Understanding the Mechanics of 3D Metal Printing

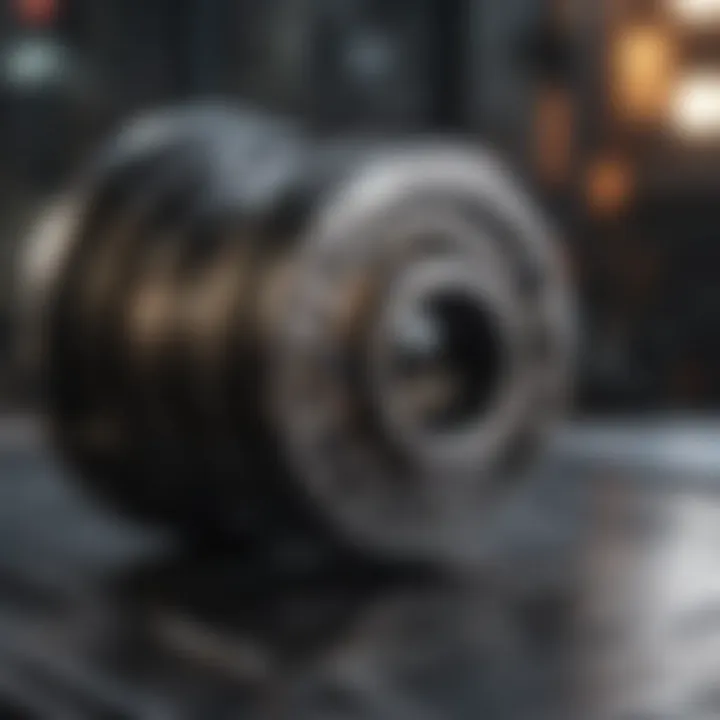
Intro
The landscape of manufacturing has changed significantly over the past decade. With the advent of 3D metal printing, a once futuristic dream is now a reality, reshaping industries and pushing the envelope of what's feasible in design and production. Rather than traditional subtractive methods, which carve out materials, 3D metal printing builds objects layer by layer, offering remarkable flexibility and precision. This article embarks on an exploration of the mechanisms behind this promising technology, detailing its key processes, materials, and applications.
In this journey, we will uncover how 3D metal printing not only streamlines manufacturing but also addresses the intricacies involved in producing complex geometries that were once thought unattainable. We will also navigate through the technological groundwork that supports this innovative fabrication method, enhancing our understanding of its relevance in today’s industrial landscape.
Research Overview
3D metal printing represents a significant leap in manufacturing technology. As we dive into its mechanisms, it is crucial to frame our understanding through a comprehensive lens.
Summary of Key Findings
- Enhanced Design Flexibility: 3D metal printing allows for intricate designs that can incorporate functional features like lattice structures, reducing weight without sacrificing strength.
- Material Efficiency: This method minimizes waste, directing resources only where needed. It contrasts sharply with traditional methods that often result in significant offcuts.
- Shortened Production Time: Prototyping and production are accelerated, enabling faster turnaround times that align more closely with market demands.
Background and Context
Metal printing has a rich history dating back to the 1980s, initially being used for creating prototypes. However, developments in technology have expanded its applications dramatically. Current trends indicate a shift towards customized solutions in sectors such as aerospace, automotive, and healthcare.
As companies recognize the potential to produce lightweight, complex parts on demand, the traditional manufacturing mindset is evolving. The increasing integration of artificial intelligence and machine learning into the design process further fuels this transition, allowing for optimized outputs that can tailor to specific needs.
Methodology
Examining the mechanisms of 3D metal printing involves a multifaceted approach.
Experimental Design
In analyzing this technology, different printing techniques such as Selective Laser Melting (SLM) and Electron Beam Melting (EBM) are under scrutiny. Such techniques contribute various potential advantages, including difference in energy source and post-processing requirements. Research studies utilize controlled experiments to compare the quality and strength of printed objects, providing insights on best practices.
Data Collection Techniques
To gather a comprehensive set of data, various techniques are employed:
- Physical Testing: Items produced through 3D metal printing are physically tested for tensile strength, fatigue resistance, and thermal properties.
- Simulation Models: Advanced software helps simulate the behavior of materials under different conditions, predicting performance before actual production takes place.
- User Parametrics: Feedback from professionals and users in industries employing these technologies also inform future developments and improvements.
The quest to understand 3D metal printing is a collaborative effort. By piecing together findings from various methodologies, we can attain a rich comprehension of both the processes and potential applications, ensuring that we are well-equipped to navigate this fascinating domain.
Preface to 3D Metal Printing
When we talk about the modern manufacturing landscape, 3D metal printing surely stands at the forefront. In this section, we’ll unpack why this technology is not just a fleeting trend, but a transformative force reshaping how industries operate. From aerospace to healthcare, the versatility of 3D printing opens up avenues previously thought impossible.
3D metal printing, at its core, brings several advantages that are hard to ignore. Firstly, it allows for the creation of complex geometries that traditional manufacturing methods struggle to achieve. Think of intricate lattice structures or bespoke implants designed for individual patients. This precision leads to enhanced performance and optimized material usage, which are essential in high-stakes sectors.
Moreover, the ability to rapidly prototype and iterate designs translates to shorter lead times in product development. Companies can go from concept to final product in a fraction of the time it would normally take, fostering innovation. In an economy where time is money, these benefits resonate deeply with manufacturers and consumers alike.
However, as we dive into the nuances, it’s crucial to also consider the limitations and challenges of 3D metal printing. Although it has come a long way, the technology faces hurdles, such as material costs and regulatory approvals. Regulations in fields like aerospace are stringent; thus, ensuring compliance adds a layer of complexity.
Understanding the mechanisms behind 3D metal printing requires a holistic view – balancing the pros and cons while recognizing the continual advancements.
Definition and Overview
3D metal printing, often regarded as a branch of additive manufacturing, involves creating parts layer by layer using metal powders or wires. Unlike subtractive methods, which reduce material through cutting or milling, additive processes add material to formulate the desired shape. This definition, while simplified, underscores a revolution in crafting techniques that synergizes technology and material science.
Additive manufacturing includes various techniques, such as Selective Laser Melting and Electron Beam Melting. These technologies empower engineers to create more efficient, lightweight components benefiting industries aiming for performance enhancements and sustainability.
Historical Context
The journey of 3D metal printing is as fascinating as the technology itself. To fully appreciate where we are today, it’s insightful to look back at its origins. The concept of additive manufacturing began in the 1980s with simple plastic-based 3D printing, gradually evolving to include metals by the late 1990s.
The introduction of metal powder-bed fusion processes marked a significant turning point. Early adopters were primarily in the niche realms of research and development. However, as companies began to realize its potential, it started finding its way into mainstream industries.
For example, aerospace giants like Boeing and GE Aviation led the charge, innovating designs that significantly reduced weight while maintaining structural integrity. This historical backdrop sets the stage for the advancements we’re witnessing today, where metal printing is not just a concept but a vital part of the production landscape.
"3D metal printing represents a leap from traditional techniques to a new era of production where complexity and customization are at the heart of innovation."
In summary, the introduction of 3D metal printing is more than an exploration of techniques; it's about understanding a paradigm shift in manufacturing that blends science, creativity, and practical application.
Core Principles of 3D Printing
The bedrock of 3D metal printing lies within its core principles. Understanding these principles is essential to grasp the intricacies of this technology. Not only do they set the stage for how objects are made, but they also inform the benefits and considerations that come with the additive manufacturing process. Specifically, these principles lay the groundwork for creativity in design, efficiency in production, and flexibility in application across various industries.
Additive Manufacturing Explained
The term "additive manufacturing" denotes a pivotal shift in how we think about creating objects. Unlike traditional subtractive methods, which carve away material to achieve a desired shape, additive manufacturing builds objects layer by layer. This method begins with a solid foundational design, often in the form of a CAD model. By introducing material—be it metal powder, filament, or even resin—incrementally and meticulously, it allows for a far greater range of complexity in designs than conventional methods might allow.
When we dissect the additive process, certain characteristics stand out:
- Reduced Waste: Materials are only used where needed. This contrasts sharply with traditional manufacturing that typically leads to excess material waste.
- Customization: Each piece can be tailored to specific requirements without the need for extensive retooling.
- Complex Geometries: Intricate design features, which were previously impractical, can now be brought to life. This opens up pathways for innovation in industries like aerospace and biomedical engineering.
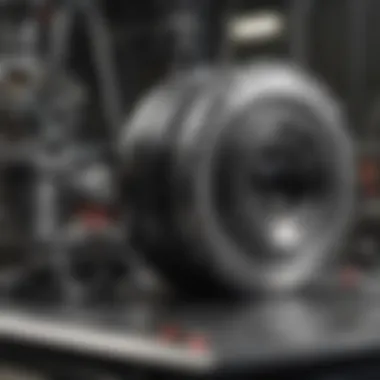
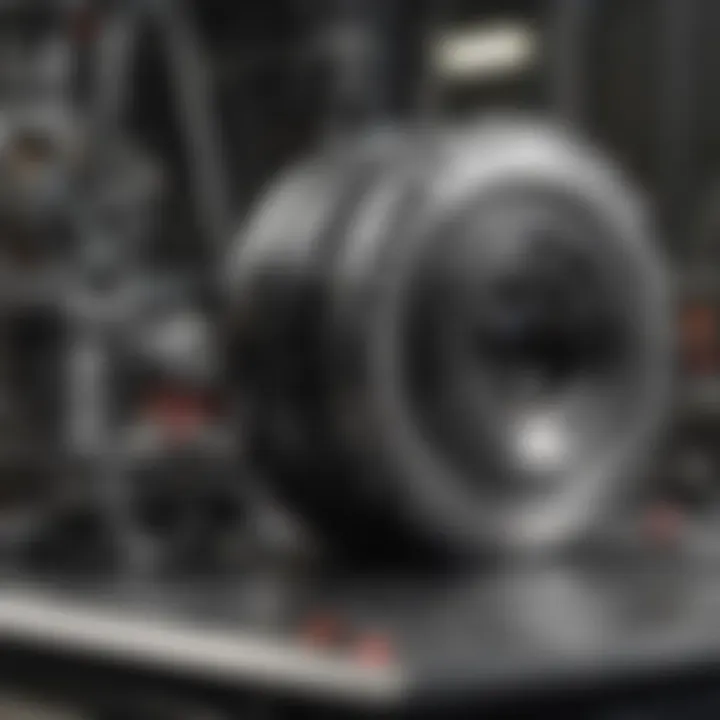
In comprehending the significance of this method, it becomes clear why many sectors are pivoting towards it. Efficiency in production and material usage is not just a benefit—it's a game-changer.
Layer-by-Layer Construction
The most distinguishing feature of additive manufacturing is its layer-by-layer construction, which profoundly impacts both the process and the outcome of 3D metal printing. This approach offers a structured, yet adaptable means of creating complex forms that would be nearly impossible to achieve through conventional methods.
The construction begins with a digital blueprint that is sliced into numerous layers. Each layer represents a specific cross-section of the final object. During the printing phase, these layers are successively deposited, either melted and fused together via heat or adhered to one another, depending on the specific printing technology in use.
Some noteworthy aspects of this technique include:
- Precision Control: Each layer can be precisely controlled for thickness and shape. This tight control allows for the adjustment of mechanical properties, which can affect strength and weight.
- Material Variety: Different materials can be blended together in the same print, creating composite layers that endow the final product with varied physical properties.
- Scalability: The process can be scaled up or down easily, meaning manufacturers can produce both small prototypes and large-scale components without a complete reconfiguration of the printing setup.
Layer-by-layer construction not only enhances the architectural freedom of metal parts but also advances how these components are integrated into larger systems, effectively pushing the boundaries of engineering.
"Additive manufacturing is not just a fad; it represents a paradigm shift in the way we think about production."
As industries strive to remain competitive, they are increasingly recognizing the core principles of additive manufacturing as a pivotal part of modern production methodologies. This mindset shift offers immense potential for innovation and efficiency, making it a fundamental aspect of understanding 3D metal printing.
Materials Used in Metal Printing
The materials employed in 3D metal printing play a vital role in determining the quality, performance, and applications of the final products. Each material carries its own properties and advantages, which can significantly influence the outcomes of manufacturing processes. Understanding the specifics of these materials is crucial for engineers, designers, and researchers engaged in the field. As we explore the different types of metals used in the industry, it becomes evident how their unique characteristics shape the landscape of manufacturing and innovation.
Types of Metals
Aluminum
Aluminum is often celebrated for its lightweight yet sturdy nature, making it a standout option in 3D metal printing. This material has a high strength-to-weight ratio, which is particularly significant in aerospace and automotive applications. Aluminum's key characteristic is its excellent corrosion resistance, granting longevity and reliability for various products.
When it comes to manufacturing processes, aluminum melts at relatively low temperatures compared to other metals, which can allow for quicker printing cycles and less energy consumption. However, aluminum can be prone to deformation under high stress, which is something that designers must consider carefully. Its unique feature is the ability to form complex geometries, a critical advantage when developing intricate designs that would be difficult to achieve with traditional methods. The main disadvantage lies in its mechanical properties that may not hold up as well under extreme temperatures, making it less ideal for certain industrial uses.
Steel Alloys
Steel alloys are another cornerstone in the realm of 3D metal printing. They offer a blend of toughness and versatility, characteristics that frequently make them the material of choice across a variety of sectors. Notably, stainless steel alloys are resistant to both corrosion and high temperatures, which enhances their usability in demanding environments like chemical processing and automotive production. This attribute is vital, as maintaining integrity under strenuous conditions is crucial for applications requiring durability.
Steel alloys are often lauded for their ease of processing and commendable finish quality. One unique feature is the ability to weld easily, enabling further manipulation of printed parts if needed. However, steel can be heavier compared to aluminum, which might be a downside in weight-sensitive applications.
Nickel Alloys
Nickel alloys are distinguished by their ability to withstand extreme temperatures and corrosive environments, making them indispensable in sectors such as aerospace and energy. They excel in applications where high-performance materials are essential, characterized by superior mechanical properties at elevated temperatures. This feature is extremely beneficial for components that must function reliably in challenging environments, such as gas turbines or jet engines.
Nickel alloys also display excellent weldability, which is a significant advantage in manufacturing processes where components may need to be joined after printing. However, the processing of nickel alloys can be more challenging due to their higher melting points. This translates to longer production times and higher energy costs during the printing phase. Furthermore, the cost of these materials may also be a reflective concern for manufacturers, prompting a careful evaluation when selecting materials for a project.
Powder Characteristics
In 3D metal printing, the properties of the powder used can considerably affect the quality and reliability of the printed object. Essential characteristics such as particle size, shape, flowability, and distribution significantly impact the printing process and the final product's structural integrity.
- Particle Size: Smaller particles can create finer details, but require more energy to sinter, while larger particles can lead to quicker printing times.
- Particle Shape: The geometry can influence how well the powder packs during the printing phase, affecting density and strength. Spherical particles are often preferred for their excellent flow properties.
- Flowability: This determines how easily the powder moves within the system, directly impacting printing speed and consistency.
- Distribution: A good mix of particle sizes can enhance packing density, leading to improved mechanical properties in the final piece.
Understanding these characteristics provides invaluable insights into optimizing materials for specific applications in 3D metal printing, paving the way for advancements in this technology. The interplay of various metals and their powder forms shapes a developing landscape that continues to revolutionize manufacturing and engineering.
Common Techniques in 3D Metal Printing
The realm of 3D metal printing is not just about fancy machines; it’s largely defined by the techniques that drive the process. Understanding these techniques gives insight into how designs are transformed into robust physical objects. The choice of technique can affect everything from the cost to the quality of the final output. Here, we will explore three predominant methods: Selective Laser Melting, Electron Beam Melting, and Direct Metal Deposition. Each has its own advantages and trade-offs—important considerations for any user.
Selective Laser Melting (SLM)
Selective Laser Melting is a well-established technique that uses a high-powered laser to melt and fuse metallic powders together. This technique allows for intricate designs and often results in parts with superior mechanical properties. One of the key benefits of SLM is its ability to create complex geometries that traditional manufacturing wouldn't easily permit. Features like internal cooling channels, which are essential in aerospace parts, can be effectively produced only through SLM.
However, it comes with considerations such as the requirement for precise laser settings and a proper powder bed management, which can be tedious. Moreover, the machines for this method represent a significant investment, often tipping the scales for small businesses. As this technique becomes more defined in various industries, practitioners must plan for the implications on time and costs, ensuring the potential reward outweighs these barriers.
Electron Beam Melting (EBM)
Electron Beam Melting is another player in this field, utilizing electron beams instead of lasers to melt metal powders. The high-energy electron beam not only increases the melting speed but is also particularly suited for high-temperature materials, which are crucial for aerospace and medical applications. One noteworthy advantage of EBM is that it operates in a vacuum, reducing contamination risks, but it also demands more extensive post-processing since there can be residual stress within the printed parts.
While EBM provides impressive layering and builds components with excellent mechanical characteristics, it requires stringent safety measures and more specialized skill sets to operate. Financially, the upfront costs are again on the higher side, but the potential for creating parts that can withstand extreme conditions serves as a strong incentive.
Direct Metal Deposition ()
Direct Metal Deposition operates a bit differently from SLM and EBM. It’s a process that uses focused energy (like a laser or an electron beam) to melt metal feedstock in layers. This method is particularly handy for repairing or adding to existing components, allowing for more versatile applications. Industries such as energy, aerospace, and automotive have begun to incorporate DMD significantly due to its adaptability.
Though its flexibility can serve as a double-edged sword, the surface finish may not be as refined as the other methods without additional post-processing such as machining. This aspect could deter some users who demand a smooth finish right off the press. However, the speed of this deposition method often makes it a valuable asset when working against tight deadlines.
In essence, the choice of technique in metal 3D printing should be driven by the specific needs of the application. Whether it’s the intricate design capabilities of SLM, the robustness offered by EBM, or the versatility of DMD, each method provides pathways for innovation, inviting both challenges and rewards within the manufacturing landscape.
"Understanding the techniques of 3D Metal Printing is not just about knowing how to print; it's about knowing why one method works better for a specific purpose than the others."
Choosing the right technique is critical when considering quality, costs, and final application. It is this nuanced understanding that separates good manufacturers from great ones.
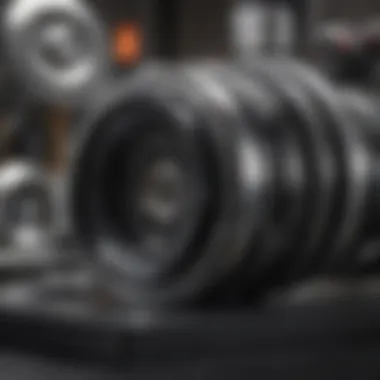
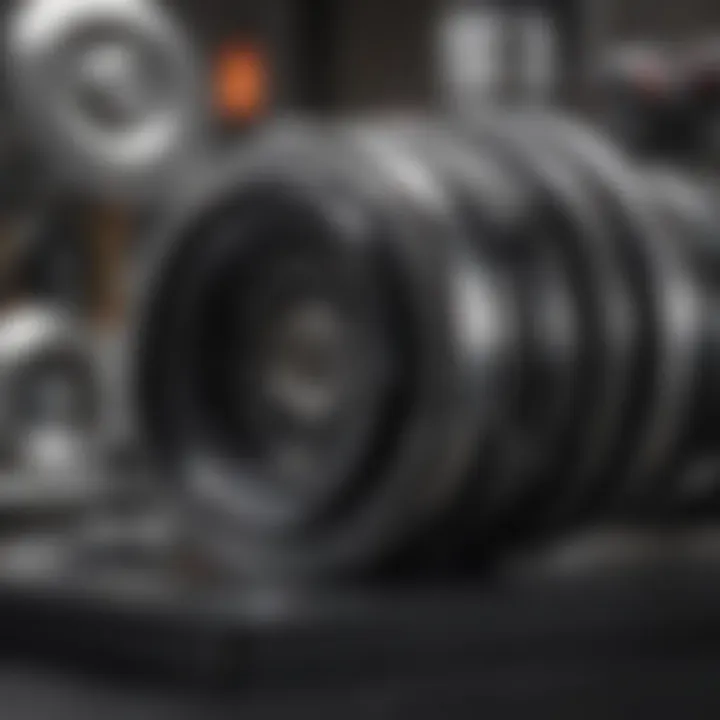
The 3D Printing Process
The 3D printing process serves as the backbone of metal printing technology, intricately linking design, material, and final product while ensuring a high degree of precision and adaptability. Understanding this process allows professionals in various fields to harness the advantages offered by 3D printing effectively, addressing specific project requirements and boosting innovation. Each phase of the process adds a unique layer, contributing to efficiency and optimal material utilization, which is crucial as industries strive for sustainability and cost-effectiveness.
Designing the Model
Creating the initial model is a critical starting point in the 3D printing process. This phase typically involves using Computer-Aided Design (CAD) software, which allows designers to build a digital representation of the object they intend to print. The beauty of the digital model lies in its flexibility; changes can be made swiftly without the need for physical alterations. Specific geometries can be crafted, leading to complex shapes that are otherwise challenging or even impossible to achieve through traditional manufacturing.
However, it’s vital to consider the compatibility of the model with metal printing. Factors such as layer thickness and support structures must be accounted for, as they can impact the printability and final quality of the item. This phase also involves optimizing the design to minimize material use and enhance performance, reflecting the design's critical role in the overall success of the 3D printing venture.
Slicing and Pre-processing
Once the design is on point, the next step is slicing it into layers. This is done using specialized software that converts the 3D model into a format the printer can understand, usually G-code. The slicing process is not merely about dividing a model; it requires strategic thinking. The software needs to define parameters like layer height and fill density, which plays a pivotal role in the strength and integrity of the final product.
Pre-processing also involves preparing the printing parameters and setting up the 3D printer itself. These preparation stages are where potential problems can be anticipated and addressed. For example, air gaps may occur if the spacing is not measured correctly, leading to weak spots in the final structure. The success of the printing largely depends on meticulous slicing and pre-processing, as they lay the groundwork for accurate and effective production.
Printing Phase
During the printing phase, each layer of metal powder is deposited and selectively fused, often with the help of lasers or electronic beams. This stage is where the magic happens. The printer follows the sliced model instructions, laying down the material layer by layer until the object takes shape.
One significant consideration here is temperature control. For processes like Selective Laser Melting, maintaining precise temperatures is vital to ensure proper melting and bonding of the metallic powder. Often, the printer is equipped with sensors that monitor heat levels throughout this phase. This attention to detail not only guarantees quality but also represents a critical factor in avoiding defects in the finished piece.
Post-Processing Techniques
After the printing is complete, the part typically requires post-processing to ensure it meets the desired specifications.
Heat Treatment
Heat treatment plays a significant role in refining the mechanical properties of a 3D printed metal part. By subjecting the printed component to specific heating and cooling cycles, the material's microstructure can be altered to enhance strength, ductility, and overall performance. One key characteristic of heat treatment is its ability to relieve residual stresses that may have developed during the printing process, which is crucial for components subjected to high stress in practical applications.
Although heat treatment offers remarkable improvements in material properties, it does come with challenges. The treatment process can lead to distortions, particularly in complex geometries. Still, many professionals consider it a necessary step for achieving performance reliability, marking it as a popular method in high-stakes industries like aerospace and automotive.
Surface Finishing
Surface finishing is another vital post-processing step, geared towards improving the object’s surface quality and finish. It addresses issues like roughness, which can directly affect functionality and aesthetics. Techniques such as polishing, bead blasting, or chemical vapor deposition can drastically improve the surface characteristics, often required to meet industry standards.
One of the key benefits of surface finishing is enhanced corrosion resistance, particularly important in applications where metals are exposed to harsh environments. However, it can be a double-edged sword; while it can enhance performance, it may also increase production time and costs. Balancing the need for a quality surface finish against economic considerations is an ongoing challenge for professionals in the sector.
In summary, the 3D printing process encompasses a series of interconnected stages, each contributing to the ultimate success of the metal components produced. Designing, slicing, printing, and post-processing form an ecosystem that demands careful attention to detail and consideration of implications for various applications.
Quality Assurance in Metal Printing
Quality assurance is a pivotal aspect of 3D metal printing, a discipline that has garnered attention across various sectors, including aerospace, medical, and automotive industries. The precision and reliability of parts produced through this technology hinge significantly on rigorous quality assurance practices. This involves not just a one-time check, but a thorough process embedded throughout every stage of production. The essence of quality assurance can be distilled into elements like validation of materials, optimization of printing parameters, and post-processing assessments, ensuring that every produced part meets the demanding specifications required by its application.
Density and Porosity Assessment
Density and porosity are key indicators of the quality of metal parts produced via 3D printing. The level of density directly impacts strength and reliability. Porosity, on the other hand, can lead to weaknesses that are often unseen until failure occurs. A piece with high porosity may be structurally compromised, lending to catastrophic performance. To evaluate these qualities, it's common to utilize methods such as Archimedes' principle for density measurements and advanced imaging techniques to identify voids. Adopting such assessments helps to create a proactive approach toward potential defects, allowing manufacturers to adjust parameters during production rather than relying solely on final tests. This not only minimizes waste but also enhances durability in final products.
Geometric Accuracy
Geometric accuracy refers to how closely the finished part matches its original design specifications. This metric is crucial, as even minute deviations can result in catastrophic failures, especially in industries like aerospace where lives are at stake. Factors influencing geometric accuracy include the quality of the initial design files, the precision of the printing machinery, and environmental conditions during printing. Advanced software solutions can simulate the printing process, predicting potential distortions and allowing preemptive corrections. Without precise geometric fidelity, the entire premise of 3D printing—design flexibility—could be compromised, leading to higher operational risks.
Non-Destructive Testing (NDT)
Non-destructive testing (NDT) methods are gaining traction as an essential quality assurance practice in metal printing. Unlike destructive testing, which sacrifices parts for analysis, NDT allows for the evaluation of components without altering their material integrity. Techniques employed in NDT include ultrasonics, X-ray imaging, and dye penetrant testing, each revealing different aspects of a component's quality, be it surface imperfections or internal defects. Utilizing NDT not only enhances safety by ensuring components are robust but also reduces costs associated with material wastage and component failure. By integrating NDT into the regular quality assurance process, manufacturers can maintain an efficient production cycle while fostering trust in the reliability of their outputs.
"In metal printing, ensuring quality is not merely a check box; it’s about forging trust among end-users and maximizing the potential of design innovations."
Applications of 3D Metal Printing
The realm of 3D metal printing boasts a myriad of applications spanning across various industries. Understanding these applications is essential, as they illustrate not just how the technology functions, but also why it matters in today’s world. From aerospace to healthcare, the benefits of 3D metal printing are palpable. Companies now leverage the technology not only to reduce material waste but also to produce designs that were once confined to the realm of imagination.
3D metal printing opens doors for customization that traditional manufacturing methods struggle to achieve. This capacity for on-demand production allows for rapid iteration in design, meaning products can evolve based on immediate feedback and specific requirements. For businesses and sectors where precision is key, this presents a significant advantage.
Yet, there are considerations to keep in mind. While the technology fosters innovation, navigating the legal and safety landscapes is paramount, particularly in regulated fields like medicine and aerospace. Therefore, the applications of this technology should be examined not just through the lens of possibility, but also through the prism of responsibility.
Aerospace Industry
In the aerospace sector, the stakes are incredibly high, demanding advanced materials and innovative manufacturing techniques. 3D metal printing has emerged as a game-changer, enabling the production of lightweight components that maintain structural integrity. The ability to print complex geometries allows for parts that are lighter yet stronger, significantly enhancing fuel efficiency and performance. Key manufacturers like Boeing and Airbus are already harnessing this technology, creating everything from engine mounts to intricate structural components.
Furthermore, the reduced lead times associated with 3D metal printing are invaluable in an industry where time is money. The creation of just-in-time parts also means manufacturers can keep inventories low, decreasing overhead costs. Moreover, long-term maintenance of aircraft can benefit tremendously, enabling rapid prototyping for replacement parts that may cease to be in production.
"3D metal printing paves new paths for innovation; it's not merely about making things, it's about reshaping possibilities."
Medical Devices and Implants
The medical field stands at the forefront of the transformative potential of 3D metal printing. Here, customization reaches an entirely new level. Surgeons can devise individualized implants tailored to the specific anatomy of a patient, significantly improving outcomes in procedures.
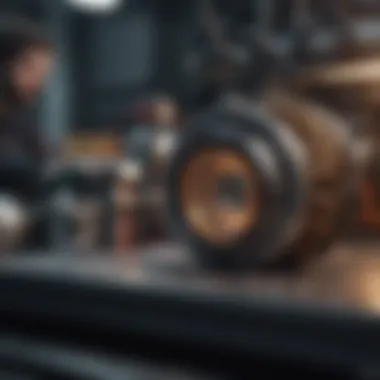
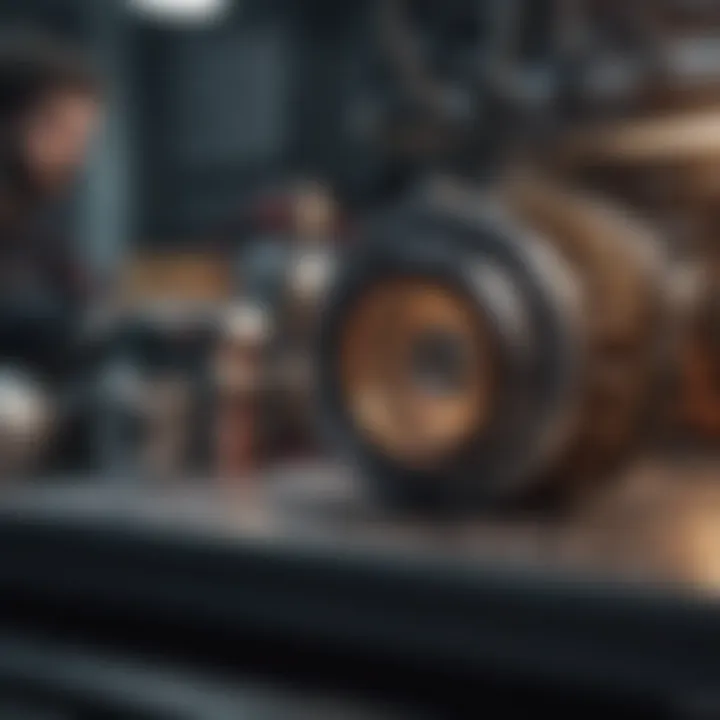
Titanium alloys are frequently used in this domain, providing the strength required for critical components like orthopedic implants and dental structures. The layer-by-layer printing method fosters intricate designs, resulting in implants that mimic the natural bone structure, facilitating better integration and healing.
Moreover, the ability to rapidly iterate designs based on clinical feedback means that products can evolve swiftly, keeping pace with new research and technological advances. This rapid responsiveness is crucial in a field where patient needs are paramount.
Automotive Sector
While some might view 3D printing as mainly an aerospace or medical technology, the automotive industry is tapping into its potential, too. Car manufacturers increasingly turn to 3D metal printing for prototyping and producing functional parts. Ford and BMW are paving the way in this arena, utilizing metal printing to create lightweight components that enhance performance and efficiency.
One significant advantage is the reduction in material wastage. Traditional manufacturing processes can generate a lot of scrap metal; 3D printing, being additive, minimizes this by utilizing only the material necessary to construct the part.
Additionally, automotive applications often focus on the customization of vehicles. Enthusiasts can now explore bespoke parts that bring a personal flair to their cars, which was previously a complex and expensive process. With 3D metal printing, custom solutions become not just viable but also economically sensible.
Future Trends in 3D Metal Printing
The landscape of 3D metal printing is continuously shifting. Understanding future trends is vital for industry leaders and researchers alike. This understanding not only anticipates changes but offers insights on strategic opportunities that can be harnessed.
Advancements in Materials Science
In the realm of 3D metal printing, materials science is undergoing a renaissance. Manufacturers are not simply limited to traditional metals like stainless steel and titanium anymore. There’s a growing interest and investment in developing new alloy compositions and advanced metal powders that enhance printability and performance.
One particular area of excitement is the development of biocompatible materials for medical applications. Researchers are exploring the use of magnesium and titanium alloys that not only match the mechanical properties needed for implants but also promote bone growth, blending seamlessly with human tissue. As we delve deeper into these materials, we can expect:
- Enhanced Performance: Alloys that can withstand extreme conditions, making them suitable for aerospace and automotive industries.
- Lightweight Options: New materials that cut down on weight while retaining strength, crucial for energy efficiency.
Moreover, the properties of existing materials are being improved through nanotechnology, allowing for finer control and better characteristics, such as corrosion resistance and thermal stability. Experiments in using recycled powders are also gaining traction, pointing towards a more sustainable approach in manufacturing.
Integration with AI and Robotics
Artificial intelligence and robotics are playing a pivotal role in transforming 3D metal printing practices. The integration of these technologies promises enhanced productivity and quality, focusing heavily on automation and precision. Automated systems can improve the design-to-print workflow, reducing human error and optimizing machine operations.
For instance, AI can analyze print data in real-time, allowing for adjustments during production. This enables:
- Feedback Loops: Continuous monitoring can adjust parameters like temperature and speed on the fly, ensuring greater accuracy and quality.
- Predictive Maintenance: AI algorithms can predict when machinery will require maintenance, minimizing downtime and saving costs.
Moreover, using robots for tasks such as post-processing not only reduces labor but also increases efficiency in finishing parts. The manufacturing floor is becoming a more connected space, where machines communicate with one another, leading to smoother operations and a more streamlined production cycle.
"The synergy between materials science advancements and AI integration will not just drive innovation but fundamentally reshape the capabilities of 3D metal printing for many industries moving forward."
As this fusion of technologies continues, we can expect significant breakthroughs that extend beyond traditional boundaries, ultimately resulting in more efficient, cost-effective, and impactful applications of 3D metal printing.
Challenges Facing the Technology
The evolution of 3D metal printing is indeed revolutionary, but like any emerging technology, it doesn't come without its hurdles. Understanding these challenges is critical, not just for those in the field but also for industries considering adopting this innovative approach for their manufacturing needs. The barriers to entry can shape the trajectory of how this technology develops and integrates into various domains. Therefore, let’s take a closer look at some of the significant challenges faced by 3D metal printing today.
Cost of Equipment
The machinery and equipment needed for 3D metal printing often come with a hefty price tag. High-end printers such as those created by companies like EOS or Renishaw can set you back hundreds of thousands of dollars. This initial investment might deter small businesses or startups from venturing into 3D printing, as they often operate on tighter budgets. Not to mention the cost of maintenance, which can also be substantial.
The ongoing expenses don't stop at just the printers. Post-processing equipment, such as heat treatment ovens or CNC machines, also contribute to the total cost. It’s a financial hurdle that can widen the gap between large corporations and smaller enterprises.
Manufacturers looking to capitalize on this advanced technology need to weigh the benefits against the financial commitment. The return on investment won't be immediate, but it can be rewarding with strategic business planning.
Regulatory Barriers
Navigating the regulatory landscape can be another tough nut to crack. As 3D metal printing pushes boundaries, different industries must adhere to strict guidelines and compliance requirements. For example, aerospace or medical sectors require rigorous certifications due to the potential implications of failure in critical applications.
What complicates matters further is that regulations can vary widely between regions. For companies looking to operate globally, this means having to keep up with multiple sets of rules and regulations, which can be a daunting task.
Additionally, the materials used in 3D printing might also be subject to regulations, as they can greatly affect the safety and performance of the printed objects. Understanding and ensuring compliance can be cumbersome and might slow down the ramp-up phase for businesses looking to implement this technology.
"The complexity of integration cannot be underestimated; it can either propel a company into the future or stall them right in their tracks."
By being aware of both cost and regulatory messes that lie ahead, stakeholders can better prepare themselves for implementing strategies to overcome these barriers. The knowledge of these challenges provides a solid footing for future breakthroughs in the technology.
Culmination
In concluding this article, it’s pivotal to underscore the significance of 3D metal printing, particularly in its role as a game-changer within diverse sectors. This technology not only offers innovative manufacturing solutions but also facilitates a paradigm shift in how products are conceived, designed, and produced. The capacity for intricate designs that traditional methods cannot achieve is a noteworthy advantage, promoting creativity and enhancing functionality in finished products.
Recap of Key Points
To summarize, we have delved into the following key aspects of 3D metal printing:
- Core Principles: We examined the additive manufacturing process, highlighting how layer-by-layer construction revolutionizes design possibilities.
- Materials: A variety of metals, such as aluminum and steel alloys, were explored, shedding light on their properties and applications.
- Techniques: We identified techniques like Selective Laser Melting and Electron Beam Melting, distinguishing their unique contributions to the field.
- Quality Assurance: Key processes like density assessment and geometric accuracy were emphasized as critical measures for ensuring product integrity.
- Industry Applications: Real-world applications in aerospace, medical, and automotive sectors showcased the practical significance of this technology.
- Challenges: Cost barriers and regulatory hurdles were discussed, illustrating the complexities that the industry faces.
Implications for Future Developments
Looking ahead, the future of 3D metal printing teems with potential. Innovations in materials science may lead to the discovery of new alloys and composites, enhancing performance and capabilities in manufacturing. The integration of artificial intelligence and robotics into the printing process is likely to bolster efficiency, reduce error rates, and democratize production further.
Moreover, as regulatory frameworks evolve, they may pave the way for broader acceptance and adoption across industries. This shift can lead to reduced waste and more sustainable manufacturing practices, aligning with broader environmental goals. In essence, the trajectory of 3D metal printing is poised for substantial growth, with implications that will echo throughout various fields for years to come.
"The future is not something we enter. The future is something we create."
In all, while 3D metal printing is not without its challenges, the benefits it offers to innovation and efficiency make it a cornerstone for future manufacturing. It’s a field ripe for exploration, and its advancements will undoubtedly shape industries far beyond our current imagination.