Optimizing TEC Heatsinks for Advanced Thermal Management
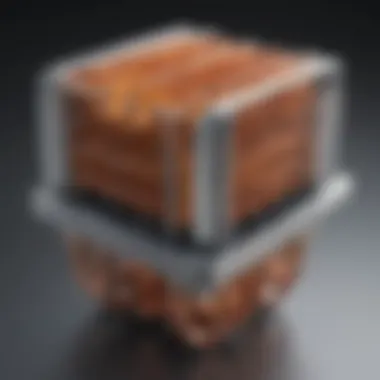
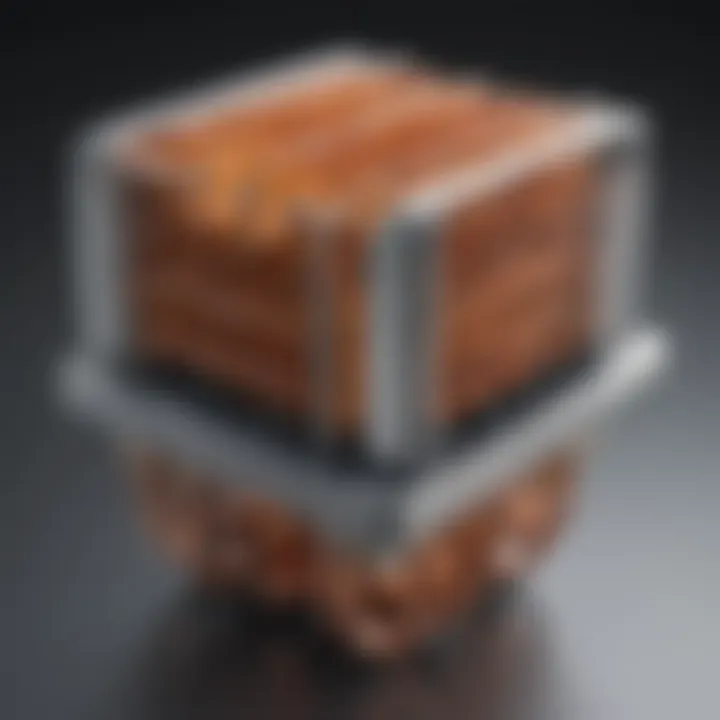
Intro
Thermal management plays a vital role in the performance and longevity of electronic devices. As electronics become more compact and powerful, the need for efficient cooling systems has intensified. One innovative solution that has emerged in this field is the use of Thermoelectric Cooler (TEC) heatsinks. These devices serve critical functions by transferring heat away from sensitive components, thereby ensuring optimal operational temperatures.
TEC heatsinks are often employed in various applications, from consumer electronics to industrial machinery. By understanding their design and function, stakeholders can improve device reliability and efficiency. This article will explore the intricacies of TEC heatsinks, including their materials, design principles, and innovative technologies that enhance thermal management.
Research Overview
Summary of Key Findings
The exploration of TEC heatsinks reveals several key findings:
- Effective Thermal Management: TEC heatsinks provide superior heat dissipation, crucial for high-performance electronics.
- Material Selection: The choice of materials impacts thermal conductivity and overall performance. Common materials include aluminum, copper, and specialized alloys that enhance thermal transfer.
- Innovations in Design: Advances in design, such as the implementation of microchannels and nanostructures, lead to enhanced heat transfer efficiency.
- Versatility of Applications: TEC heatsinks can be found in various environments, from consumer electronics to medical devices, demonstrating their wide-ranging applicability.
Background and Context
The need for effective thermal management dates back to the early days of electronics. As circuits became denser and more complex, the heat they generated increased significantly. Traditional cooling methods, such as fans and passive heatsinks, began to fall short of expectations in high-performance applications. TECs were developed as a solution to these limitations. Their ability to move heat using the Peltier effect allows for localized cooling, which is particularly beneficial in compact electronic systems where space is at a premium.
As electronic components evolve, so too do the demands placed on thermal management systems. In light of these challenges, TEC heatsinks have emerged as valuable tools for managing heat in both standard and extreme conditions.
Preamble to TEC Heatsinks
TEC heatsinks play a critical role in the field of thermal management, particularly in electronic systems. These components are essential in maintaining optimal operating temperatures for various devices, thereby enhancing their longevity and reliability. With rising demands for efficient cooling solutions in many industries, understanding TEC heatsinks is more relevant than ever.
Effective thermal management is crucial for preventing overheating and ensuring that electronic devices function efficiently. As devices become smaller and more complex, heat generation tends to increase significantly. A TEC heatsink helps dissipate this heat, keeping the components cool and functioning well.
This section explores the definition and purpose of TEC heatsinks, as well as a brief overview of their historical context in thermoelectric cooling. A well-designed TEC heatsink not only improves performance but also contributes to energy savings and overall system sustainability.
Definition and Purpose
A TEC heatsink consists of a thermoelectric cooler (TEC) and an associated heat dissipation structure. The primary purpose is to transfer heat away from sensitive electronic components. TECs operate using the Peltier effect, which enables them to absorb heat from one side and expel it through the other. This mechanism is essential in providing active cooling solutions where conventional methods may fall short.
The design of TEC heatsinks often varies based on the application and required cooling capacity. While some configurations operate silently, others incorporate fans to enhance airflow. These variances in design allow TEC heatsinks to be tailored for specific environments, improving their effectiveness in different scenarios.
History of Thermoelectric Cooling
The concept of thermoelectric cooling has roots in the early nineteenth century, with the discovery of the Peltier effect by Jean Charles Athanase Peltier in 1834. Researchers explored the potential for using electrical junctions to create cooling effects. This initial curiosity laid the groundwork for what would become a significant advancement in electronic cooling systems.
In the decades that followed, thermoelectric materials were developed, leading to more practical applications. Initially, these were primarily used in niche markets. However, as demand for more efficient thermal management solutions grew, thermoelectric cooling gained traction in various industries.
The evolution of TEC heatsinks reflects ongoing research and development in thermoelectric materials and design methodologies. Today, TECs are used not only in consumer electronics but also in industrial and medical applications, showcasing their versatility and effectiveness in diverse environments.
"Thermoelectric cooling harnesses the power of electricity to achieve cooling without moving parts, providing a longer life cycle and enhanced reliability."
Understanding both the definition and historical context of TEC heatsinks equips professionals and researchers with essential knowledge that underpins current advancements in thermal management technology. This insight is crucial as electronic devices continue to evolve in functionality and design.
Basic Principles of Thermoelectric Cooling
Understanding the basic principles of thermoelectric cooling is crucial when examining the functionality of TEC heatsinks in various applications. This section delves into the fundamental mechanisms that govern thermoelectric cooling, specifically the Peltier effect and heat transfer mechanisms. By grasping these principles, one can better appreciate the design and operational intricacies of TEC systems, which are essential for effective thermal management in electronics.
Peltier Effect Mechanism
The Peltier effect is a thermoelectric phenomenon where a temperature difference is created when an electric current flows through a junction of two different materials. This mechanism is the cornerstone of thermoelectric cooling. When the current passes through the junction, one side absorbs heat, while the other expels it. This temperature differential can be harnessed to cool electronic components, making it beneficial in applications such as portable coolers and computer cooling systems.
The efficiency of the Peltier effect is influenced by the choice of materials used in the thermoelectric modules. Some materials exhibit better thermoelectric properties than others, enhancing the effectiveness of the cooling process. Popular thermoelectric materials include bismuth telluride and lead telluride, known for their low thermal conductivity and high Seebeck coefficient. Understanding these materials' properties is vital for optimizing the design and performance of TEC heatsinks.
Heat Transfer Mechanisms

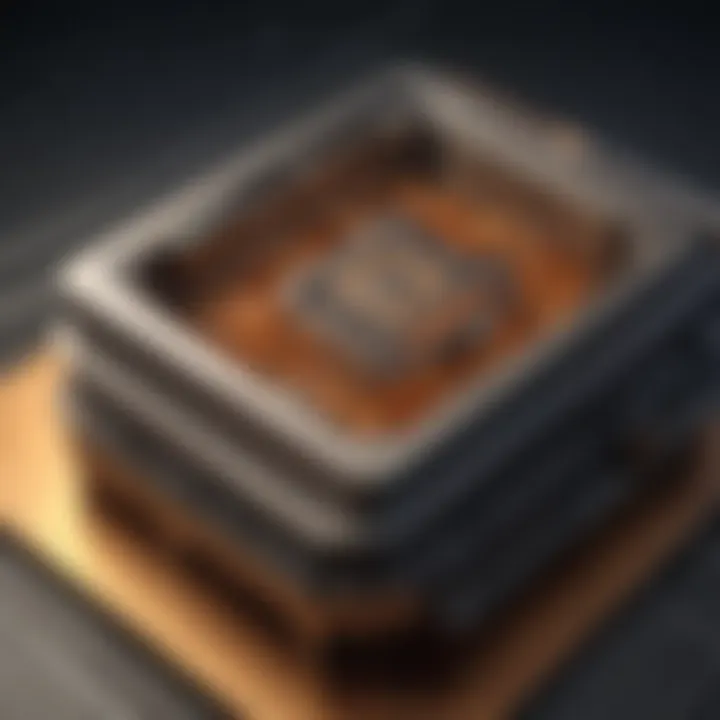
In addition to the Peltier effect, several heat transfer mechanisms play a significant role in the overall performance of TEC systems. These mechanisms include conduction, convection, and radiation.
- Conduction occurs when heat travels through solid materials. This takes place in the components of the TEC module and heatsink itself. The thermal conductivity of the materials can greatly affect the speed at which heat dissipates.
- Convection is the movement of heat through fluids (liquids or gases). Cooling fans are often employed to enhance convective heat transfer by promoting airflow over the heatsink, thus increasing heat dissipation efficiency.
- Radiation is the transfer of heat through electromagnetic waves. While it is less significant compared to conduction and convection in most TEC applications, it can play a role in specific environments.
Combining these heat transfer mechanisms with the Peltier effect allows TEC heatsinks to effectively manage heat in electronic devices. This interplay among various principles is what makes thermoelectric cooling a versatile solution in the quest for better thermal management. By deeply exploring these fundamentals, one can gain valuable insights into the optimal use and future advancements in TEC heatsink technology.
Components of a TEC Heatsink System
A thorough understanding of the components of a TEC heatsink system is crucial for anyone involved in the design and application of thermal management solutions in electronics. Each component plays a significant role in ensuring efficient heat dissipation and optimal performance.
Thermoelectric Modules
Thermoelectric modules are essential in TEC heatsink systems. These devices use the Peltier effect to transfer heat from one side to the other. The efficiency of a thermoelectric module is primarily determined by the quality of the thermoelectric materials used in its construction. Common materials include bismuth telluride and lead telluride.
The ability of these modules to create a temperature difference is crucial for effective cooling. Thus, it is essential to consider their specifications, such as maximum temperature difference and electrical resistance, when selecting a module for a specific application. Proper selection can enhance cooling performance and lower energy consumption.
Heat Exchangers
Heat exchangers complement thermoelectric modules by transferring heat away from the cooled components to the surrounding environment. Their design can vary, depending on the specific application needs. Effective heat exchangers maintain an optimal temperature, preventing overheating and improving system reliability.
When designing a heat exchanger, conductive and convective heat transfer properties are essential factors. Heat sinks made of materials like aluminum or copper offer good thermal conductivity. Also, larger surface areas of heat exchangers help increase the efficiency of the heat transfer process, maximizing cooling potential in compact electronic devices.
Cooling Fans and Additional Components
Cooling fans are integral in promoting airflow through the heatsink system. They enhance the cooling effect of the thermoelectric modules and dissipate heat from heat exchangers. Choosing the right fan involves considering factors like air flow rate, noise levels, and power consumption.
In addition, other components, such as thermal paste and mounting interfaces, also play a role in maximizing the thermal contact between the thermoelectric modules and the surfaces of the devices being cooled.
Overall, the synergy between these components is necessary for effective thermal management. Understanding each element’s function helps in creating a cohesive and high-performing TEC heatsink system.
Material Considerations in TEC Heatsink Design
The selection of materials in the design of TEC heatsinks plays a crucial role in ensuring effective thermal management. The materials must meet specific performance requirements to promote heat transfer, enhance durability, and withstand various environmental conditions. Factors such as thermal conductivity, electrical insulation, and mechanical strength must be accounted for during the design process. This section will explore the types of materials involved and their implications for TEC heatsink efficiency and reliability.
Thermoelectric Materials
Thermoelectric materials are at the heart of thermoelectric cooling systems. These materials are designed to exploit the Peltier effect, allowing for effective heat exchange. The efficiency of a TEC heatsink significantly depends on the characteristics of these thermoelectric materials. Commonly used thermoelectric materials include bismuth telluride, lead telluride, and skutterudites. Each material presents unique benefits:
- Bismuth Telluride: This is widely used in commercial applications due to its relatively high efficiency at room temperature. It shows a good balance between thermal conductivity and electrical conductivity.
- Lead Telluride: This material is used in higher temperature applications, where it can deliver better performance than Bismuth Telluride.
- Skutterudites: These are promising for advanced applications due to their tunable properties, allowing enhancements in thermoelectric performance through alloying.
Enhancements in these materials, such as doping and nanostructuring, can further improve their efficiency. As a consequence, significant research is ongoing to discover new thermoelectric materials that can offer better performance and lower costs.
Conductive and Insulative Materials
The choice of conductive and insulative materials is critical in ensuring the overall efficiency and effectiveness of TEC heatsinks. Conductive materials facilitate heat transfer from the electronic components to the coolant medium, while insulative materials prevent unwanted heat loss and protect sensitive components.
- Conductive Materials: Commonly, metals like copper and aluminum are preferred for their high thermal conductivity. Copper is known for its superior performance, while aluminum is valued for its lighter weight and corrosion resistance. Selecting the appropriate metal involves balancing cost, weight, and thermal performance needs.
- Insulative Materials: Materials such as ceramic and certain polymers are essential for optimal thermal management. They serve to insulate the thermoelectric modules from heat sources, preventing thermal shorts. Selecting high-quality insulative materials is even more important in applications where maintaining stable thermal profiles is critical.
Performance Metrics of TEC Heatsinks
Performance metrics of TEC heatsinks are crucial because they provide a quantitative understanding of how effective these systems are at managing heat. Understanding these metrics helps in designing efficient thermal management systems for a variety of applications. The most notable performance metrics to consider include the Coefficient of Performance, Thermal Resistance, and Electrical Efficiency. Each of these metrics has significant implications not just for operation, but also for the longevity and reliability of electronic devices.
Coefficient of Performance (COP)
The Coefficient of Performance (COP) is a primary metric in evaluating the efficiency of thermoelectric cooling systems. COP is defined as the ratio of heat removed from the cold side to the electrical power consumed at the hot side. A high COP indicates that a TEC heatsink is efficient, meaning it removes a substantial amount of heat while using a minimal amount of energy.
For effective thermal management, targeting a COP that meets or exceeds industry standards is essential.
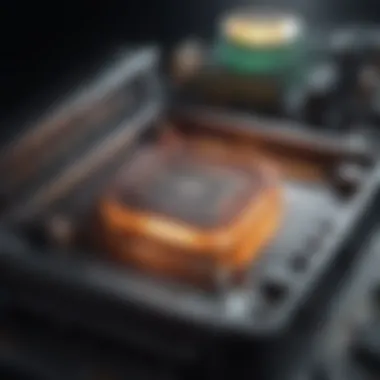
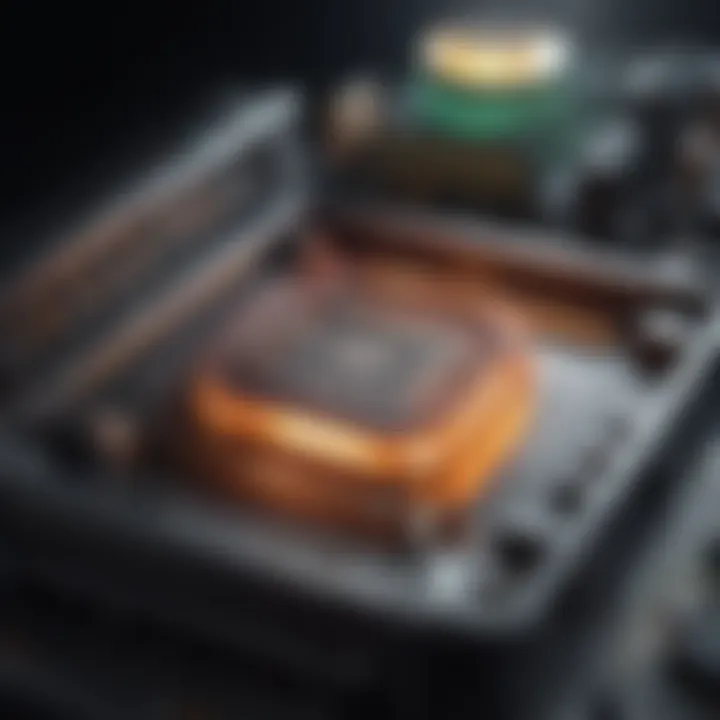
Suboptimal COP values can lead to higher energy costs and overheating issues, ultimately affecting device performance. In applications where energy efficiency is paramount, like portable electronics, a higher COP can significantly enhance overall device usability.
Thermal Resistance
Thermal resistance is another critical factor in the performance metrics of TEC heatsinks. It is defined as the measure of a material’s resistance to the flow of heat. Lower thermal resistance indicates that heat is dissipated more effectively, making the heatsink more efficient. This metric plays a significant role in determining how well a TEC heatsink can manage heat transfer between the thermoelectric module and ambient environment.
A variation in design can influence thermal resistance. Materials selected for construction, the geometry of the heatsink, and air circulation dynamics are all factors that affect this metric. Assessing thermal resistance is not just about being conductive; it also involves understanding how heat dissipates in real-world applications. For instance, the efficiency of fan integration in a TEC heatsink can heavily influence overall thermal performance.
Electrical Efficiency
Electrical efficiency is an additional performance metric that should not be overlooked. It deals with how well the electrical energy supplied to the thermoelectric module translates into cooling power. High electrical efficiency implies that a majority of the input energy contributes to effective cooling rather than being lost as waste energy.
Maximizing electrical efficiency is particularly important in compact devices where space is at a premium. Devices like laptops and smartphones benefit from technologies that optimize this efficiency, reducing heat production and prolonging device lifespan.
Applications of TEC Heatsinks
The applications of Thermoelectric Cooler (TEC) heatsinks are crucial in modern electronic systems. Their ability to effectively manage thermal energy for various devices enhances performance and longevity. Different sectors utilize TEC heatsinks, significantly impacting efficiency and functionality. Understanding these applications helps in optimizing designs and selections in different environments.
Consumer Electronics
In the consumer electronics sector, TEC heatsinks are found in devices like computers, gaming consoles, and smartphones. The primary function is to regulate temperatures and prevent components from overheating. With demanding processors and graphics cards, maintaining optimal thermal conditions is essential.
TEC heatsinks enhance product reliability. By reducing heat build-up, they prolong the lifespan of sensitive components. Moreover, efficient thermal management enables devices to perform better, allowing for higher processing speeds and improved user experience. The integration of TEC technology leads to quieter systems, as passive cooling can be complemented by thermoelectric solutions.
Industrial Systems
Industrial systems often face rigorous operating conditions, where thermal management is critical. TEC heatsinks are employed in machinery, control systems, and robotics to safeguard components from thermal damage. In production lines, overheating can lead to breakdowns, affecting efficiency.
The adaptability of TEC technologies allows industries to implement tailored solutions. For instance, specific modules can be customized to meet the heat dissipation needs of various equipment. Improved thermal control translates to better performance of industrial systems. It can lead to increased output and reduced operational costs. Additionally, TEC heatsinks can work efficiently in a range of environments, making them suitable for diverse industrial applications.
Medical Devices
In the medical field, TEC heatsinks play a vital role in devices such as MRI machines and diagnostic tools. Their ability to maintain precise temperatures is critical for ensuring optimal functionality. Overheating in medical devices can compromise performance or even introduce errors in diagnostics.
The reliability of TEC heatsinks in medical equipment means improved patient outcomes. For example, in surgical instruments that depend on specific thermal conditions, TEC can prevent overheating during prolonged procedures. The safety and efficacy of medications stored and monitored through this technology are also enhanced, emphasizing its importance in medical applications.
"TEC heatsinks not only protect electronic components from heat but also ensure the reliability and longevity of devices across various sectors."
Challenges Faced by TEC Heatsink Technologies
Heat Dissipation Efficiency
Heat dissipation efficiency is a critical aspect of TEC heatsink technologies. The very purpose of these systems is to manage heat generated by electronic components effectively. If a TEC heatsink cannot dissipate heat efficiently, the entire cooling system may fail to function as intended. This situation can lead to overheating of electronic devices, causing decreased performance and potential damage.
One key factor affecting heat dissipation is airflow. Insufficient airflow around the heatsink can impede heat transfer, resulting in the buildup of heat. Additionally, the design of the heatsink itself influences efficiency. A heatsink with optimized fin designs enhances surface area, allowing for better heat exchange with the surrounding air. Furthermore, if the thermal interface material (TIM) used is substandard, it can create thermal resistance that obstructs the flow of heat from the electronic component to the heatsink.
"Efficient heat dissipation is not just about material; it's also about geometry and placement within an electronic assembly."
Moreover, operating conditions also play a role. Environmental factors such as ambient temperature can impact the performance of TEC heatsinks. Higher ambient temperatures reduce the effectiveness of the heat dissipation process. To achieve optimal thermal management, engineers must consider these variables in the design phase.
Material Limitations
Material limitations present another significant challenge in TEC heatsink technologies. The materials chosen for the heatsinks must exhibit excellent thermal conductivity to maximize heat transfer. Copper is often favored for its high thermal conductivity; however, it can be heavier and more expensive compared to alternatives like aluminum.
Aluminum, on the other hand, offers a good compromise between weight, cost, and thermal conductivity but may not match copper’s performance entirely. This trade-off necessitates careful material selection based on the specific application and expected performance metrics.
In addition, the thermal expansion characteristics of these materials should be in tune with the components they serve. A significant difference in thermal expansion can lead to mechanical stress and potential failure over time.
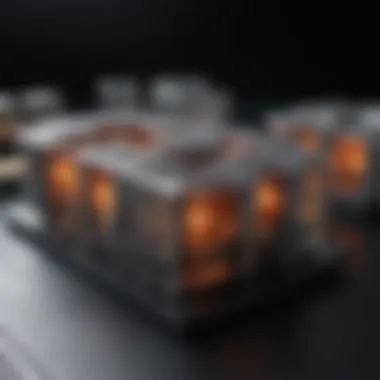
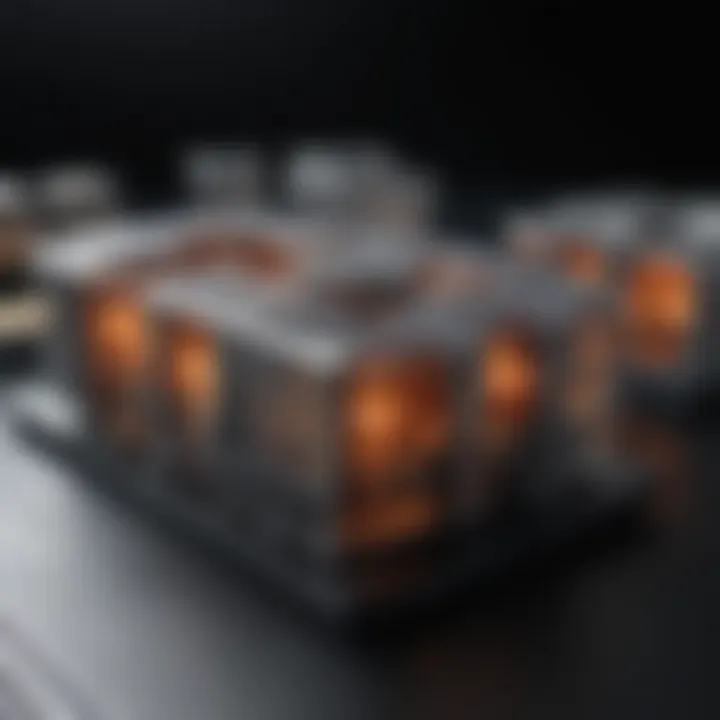
Lastly, advancements in materials science are ongoing, yet many emerging materials are still in research phases. The transition from theoretical potential to practical application can take time. Engineers must keep up with these advancements while also assessing their compatibility with existing systems and standards.
Advancements in TEC Heatsink Technology
The realm of TEC heatsink technology is evolving rapidly, driven by the need for improved thermal management in electronics. These advancements are critical as they directly influence the performance, durability, and efficiency of electronic systems. As technology progresses, it becomes increasingly important to incorporate innovations that can handle the growing thermal challenges in modern devices. This section will delve into two significant aspects of advancements in this area: emerging materials and innovative designs.
Emerging Materials
In the search for enhanced thermal management, the choice of materials used in TEC heatsinks is paramount. Recent advances have revealed a range of new materials that can significantly improve performance. For instance, materials such as graphene and carbon nanotubes demonstrate exceptional thermal conductivity. Their use not only increases heat dissipation efficiency but also contributes to reduced overall weight, a crucial factor in portable electronics.
Another notable development is the incorporation of bimetallic compounds. These materials possess unique properties that allow for better thermal conductivity and mechanical stability. The synergy between different metals can yield a composite that outperforms traditional single-material heatsinks.
Moreover, advancements in manufacturing techniques, such as 3D printing, are enabling the creation of complex geometries that optimize heat flow. This opens new possibilities for customized designs tailored to specific applications.
"The integration of advanced materials in TEC heatsinks paves the way for more efficient electronic devices."
The continuous exploration of thermoelectric materials also plays a significant role in improving the efficiency of TEC systems. Researchers are focused on discovering new alloys and compounds that can enhance the Peltier effect, which is fundamental to the operation of TECs.
Innovative Designs
Design innovation is equally crucial in the evolution of TEC heatsinks. As electronic devices shrink, the need for compact yet efficient cooling solutions becomes urgent. One significant trend is modular design, which allows for flexibility in thermal management across different systems. A modular approach enables the easy replacement or upgrade of individual components without overhauling the entire cooling system.
Furthermore, the integration of passive and active cooling strategies has emerged as a prominent design consideration. By combining natural convection with forced air cooling, designers can achieve better cooling performance while minimizing energy consumption. This hybrid approach optimizes heat dissipation in various operational environments.
Adopting fin designs and heat pipes in heatsink configurations is another innovation enhancing thermal performance. These techniques amplify surface area, enhancing the cooling capacity and allowing for better airflow, which is essential in high-heat applications.
Lastly, computational fluid dynamics (CFD) simulation plays a vital part in the design phase. By accurately modeling heat transfer and airflow, engineers can fine-tune heatsink designs before manufacturing, leading to more efficient and effective cooling solutions in final products.
Future Trends in TEC Heatsink Applications
Understanding the future trends in TEC heatsink applications is crucial for maintaining competitiveness in various fields, particularly electronics. As technology evolves, the demand for more efficient thermal management systems grows. The ability to manage heat effectively directly impacts the performance, reliability, and lifespan of electronic devices. TEC heatsinks, due to their unique cooling properties, are becoming more integrated into advanced systems. The potential for leveraging these technologies can lead to significant advancements in thermal management.
Integration with Renewable Energy Sources
The integration of TEC heatsinks with renewable energy sources is a crucial future trend. With the global push for sustainability, there is an increased focus on using renewable energy in various applications, including thermal management. TEC systems can play a vital role in solar-powered applications, where excess heat needs to be managed efficiently.
By combining TEC heatsinks with solar panels, it is possible to enhance the efficiency of energy conversion. For example, when solar panels operate at lower temperatures, their energy conversion efficiency improves significantly. This requires an effective mechanism to remove excess heat.
Key Benefits:
- Sustainability: Utilizing TEC heatsinks with renewable sources reduces reliance on traditional, non-renewable energy.
- Efficiency: Improved thermal management results in higher efficiency rates for solar panels or wind turbines.
- Versatility: TEC heatsinks can be adapted to various renewable systems, making them flexible for different applications.
Advancements in Miniaturization
Another notable trend is the continuous advancements in miniaturization of TEC heatsinks. As electronic devices become smaller, there is a pressing need for thermal management solutions that can fit within compact spaces while still delivering high performance.
This focus on miniaturization means that manufacturers are developing new designs and materials to create more efficient TEC heatsinks that occupy less space. Smaller devices, ranging from smartphones to medical instruments, require sophisticated cooling solutions.
Considerations:
- Performance vs Size: Maintaining high performance in a smaller form factor is challenging and requires innovative design techniques.
- Heat Dissipation: As devices shrink, efficient heat dissipation becomes vital to avoid overheating and device failure.
- Cost Efficiency: Producing compact heatsinks can lead to cost reductions in manufacturing since they use less material.
"The future of TEC technology lies in its ability to adapt to the needs of smaller, more efficient electronic systems while contributing to sustainable energy efforts."
Finale
The conclusion of this article emphasizes the critical role of TEC heatsinks in the thermal management of electronic devices. As technology continues to advance, the demand for efficient cooling solutions becomes paramount. TEC heatsinks are an essential component in achieving optimal performance in a wide range of applications, from consumer electronics to industrial systems.
Summary of Key Points
- Importance of Thermal Management: Effective thermal management ensures the longevity and reliability of electronic devices, preventing overheating and failure. TEC heatsinks play a pivotal role in this by efficiently transferring heat away from components.
- Versatility of Applications: TEC heatsinks have diverse applications, catering to industries such as consumer electronics, medical devices, and industrial systems. Each of these sectors benefits from controlled thermal environments.
- Material Considerations: The choice of thermoelectric materials and conductive components influences the overall efficiency and performance of TEC heatsinks. The right materials enhance heat dissipation and overall functionality.
- Advancements in Technology: Recent innovations in material science and design have propelled TEC heatsinks toward new frontiers, allowing for greater integration with renewable energy sources and miniaturization of devices.
Final Thoughts on TEC Heatsinks
In summary, TEC heatsinks are indispensable for maintaining thermal control in a rapidly evolving technological landscape. They not only enhance the performance of electronics but also contribute to sustainability by supporting energy-efficient solutions. Looking forward, advancements in TEC technology will likely lead to even more sophisticated heating and cooling strategies, aligning with the broader goals of energy conservation and efficiency in electronic device design. As we explore these paths, understanding the various aspects of TEC heatsinks becomes ever more crucial for students, researchers, and professionals alike.