined with other methods like computational fluid dynamics, the accuracy of assessments can significantly improve. This makes it easier to visualize where improvements are needed, whether that's in a lab setting or an industrial application.
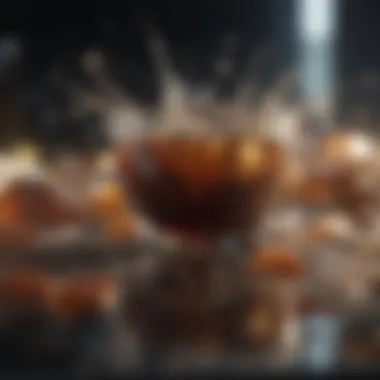
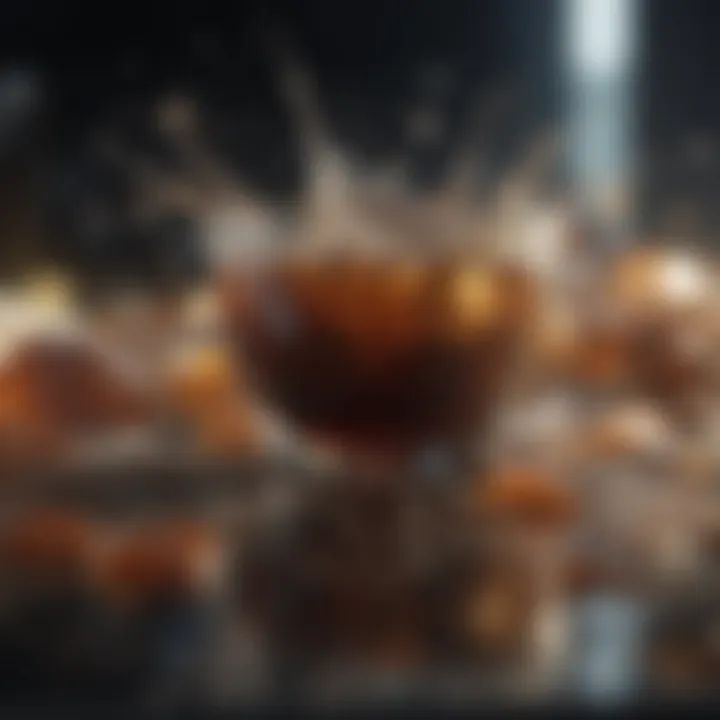
Digital imaging, therefore, not only adds a layer of depth to the understanding of mixing efficiency but also equips researchers and practitioners with tools that can enhance the overall effectiveness of mixing processes.
"The precision required in measuring mixing efficiency fuels not only innovation but also the sustainability of practices across industries, leading to enhanced product quality."
In summary, measuring mixing efficiency through feedback mechanisms and digital imaging plays a vital role in refining the mixing processes. Both approaches offer valuable insights that can optimize material performance, reduce operational costs, and minimize environmental impacts, which is particularly critical in today’s fast-paced scientific and industrial landscapes.
Challenges and Limitations
Understanding the challenges and limitations associated with rapid mixing processes is crucial in both scientific research and industrial applications. These aspects not only affect the efficiency of mixing, but could also have implications on energy consumption, material compatibility, and the overall effectiveness of the end products. Given the increasing emphasis on sustainable practices and efficiency, recognizing these hurdles allows professionals to develop strategies for improved performance and innovation.
Energy Consumption in Rapid Mixing Processes
When diving into the topic of energy consumption in rapid mixing processes, the stakes are high – literally. Energy use can sometimes be staggering, leading to increased operational costs and potential environmental harm. Forging a balance between achieving high mixing efficiency and minimizing energy expenditure is a tightrope walk for engineers and scientists alike.
Consider this: In a typical mixing study, the differences in energy requirements between low and high shear mixing techniques can be substantial. High shear processes often consume a significant chunk of energy yet can yield greater homogeneity in mixed products. Thus, understanding the nuances involves assessing the trade-offs; although a high-energy input could result in better results, it doesn't always translate to better practices or lower emissions.
Some tools and methods can help cut down on energy consumption without sacrificing efficiency. For instance, implementing advanced sensors allows for real-time monitoring and adjustments during the mixing process, ensuring that energy is utilized optimally.
Key points to consider include:
- Optimization Techniques: Adjusting parameters like speed, duration, and the setup of the mixing equipment can lead to considerable energy savings.
- Alternative Mixing Systems: Exploring newer methods, such as ultrasonic or membrane filter mixers, may provide lower energy consumption without compromising the mixing quality.
- Feedback Mechanisms: Incorporating machine learning technologies could predict and optimize energy needs based on specific material properties or process requirements.
Material Compatibility Issues
Now, shifting our focus towards material compatibility issues, this aspect tends to be the unsung hero of successful rapid mixing. When different substances are combined, it is vital to ensure that they won't react adversely or lead to unstable mixtures.
Consider a scenario: mixing certain polymers with solvents might lead to phase separation or degradation of the material, undermining the purpose of mixing in the first place. A deep understanding of the chemical properties and behaviors of the materials being mixed is imperative for achieving desired outcomes.
Some critical aspects include:
- Chemical Interaction: It is essential to know how different substances interact, as incompatibility can lead to byproducts that may affect the final product's quality.
- Physical Properties: Variations in viscosity, particle size, and density among materials can lead to uneven mixing, ultimately affecting performance.
- Testing Protocols: Implementing robust testing frameworks during the development phase can minimize compatibility issues. Pilot studies can assess how materials behave under various conditions.
Future Perspectives
The field of rapid mixing is set on a path that promises significant advancements and transformative applications across a variety of sectors. As we delve into the importance of exploring the future perspectives within this domain, it becomes clear that embracing innovative trends and technologies will be essential for improving efficiencies and outcomes in mixing processes.
Trends in Rapid Mixing Research
Research in rapid mixing is broadening its horizons, incorporating an array of developments designed to enhance the understanding and application of mixing techniques. One prominent trend is the growing involvement of computational fluid dynamics (CFD) in the modeling and simulation of mixing processes. This approach allows researchers to visualize complex fluid behaviors and understand how different variables influence mixing efficiency. The ability to predict outcomes based on simulations can lead to more precise and cost-effective mixing designs in real-world applications.
Moreover, scientists are increasingly focusing on micro-scale mixing. This is particularly relevant in fields such as pharmaceuticals, where effective mixing at a micro-level can greatly influence drug efficacy. As researchers explore nanotechnology applications, the integration of advanced materials and additives holds promise for enhancing mixing performance and efficiency.
Additionally, emphasis on sustainable practices is driving innovation in mixing research. Various studies explore ways to minimize energy consumption while maximizing mixing effectiveness. Utilizing renewable energy sources or developing energy-efficient mixers is gaining traction and shaping future research initiatives.
In summary, trends in rapid mixing research reflect a blend of innovative technologies and environmental considerations. As these trends evolve, they pave the way for a more nuanced understanding of mixing processes and usher in changes that could redefine various industries.
Integration with Automation Technologies
The integration of automation technologies into rapid mixing processes is another key element poised to shape the future of this field. As industries drive toward greater efficiency and precision, automation is becoming a game-changer in how mixing systems operate.
One significant benefit of automation is the real-time monitoring and control of mixing parameters. For example, employing smart sensors can track variables such as viscosity, temperature, and pH levels, providing immediate feedback that allows for dynamic adjustments. This capability enables a level of consistency that manual processes simply can not achieve.
Moreover, the advent of machine learning in mixing technology offers the potential to analyze vast datasets to optimize mixing strategies. By training algorithms on historical mixing data, systems can adapt protocols, reducing trial-and-error phases and enhancing outcome predictability.
As industries continue to embrace automation, collaborative robots, or cobots, are finding their way into mixing setups. These robots can assist human operators, performing repetitive tasks and showcasing high agility and flexibility in workspaces where mixing occurs. Cobots not only alleviate manual labor but can also significantly reduce the risk of errors in the mixing process—ultimately leading to improved product quality.
Incorporating automation technologies into rapid mixing isn’t just a matter of convenience. It's about staying competitive and responsive in an ever-evolving market landscape. As this integration grows, we’ll likely witness a transformative shift in how mixing processes are designed, executed, and evaluated, allowing industries to capitalize on efficiencies and drive innovation further.
Closure
The conclusion of this article highlights the critical importance of rapid mixing in various scientific and industrial realms. Throughout the exploration, we’ve learned that rapid mixing is not just a technical maneuver; it serves as a backbone for multiple processes that directly impact efficiency and quality in diverse applications such as chemical reactions, material properties, and environmental management. The discussions have outlined significant correlations between effective mixing and successful outcomes in numerous experiments and operations, elucidating why understanding rapid mixing is of paramount importance.
Summarizing the Importance of Rapid Mixing
To encapsulate the essence of rapid mixing, we can break down several core aspects:
- Efficiency: Rapid mixing enhances the rate at which components interact, ultimately leading to quicker reaction times and better yield in chemical processes.
- Uniformity: Achieving a homogenous mixture is essential in applications ranging from pharmaceuticals to food production, where consistency cannot be compromised.
- Cost-effectiveness: By improving operational efficiency, rapid mixing can reduce waste and lower production costs, making it economically beneficial for businesses.
- Quality: The performance of products significantly relies on mixing quality. Inconsistent mixtures can lead to defects or failures in end products.
Emphasizing these points demonstrates that irrespective of the field, be it engineering, environmental science, or material science, rapid mixing plays a pivotal role in shaping outcomes. It's clear that as industries increasingly adopt more complex processes, ensuring effective mixing remains a priority for ongoing success.
Call for Continued Research and Innovation
The journey does not end here. As we've seen, while significant advancements have been made in understanding rapid mixing, there still lies an ocean of opportunities for further exploration and innovation. Here are several considerations for future research:
- Emerging Technologies: Research can focus on how innovations like artificial intelligence and machine learning can further optimize mixing processes.
- Sustainable Practices: Investigating energy-efficient mixing systems that enhance environmental sustainability could be pivotal, especially in today's context where environmental concerns are at the forefront.
- Microscale Mixing: Studies into more intricate mixing at smaller scales, such as in microfluidics, could lead to breakthroughs in areas like biomedical applications or personalized medicine.
- Collaborative Research: Interdisciplinary collaboration will forge new paths in understanding the dynamics of mixing better, leading to holistic approaches in tackling real-world problems.
"In every challenge lies an opportunity for betterment; ongoing research is the key to unlocking the full potential of rapid mixing."
As we move forward, it is imperative that students, researchers, and professionals remain engaged in this vital area of study. The stakes are high, and the future of many applications could hinge on our understanding and optimization of rapid mixing.