High Speed Tool Steel: Properties, Applications and Innovations
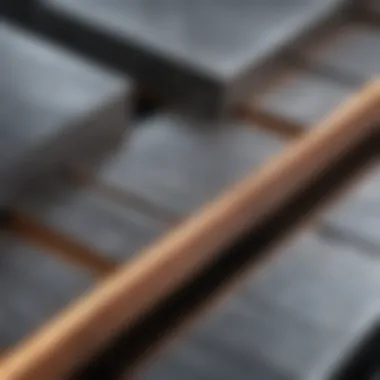
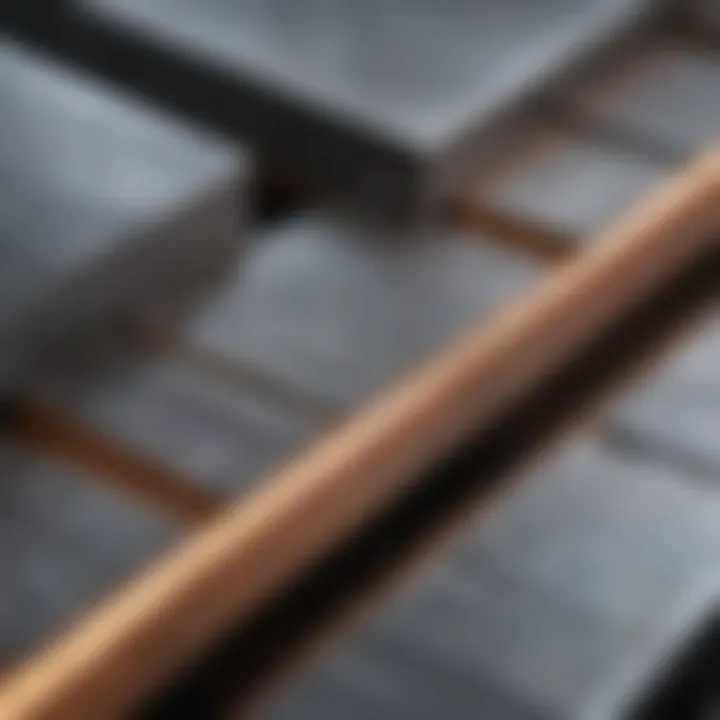
Intro
High-speed tool steel, a term carrying significant weight in the manufacturing and machining industries, plays a pivotal role in shaping modern technology. The unique characteristics of this alloy make it one of the preferred choices for various tooling applications. From drilling to milling, high-speed tool steels exhibit a balance of hardness, toughness, and wear resistance that caters to a range of industrial needs.
Understanding this material goes beyond surface knowledge; it dives deep into its composition, performance under stress, and the advancements that shape its future. In this discussion, we will explore essential aspects of high-speed tool steel, including its properties, applications, and recent innovations that signal exciting times ahead for manufacturers and engineers alike.
As we embark on this exploration, it’s crucial to acknowledge how the landscape of production is constantly evolving. This article seeks to provide a thorough examination, arming students, researchers, educators, and professionals with insights that will not only satisfy curiosity but also enhance practical knowledge. Let's begin by laying a foundation for our exploration.
Prolusion to High Speed Tool Steel
High speed tool steel is pivotal in today’s manufacturing landscape. Its unique properties enable the production of precision components across a variety of industries. In the realms of cutting and machining, high speed tool steel stands out as a material that can withstand extreme conditions, making it vital for maintaining efficiency and precision in production processes.
This section delves into the nuances of high speed tool steel, starting with a clear definition of what it embodies and why it’s significant. Understandably, its importance cannot be understated, as it shapes both the tools we use and the very fabric of manufacturing efficiency.
Definition and Importance
High speed tool steel is a subset of tool steels that are tailored to perform at elevated speeds. This is not just a matter of semantics; the definition encompasses the material's ability to retain hardness even under the high temperatures generated during fast machining operations. These steels are generally alloyed with elements such as tungsten, molybdenum, and chromium, which enhance their capabilities significantly. The importance lies not just in their performance but also in their widespread application in tools that shape metals and refractories at high velocities.
The ability of high speed tool steel to maintain cutting edges ensures that production lines run smoothly without frequent downtime for tool replacements or maintenance, which is a significant cost factor in many sectors. These steels contribute to increased productivity and quality, which are essential in a fiercely competitive market.
Historical Context
The development of high speed tool steel is rooted in a desire to push the boundaries of what was possible in metalworking. Originally, traditional carbon steels dominated tool production, but as the demand for efficiency rose, the advantages of alloying elements were recognized. In the early 20th century, the introduction of molybdenum and tungsten boosted the performance of tool steels remarkably, allowing them to maintain their hardness under stress and heat.
By the 1920s and 30s, manufacturers began to innovate deliberately, leading to the design of various high speed tool steel grades, each one tailored to specific applications. This progression marked a milestone in mechanical engineering, as it allowed industries to achieve faster production cycles with improved end products.
The rich history of high speed tool steel underscores a continuous evolution, where the materials have adapted in response to technological advancements and the ever-growing demands for efficiency and performance in industry. Today, this historical context serves as a foundation upon which the modern applications and innovations in high speed tool steel are built, making it a constant subject of study and enhancement.
Chemical Composition of High Speed Tool Steel
The chemical composition of high speed tool steel is crucial in molding its properties, which in turn define its effectiveness in various applications. Tool steel alloys are carefully designed mixes of different elements to enhance certain characteristics like hardness, wear resistance, and toughness. This section delves into the key alloying elements and their respective contributions, as well as shedding light on the microstructural features that arise from the unique combinations used in these steels.
Alloying Elements
Alloying elements play a pivotal role in determining the overall performance of high speed tool steels. Each element imparts specific characteristics, which can greatly affect the tool’s capability under high-speed machining conditions.
Molybdenum
Molybdenum is essential in high speed tool steels primarily for its ability to enhance hardness and toughness. It aids in stabilizing the carbide structure, which is vital for maintaining strength at elevated temperatures. This characteristic proves beneficial in high-speed machining applications where heat buildup can be significant. Molybdenum's unique feature is its high melting point, which allows tool steels to maintain performance even under harsh conditions. However, while it improves various mechanical properties, excessive molybdenum can lead to issues with toughness, making it necessary to achieve a balance in alloying.
Tungsten
Tungsten is another stalwart in the composition of these tool steels. One of its key attributes is its capacity to enhance hardness and wear resistance at elevated temperatures, aligning perfectly with the demands of high-speed operations. Concrete benefits derive from its ability to form hard carbides, which provide exceptional wear characteristics. Tungsten's robust presence in the alloy is what often allows tools to achieve longer service life. Yet, it’s worth noting that reliance on tungsten can create challenges in the fabrication process due to its cost and impact on hot workability.
Vanadium
Vanadium stands out for its contribution to refining the steel's microstructure, leading to improved toughness and wear resistance. It assists in controlling the size of the carbide particles that form during heat treatment, promoting a finer microstructure that ultimately enhances the overall durability of the tool. Vanadium’s unique feature lies in its effectiveness even at low concentrations; thus, it is often a welcomed addition to high speed tool steel formulations. However, too much vanadium can complicate weldability and may lead to brittleness if not managed with care.
Microstructure Analysis
Understanding the microstructure of high speed tool steel is fundamental for grasping how alloying elements manifest in the steel's performance. Two pivotal focus areas are martensite formation and carbide distribution.
Martensite Formation
Martensite is the primary phase that forms when high speed tool steel undergoes rapid cooling during quenching. This transformation is critical because the presence of martensite contributes directly to the hardness and wear resistance of the final product. A key characteristic of martensite is its needle-like crystal structure, which renders the material harder compared to other microstructural forms. The balance achieved during formation influences not just hardness but also impact strength. However, a high martensite content can lead to increased brittleness, making careful heat treatment vital to optimize performance.
Carbide Distribution
Carbides represent another critical component in the microstructural layout. They form when carbon reacts with alloying elements such as tungsten and molybdenum, creating hard particles that help the tool resist wear. The unique feature of carbide distribution is its relation to the machining properties; evenly distributed carbides typically result in improved fatigue resistance and effective cutting edge retention. Nevertheless, clustering can occur, which can negatively affect the toughness and overall performance of the tool. Hence, managing carbide distribution is essential for maximizing the advantages of high speed tool steels.
"The sophistication of alloying elements and the resulting microstructure ultimately define the potential of high speed tool steels in industrial applications."
By understanding the combination of these alloying elements—molybdenum, tungsten, and vanadium—along with the nuances of martensite formation and carbide distribution, one can appreciate the intricate balance that high speed tool steel strikes to excel in demanding environments.
Physical Properties of High Speed Tool Steel
Understanding the physical properties of high speed tool steel is crucial for anyone who engages with this versatile material. These properties play a pivotal role in how the tool steel performs during machining processes. Not only do they determine the efficiency of cutting operations, but also the longevity and quality of the tools produced. Let's take a closer look at some of the prominent characteristics that make high speed tool steel stand out in the industry.
Hardness and Wear Resistance
Hardness is one of the signature properties that define high speed tool steel. Often measured on the Rockwell scale, hardness indicates a material's resistance to deformation under load. High speed tool steel typically exhibits high hardness levels, generally around 60-67 HRC. This hardness is essential as it allows tools to maintain a sharp cutting edge, significantly reducing the frequency of tool changes during the machining process.
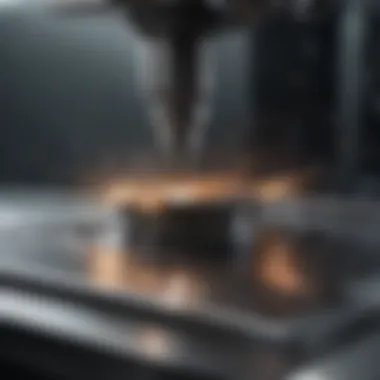
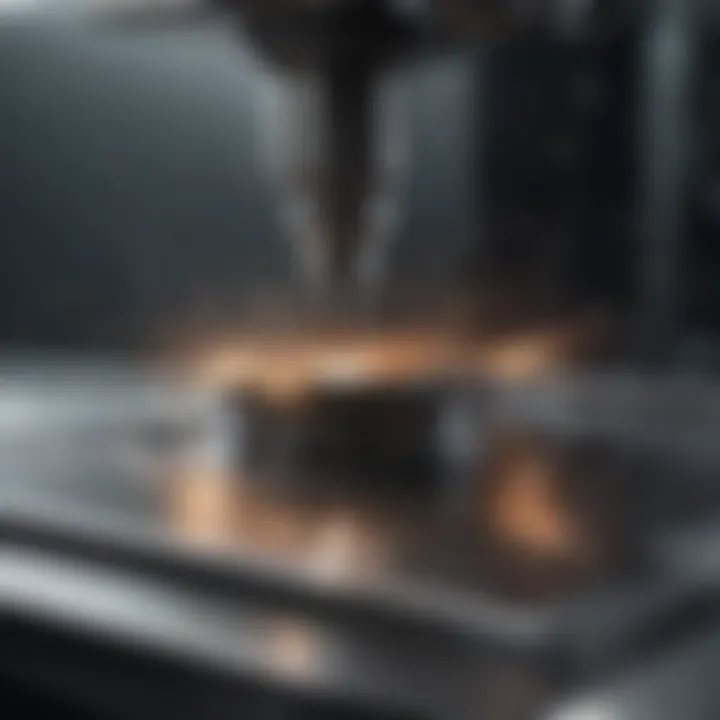
Wear resistance goes hand in hand with hardness. It refers to the ability of the tool to withstand the wear and tear that occurs during cutting operations. The composition of high speed tool steel, especially its alloying elements like tungsten and molybdenum, contributes to a microstructure that can resist wear better than many other material options.
"The key to longevity in tool life is not just how hard a material is, but how well it withstands wear and tear in practical applications."
Moreover, the high hardness and excellent wear resistance enhance productivity. Operators can achieve consistent performance, minimizing downtime that arises from tool replacements. As a result, industries ranging from aerospace to automotive reap the rewards of these properties, realizing significant savings on tool management and production timelines.
Toughness and Ductility
While hardness is undeniably important, we must also consider toughness and ductility. These properties relate to the material's ability to absorb energy and deform without breaking, respectively. High speed tool steels, despite their hardness, are designed with a balance in mind—too much hardness can lead to brittleness, which is not desirable in machining scenarios.
Toughness ensures that the tool can withstand shock loads—sudden, intense forces that can occur during machining processes. It’s like having your cake and eating it too; one wants a hard tool that doesn’t chip easily when faced with unexpected challenges. An optimal balance of toughness allows high speed tool steel to resist cracking and chipping under duress, which is essential when dealing with materials that might shift unexpectedly during machining.
Ductility is the property that lets the material change shape without breaking. High speed tool steels are designed to retain a level of ductility, enabling them to tolerate certain amounts of stress and strain, thereby ensuring that they do not fail catastrophically. This aspect is particularly critical in industries where precision is paramount, such as medical device manufacturing. The ability of the tools to withstand and absorb energy without failure enhances not just the tool’s life, but importantly, the quality of the final product as well.
In summary, the physical properties of high speed tool steel—namely, hardness, wear resistance, toughness, and ductility—work in concert to define its effectiveness in applied industrial settings. These characteristics not only validate its popularity but also underscore the complexities of selecting the appropriate tool steel for specific applications.
Thermal Properties and Heat Treatment
The significance of thermal properties and heat treatment in high speed tool steel cannot be overstated. These elements are critical as they determine how the material performs under demanding conditions. With high speed machining, the heat generated can impact tool life and efficiency. Understanding these properties leads to better tool design and improved performance in various applications.
Heat Treatment Processes
Annealing
Annealing is a thermal process that softens high speed tool steel, facilitating further machining and shaping. The main characteristic of annealing is its ability to relieve internal stresses and homogeneously distribute carbide structures within the steel. As a beneficial choice for many toolmakers, annealing enhances machinability. Its unique feature lies in the control over the microstructure; with proper annealing, the material can be prepped for hardening, improving toughness in the finished product. However, it comes with disadvantages, such as the need for precise temperature regulation. An improper annealing cycle may lead to non-uniform hardness, affecting overall performance.
Hardenability
Hardenability refers to how well a material can harden when subjected to heat treatment. The contribution of hardenability to high speed tool steel is pivotal, as it dictates the depth and uniformity of hardness achieved after quenching. A key characteristic of hardenability is its dependence on the chemical composition, particularly the alloying elements like chromium and molybdenum. This property makes it an appealing option for manufacturers who are looking for enhanced wear resistance. On the downside, achieving optimal hardenability can sometimes be tricky; too high of an alloy content can lead to increased brittleness. This trade-off must be carefully considered when developing high-performance tools.
Thermal Conductivity
Thermal conductivity is another crucial factor in tool steel. This property dictates how effectively heat travels through the material during machining. High thermal conductivity means heat generated at the cutting edge can be quickly dissipated, reducing the risk of overheating and extending tool life. However, there's a balance to be struck; while high thermal conductivity is desirable, it must not compromise the overall hardness and strength of the steel. The challenge lies in selecting the right alloying elements and heat treatment processes that optimize thermal conductivity without sacrificing other essential properties. Understanding these intricate relationships allows for the development of high speed tool steel that can withstand the rigors of advanced manufacturing.
In Summary: The interplay of thermal properties and heat treatment processes in high speed tool steel is fundamental in defining performance. Innovations in these areas have paved the way for the manufacture of cutting tools that meet the increasing demands of the industry.
Mechanics of High Speed Machining
Understanding the mechanics of high-speed machining is critical for anyone working with high-speed tool steel. This field addresses the forces, motions, and thermal interactions that define how tools perform when cutting materials at elevated speeds. High-speed machining isn't merely a speed game; it requires precision engineering and a keen appreciation of material behavior under stress.
Cutting Speed Dynamics
Cutting speed dynamics refers to the relation between the tool, the workpiece, and the cutting speed applied during machining. When you push the limits of speed, it leads to several intertwined effects that can enhance performance if approached correctly.
- Material Removal Rate: Higher cutting speeds generally improve the rate of material removal, making machining operations more efficient. Increased speeds can lead to a larger volume of metal removed per minute, greatly boosting productivity.
- Tool Wear: While speed is beneficial, it can be a double-edged sword. Tools experience accelerated wear with increased cutting speeds due to the increased heat generated. This can lead to shorter tool life and necessitate more frequent tool changes, which can offset the benefits gained from efficiency.
- Surface Finish: High-speed machining produces smoother finishes on workpieces. This is due to the constantly engaged cutting tool that interacts with the workpiece. A consistent cutting speed can minimize vibrations, leading to a refined surface quality with enhanced precision.
- Thermal Effects: The temperature generated during high-speed operations can be substantial, impacting both tool and workpiece materials. For instance, excessive temperatures can affect the properties of high-speed tool steels, changing their hardness and overall effectiveness. Understanding these thermal dynamics is vital for optimizing cutting speeds without compromising performance.
Striking the right balance in cutting speeds can be the difference between harnessing efficiency and encountering tool failure. Careful calibration and consideration of factors such as tool material, geometry, and workpiece properties play a crucial role here.
Chip Formation Mechanisms
Chip formation is the process by which material is removed from a workpiece during machining. The characteristics of chip formation significantly influence efficiency, surface finish, and the overall productivity of machining operations.
In the context of high-speed machining, understanding the following mechanisms is essential:
- Shear Mechanism: At high cutting speeds, chip formation often involves a shear mechanism. The higher speeds lead to less friction between the tool and the workpiece, resulting in cleaner cuts and more uniformly shaped chips. This mechanism reduces energy consumption during the process as less force is required.
- Chip Thickness: The thickness of chips generated can vary widely depending on the cutting conditions. Thinner chips may indicate a well-optimized process, as they suggest that the material is being removed efficiently without excessive force or heat generation. However, if chips become too thin, they can create challenges in chip removal and lead to issues with built-up edge formation on the tool.
- Nature of Chips: High-speed machining tends to produce short, helix-shaped chips. Their physical characteristics ease the transition from the cutting zone, leading to better thermal management. This aspect is essential as it can reduce the chances of chip re-cutting, which can cause additional wear on the tool.
In high-speed machining, understanding the interplay between cutting dynamics and chip formation is crucial, as it directly impacts efficiency, cost, and tool life.
By delving into the mechanics of cutting speed dynamics and chip formation mechanisms, manufacturers not only enhance productivity but also safeguard the integrity of their high-speed tool steel. Ultimately, these factors dictate the success of a machining operation under high-speed conditions, allowing for both quality and efficiency to flourish.
Applications in Various Industries
High speed tool steel has carved out a prominent niche across several key industries due to its exceptional qualities. This section delves into how different sectors utilize these materials to enhance precision, efficiency, and overall production performance. It’s not just about the tools themselves; it’s about what they enable—progress, innovation, and quality.
Aerospace
The aerospace industry is perhaps one of the most demanding fields when it comes to material selection. Here, high speed tool steels play a pivotal role. These steels are crucial for manufacturing components that need to withstand extreme pressures and temperatures. Aviation parts, such as turbine blades and shafts, require materials that are not only strong but also capable of enduring cyclical stress.
Key points include:
- Machining Precision: Components often have tight tolerances, meaning that high speed tool steels must deliver consistent results in complex shapes.
- Heat Resistance: The materials need to retain their properties even when exposed to high temperatures during operation.
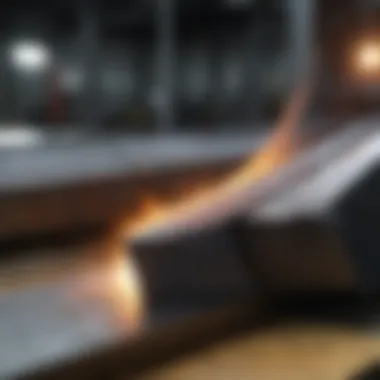
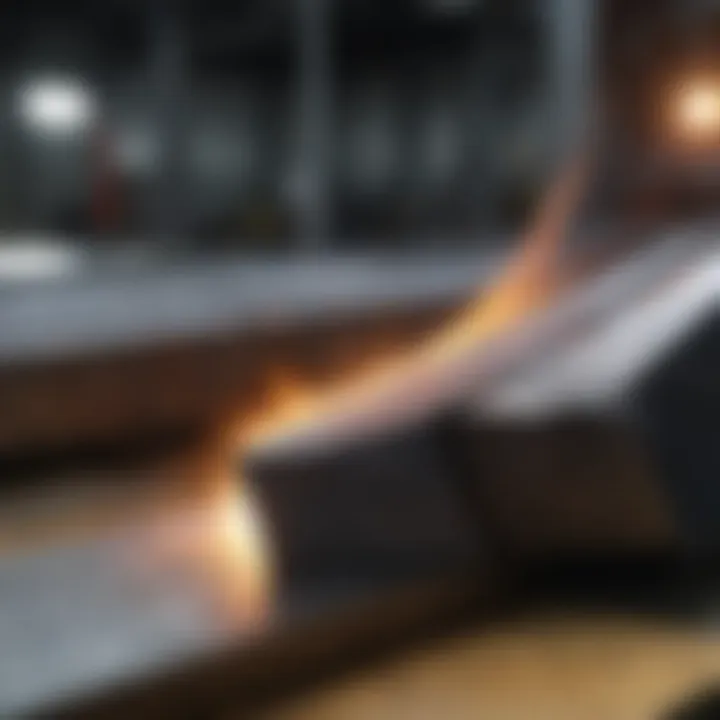
In summary, tool steels are fundamental in crafting reliable aircraft parts, which directly contribute to safety in air travel and the endurance of air vehicles.
Automotive
In the fast-paced automotive industry, the focus is centered on both efficiency and performance. High speed tool steels aid in manufacturing a variety of components, from engine parts to transmission systems. Their ability to maintain toughness while showcasing enhanced wear resistance is invaluable in this field.
Some considerations in automotive applications are:
- Cost Efficiency: With the right tool steel, manufacturers can reduce downtime caused by maintenance or tool changes.
- Versatility: Automotive components vary widely in design, meaning high speed tool steels must be versatile enough to handle different machining processes.
The result is a smoother production process that leads to higher-quality vehicles, contributing to a competitive edge in a crowded market.
Medical Devices
When it comes to medical devices, precision is non-negotiable. High speed tool steels are critical in producing surgical instruments, implants, and diagnostic equipment. In the medical field, stringent regulatory standards require materials that not only perform well but also are safe and reliable.
Points of significance include:
- Sterilization Compatibility: Components made from these steels must withstand multiple sterilization processes, without degrading in quality.
- Durability: Surgical tools need to maintain their sharpness and effectiveness over time, minimizing risks during procedures.
As such, high speed tool steels contribute significantly to advancements in medical technology, helping save lives and improve patient outcomes.
"The precision of tools utilized in the medical field can mean the difference between life and death. High speed tool steel ensures that these tools meet those demands."
In each of these sectors, high speed tool steel demonstrates an incredible adaptability that underscores its importance. Through enhancing production processes and ensuring the reliability of vital components, high speed tool steel is a game changer in modern manufacturing.
Advantages of High Speed Tool Steel
High speed tool steel holds a significant position in modern manufacturing. The material's unique characteristics cater to a variety of machining requirements, offering several advantages that enhance performance and sustainability in operations. This section delves into key advantages of high speed tool steel, focusing on its enhanced efficiency and cost-effectiveness.
Enhanced Efficiency
One of the standout features of high speed tool steel is its ability to maintain sharpness and precision at elevated temperatures. When it comes to cutting tools, this property results in better productivity in manufacturing environments. Unlike traditional tool steels that tend to soften under heat, high speed tool steel can withstand higher temperatures without a loss in performance. This allows for greater cutting speeds during machining operations.
"Using high speed tool steel can significantly cut down on production time and improve overall workflow."
Additionally, the material's microstructure, characterized by a fine distribution of hard carbides, contributes to improved wear resistance. This quality means that tools can endure longer periods of use before requiring replacements. Consequently, machinists experience fewer interruptions in their workflow, directly correlating to enhanced efficiency rates. Overall, its robustness permits longer runs and reduces the necessity for frequent tool changes.
Cost-Effectiveness
Cost effectiveness plays a vital role in the decision-making process for manufacturers. Although the initial investment for high speed tool steel can be higher than other options, the long-term savings generated from its use can be substantial.
The durability of high speed tool steel translates to a lower replacement rate over time. Simply put, these tools last longer, maintaining functionality even under rigorous conditions. When tools do not require frequent replacement, production costs substantially decrease.
Moreover, by enabling faster cutting speeds and minimizing downtime, high speed tool steel can contribute to a reduction in operational costs. The labor associated with tool changes, setup, and maintenance is decreased as well when using high speed tools due to their longevity.
In summary, the advantages of high speed tool steel, rooted in its efficiency and cost-effectiveness, are hard to overlook in a manufacturing landscape that demands precision and economical practices.
Challenges and Limitations
The discussion of challenges and limitations associated with high speed tool steel is pivotal to understanding its comprehensive impact in various industries. Being aware of these hurdles enables manufacturers and engineers to make educated decisions when selecting materials for specific applications. This section will delve into two prominent aspects: brittleness and failure mechanisms, along with the machinability issues that professionals often encounter. Through this exploration, insight will be gained into effective strategies for overcoming these challenges, ultimately enhancing the performance of high speed tool steel.
Brittleness and Failure Mechanisms
Brittleness in high speed tool steel can be a double-edged sword. While the material exhibits exceptional hardness and resistance to wear—a crucial trait in high-speed machining—it may also suffer from a lack of toughness. This brittle nature becomes a significant concern, particularly under conditions that subject the tool steel to unexpected stress or impact.
One major failure mechanism is catastrophic fracture, which refers to a sudden and complete failure of the material. Such a situation often arises from manufacturing flaws or improper heat treatment that leads to uneven microstructure. Therefore, careful monitoring during the production process is essential. To mitigate the risks of brittleness, the following considerations should be taken into account:
- Microstructural Integrity: Ensuring a uniform distribution of carbides can enhance toughness and reduce brittleness.
- Proper Heat Treatment: A well-planned heat treatment regimen can help optimize the properties of the tool steel.
- Use of Toughening Agents: Incorporating elements that promote toughness can prevent failures in high-stress scenarios.
To enhance performance, it is imperative to strike the right balance between hardness and toughness in high speed tool steel.
Machinability Issues
Machinability is a critical concern in the context of high speed tool steel, mainly because it's not always the simplest material to work with. The hardness that gives this steel its reputation can also make cutting, shaping, and finishing challenging. Factors affecting machinability include tool wear, cutting speed, and the choice of cutting fluids.
When machining high speed tool steel, a common issue is tool wear, which often results from excessive friction and temperature during cutting. Maintaining optimal cutting conditions can therefore be quite tricky. Key points to keep in mind regarding machinability include:
- Tool Selection: Using high-quality cutting tools designed specifically for high-speed applications can significantly improve performance. Materials such as carbide or ceramic are often preferred over conventional steels.
- Cutting Fluid Strategies: Utilizing effective cooling and lubrication can help minimize wear and prolong tool life. Proper fluid helps flush away chips and keep temperatures in check.
- Monitoring Cutting Parameters: Observing and adjusting feed rates and speeds is essential to ensure optimal machining.
As these issues illustrate, the challenges associated with high speed tool steel are multifaceted. However, with a fundamental understanding of its brittleness and machinability limitations, industry professionals can develop solutions that enable them to fully capitalize on the benefits of this advanced material.
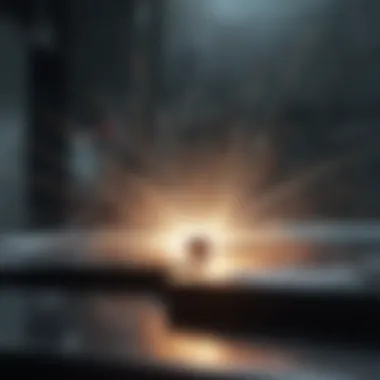
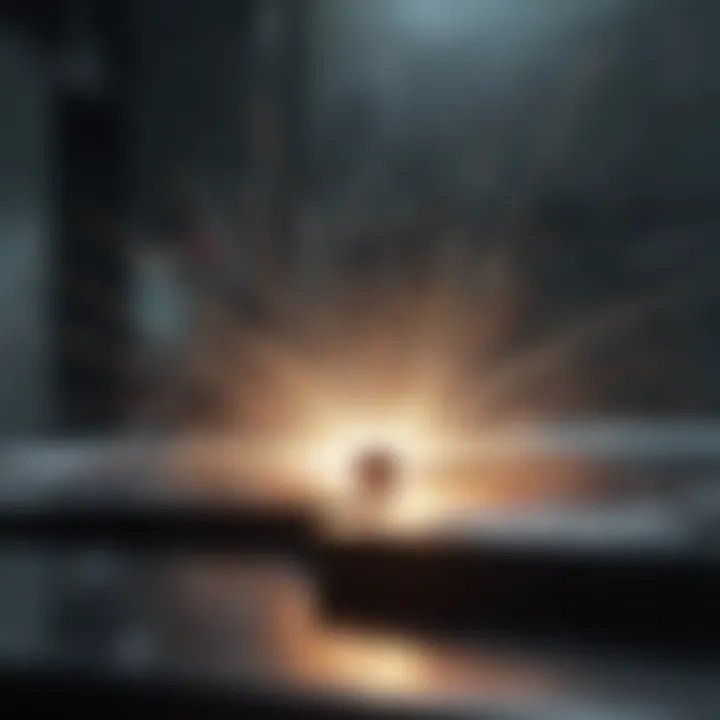
Recent Innovations in High Speed Tool Steel
In the ever-evolving landscape of manufacturing and metalworking, recent innovations in high speed tool steel have sparked considerable interest among engineers and technologists. The enhancement of tool performance, durability, and versatility stands at the forefront while addressing the contemporary demands of speed and efficiency. As industries push the envelope, new alloys and sophisticated heat treatment techniques are taking center stage, showcasing how vital innovation is to maintaining competitiveness.
Importance of Innovations
The significance of these developments can’t be overstated. Improved alloys not only extend tool lifespan but also excel in extreme conditions where earlier versions would falter. This makes them indispensable in industries such as aerospace and automotive, where precision is paramount. Furthermore, advancements in heat treatment enable these materials to withstand higher temperatures, leading to enhanced cutting speeds without compromising tool integrity.
"Innovation is the ability to see change as an opportunity—not a threat."
This philosophy rings true in the realm of high speed tool steel, where achieving more with less becomes the mantra for success.
New Alloys and Their Performance
Recent developments in alloys have introduced a range of new compositions tailored for improved performance. Notably, some manufacturers have focused on high cobalt contents in their formulations. This adjustment results in significantly better wear resistance, allowing tools made from these alloys to operate longer before needing replacement.
Utilizing elements like tungsten and molybdenum in conjunction with cobalt has led to promising results. Specific benefits include:
- Increased hardness: New alloys often boast hardness levels above traditional standards, enhancing performance under heavy loads.
- Enhanced thermal stability: This characteristic allows tools to maintain effectiveness at elevated temperatures, ensuring consistent results in various applications.
- Improved chip removal: The geometry of modern tool designs paired with these new alloys facilitates better chip evacuation, resulting in smoother processes and reduced cycle times.
These properties collectively contribute to operational efficiency, making new alloys not just an improvement but a game-changer in high speed machining.
Advancements in Heat Treatment Techniques
Alongside innovations in alloy compositions, advancements in heat treatment are reshaping how high speed tool steel is handled in production environments. Techniques such as cryogenic treatment have gained traction, where tools are subjected to extreme cold post-quenching. This process enhances the microstructure by refining carbide distributions and improving toughness.
Some key advancements include:
- Vacuum Heat Treatment: This process limits decarburization and oxidation, allowing for better control over the final properties of the steel. It supports finer grain structure, which translates to improved strength and performance.
- Aging Treatments: Some new methods involve controlled aging after the initial hardening phase, which provides additional toughness and resilience against wear.
The synergy between these approaches not only tailors tools to specific cutting conditions but also pushes the overall performance envelope further than before. By aligning chemical composition with treatment practices, manufacturers can create tools that adapt better to the rigors of modern machining demands.
In summary, the recent innovations in high speed tool steel, marked by new alloys and refined heat treatment techniques, are pivotal in driving the industry towards a new era of manufacturing excellence. The quest for enhanced performance continues to evolve, promising even greater advancements on the horizon.
Future Trends in Tool Steel Research
In recent years, the landscape of tool steel research has undergone significant transformations, primarily driven by the need for innovation and sustainable practices. Understanding future trends in high speed tool steel research is crucial as industries face mounting pressures to enhance productivity while reducing environmental footprints. The exploration into sustainability and advanced manufacturing technologies presents a golden opportunity for advancement in this vital sector.
Sustainability and Recycling
The quest for sustainability in tool steel production is becoming paramount. Traditionally, the manufacturing processes have raised concerns about resource consumption and waste generation. Now, researchers are focusing on developing processes that not only minimize material waste but also emphasize recycling. The use of reclaimed tool steels, for instance, is gaining traction as a means to produce new steel with equivalent properties.
- Benefits of Recycling: It lessens the need for raw materials, which can often be both expensive and environmentally taxing to extract. Furthermore, recycling high speed tool steel retains most of the desirable properties, making it a viable alternative in many applications.
- Advanced Recycling Techniques: Innovations like hydrometallurgical extraction processes allow for efficient recycling of critical alloying elements, such as tungsten and molybdenum. This kind of process not only reduces waste but also offers a significant cost advantage over acquiring virgin materials.
By prioritizing sustainability, manufacturers can contribute to a circular economy while still meeting high-performance criteria required in various applications
Integration with Advanced Manufacturing Technologies
The advent of advanced manufacturing technologies represents another exciting frontier in tool steel research. As industries evolve, the blend of high-speed tool steel with cutting-edge manufacturing processes offers promising avenues for enhanced performance.
- Additive Manufacturing: Techniques like 3D printing are reshaping the traditional paradigms of tool manufacturing. The ability to create complex geometries that were previously unachievable presents advantages such as reduced production time and material usage. Not only does this save valuable time but it also allows for customization in tool design, tailored specifically for unique applications.
- Smart Manufacturing: The integration of IoT devices in manufacturing environments leads to real-time data collection and analysis. This data-driven approach can significantly improve efficiency in the machining process. With sensors on machined tools, companies can track wear and tear, thus deciding when to replace or sharpen tools, optimizing operations.
This transition towards integrating advanced technologies represents a shift from traditional craftsmanship to a more intelligent, data-driven approach in tool steel applications.
In summary, the realm of high speed tool steel is on the brink of dramatic change, driven by sustainability imperatives and technological advancements. These evolving trends not only address the immediate needs of industries but also set a foundation for the long-term resilience of the sector. By staying alert to these developments, stakeholders can better position themselves to embrace the challenges and opportunities that lie ahead.
Culmination
In wrapping up our exploration of high speed tool steel, we gain a clearer insight into this remarkable material and what it represents in the realm of manufacturing. The journey through its properties, applications, and innovations emphasizes its paramount importance in enabling industries to achieve superior performance and quality in their machining processes.
Summary of Key Points
To distill the critical aspects of this article, a few key points must be reiterated:
- Properties: High speed tool steel exhibits exceptional hardness, wear resistance, and toughness, making it highly suitable for demanding machining tasks.
- Applications: Its versatility finds it a home in many industries, from aerospace to medical devices, each benefiting from the precision and durability that high speed tool steel offers.
- Innovations: Recent advancements in alloy compositions and heat treatment techniques have further enhanced its effectiveness, driving better performance in manufacturing.
- Future Trends: As industries aim for sustainability, high speed tool steel is increasingly seen through the lens of recyclability and integration with cutting-edge manufacturing technologies.
By summing up these points, readers can appreciate not just the technical specifications, but the broader implications that accompany the use of high speed tool steel in current and future manufacturing practices.
Implications for the Future
Looking ahead, the trajectory of research and innovation in high speed tool steel presents compelling opportunities. As environmental considerations become ever more pressing, the quest for sustainable production methods will likely steer the development toward greener alternatives and recycling processes that reduce waste. Furthermore, innovation in manufacturing technologies, such as 3D printing and additive manufacturing, could meld with the high-speed capabilities of this material, creating unimagined efficiencies.
"The future of high speed tool steel isn’t just about better performance; it’s about responsible progress."
Important Considerations
- Curation of Quality: It is critical to select references that are up-to-date and relevant. The field of metallurgy evolves rapidly, and only the latest studies can truly reflect the current state of high speed tool steel technologies.
- Diverse Sources: Relying on a mix of literature, including books, journal articles, and online resources like encyclopedias, enhances perspectives. Websites such as Wikipedia and Britannica can provide a great introductory understanding, while specialized journals will have in-depth research.
- Accessibility: Given the advanced nature of this topic, ensuring references are accessible to the audience is key. Many professionals may not have access to certain academic journals, so it's wise to include references that can be easily found online.
"Quality references are not just footnotes; they are the pillars upon which knowledge is built."