Understanding Titanium Corrosion: Mechanisms and Advances
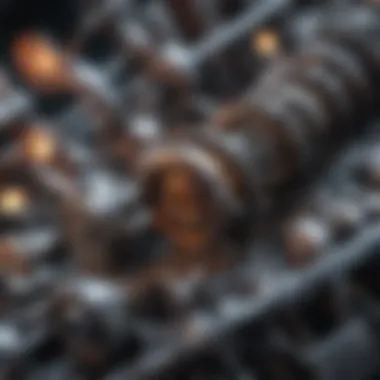
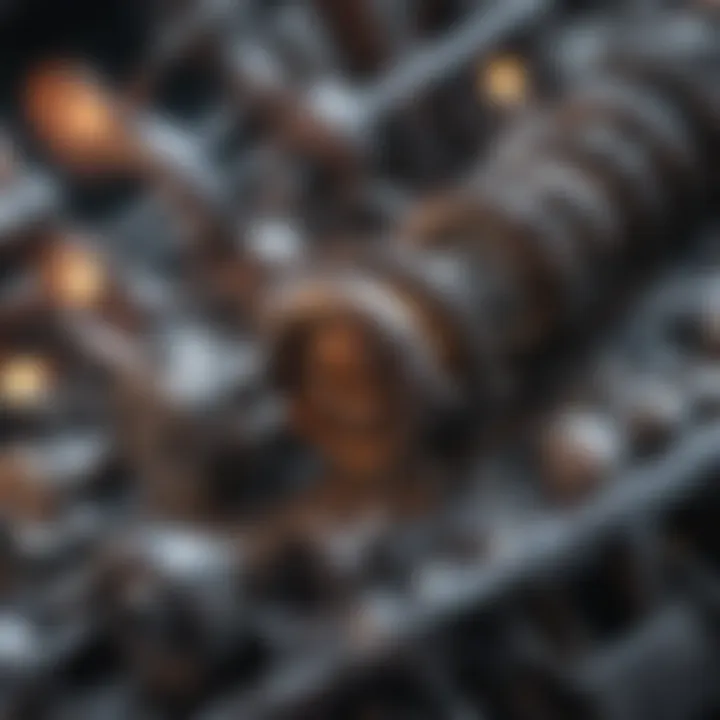
Intro
Corrosion of titanium is a complex subject that affects many fields. Titanium is known for its strength and low density, making it important in aerospace, medical, and chemical industries. However, its susceptibility to corrosion is a significant concern. Understanding how and why titanium corrodes is crucial for those working with this material.
This article aims to give an overview of the factors influencing titanium corrosion, including environmental conditions and mechanical stress. We will also look into the specific mechanisms that cause degradation and find solutions to these challenges.
In this exploration, both theoretical insights and practical implications will be considered. Ultimately, the aim is to deepen the understanding of a material that plays a vital role in modern technology and engineering.
Intro to Titanium Corrosion
The corrosion of titanium is a subject of paramount importance in various industrial and research contexts. Understanding titanium corrosion is essential for those working with this metal, which is known for its unique properties such as high strength-to-weight ratio, exceptional corrosion resistance, and biocompatibility. This article aims to provide an extensive examination of the mechanisms contributing to corrosion, the challenges faced in different environments, and innovations geared toward mitigating these issues. Knowledge of titanium corrosion informs material selection, application strategies, and overall safety in industries where titanium is prevalent.
The Importance of Titanium in Modern Applications
Titanium plays a critical role in multiple sectors, including aerospace, automotive, medical devices, and marine engineering. In aerospace, titanium alloys are crucial due to their lightweight nature and ability to withstand extreme temperatures, which enhances fuel efficiency and performance.
In the medical field, titanium is commonly used in implants because of its compatibility with human tissues, reducing the risk of rejection. Additionally, the automotive industry seeks titanium to produce lighter vehicles and improve energy efficiency. Its resistance to corrosion in environments prone to harsh conditions, such as salty or acidic atmospheres, makes titanium a strategic choice for marine engineering.
Overall, the demand for titanium across these sectors continuously grows, driving research into its corrosion properties and mitigation strategies.
Defining Corrosion in Metallurgical Terms
Corrosion, in metallurgical terms, refers to the degradation of a material due to its interaction with its environment. This process often leads to the deterioration of mechanical properties and overall performance. For metals like titanium, corrosion occurs primarily through electrochemical reactions where metal ions are released into the surrounding environment.
Key types of corrosion relevant to titanium include uniform corrosion, where the metal thins uniformly, and localized forms like pitting and stress corrosion cracking, which can be particularly detrimental in critical applications. Recognizing these corrosion types helps engineers and researchers identify appropriate safeguards and design considerations while working with titanium.
In summary, understanding the corrosion mechanisms of titanium is vital not only for enhancing its longevity and integrity but also for ensuring the safety and efficiency of applications utilizing this versatile metal.
Fundamental Properties of Titanium
The fundamental properties of titanium play a crucial role in its application across various industries, particularly in areas where strength, lightweight, and corrosion resistance are prioritized. Understanding these properties is essential in the context of corrosion because they directly influence the material's performance and longevity in challenging environments. Titanium offers a unique balance of physical and chemical qualities that make it distinctive among metals and entirely indispensable in modern engineering and technology.
Physical and Chemical Characteristics
Titanium is known for its remarkable strength-to-weight ratio. It is both lighter than steel and denser than aluminum. This allows for significant weight savings in applications where low mass is critical. Another notable property is its high tensile strength, which is about twice that of aluminum but still considerably lighter.
In terms of chemical characteristics, titanium exhibits excellent corrosion resistance due to the formation of a stable oxide layer on its surface when exposed to oxygen. This layer protects the titanium substrate from a range of corrosive agents. In particular, it resists oxidation, which is vital in high-temperature settings.
The melting point of titanium exceeds 1,660°C, making it suitable for applications involving high heat. Additionally, it has a relatively low thermal conductivity, contributing to its thermal stability in extreme conditions. These properties underscore titanium's versatility in aerospace, biomedical, and marine applications, where it routinely faces exposure to harsh environments.
Comparison with Other Metals
When comparing titanium to other common metals like steel and aluminum, its advantages become clear. Unlike steel, titanium does not rust and maintains its strength at high temperatures. While aluminum is lighter, it lacks the strength that titanium provides under stress. This makes titanium a more favorable option for applications where performance under pressure is necessary.
However, titanium does have its challenges. It is more expensive than both aluminum and steel. Additionally, it is more difficult to machine, requiring specialized tools and processes. Therefore, while titanium offers superior properties, the economic and practical considerations can sometimes limit its usage.
Titanium's unique properties position it as a critical material in industries where performance is non-negotiable.
In summary, the fundamental properties of titanium are a significant factor in understanding its behavior against corrosion. Its physical advantages and chemical resilience make it a highly sought-after material, despite its potential drawbacks in cost and machinability. As research continues, new innovations may further enhance its applicability in demanding fields.
Mechanisms of Corrosion in Titanium
Corrosion mechanisms in titanium are vital to understanding how this metal behaves under various environmental conditions. Titanium offers a unique blend of strength, lightness, and resistance to corrosion, yet it is not immune to degradation. Investigating its corrosion mechanisms is crucial for the development of strategies to enhance its longevity in demanding applications. Factors such as chemical composition, exposure environments, and manufacturing methods play significant roles in corrosion behavior. Understanding these mechanisms allows researchers and engineers to make informed decisions about titanium’s use and maintenance in critical sectors like aerospace, medical implants, and marine engineering.
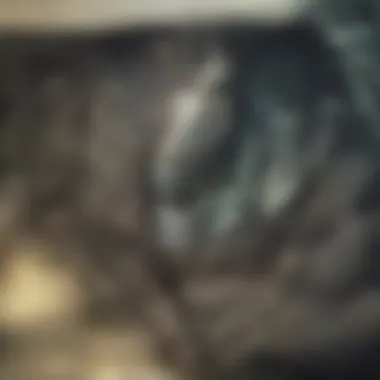
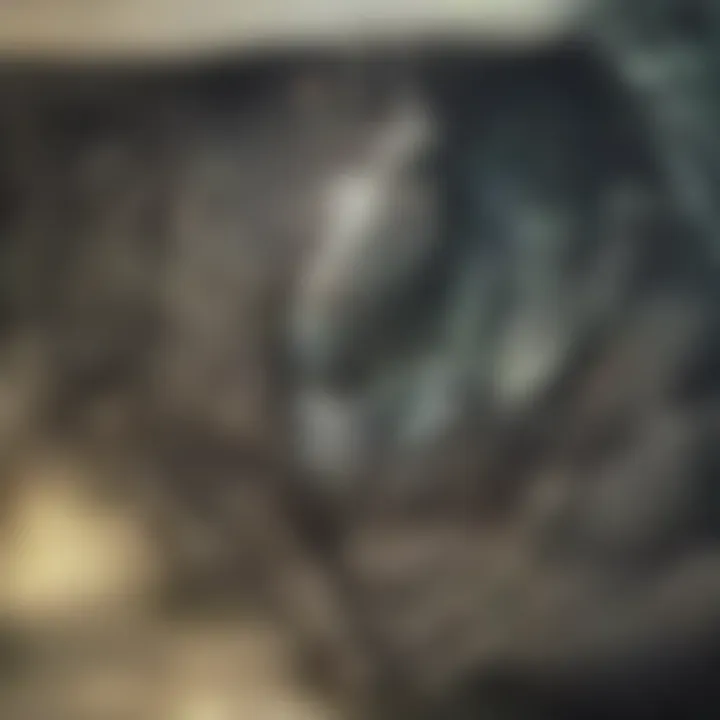
Electrochemical Corrosion Processes
Electrochemical corrosion in titanium typically occurs when titanium is exposed to electrolytes. It involves an anode and cathode where oxidation and reduction reactions take place. In simpler terms, this is where the titanium loses electrons and eventually corroding the material. The process can be influenced by several variables:
- Conductivity of the electrolyte: A higher conductivity increases the rate of corrosion as it allows the flow of electrical current between anode and cathode more effectively.
- pH levels: Acidic environments significantly increase the likelihood of corrosion. In contrast, basic conditions can sometimes help in reducing rates of corrosion.
- Temperature: As temperature increases, so does the rate of corrosion because of enhanced kinetic energy of the reacting particles.
Pitting Corrosion Phenomena
Pitting corrosion is a localized form of corrosion, often serious despite the material's overall good condition. This type of corrosion results in small holes or pits in the metal, which can compromise structural integrity. Factors that contribute to pitting include:
- Chloride ions: Highly corrosive and capable of penetrating the protective oxide layer of titanium, leading to small, localized anodes.
- Oxygen concentration: Variations in oxygen levels can lead to differential aeration cells, enhancing pitting susceptibility.
- Surface finish: Rough surfaces can trap corrosive agents, thereby increasing the risk of pitting.
It is essential for engineers to monitor environments where titanium is used to mitigate risks associated with pitting corrosion, especially in chloride-rich environments like seawater.
Stress Corrosion Cracking
Stress corrosion cracking (SCC) occurs when tensile stress interacts with a corrosive environment, leading to sudden and unexpected failure. This phenomenon is critical for titanium, particularly in high-stress applications. Key considerations include:
- Stress state: Residual or applied stresses can make titanium more susceptible to SCC.
- Environmental factors: Exposure to specific environments, such as saltwater or acidic solutions, heightens the risk of SCC.
- Metal microstructure: Altered microstructures within titanium alloys can influence susceptibility to cracking. It is important for engineers to account for these aspects during design and material selection.
To mitigate the risks associated with SCC, proper handling and preventive measures must be employed throughout the lifecycle of titanium components. Understanding these mechanisms forms a fundamental basis for improving titanium’s performance in various applications.
Influence of Environmental Factors
The interaction of titanium with its environment plays a significant role in determining its corrosion behavior. Understanding these factors is crucial for predicting durability and performance. In this section, we will explore three key environmental elements: temperature, moisture, and chemical exposure. Each of these factors influences corrosion rates differently, and being aware of them allows for better material selection and management.
Impact of Temperature on Corrosion Rates
Temperature has a direct effect on the kinetics of electrochemical reactions. As the temperature increases, the rate of corrosion reactions generally rises, leading to faster degradation of titanium. This increase in activity can be attributed to enhanced ion mobility and greater energy within the chemical bonds of surrounding molecules.
A few important points about temperature and titanium corrosion include:
- Critical Thresholds: The temperature increases can lead to critical thresholds beyond which the accelerated corrosion may compromise component integrity.
- Thermal Cycling: In applications exposed to fluctuating temperatures, the thermal cycling can cause physical stresses, further promoting corrosion.
Research has shown that titanium in high-temperature environments may undergo phase changes, altering its protective oxide layer. Therefore, engineering designs must consider these thermal impacts carefully to mitigate risks associated with elevated temperatures.
Role of Moisture and Humidity
Moisture and humidity are significant factors influencing the corrosion of titanium. Water acts as a medium for electrochemical reactions, and the presence of moisture can significantly increase corrosion rates.
Some considerations regarding moisture and corrosion include:
- Electrolyte Formation: High moisture levels can form electrolytic solutions that facilitate corrosion processes.
- Localized Corrosion: Areas with stagnant moisture may allow for localized attack, leading to pitting or crevice corrosion.
Understanding the environment where titanium components are deployed helps in developing effective protective measures against moisture-induced degradation. Monitoring humidity levels can be an essential part of corrosion management strategies in critical applications.
Chemical Exposure: Salts and Acids
The presence of aggressive chemicals like salts and acids in the environment poses challenges for titanium's corrosion resistance. These substances can actively break down the protective oxide layer that titanium forms, leading to accelerated wear.
Key points to consider regarding chemical exposure are:
- Salinity Effects: Salts, especially in marine environments, can create chlorides that significantly increase localized corrosion rates.
- Acidic Conditions: Acids can directly attack titanium, leading to rapid material loss and structural failures.
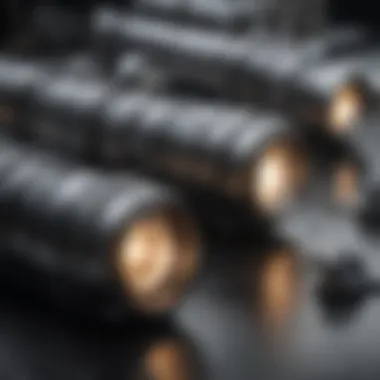
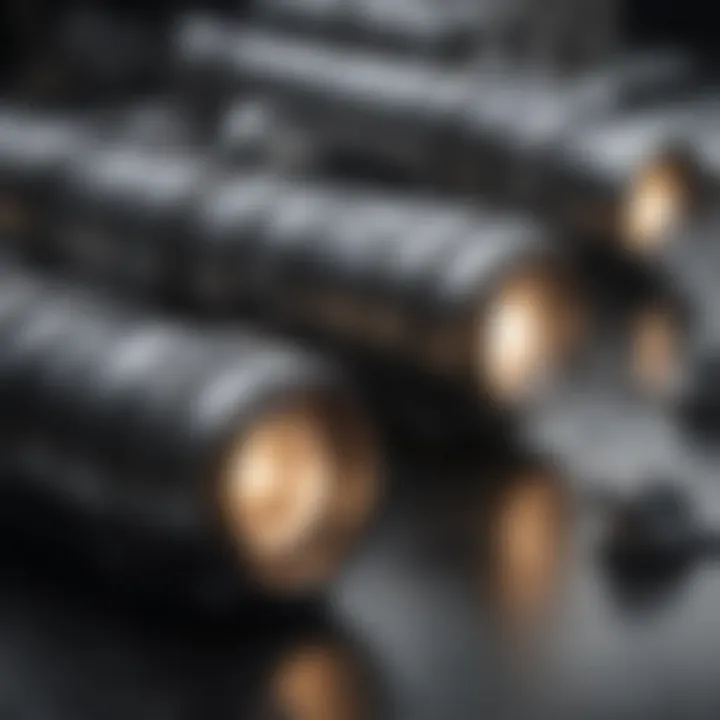
Predicting the impact of chemical exposure is essential in applications such as marine engineering and chemical processing. Knowledge of the specific environment will aid in the selection of appropriate protective measures and enhance the long-term reliability of titanium components.
In summary, environmental factors such as temperature, moisture, and chemical exposure influence titanium corrosion in significant ways. Understanding these interactions allows for informed decisions in material selection and protective strategies.
Case Studies of Titanium Corrosion
Understanding the corrosion of titanium through real-life applications provides critical insights into its behavior in various environments. Case studies enable analysis of corrosion mechanisms, effectiveness of mitigation strategies, and influence on material selection. This helps to demonstrate the practical implications of titanium's unique properties in diverse sectors such as aerospace, medical, and marine engineering. By studying specific instances, professionals can derive lessons that inform future practices and innovations.
Aerospace Applications
In aerospace engineering, titanium is widely used for its strength-to-weight ratio and excellent corrosion resistance. However, several notable cases highlight challenges related to titanium corrosion in this industry. For instance, aircraft components often experience environmental stressors that can induce localized corrosion.
A key case involved a titanium alloy used in a military aircraft where pitting corrosion was observed. This degradation prompted a review of maintenance procedures and material selection for critical components.
Engineers had to adapt their strategies, enhancing inspection processes and employing protective coatings to combat corrosion. The importance of this case underscores the need for ongoing evaluation of materials used in flight-critical applications.
Medical Implants
Medical implants made from titanium are renowned for their biocompatibility and resistance to body fluids. However, certain implant cases have shown unexpected corrosion, especially in specific environments like places with high chloride concentration.
For instance, studies of dental implants frequently reveal that improper sterilization techniques and poor oral hygiene can lead to localized corrosion. This can affect the implant's longevity and necessitate revision surgeries. Evaluating these cases has spurred advancements in surface treatments and engineering designs aimed at improving corrosion resistance in implants.
Marine Engineering Contexts
Marine engineering presents another significant arena for observing titanium corrosion behaviors. The maritime environment, characterized by its high salinity and moisture levels, poses severe corrosion threats. A notable case involved the use of titanium in the construction of submarines and offshore structures.
In these contexts, extensive exposure to seawater can lead to aggressive corrosion phenomena, including stress corrosion cracking. As a response to these cases, engineers have developed tailored titanium alloys designed to withstand the specific corrosive agents found in marine environments. The case studies have reinforced the understanding of material limits and the necessity for continual innovation in alloy development.
In summary, case studies in various fields reveal the complexities of titanium corrosion and the critical need for preventive measures tailored to specific conditions. These scenarios not only highlight existing challenges but also pave the way for smarter design and material choices going forward.
Mitigation Techniques for Corrosion Prevention
The mitigation of corrosion is essential for enhancing the longevity and reliability of titanium in various applications. This section will explore several crucial strategies aimed at preventing or delaying the corrosion processes that can compromise the structural integrity of titanium alloys. Adopting effective mitigation techniques not only prolongs the lifespan of titanium components but also reduces maintenance costs, thus presenting a compelling case for their implementation in engineering and manufacturing sectors.
Protective Coatings
One of the primary methods for corrosion prevention is the application of protective coatings. These coatings act as barriers between the titanium surface and corrosive environments. Common materials for coatings include polymers, epoxies, and metallic layers such as zinc or aluminum. The choice of coating material depends on the specific environment the titanium will face.
- Key benefits of protective coatings:
- Enhanced Durability: Coatings can significantly increase the resistance of titanium against environmental stressors, including salts and acids.
- Aesthetic Improvement: Besides functionality, coatings can improve the appearance of titanium products, making them more attractive in consumer markets.
- Customization: Different coatings can be tailored for specific applications, such as aerospace, marine, or medical uses.
However, it is imperative to consider adhesion properties between the coating and titanium to ensure effectiveness. Proper surface preparation before applying coatings is a critical step that impacts long-term performance.
Material Selection Strategies
Another important aspect of corrosion mitigation is the strategic selection of materials that can withstand hostile environments. Various titanium alloys exhibit different corrosion resistances based on their compositions and microstructures.
- Considerations for material selection:
- Alloy Composition: Alloys containing aluminum or vanadium generally offer better performance in certain corrosive environments compared to pure titanium.
- Resilience to Specific Corrosive Agents: Certain titanium alloys are better suited for specific conditions, such as high salinity in marine applications or acidic environments in chemical processing.
- Availability and Cost: While high-performance alloys may offer superior resistance, cost-effectiveness and supply chain availability must also be taken into account.
By choosing the right alloy, engineers can significantly reduce the risk of corrosion-related failures, thereby enhancing the overall safety and reliability of titanium applications.
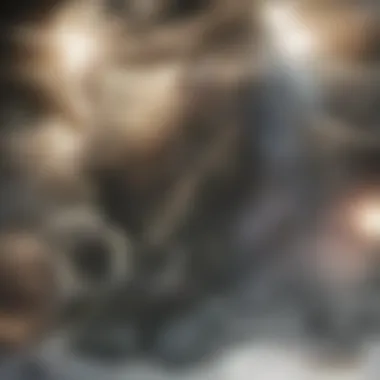
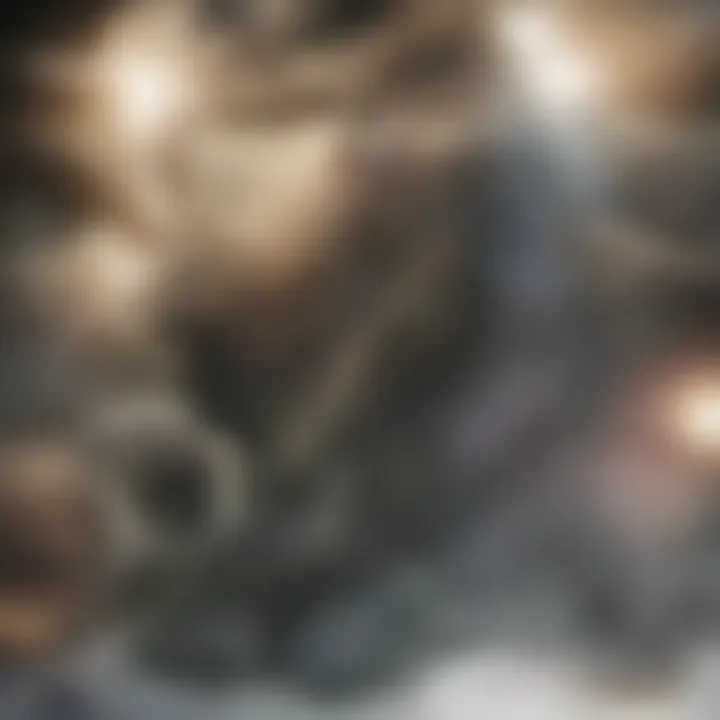
Corrosion Inhibitors and Additives
The use of corrosion inhibitors is another effective strategy for reducing the rate of corrosion. These chemical substances can be added to environments where titanium is present, to minimize the electrochemical reactions that lead to corrosion.
- Examples of corrosion inhibitors:
- Chromates: Traditionally used, chromates provide effective protection but are now facing regulatory pressures due to environmental concerns.
- Nitrites and Molybdates: These offer alternative mechanisms of protection, particularly in industrial cooling systems.
- Organic Inhibitors: Recent advancements have shown promise with organic compounds that can inhibit corrosion when applied to titanium in various environments.
While these inhibitors can offer significant benefits, their effectiveness can depend on concentration, type of environment, and presence of other species in the system. Therefore, continuous monitoring and adjustments may be necessary to ensure optimal performance.
Engaging in corrosion prevention through tailored techniques is not only a practical approach but also a necessity in industries where titanium plays a crucial role.
Innovative Research on Titanium Corrosion
Research on titanium corrosion is essential for improving the longevity and performance of titanium alloys in various applications. By understanding the specifics of corrosion mechanisms and exploring innovative approaches to mitigate them, researchers can significantly enhance the usability of titanium in sectors like aerospace, medical implants, and marine engineering. This section delves into recent developments, highlighting key aspects that may shape future studies and practices.
Recent Advances in Material Science
In recent years, material science has seen substantial progress regarding titanium alloys and their corrosion resistance. Researchers focus on modulating the microstructure of titanium through alloying elements and processing techniques. By using elements such as aluminum and vanadium, the corrosion resistance of titanium can improve under specific environmental conditions.
Furthermore, advanced techniques like additive manufacturing enable the production of complex shapes and geometries. This flexibility in design leads to more efficient use of titanium while potentially lowering corrosion rates.
Another significant advancement is surface engineering, which includes techniques like plasma nitriding and surface texturing. These methods improve the effectiveness of protective oxide layers, enhancing resistance to localized corrosion phenomena such as pitting and crevice corrosion. The following are some recent advancements:
- Enhanced alloy compositions that improve resistance to aggressive environments.
- Development of efficient surface treatments to optimize protective features.
- Utilization of advanced manufacturing processes to create near-net-shape components reducing waste and improving performance.
Nanotechnology Applications
Nanotechnology offers a promising frontier for enhancing the corrosion resistance of titanium alloys. Incorporating nanomaterials, such as graphene or carbon nanotubes, can improve excellent mechanical properties and provide superior barrier effects against corrosive agents. By creating nanostructured coatings, researchers have achieved significant improvements in corrosion protection.
Nanotechnology also allows for a better understanding of surface interactions at the atomic level. Molecular simulations and modeling help predict how specific nanostructures behave in corrosive environments. Researchers have made strides in developing self-healing coatings that utilize nanotechnology to repair damaged surfaces automatically. These innovative strategies foster long-term durability in titanium components, which is crucial in demanding applications.
Sustainable Practices in Corrosion Management
As industries move towards more sustainable practices, managing titanium corrosion also adapts to these ideals. Researchers are now exploring environmentally friendly corrosion inhibitors derived from natural sources. These biodegradable options lower environmental impact, contrasting with traditional synthetic inhibitors.
Another sustainable approach is recycling. Implementing effective recycling programs for titanium can reduce material usage and subsequently decrease the overall environmental footprint. Studies indicate that recycling can recover up to 90% of titanium alloys effectively, presenting an opportunity to manage corrosion challenges through resource efficiency.
Moreover, sustainable practices extend to manufacturing processes and methodologies. By implementing green chemistry principles, industries can minimize harmful emissions and reduce chemical waste associated with surface treatments and protective coatings. The following practices promote sustainability in corrosion management:
- Research into biodegradable corrosion inhibitors.
- Commitment to recycling titanium alloys post-use.
- Adoption of green chemistry in surface treatment and coating processes.
Understanding and applying innovative research in titanium corrosion not only fosters material longevity but also aligns with global sustainability goals.
The End and Future Directions
The study of titanium corrosion has become increasingly vital in various fields, including aerospace, medicine, and marine engineering. Understanding the corrosion mechanisms specific to titanium helps engineers and researchers tackle some of the toughest challenges that arise with material degradation in complex environments. The conclusions drawn from current research reveal critical insights into factors that influence corrosion rates and the strategies necessary for prevention. These findings pave the way for innovations that enhance the longevity and performance of titanium alloys.
Summary of Key Findings
- Corrosion Mechanisms: The main processes of titanium corrosion include electrochemical reactions, pitting corrosion, and stress corrosion cracking. Recognizing these mechanisms allows for better assessment of material behavior in specific environments.
- Environmental Influences: Factors such as temperature, moisture, and exposure to corrosive chemicals deeply affect corrosion rates. Engineers must consider these elements when designing components that utilize titanium.
- Case Studies: Reviewing real-world applications in aerospace, medical implants, and marine contexts illustrates the diverse challenges posed by corrosion. These case studies highlight the need for tailored solutions in different sectors.
- Mitigation Techniques: Innovations in protective coatings, strategic material selection, and use of corrosion inhibitors have shown promise in extending the life of titanium components.
- Research Directions: Recent advancements in nanotechnology and sustainable practices suggest future pathways for corrosion management in titanium applications. Continuous research is essential to keep pace with emerging technologies and environmental challenges.
Implications for Future Research and Industry
The implications of these findings are significant for both academic research and industrial practices. Future investigations should focus on the following areas:
- Material Development: There is a need for the creation of new titanium alloys that are more resistant to corrosion without compromising their mechanical properties.
- Corrosion Testing: Standardized testing methods must be refined to better simulate real-life conditions that titanium components may face. This can lead to improved predictive models for corrosion behavior.
- Cross-Disciplinary Approaches: Collaboration between material scientists, engineers, and environmental experts can foster a more comprehensive understanding of how titanium interacts with different corrosive environments.
- Regulatory Considerations: As industries increasingly adopt titanium alloys, regulations surrounding sustainable use and corrosion management will become more important. Policymakers must work with researchers to develop guidelines that promote safety and environmental stewardship.
"Ongoing research not only addresses current challenges but also anticipates future needs in material application, ensuring that titanium remains a cornerstone in engineering applications."
As we look to the future, the commitment to furthering our understanding of titanium corrosion is crucial. Whether for enhancing existing applications or developing new technologies, this field will continue to evolve, seeking solutions that marry durability with sustainability.