Exploring Aluminum Hardening Techniques and Uses
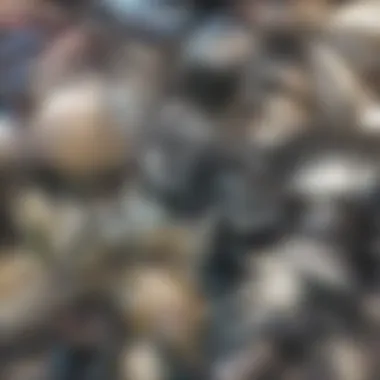
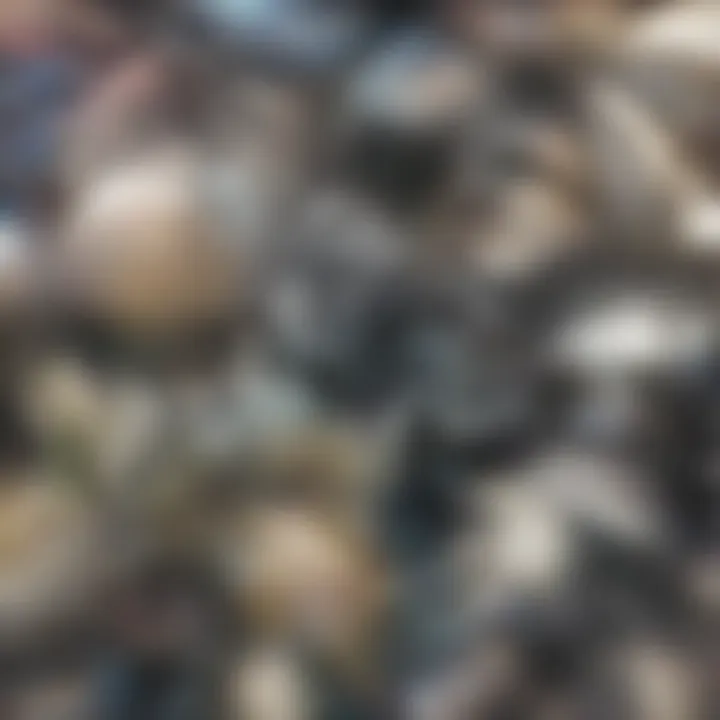
Intro
Aluminum is a versatile material known for its light weight and good resistance to corrosion. However, in many applications, aluminum's inherent softness and low strength limit its usability. Hardening processes allow for significant improvement in its mechanical properties, making it suitable for demanding environments. This article investigates the various methods employed to harden aluminum, their applications, and how advancements in technology are transforming the landscape of manufacturing and engineering.
Research Overview
Summary of Key Findings
The hardening of aluminum can be achieved through several methods, each offering unique benefits. Notable techniques include:
- Alloying: Combining aluminum with other metals enhances strength and durability.
- Precipitation Hardening: This method involves the formation of fine precipitates within the alloy to block dislocation movement, thereby increasing strength.
- Cold Working: This technique deforms aluminum at room temperature to improve hardness and strength.
Understanding these techniques provides insight into their significance in modern applications, particularly in aerospace, automotive, and construction sectors.
Background and Context
Historically, aluminum has played a crucial role in various industries due to its favorable properties. However, with the increasing demand for high-performance materials, the need for aluminum hardening has become paramount. The following discussion highlights the transformative impact of hardening techniques in different fields, underscoring the importance of continued research and development.
Methodology
Experimental Design
To properly assess the effectiveness of aluminum hardening methods, systematic experimental designs are paramount. Researchers may employ a range of standardized tests that evaluate mechanical properties like tensile strength, yield strength, and hardness. This enables the comparison of untreated aluminum with hardened variants under identical conditions.
Data Collection Techniques
Data collection techniques can include:
- Mechanical Testing: Standard procedures like Rockwell and Brinell hardness tests.
- Microscopy: Use of scanning electron microscopy to observe microstructure changes post-hardening.
- X-ray Diffraction: To analyze phase changes induced by various hardening methods.
Foreword to Aluminum Hardening
The hardening of aluminum is a pivotal concern in material science, and its relevance extends across various industries. Understanding how to enhance aluminum's mechanical properties can lead to superior products and applications. With increased demand for lightweight yet strong materials, aluminum hardening has gained prominence in sectors like aerospace, automotive, and construction.
Definition and Importance
Aluminum hardening refers to the processes employed to increase the hardness and durability of aluminum alloys. This transformation is essential for improving the performance of aluminum in demanding environments. The significance of this process lies in its ability to modify the material's structure, thereby enhancing its resistance to deformation and wear. As industries move towards more efficient and effective materials, the need for hardened aluminum becomes clearer. The benefits include increased load-bearing capabilities, which can lead to lighter structures without compromising strength.
Overview of Aluminum Alloys
Aluminum alloys form the basis of aluminum hardening. They consist of aluminum combined with other elements, such as copper, magnesium, and silicon, to enhance specific characteristics. Each alloy is designed with particular applications in mind, and understanding their composition is crucial for selecting the right one based on performance requirements.
The main categories of aluminum alloys are:
- Wrought alloys: These are manipulated through mechanical processes and typically exhibit good ductility and strength. Commonly used in structural applications.
- Casting alloys: Prominent for their ability to be easily molded, these alloys are beneficial in manufacturing complex shapes.
Different alloys exhibit varying mechanical properties due to their distinct compositions. Thus, the decision to harden aluminum involves not just hardening techniques but also which alloy to select, as this determines the effectiveness of the hardening process.
Overall, the exploration of aluminum hardening is essential for advancing capabilities in material applications. The techniques discussed in the following sections will clarify how these processes intricately affect the properties and usability of aluminum in modern engineering.
The Science Behind Hardening Aluminum
Understanding the science behind aluminum hardening is crucial for several reasons. This section aims to elucidate how the atomic characteristics of aluminum interact with various hardening methods. The result is enhanced mechanical properties, which are vital for many applications. As industries increasingly rely on lightweight materials that can withstand rigorous conditions, knowing the underlying science can facilitate innovation, lead to better material selection, and optimize design processes.
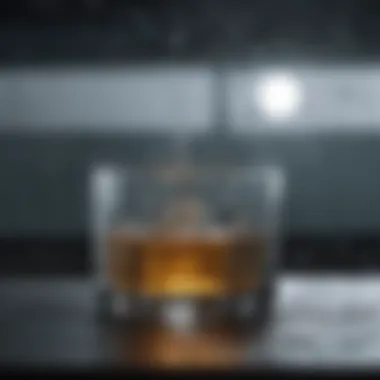
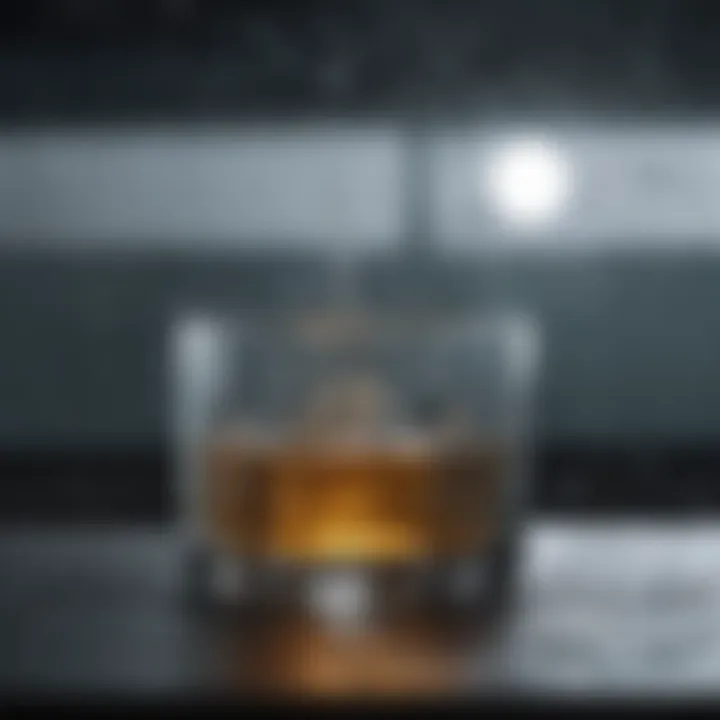
Atomic Structure and Properties of Aluminum
Aluminum has an atomic number of 13, and its atomic structure significantly influences its properties. It possesses a face-centered cubic (FCC) crystal structure. This arrangement allows for considerable ductility, but only limited strength in its pure form.
The primary properties of aluminum include:
- Lightweight: Aluminum is less dense compared to steel, making it a preferred choice for applications where weight reduction is critical.
- Corrosion Resistance: Naturally forms a protective oxide layer, enhancing its durability in many environments.
- Electrical Conductivity: Good conductor of electricity, making it suitable for electrical applications.
Despite these benefits, pure aluminum's weakness necessitates hardening methods. By manipulating its atomic structure through various techniques, manufacturers can achieve desired mechanical properties such as improved strength while retaining other advantageous properties.
"Understanding aluminum's atomic structure is key to exploiting its mechanical properties effectively."
Phase Diagrams: Understanding Alloying
Phase diagrams serve as fundamental tools for understanding how different alloying elements influence aluminum's properties. They illustrate the relationships between temperature, composition, and the phases of a material.
In the case of aluminum alloys, phase diagrams help determine how different metals, such as copper, magnesium, or zinc, interact with aluminum at various temperatures. This information is vital for choosing appropriate alloy compositions for specific applications.
Key components of aluminum phase diagrams include:
- Liquid Phase: Where the alloy is in a molten state.
- Solid Phase: Represents the various solid solutions and intermetallic compounds.
- Eutectic Point: Shows the specific composition where liquid and solid phases coexist at a lower temperature.
Through careful analysis of phase diagrams, manufacturers can predict the resultant properties of specific aluminum alloys, enabling optimization of hardening processes. Consequently, this understanding allows engineers to produce materials with enhanced performance tailored for precise applications.
Methods of Aluminum Hardening
Understanding the methods of aluminum hardening is essential for various industries looking to improve the performance of aluminum components. These methods not only enhance the strength and durability of aluminum but also provide it with improved resistance to wear and corrosion. In this section, we delve into different techniques, including alloying, heat treatment, precipitation hardening, cold working, and surface hardening methods. Each method has distinct advantages and considers the material's specific applications.
Alloying Techniques
Alloying is the process of combining aluminum with other elements to create a material with enhanced properties. Common alloying elements include copper, magnesium, and zinc. The combination increases strength and sometimes improves corrosion resistance. Some alloys might be easier to extrude or weld. Understanding these different combinations is crucial for tailored applications, as specific alloy compositions can significantly influence the material's mechanical properties. Typically, alloy series like 2000, 6000, and 7000 series highlight unique characteristics based on their constituent elements.
Heat Treatment Processes
Heat treatment processes involve controlled heating and cooling cycles, which modify aluminum's microstructure and enhance its mechanical properties. This method can vary widely, focusing on aspects like solution heat treatment, quenching, and aging. Each process contributes distinctively to the final physical characteristics of the material. For instance, proper heat treatment can result in significant gains in yield strength, making the aluminum more capable of withstanding high stress conditions. Manufacturers often consider these processes to achieve desired specifications, especially in sectors such as aerospace and automotive.
Precipitation Hardening Explained
Precipitation hardening is a method employed to significantly increase the strength of aluminum alloys through a two-step process involving solution treatment and aging, which leads to the formation of finely dispersed precipitates. This process is particularly used for alloys that are difficult to strengthen through other traditional methods.
Solution Treatment
Solution treatment involves heating the aluminum alloy to a high temperature, where the alloying elements dissolve into the aluminum matrix, creating a homogeneous solution. The specific characteristic of solution treatment is its ability to maximize the solubility of other elements. This step is beneficial because it prepares the alloy for the aging process that follows because it allows fine precipitate particles to form later. The unique feature of this method lies in its capacity to enhance strength without drastically sacrificing ductility. Although it is effective, careful control of temperature and time are critical, as excessive heat can lead to material loss due to oxidation.
Aging Process
Aging is the second phase of precipitation hardening, where the treated alloy is held at a lower temperature to allow precipitates to form. The key characteristic of the aging process is its fine-tuning effect on the alloy, enhancing its strength through the controlled growth of particles. This method is immensely beneficial as it can increase yield strength significantly while maintaining the fine balance of ductility that aluminum is renowned for. The aging process can be tailored to specific applications depending on the desired hardness and strength characteristics. However, it is also crucial to consider that improperly executed aging can lead to over-aged alloys that lose desirable properties.
Cold Working Techniques
Cold working techniques involve deforming aluminum at room temperature to enhance its mechanical properties. This process increases dislocation density within the material, leading to improved strength. Common methods include rolling, forging, and drawing. Cold working allows manufacturers to achieve shapes and sizes with more precise tolerances. However, this method may also lead to increased brittleness, which limits further processing unless an annealing step occurs to restore ductility.
Surface Hardening Methods
Surface hardening methods are crucial for applications requiring enhanced wear resistance and durability on the outer layer of aluminum components. These techniques can provide materials with a hard exterior while maintaining a softer, tougher interior, effectively combining strengths and mitigating weaknesses. Two prominent methods include anodizing and nitriding.
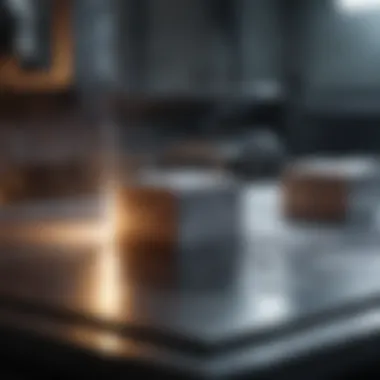
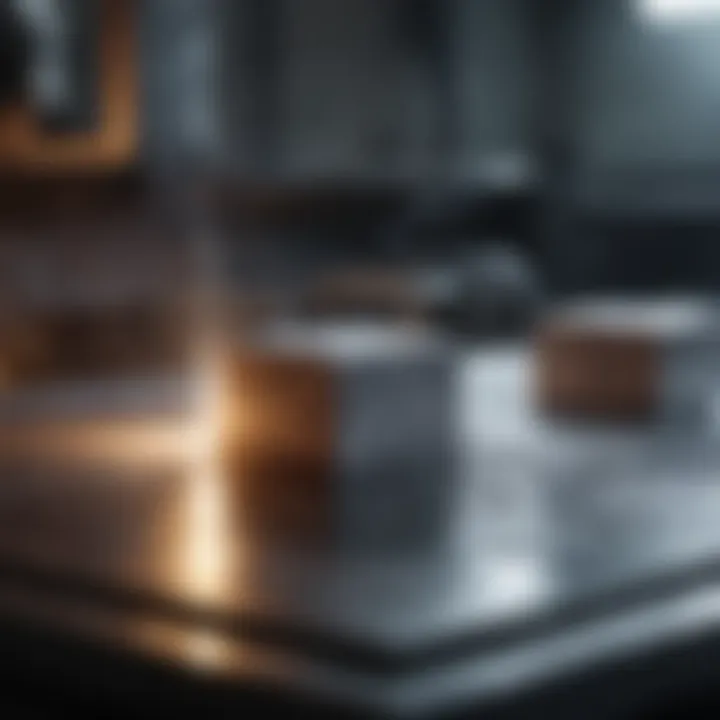
Anodizing
Anodizing is an electrochemical process that converts the aluminum surface into a decorative, corrosion-resistant, anodic oxide finish. The key characteristic of anodizing is that it not only increases surface hardness but also improves corrosion resistance significantly. This makes it a popular choice for applications where aesthetics are essential, such as in consumer electronics and architectural products. It offers the unique advantage of allowing further dyeing or coloring of the surface, enhancing appearance without compromising functionality. However, it requires proper surface preparation and can be limited by the alloys used.
Nitriding
Nitriding involves diffusion of nitrogen into the aluminum surface, creating a hard nitride layer. The primary contribution of nitriding is the significant enhancement of wear resistance it provides to aluminum components. This method is highly valued in situations demanding high surface hardness, such as in dies and tooling. The unique feature of nitriding is that it allows for excellent fatigue strength while maintaining aluminum's lighter weight. Nonetheless, it may not suit all aluminum alloys and can lead to brittleness if not carefully processed.
Mechanical Properties of Hardened Aluminum
The mechanical properties of hardened aluminum are vital for understanding its performance in various applications. As aluminum undergoes hardening processes, it exhibits enhanced characteristics that improve its usability across different industries. These properties primarily include strength, toughness, fatigue resistance, and ductility. Each of these factors plays a crucial role in determining how aluminum components will perform under stress, making it essential for engineers and manufacturers to consider them.
Hardened aluminum is often chosen for its favorable strength-to-weight ratio. This makes it an ideal material in sectors such as aerospace and automotive, where maximizing strength while minimizing weight is essential. Furthermore, the toughness of aluminum is significantly improved after hardening, which prevents materials from fracturing under high load or impact conditions. These attributes increase the lifespan and reliability of aluminum products.
Strength and Toughness
Strength in aluminum refers to its ability to resist deformation or failure when subjected to stress. The hardening processes, such as heat treatment and alloying, are key to augmenting this strength. Hardened aluminum demonstrates considerable resilience, which is essential in applications where structural integrity is paramount.
Toughness, on the other hand, is the ability of a material to absorb energy and plastically deform without breaking. In hardened aluminum, the toughening mechanisms allow it to withstand significant forces without succumbing to fracture. This combination of strength and toughness is critical in components used in extreme conditions, such as airframes or automotive chassis. The balance between these properties must be precisely managed for optimal performance.
Strength and toughness contribute to the reliable performance of aluminum components under demanding conditions, ultimately affecting the safety and functionality of the products.
Fatigue Resistance and Ductility
Fatigue resistance is an indispensable property in materials that undergo repeated loading and unloading. Hardened aluminum exhibits improved fatigue resistance due to its microstructural changes during the hardening processes. This makes it less prone to developing cracks over time, providing an extended service life in cyclic-load applications. For engineers, understanding fatigue behavior is crucial for selecting materials that will endure over time.
Ductility, defined as a material's ability to deform under tensile stress, is equally important. While hardening generally increases strength, it can reduce ductility if not carefully controlled. In aluminum alloys, maintaining a balance between strength and ductility is essential. This ensures that a material can withstand deformation without breaking, making it suitable for applications that require bending or shaping.
In summary, the mechanical properties of hardened aluminum—its strength, toughness, fatigue resistance, and ductility—are central to its performance in a range of applications. Understanding these properties allows for more informed decisions in material selection, fostering innovations in engineering design.
Applications of Hardened Aluminum
Hardened aluminum plays a pivotal role across various industries due to its enhanced mechanical properties. Understanding its applications is crucial for appreciating the material's significance. The benefits of using hardened aluminum include increased strength, reduced weight, and improved corrosion resistance. These properties make the metal suitable for demanding environments and high-performance applications.
Aerospace Industry
The aerospace sector is one of the primary beneficiaries of hardened aluminum. Aircraft components require materials that can withstand extreme conditions while maintaining a lightweight profile. Hardened aluminum alloys, like 7075 and 6061, are often utilized in manufacturing airframes and other structural components. The use of precipitation hardening techniques leads to a significant increase in tensile strength and fatigue resistance.
Moreover, the corrosion-resistant properties of these alloys are essential, as aircraft must endure varying atmospheric conditions. As such, the performance and lifespan of aerospace components are greatly enhanced with the use of hardened aluminum.
Automotive Applications
In the automotive industry, the shift toward lightweight materials has made hardened aluminum an attractive option. Reducing weight contributes to improved fuel efficiency and lowers emissions. Vehicle parts such as engine components, frames, and wheels increasingly utilize hardened aluminum alloys. These materials not only reduce overall weight but also provide strong resistance to impact and wear.
Hardened aluminum can also help in improving the design flexibility of automotive engineering. It allows for more complex shapes and structures. As electric vehicles continue to rise in popularity, the need for durable and lightweight materials will likely increase even further.
Construction and Manufacturing
The construction industry benefits from the use of hardened aluminum in applications such as structural frameworks, window frames, and roofing. Its strength-to-weight ratio allows for the design of buildings with larger spans and increased durability. The corrosion resistance of aluminum also minimizes long-term maintenance costs, making it a cost-effective choice in various projects.
Manufacturing processes use hardened aluminum in tooling and equipment as well. Its ability to withstand wear and tear makes it a favorable option for producing high-quality products. The material's versatility further enhances its role in modern construction methods.
Consumer Goods and Electronics
In the realm of consumer goods, hardened aluminum finds its place in numerous applications, from smartphones to laptops. The lightweight nature of aluminum combined with its durability make it ideal for creating portable devices that can resist damage from daily use. Hardening processes ensure that these products can withstand drops and impacts, prolonging their lifespan.
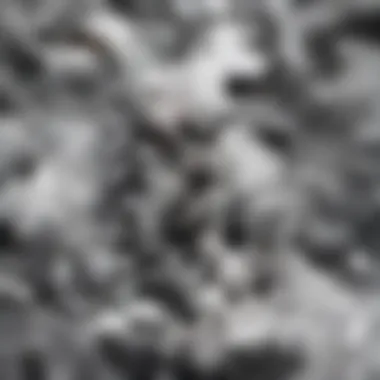
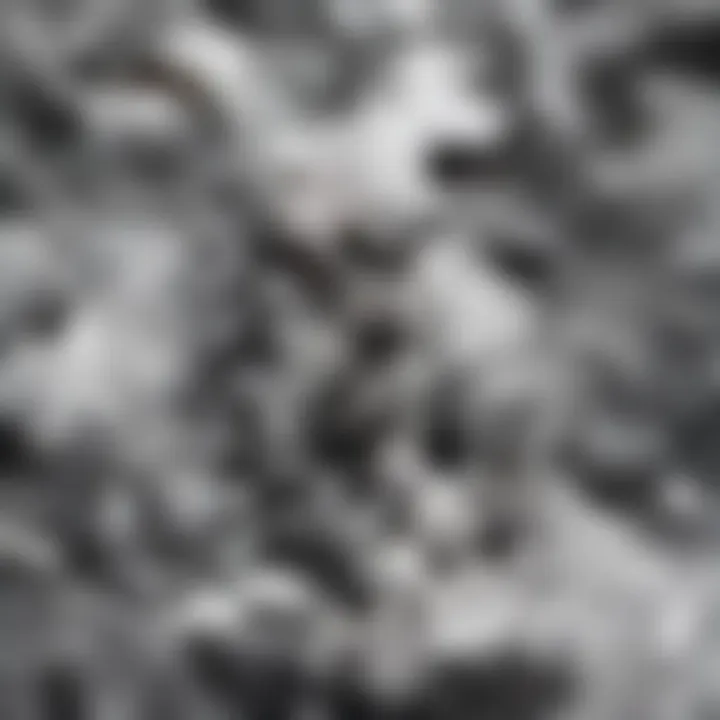
In electronics, the heat dissipation properties of aluminum are critical. Devices like laptops and gaming consoles often feature aluminum housings or heatsinks made from hardened aluminum alloys. This enhances thermal management and contributes to the overall performance of electronic devices.
The adaptability of hardened aluminum positions it as an essential material across multiple disciplines, showcasing its versatility and strength.
Challenges and Considerations in Aluminum Hardening
Understanding the challenges and considerations involved in aluminum hardening is crucial for anyone engaged in material science, engineering, or manufacturing. This section will explore the varying factors that impact the hardening process, focusing on both material limitations and environmental impacts. Addressing these concerns is vital for optimizing the performance of hardened aluminum and ensuring sustainable production practices.
Material Limitations
Aluminum alloys are known for their light weight and excellent corrosion resistance. However, they also come with certain limitations when it comes to hardening. One primary challenge is the inconsistency in material properties across different alloy types. Each aluminum alloy possesses unique characteristics which can influence the chosen hardening method. For example, not all alloys respond equally well to heat treatment.
Some alloys may not achieve desired strength levels due to inadequate hardening techniques or improper processing. Additionally, aging processes can lead to unwanted precipitate formation, which can negatively affect ductility. This makes it essential for engineers to select the appropriate alloy and hardening combination for specific applications.
Furthermore, hardening methods such as precipitation hardening and cold working can introduce residual stresses in the material. These stresses may lead to warping or distortion during machining or when subjected to service conditions. Hence, an understanding of alloy behavior under various hardening processes is critical for minimizing these effects.
Environmental Impacts
As industries push for sustainability, the environmental impacts of aluminum hardening processes cannot be overlooked. Many hardening methods, including anodizing and nitriding, require the use of chemicals that can potentially harm the environment. The disposal and management of these hazardous materials pose challenges for manufacturers aiming to adhere to regulations and reduce their ecological footprint.
Another concern relates to the energy consumption associated with heat treatments. High temperatures used in many aluminum hardening processes result in substantial energy usage, contributing to greenhouse gas emissions. Manufacturers are increasingly seeking to optimize these processes to reduce energy requirements. Implementing innovative technologies can help mitigate environmental impacts while maintaining or improving product performance.
"Sustainability in aluminum hardening is not just a regulatory challenge. It’s an opportunity for innovation that can lead to better products and processes."
Future Trends in Aluminum Hardening
The landscape of aluminum hardening is evolving rapidly. Understanding future trends in this area is crucial for leveraging new opportunities and addressing the emerging challenges. As industries increasingly adopt aluminum for its lightweight and strong characteristics, the methods to enhance its properties must also progress. This section aims to highlight significant future directions including advancements in material sciences and innovations in manufacturing techniques.
Advancements in Material Science
Material science plays a vital role in the continued evolution of aluminum hardening. Researchers are exploring new alloy compositions and microstructural changes to improve mechanical properties. For example, the development of high-entropy alloys represents a novel approach that combines multiple elements to increase strength and thermal resistance. Such materials are being tested for high-performance applications in the aerospace and automotive sectors.
The utilization of computational methods in material design is also gaining traction. Techniques like machine learning algorithms help predict how different alloying elements will interact at an atomic level. This predictive capability allows researchers to tailor aluminum alloys more effectively, optimizing performance before proceeding to manufacturing stages. Additionally, scientists are investigating nanostructured materials which can exhibit superior strength without compromising weight, potentially leading to significant breakthroughs in aluminum applications.
Innovations in Manufacturing Techniques
Manufacturing processes are adapting to accommodate the future needs of aluminum hardening. One such innovation is additive manufacturing or 3D printing using aluminum alloys. This method allows for the creation of complex geometries that were previously difficult or impossible to achieve with traditional methods. Advances in 3D printing technology can lead to reduced waste and enhanced material utilization, making production more efficient.
Furthermore, the integration of automated systems and digital technologies in manufacturing processes is facilitating precision in hardening techniques. Processes like laser treatment for surface hardening have been refined to provide more uniform and controllable outcomes. This negates the limitations of conventional methods, allowing for real-time adjustments based on the material properties observed during the hardening process.
End
The conclusion of this article emphasizes the significant role of hardening aluminum in enhancing its properties and suitability across various applications. With the increasing demand for lightweight yet strong materials, understanding the methods to harden aluminum becomes essential for scientists, engineers, and manufacturers. Through alloying, heat treatment, and other methods, aluminum's resilience can be improved, allowing it to meet the rigorous performance standards required in modern industries.
Understanding key insights such as the differences between various hardening techniques aids in selecting the ideal method for specific applications. Knowledge about the mechanical properties of hardened aluminum helps industries like aerospace and automotive to harness its advantages effectively, leading to innovations and improved product performance.
Summarizing Key Insights
The exploration of aluminum hardening reveals several critical insights:
- Variety of Methods: Different techniques including alloying, heat treatments, and surface hardening are available to enhance aluminum’s mechanical properties.
- Industry Applications: Hardened aluminum is vital in sectors such as aerospace, automotive, and construction, showcasing its versatility and relevance.
- Environmental Considerations: While hardening processes enhance material strength, they also require careful consideration of their environmental impacts and sustainability.
These insights reinforce the importance of aluminum hardening in engineering as it directly influences the safety, efficiency, and reliability of various products.
The Importance of Continued Research
Continued research in aluminum hardening methods is crucial. Advancements in material science pave the way for new techniques that are more efficient and environmentally friendly. Research efforts exploring:
- Innovative Alloys: The development of advanced aluminum alloys that offer superior properties can lead to breakthroughs in multiple industries.
- Sustainable Practices: Investigating the environmental aspects of hardening processes will help mitigate risks and improve sustainability in manufacturing.
Keeping pace with ongoing research ensures that industries utilize the most effective and sustainable methods to enhance aluminum properties, fostering technological growth while addressing environmental responsibilities.