Wafer to Wafer Bonding: Techniques and Applications
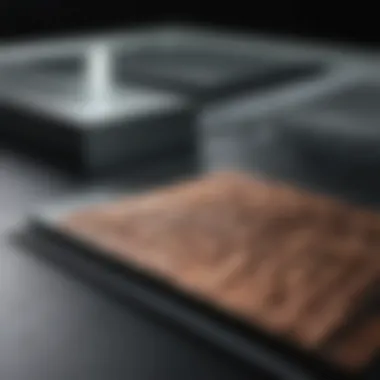
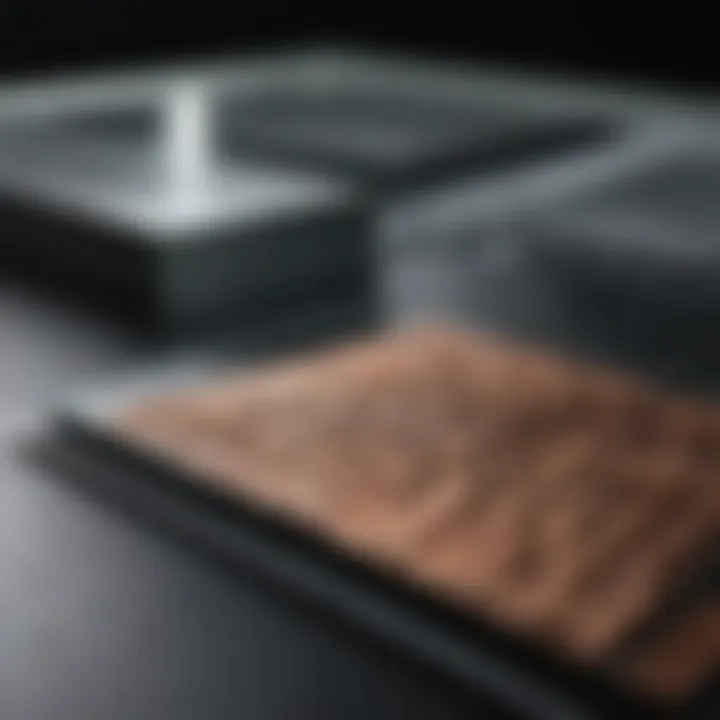
Intro
Wafer to wafer bonding is an essential technique in the field of semiconductor manufacturing. As microelectronics continue to evolve, understanding the methods and implications of this process becomes increasingly critical. This section sets the stage by outlining the process and its importance in modern technology.
The concept of wafer bonding involves joining two silicon wafers together under controlled conditions to create a single, integrated unit. The necessity for this technique arises from the demand for smaller, thinner, and more powerful electronic devices. Given the miniaturization trend in technology, the ability to combine multiple functions onto a single chip is paramount.
As advancements in technology happen, various techniques for wafer bonding have emerged. These methods cater to different requirements such as thermal conductivity, electrical isolation, and mechanical stability. The goal of this article is to provide a detailed exploration of these techniques, their applications, and the challenges faced in the industry today.
The audience for this article includes students, researchers, educators, and professionals. Readers will gain insights into the state-of-the-art practices and future prospects of wafer bonding.
In summary, the subsequent sections will delve into findings, methodologies, various practices, and an outlook on future developments in wafer bonding.
Prolusion to Wafer to Wafer Bonding
Wafer to wafer bonding represents a foundational process in the realm of semiconductor manufacturing. The capacity to bond multiple wafers is essential for the creation of complex three-dimensional structures, making this technique critical for advancing microelectronics. In this section, we will explore its significance, delve into its definition, and review its historical context.
Definition and Significance
Wafer to wafer bonding refers to the process of joining two or more semiconductor wafers together to create a single functioning device. This technique enhances the functionality and performance of electronic devices by integrating multiple materials and structures at a microscopic level. It serves as a bridge between traditional two-dimensional (2D) designs and emerging three-dimensional (3D) architectures, enabling improved electrical performance, reduced power consumption, and increased device density.
The significance of wafer bonding cannot be overstated, as it affects everything from manufacturing efficiency to the performance of end products. Without effective bonding, it would be nearly impossible to achieve the highly sophisticated circuits used in modern electronics. Additionally, understanding the various techniques and applications of wafer bonding informs the ongoing development of innovative devices in microelectronics.
Historical Background
The history of wafer to wafer bonding dates back several decades. Initially, researchers focused on simple methods of bonding wafers, primarily using thermal and adhesive techniques. In the late 20th century, advancements in materials science and engineering led to enhanced methods that increased the strength and reliability of these bonds.
Technological progress during the 1990s, particularly in device miniaturization, prompted a surge in interest and research in wafer bonding techniques. Notable successes were seen with the introduction of direct bonding methods, which eliminated the need for adhesives and improved the interface between wafers. This period laid the groundwork for the sophisticated bonding techniques employed today, such as plasma activation and novel materials for improved adhesion.
As the semiconductor industry continues to evolve, so does the historical narrative of wafer to wafer bonding. Ongoing innovations and research will only further cement its relevance in shaping the future of technology, particularly as we advance toward more complex systems and applications.
"Understanding the historical context of wafer bonding is crucial for grasping the current trends. Each innovation builds upon the successes and failures of the past, creating a roadmap for future exploration."
In summary, wafer to wafer bonding is not merely a technique; it is a critical component in the framework of modern semiconductor manufacturing. Its definition highlights its importance in device performance, while its historical background showcases the evolution that has led to today's sophisticated methods.
Overview of Wafer Bonding Techniques
Wafer bonding techniques play a crucial role in the semiconductor manufacturing industry. This overview will delve into the significance of these methods and their impact on various applications. Understanding wafer bonding techniques is essential for researchers, engineers, and industry professionals as they facilitate the construction of complex multi-layered devices.
These techniques enable the integration of different materials and functionalities, which is necessary for modern microelectronics. Each method has its unique advantages and challenges, making it vital to choose the appropriate technique based on desired outcomes, material compatibility, and production efficiency. Advancements in technology continue to drive innovation in these techniques, shaping the future of semiconductor fabrication.
Direct Bonding
Direct bonding, often referred to as fusion bonding, is one of the most straightforward methods of wafer bonding. This process involves bringing two wafers into contact under controlled conditions, promoting atomic-level interactions between the surfaces. The lack of intermediate layers ensures minimal contamination and excellent adhesion.
In this technique, the surfaces must be extremely flat and clean. Direct bonding is typically applied in silicon-on-insulator technologies and other applications where high-quality interfaces are paramount. Its effectiveness lies in the ability to achieve high bond strength without compromising the electrical or thermal properties of the materials involved.
Adhesive Bonding
Adhesive bonding utilizes polymeric materials or adhesives to bond two wafers. This method is more flexible than direct bonding, as it accommodates surface imperfections and does not require the same level of cleanliness. Adhesive bonding is particularly advantageous for dissimilar materials, where thermal compatibility may be an issue.
Different adhesive formulations are available, each suited for specific applications. The choice of adhesive can affect thermal, electrical, and mechanical properties. This technique is broadly used in micro-electromechanical systems (MEMS) and packaging applications, especially when the integrated circuits need protection against environmental factors.
Thermal Bonding
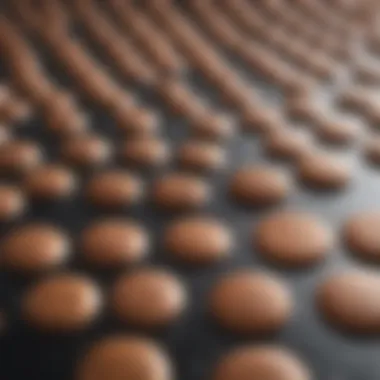

Thermal bonding combines heat and pressure to join two wafers. This technique takes advantage of the viscous nature of certain materials at elevated temperatures, allowing for the creation of strong interconnections. In thermal bonding, careful control of temperature and pressure is essential to ensure a reliable bond and to prevent deformation of the wafers.
This method is particularly effective for materials with similar thermal expansion coefficients, which helps to reduce stress on the bonded interface. Thermal bonding finds applications in the production of advanced semiconductor devices, where maintaining structural integrity during thermal cycling is crucial.
Plasma Activation
Plasma activation involves the use of plasma to clean and activate wafer surfaces prior to bonding. This technique is beneficial for enhancing interfacial bonding, as plasma treatment removes contaminants and modifications occur at the atomic level. Plasma engineering can significantly improve bonding strength, making it suitable for various applications.
The types of plasma used can vary, and the choice depends on the materials being bonded. For instance, oxygen plasma is often effective in activating silicon surfaces, while other gas mixtures may be required for different materials. Plasma activation enhances surface properties, increasing wettability and promoting chemical bonding, which is essential for high-performance devices.
Principles of Wafer Bonding
Understanding the principles of wafer bonding is critical to grasping how this process influences semiconductor manufacturing. This section examines the core physical and chemical aspects of bonding, each of which dictates the effectiveness and reliability of wafer connections. Insights into these principles not only offer a foundation for developing robust technologies but also assist researchers in troubleshooting various bonding challenges.
Physical Principles
The physical principles of wafer bonding revolve around the interactions between surfaces at a microscopic level. These interactions play a crucial role in the formation of tight, defect-free bonds between two wafers. Typically, this involves the alignment of atomic structures, where close contact is essential for initiating bonding at the atomic level.
When two wafers come into proximity, Van der Waals forces and other surface forces become significant. These forces compel atoms from one wafer to interact with those on the other, which can strengthen the connection. The physical attributes of wafer surfaces, such as flatness, cleanliness, and roughness, directly influence the contact area and bonding quality.
Factors such as the surface energy of the materials also play important roles. High surface energy often results in better bonding due to enhanced adhesion. Engineers must carefully manage these physical attributes to achieve optimal results.
Chemical Principles
Chemical principles underpin the reactions that facilitate bonding between materials. These principles involve both the nature of the materials being bonded and the chemical processes that occur at the interface.
Chemical bonding typically arises from two main mechanisms: covalent bonding and ionic bonding. In covalent bonding, atoms share electrons, leading to a much stronger bond compared to other types. In contrast, ionic bonding involves the transfer of electrons from one atom to another, resulting in charged ions that attract each other. Understanding which type of bonding applies to specific materials is vital for material selection during the bonding process.
Surface treatments, like plasma activation or chemical etching, often enhance chemical bonding by modifying the surface properties. These treatments can increase surface reactivity, making it easier for the wafers to bond during the process.
The intersection of physical and chemical principles ultimately defines the success of wafer bonding, influencing yield, reliability, and performance of semiconductor devices.
Through a combined understanding of these principles, professionals can design better processes and materials that lead to innovative advancements in wafer-to-wafer bonding technology.
Materials Used in Wafer Bonding
Wafer bonding relies on specific materials for successful integration and functionality. Understanding the materials used in this process is essential, as they determine the effectiveness and reliability of the bonding techniques. Different materials offer unique properties, which can lead to advantages or complications during bonding. Evaluating the material characteristics enables researchers and technicians to tailor processes to achieve desired outcomes, making this a critical area of study in semiconductor manufacturing.
Silicon Wafer Characteristics
Silicon wafers are the primary materials used in most wafer bonding processes. Their unique properties contribute significantly to the success of microelectronic device fabrication.
- Electrical Properties: Silicon is a semiconductor, allowing it to conduct electricity when doped adequately. This property makes it ideal for integrated circuits. The silicon wafer's resistivity can be controlled, enabling specific electrical performance.
- Mechanical Strength: Silicon wafers exhibit excellent mechanical strength, making them suitable for handling and processing. They can withstand considerable stress without breaking, which is crucial during high-temperature bonding processes.
- Thermal Conductivity: High thermal conductivity is another important characteristic of silicon. This property helps in dissipating heat generated during electrical activity in microelectronic devices. Maintaining optimal thermal performance enhances device reliability.
In addition to these properties, silicon wafers are also compatible with various doping elements, allowing for modified electrical characteristics. Their availability and well-established process frameworks make silicon the preferred choice in most applications.
Dissimilar Material Bonding
Bonding dissimilar materials presents a unique set of challenges in wafer bonding. The intrinsic differences in physical and chemical properties can affect the strength and reliability of the bond. Key considerations include:
- Material Compatibility: It is vital to assess the compatibility of different materials to minimize stress during temperature shifts and mechanical loads. Mismatched expansion coefficients can lead to cracks or delamination.
- Interfacial Adhesion: The adhesion at the interface of dissimilar materials may differ greatly compared to that of identical materials. Special adhesives or bonding techniques may be required to achieve optimal results.
- Thermal and Electrical Performance: Understanding how dissimilar materials will perform under operational conditions is critical. For example, different thermal conductivity can lead to localized overheating, affecting device performance.
- Examples of Dissimilar Material Systems: Common combinations include silicon with gallium arsenide or silicon with III-V compounds. These combinations can create advanced devices benefiting from the properties of both materials.
By studying dissimilar material bonding, researchers can develop solutions that enhance integration options and enable the creation of multifunctional devices. The ongoing advancement in this field makes it an area of significant interest for future applications.
Applications of Wafer to Wafer Bonding
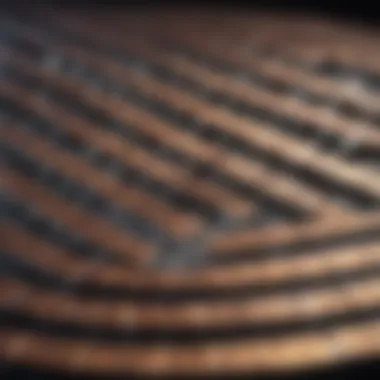
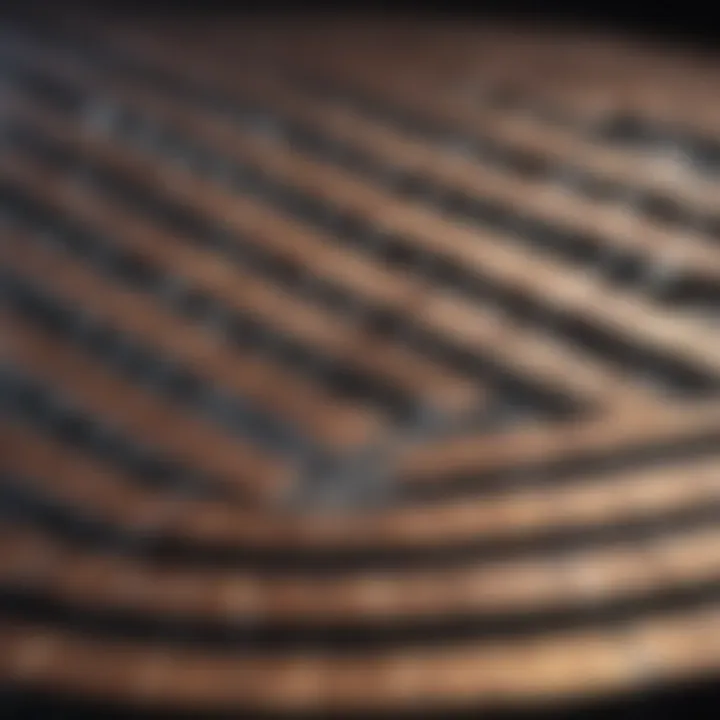
Wafer to wafer bonding holds a pivotal role in modern semiconductor manufacturing. This process allows for the fabrication of complex devices by stacking layers of materials. Understanding its applications is crucial for grasping its significance in advancing microelectronics. The efficiency and capability of this bonding process pave the way for innovations across various sectors.
This section delves into the core applications of wafer bonding, emphasizing its impact on microelectronics, 3D integrated circuits, and MEMS devices. Each application showcases the unique advantages provided by wafer bonding, driven by the need for higher performance, reduced size, and enhanced functionality.
Microelectronics
Microelectronics is a fundamental area where wafer to wafer bonding is utilized. This field involves the production of integrated circuits (ICs) that perform essential tasks in electronic devices. By using wafer bonding, manufacturers can enhance integration density, leading to more compact and efficient devices.
The advantages of wafer bonding in microelectronics include:
- Increased Performance: Bonding processes allow for the integration of different materials, such as silicon and germanium. This integration aids in improving overall device performance, increasing speed, and reducing energy consumption.
- Enhanced Capabilities: With the ability to stack multiple layers, designers can create sophisticated circuits that deliver advanced functionalities.
- Cost-Effectiveness: Wafer bonding can reduce the number of processing steps needed, ultimately decreasing manufacturing costs.
As the demand for smaller, faster, and more reliable electronics grows, the role of wafer bonding in microelectronics becomes increasingly vital.
3D Integrated Circuits
The shift towards 3D integrated circuits revolutionizes how electronic components are designed and manufactured. Wafer to wafer bonding is essential for creating these circuits, which stack multiple die vertically. This approach provides a smaller footprint while increasing performance.
The key benefits include:
- Space Efficiency: Stacking chips significantly reduces space, allowing for more compact devices.
- Improved Performance: Shorter interconnects in 3D arrangements enhance signal speed and efficiency.
- Thermal Management: Advanced bonding techniques help manage heat dissipation more effectively than traditional planar designs.
3D integrated circuits stand as a testament to the potential of wafer bonding technology, meeting the demands of modern applications that depend on high-performance computing.
MEMS Devices
Micro-electromechanical systems (MEMS) devices are another critical application of wafer to wafer bonding. MEMS combine mechanical elements with electronics at a microscale, used in various applications such as sensors and actuators.
Wafer bonding plays a significant role in MEMS fabrication by:
- Precise Alignment: Achieving accurate alignment between components during the bonding process is crucial for MEMS performance.
- Enhanced Sensitivity: Multi-layer structures can improve the sensitivity of MEMS sensors, allowing for better detection capabilities.
- Scalability: Wafer bonding facilitates large-scale production of MEMS devices, leading to affordability and broader adoption.
Challenges in Wafer Bonding Processes
Wafer bonding is an essential part of modern semiconductor manufacturing, yet it is not without its challenges. Addressing these challenges is vital for improving the efficiency and quality of bonded wafers. Understanding the intricacies involved in this process can provide crucial insights for researchers and practitioners in the field. Each challenge not only affects yield but impacts the overall reliability of the final product.
Thermal Stresses
Thermal stresses arise due to differences in thermal expansion coefficients between bonded wafers. When the temperature fluctuates, such as during processing or cooling, each material may expand or contract at different rates. This difference can create significant stress at the interface of the bond, leading to defects like cracks and delamination. Therefore, managing thermal stress is crucial in minimizing failure rates in bonded semiconductor devices. In practice, careful selection of materials with compatible thermal properties is necessary. Additionally, controlling the bonding temperature can mitigate the onset of these stresses.
Void Formation
Another critical issue in wafer bonding is void formation. Voids can occur during the bonding process when there are small pockets of air trapped at the interface. These voids can act as stress concentrators, leading to mechanical failures. Moreover, the presence of voids can affect the electrical and thermal conductivity of the bonded assembly, degrading its performance. To reduce the likelihood of voids, it is essential to optimize the bonding techniques, such as using proper pressure during bonding and ensuring clean surfaces to enhance adhesion. Monitoring the bonding process for void detection can further improve the integrity of the final product.
Material Compatibility Issues
Material compatibility is a fundamental challenge in wafer bonding, particularly when joining different types of materials. The chemical and physical properties of each material must be compatible to ensure a successful bond. Issues can arise from differences in crystallography, thermal conductivity, and even the inherent properties of the materials. For instance, when bonding silicon to gallium arsenide, careful consideration of the interfacial reactions is needed. Researchers must conduct thorough material studies to identify the best combinations for successful bonding. Additionally, advanced techniques may need to be employed to enhance compatibility, such as using intermediate layers or specialized adhesive materials.
"Understanding the challenges in wafer bonding processes is key to addressing defects and improving yield. A thorough investigation into thermal stresses, voids, and material compatibility can lead to innovative solutions."
Recent Advancements in Wafer Bonding Technologies
In the realm of semiconductor manufacturing, wafer to wafer bonding techniques are fast becoming a focal point of innovation. Recent advancements in these technologies are critical, as they pave the way for increased performance, reduced costs, and expanded applications. This section discusses the latest developments, their benefits, and key considerations surrounding these advancements.
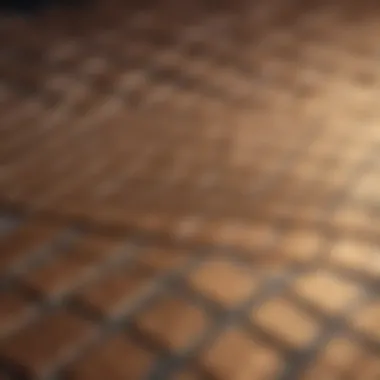
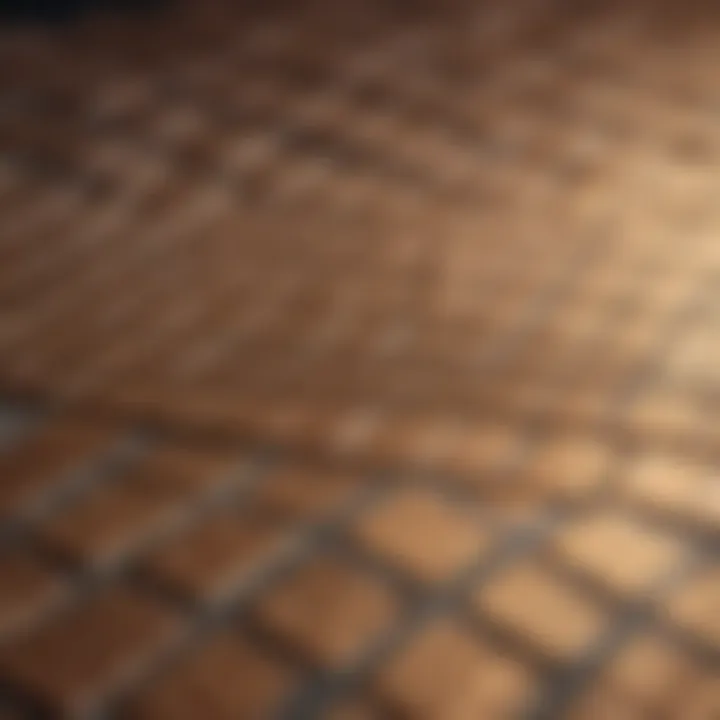
Innovations in Bonding Techniques
Recent years have witnessed significant innovations in bonding techniques. Technologies such as direct bonding and adhesive bonding have evolved. For instance, improvements in surface preparation methods have increased yield rates by minimizing defects in the bonding process. Researchers are also exploring the integration of laser heating in bonding procedures, which allows for better control over thermal profiles during the bonding phase.
By optimizing these parameters, manufacturers can achieve stronger bonds with fewer defects. This is crucial, as higher bonding strength directly impacts device reliability. Overall, aditional investigants into new materials for bonding agents are ongoing, which can lead to enhanced compatibility and performance across a variety of applications.
- Benefits of Innovations:
- Increased bond strength.
- Enhanced process control.
- Reduction in thermal stress.
Integration with Nanotechnology
The intersection of wafer bonding and nanotechnology presents unique opportunities in device fabrication. By leveraging nanoscale materials, researchers are able to create more efficient bonding interfaces. The use of nanoparticles, for example, can improve the overall adhesion qualities between dissimilar materials, which is essential in multi-material systems.
Furthermore, nanostructured surfaces can enhance surface area interactions, leading to improved bond formation. This integration allows for the development of compact devices that maintain high performance levels. As the semiconductor industry pushes towards miniaturization, these advancements become increasingly relevant.
In summary, the advancements in wafer bonding technologies are not just incremental improvements, but they represent a shift that could redefine the landscape of semiconductor fabrication. These technologies are at the forefront of enabling next-generation devices that can meet the demands of diverse applications, ranging from microelectronics to advanced photonic systems.
"Recent advancements in wafer bonding technologies are crucial for redefining manufacturing processes and enhancing device functionalities."
As researchers and industries continue to explore these emerging technologies, continued innovation in wafer bonding methods is essential for maintaining competitiveness in the semiconductor market.
Future Prospects of Wafer Bonding
The future of wafer bonding is a topical area of significant interest. As technology advances, the methods and applications of wafer bonding become more varied and sophisticated. This section explores the trends in the semiconductor industry and the potential for new applications, emphasizing the importance of the evolution of this critical process.
Trends in the Semiconductor Industry
The semiconductor industry is in a state of dynamic transformation. Several key trends are shaping its direction, particularly in relation to wafer bonding:
- Miniaturization: As devices continue to shrink, there is a growing need for advanced wafer bonding techniques that can ensure reliability while saving space.
- Increased Integration: There is a shift towards 3D integration to enhance performance. This requires efficient bonding processes to unify multiple layers of materials.
- Customization: The demand for application-specific integrated circuits (ASICs) has skyrocketed. This enables manufacturers to tailor wafer bonding techniques to match specific requirements, offering a competitive edge.
Furthermore, growing emphasis on energy efficiency is pushing manufacturers to invest in research and development. Wafer bonding processes must evolve to support low-power applications, aligning with global goals for sustainability. The increasing use of artificial intelligence and machine learning in semiconductor design also accelerates innovations in bonding techniques.
Potential for New Applications
The landscape for wafer bonding is broadening, offering exciting potential for new applications. Some areas of interest include:
- Photonics: Wafer bonding can significantly improve the integration of photonic devices, paving the way for faster optical communications and more efficient data processing.
- Quantum Computing: The burgeoning field of quantum computing requires effective thermal management and integration of disparate materials. Wafer bonding techniques may play a vital role in achieving reliable qubit connections.
- Biomedical Devices: The integration of sensors and microelectronics through wafer bonding can lead to more sensitive and compact biomedical devices, enhancing diagnostics and patient monitoring.
"The continuous advancement in wafer bonding technologies is not just about improving existing processes; it is about whether new markets can be opened and current limitations can be overcome."
The future of wafer bonding is promising, as its continuous evolution aligns with technological advancements. The factors influencing this transformation are numerous and complex, warranting attention from students, researchers, and professionals alike.
Finale
The final section of this article reiterates the importance of wafer to wafer bonding within the semiconductor manufacturing sector. This process is a cornerstone for creating integrated circuits and other microelectronic devices, linking separate wafers into a single functional unit. Understanding this topic helps elucidate the complexities involved in modern technology development. The article discusses significant techniques, applications, and challenges. Each of these elements contributes to a comprehensive view of the industry and its needs.
Summary of Key Insights
Here are some key insights gathered from the discussion throughout this article:
- Techniques: Various methods like direct bonding, adhesive bonding, and thermal bonding are central to achieving efficient connections between wafers.
- Applications: The bonding techniques have found critical usage in fields such as microelectronics, 3D integrated circuits, and MEMS devices.
- Challenges: Issues like thermal stresses and void formation must be addressed to optimize the bonding process.
- Future Prospects: The advancement of technology, particularly in integration with nanotechnology, holds promising possibilities for new applications and innovations.
These insights illustrate not only the current landscape but also the ongoing evolution within wafer bonding methodologies. The understanding of these areas unlocks further research opportunities and innovative solutions.
Call for Continued Research
While this article covers a broad range of topics related to wafer bonding, it is clear that the field requires continued exploration. Research should focus on:
- Identifying novel bonding materials that can enhance adhesion and reduce voids.
- Investigating the impact of emerging technologies on existing processes, particularly with the integration of nanotechnology.
- Understanding the long-term reliability of bonded assemblies under various operational conditions.
- Developing improved processes that reduce thermal stresses and ensure material compatibility.