Science and Applications of Spray Drying Oil

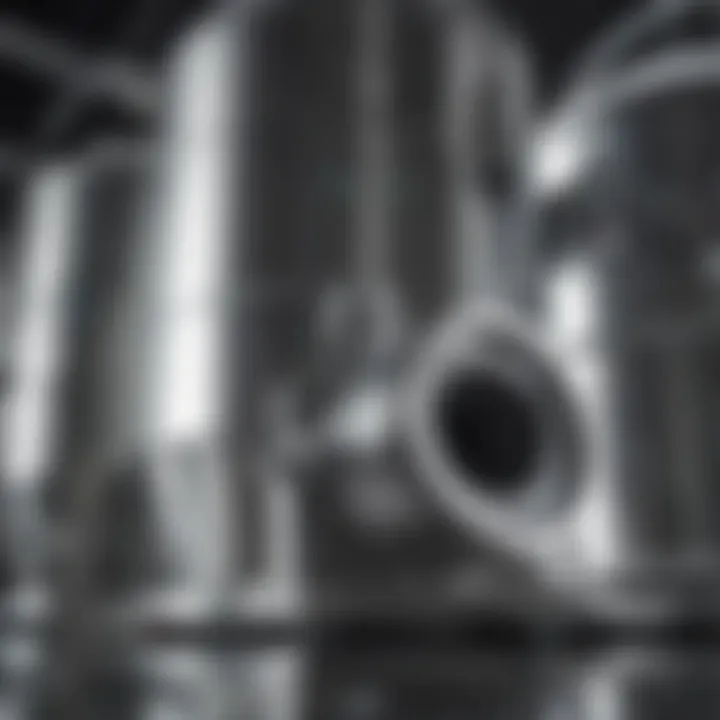
Intro
Spray drying is a method that many people might overlook, yet it plays a vital role in various industries, particularly when it comes to oil processing. This technique involves turning liquid into powder, creating formats that are both stable and easy to handle. The process is essential for a variety of applications—from enhancing flavors in food products to ensuring the stability of active ingredients in pharmaceuticals and cosmetics. Understanding this technology opens up a world of possibilities, helping industries meet consumer demands in a more efficient manner.
Research Overview
In this section, we will summarize key findings in the realm of spray drying oils, setting the stage for a detailed exploration of its applications. The existing literature reveals the transformative impact of spray drying on the oil industry, shedding light on its versatility and efficiency. Here, we'll touch on some pivotal aspects of the technology.
Summary of Key Findings
One of the standout findings in recent studies is how spray-dried oils maintain their functional characteristics while enhancing their shelf-life. A range of oils including essential oils, edible oils, and specialty oils have been successfully transformed using this method. This not only preserves their nutritional benefits but also mitigates oxidation and degradation, which is often a significant challenge in oil storage.
Moreover, the integration of spray-drying techniques in product formulation has been shown to yield innovative solutions, enabling the incorporation of oils that might otherwise be too volatile or sensitive to heat.
Background and Context
Historically, spray drying began to gain traction in the mid-20th century, primarily in the dairy industry. Over the years, however, its applicability has broadened dramatically. Initially, the focus was on milk powder; today, the approach has expanded to encompass oils, flavors, and even polymers. Each sector has adapted the technique to its specific needs, resulting in a rich diversity of applications driven by the need for better preservation and formulation.
Methodology
With the considerable advancements in technology, the methodologies employed in spray drying have evolved too. Here’s a deeper look into how spray drying is presently approached in research and industry.
Experimental Design
The design of experiments in spray drying involves a thorough understanding of the interactions between various parameters such as temperature, feed rate, and atomization method. A common approach includes the systematic variation of these factors to evaluate their effects on the properties of the dried product. This ensures not only quality outputs but also an optimized process that can be replicated at scale.
Data Collection Techniques
When it comes to gathering data, several techniques dominate the field. For instance, spectral analysis techniques help in identifying the chemical composition of oils before and after spray drying. Additionally, physical property assessments such as moisture content and particle size distribution are routinely measured to ensure compliance with industry standards.
"Spray drying is not just a processing technique; it is a pivotal innovation that has reshaped our approach to oil handling and application."
Prelude to Spray Drying
Spray drying is not just another method in the world of food technology, pharmaceuticals, and cosmetics; it is a game changer. The process transforms liquid into powder form, a feat that holds significant importance across various sectors. The rise of consumers looking for shelf-stable products has highlighted the need for effective techniques like spray drying. This method aids in improving product longevity, enhancing flavor profiles, and refining textures, making it crucial for manufacturers and consumers alike.
Understanding the principles of spray drying can illuminate its wide range of benefits. For instance, it allows for uniform particle size, which can greatly influence how products are processed and perceived by consumers. Moreover, it minimizes the degradation of sensitive compounds, ensuring that the nutritional and functional properties of oils are preserved effectively.
While the advantages are significant, there are considerations to keep in mind as well. Different oils have varying characteristics that determine their suitability for spray drying. Each industry, with its unique requirements, must weigh the potential benefits against these factors. Such insights pave the way for improved formulations and innovative applications in sectors ranging from food to pharmaceuticals.
In a nutshell, the significance of spray drying oil transcends mere production technique; it plays a vital role in shaping the future of product development. By diving deep into the aspects of this process, we can appreciate the nuances that make spray drying an invaluable tool in modern manufacturing.
Fundamental Principles of Spray Drying
Understanding the fundamental principles of spray drying is crucial, particularly in terms of how this technology fits into the broader landscape of food, pharmaceutical, and cosmetic production. To put it simply, spray drying transforms liquids into powders by atomizing the liquid and rapidly evaporating the solvent. This seemingly straightforward process hinges on intricate thermodynamics and fluid dynamics that ultimately influence the quality of the final product.
The harmony of these principles contributes positively to efficiency, product consistency, and shelf stability. By gaining insight into these core elements, industry professionals can enhance their applications of spray drying, tailoring their processes to meet specific requirements and challenges.
Thermodynamic Principles
Thermodynamics serves as the backbone of spray drying, dictating how moisture is evaporated from the product. The process fundamentally relies on heat transfer, where energy from hot air or gas is transferred to the liquid droplets. When the droplets are atomized, they have an increased surface area, which promotes faster evaporation of the solvent. The following aspects highlight the significance of thermodynamics in the spray drying process:
- Heat Transfer: Efficient heat transfer is vital. The temperature of the drying air and its relative humidity directly affect the rate of moisture removal. To achieve optimal drying conditions, one must carefully balance these variables.
- Latent Heat of Vaporization: The energy required to change from liquid to gas, termed latent heat, is a critical factor. It affects how quickly a droplet can lose its moisture during the drying process.
- Heat Recovery Systems: Implementing heat recovery systems can significantly enhance energy efficiency, minimizing operational costs. Capturing waste heat and reusing it for preheating air is a practice that’s becoming more common.
Understanding these thermodynamical principles offers operators the knowledge they need to manipulate conditions effectively, tailoring their approach to various oil types.
Fluid Dynamics in Spray Drying
Fluid dynamics covers how the liquid behaves when atomized and how these droplets interact with the drying medium. The characteristics of droplet size, velocity, and the prevailing flow patterns are paramount in achieving the desired outcomes. Here are some key elements:
- Droplet Size Distribution: Smaller droplets evaporate faster than larger ones. Each product may require a specific droplet size for optimal drying, which can be controlled through the nozzle design and operating pressure. This consistency ensures uniform drying and quality.
- Flow Patterns: The arrangement of airflow in the drying chamber can significantly impact drying efficiency. Co-current and countercurrent flow arrangements—where the hot air flows in the same or opposite direction to the droplets, respectively—each present unique advantages and challenges that influence the overall drying capacity and energy use.
- Cascade Effect: As droplets fall through the drying chamber, they can collide and coalesce. Managing the droplet collision rate is essential to avoid larger sizes in the final product, which can lead to uneven drying and undesirable textures in the powder.
By examining these fluid dynamic considerations, professionals can optimize their spray drying processes, adjusting parameters to achieve a high-quality product that meets the specific needs of their application.
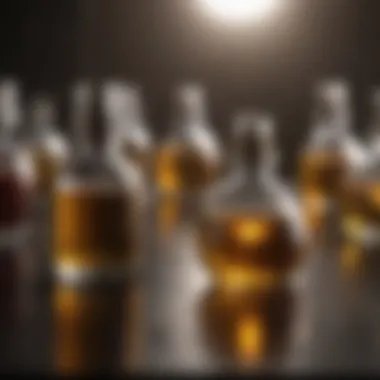
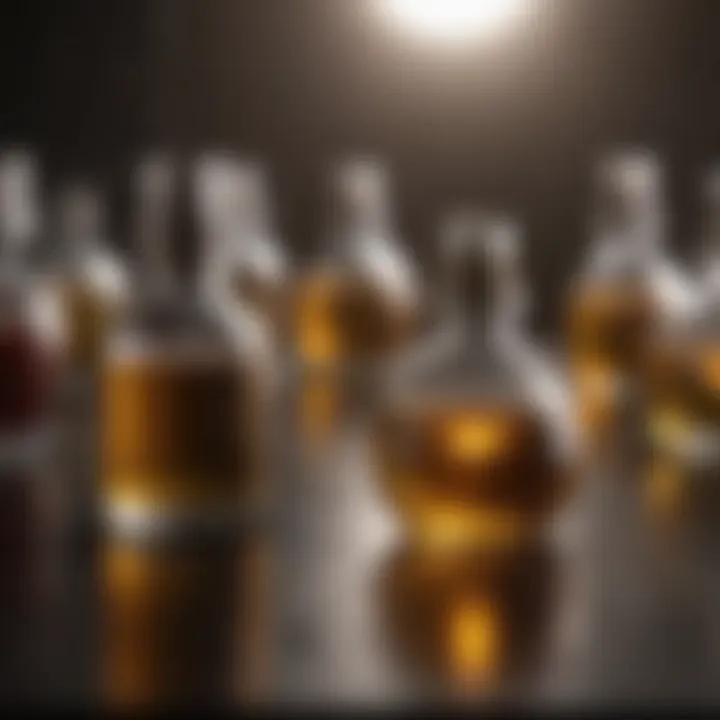
In summary, grasping the fundamentals of thermodynamic and fluid dynamics principles is essential for enhancing spray drying efficiency. This not only ensures that the resulting oils meet industry-specific standards but also paves the way for innovation in product development.
Characteristics of Oils Suitable for Spray Drying
Spray drying is a delicate dance of technology and chemistry, a process that is highly reliant on the characteristics of the oils being utilized. This section dives deep into why understanding these characteristics is paramount for achieving desired outcomes in various manufacturing contexts. Different oils exhibit unique properties that can significantly influence the efficacy of the spray drying process, impacting everything from the texture to the flavor of the final product.
Properties of Different Types of Oils
When considering the use of oils in spray drying, it is vital to assess their properties. The choice isn’t merely arbitrary; it plays a crucial role in dictating quality.
- Viscosity: Some oils are thicker than others, which is a significant consideration. Viscosity influences how well an oil can be atomized. For instance, oils with low viscosity, like canola oil, atomize more effectively than thicker oils such as coconut oil, leading to finer powder and more uniform drying.
- Fatty Acid Composition: The fatty acids present in an oil dictate its behavior during drying. Saturated fats tend to yield a more stable powdered product when compared to unsaturated fats, which may lead to oxidation issues.
- Molecular Weight: Oils with longer chain fatty acids often exhibit different characteristics in behavior during processing. For instance, oils like palm oil, with higher molecular weight, may require a careful approach to maintain the integrity during drying.
- Aroma and Flavor: Oils can vastly differ in their flavor profiles. This variability is critical in industries like food production, where the right flavor must be preserved or enhanced during the drying process.
A careful balance of these properties ensures that the spray drying operation does not compromise the quality of the final product.
Chemical Stability and Shelf Life
The relevance of chemical stability in oils suitable for spray drying cannot be overstated. Stability refers to how well an oil resists chemical changes under various conditions, especially heat.
- Oxidative Stability: This is crucial, particularly for oils high in polyunsaturated fatty acids. Oils that oxidize easily can compromise the quality of both the spray-dried product and its shelf life. Therefore, a comprehensive understanding of how each oil behaves in an oxygen-rich environment is key.
- Shelf Life Concerns: An understanding of the shelf life of various oils is essential for producers. Oils that are prone to rancidity will not only impact taste but could also pose health risks. By doing stability tests during development, manufacturers can predict product longevity accurately.
- Storage Practices: The effectiveness of spray drying can also hinge on storage conditions prior to drying. Oils stored in opaque containers may help in reducing light-induced degradation. The importance of temperature and humidity control in storage cannot be downplayed, also.
In summary, knowing the characteristics of oils suitable for spray drying involves a multi-faceted approach, evaluating viscosity, chemical composition, and stability. Each of these elements contributes to the process's entirety, allowing industries to utilize spray-dried oils effectively without compromising quality over time.
"The choice of oils in spray drying is no minor detail; it weaves into the very fabric of product quality and shelf-life viability."
By ensuring a profound understanding of these traits, producers can optimize their operations, tailor their formulations, and enhance the performance of spray-dried products across various sectors.
Equipment and Technology Used in Spray Drying
Spray drying stands as a pivotal process in the generation of powdered products from liquid feeds. Understanding the equipment and technology used in spray drying is crucial for anyone involved in industries such as food, pharmaceuticals, and cosmetics. This process not only affects the quality and yield of the final product but also plays a significant role in determining efficiency and operational costs.
In this section, we delve deeper into the different types of spray dryers available and the key components that constitute the core of spray drying systems.
Types of Spray Dryers
Different applications necessitate different types of spray dryers; each has its unique characteristics suited for specific tasks. Here are a few notable types:
- Centrifugal Spray Dryers
This type utilizes a high-speed rotating atomizer to create fine droplets, which are then dried by hot air. One of their advantages is the ability to produce a uniform particle size, making them ideal for pharmaceutical applications. - Pressure Nozzle Spray Dryers
Pressure atomization is achieved through nozzles that force the liquid feed through a small opening. This dryer type excels in producing larger droplets, and is widely used for food products. - Two-Fluid Nozzle Spray Dryers
Featuring the use of compressed air or gas, these dryers atomize the liquid into fine droplets. They are versatile and suitable for handling a variety of feed viscosities and particle sizes. - Fluidized Bed Spray Dryers
These combine spray drying with fluidized bed technology, allowing the particles to be further dried as they are suspended in an upward flow of air. This setup often leads to enhanced drying and better control over particle characteristics.
While selecting a type of spray dryer, one must consider several factors such as feed properties, the desired characteristics of the final product, as well as cost-effectiveness in relation to production scale.
Key Components of Spray Drying Systems
Understanding the intricacies of spray drying systems is fundamental for effective application. Each system comprises several essential components:
- Feed System
This system delivers the liquid feed to the atomization unit, ensuring a constant flow with precise control over the feed rate. Consistency here is key for achieving uniformity in the final product. - Atomizer
An atomizer disperses the feed into fine droplets, which can be achieved through various methods: centrifugal forces, pressure nozzles, or two-fluid nozzles. The choice influences the size of droplets produced and subsequently affects drying rates. - Drying Chamber
This is where the drying action takes place. Hot air is introduced, and as the droplets enter, they lose moisture rapidly, transforming into powder. The design of the chamber plays a role in the efficiency of heat and mass transfer. - Cyclone Separator
After the drying process, this component separates the dry particles from the exhaust air. Efficient separation is key to maximizing yield and minimizing waste. - Air Handling Unit
The quality of air circulating through the system significantly affects the final product. This unit adjusts temperature and flow rates to ensure optimal drying conditions.
"A well-designed spray drying system not only boosts productivity but can also enhance the quality and characteristics of the end product."
These systems collectively blend art and technology, ensuring that manufacturers can meet burgeoning market demands while maintaining product integrity. The right blend of equipment in the spray drying process is tantamount to creating high-quality powdered oils that cater to various industries. As the technology continues to evolve, the integration of more sophisticated components promises to further enhance the efficiency and performance of spray drying operations.
Operational Parameters in Spray Drying
Understanding operational parameters in spray drying is crucial for optimizing not just the process itself but also the quality of the end product. The efficiency of spray drying oil depends on multiple factors, including temperature, airflow, feed rate, and concentration. By fine-tuning these elements, manufacturers can significantly enhance yield while minimizing energy consumption and loss of product integrity.
Impact of Temperature and Air Flow
Temperature and airflow play a pivotal role in the spray drying process. The heat serves to evaporate the solvent from the oil emulsion, thus impacting the drying time. An optimal temperature ensures that the solvent evaporates without causing degradation of the product. However, soaring temperatures can lead to a host of issues, from a burnt taste in food products to the partial oxidation of sensitive oils.
- Temperature Optimization:
Ensuring that the temperature is just right involves monitoring heat transfer dynamics. Employing advanced thermal control systems can mitigate overheating risks and improve energy efficiency. - Airflow Dynamics:
Airflow rates directly affect the drying rate and the dispersion of particles during the spray process. Low airflow can lead to inadequate drying, resulting in clumping, while overly fast airflow can cause particles to dry too quickly, affecting their texture.
Controlling airflow can be achieved with adjustable fan speeds, but this introduces added complexity when aligning with temperature control.
"The key to successful spray drying lies in maintaining a delicate balance between temperature and airflow to achieve optimal product quality and economic efficiency."
Feed Rate and Concentration Effects
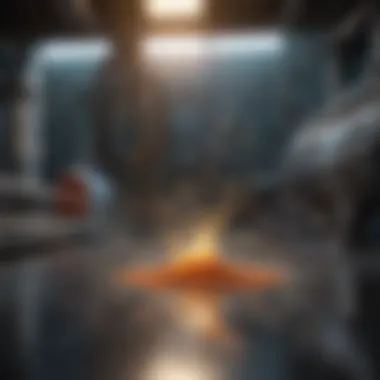
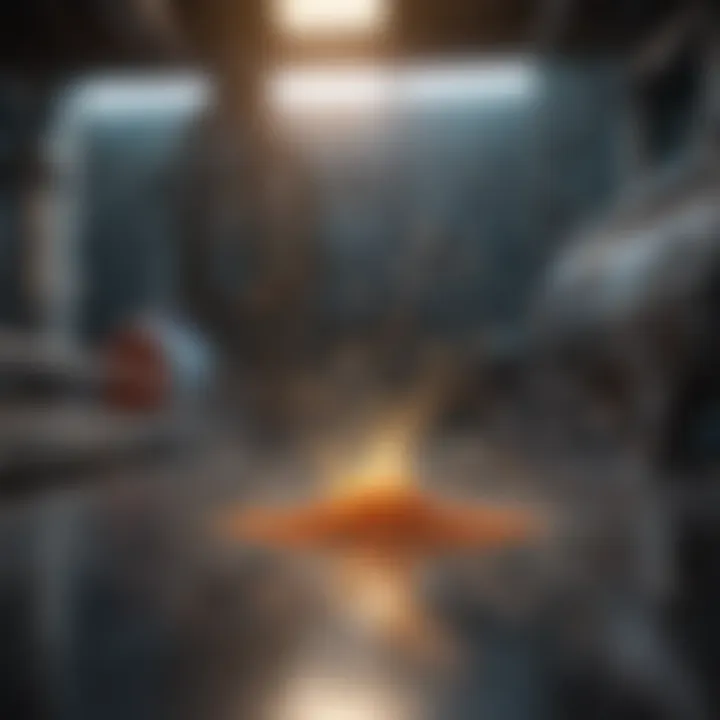
The feed rate also stands as a critical aspect in the spray drying operation. Essentially, it dictates how much product is being fed into the drying chamber and how quickly.
- Feed Rate Determinants:
A higher feed rate may seem advantageous as it promises increased throughput, but it can have counterproductive effects if not managed correctly. When the feed rate exceeds the system capacity, the resultant layer of product may not dry adequately, leading to poor quality and increased waste. - Concentration Importance:
The concentration of the oil feed alters the viscosity of the material. High viscosity can lead to pump issues, while low viscosity may result in incomplete drying as the particles form larger droplets instead of a fine mist. Both scenarios affect how efficiently the drying chamber operates and the purity of the end product.
Balancing the feed rate and concentration demands a careful study of the specific product properties while also accounting for variations in ambient conditions. Various techniques, such as using rheological modifiers, can help stabilize feeds of differing concentrations to ensure optimal performance.
In sum, operational parameters like temperature, airflow, feed rate, and concentration are intertwined and can substantially affect outputs from spray dried systems. Understanding them not only strengthens process control but also enhances the feasibility of meeting end-product specifications.
Efficiency and Yield in Spray Drying
Efficiency and yield play a vital role in the spray drying process. This section examines how both factors influence the effectiveness of producing spray-dried oils across various industries. Efficiency in spray drying refers to the ratio of usable product obtained versus the input spent during the process. Yield, on the other hand, indicates the actual output of spray-dried materials. In a tightly competitive market, balancing these aspects becomes essential for economic viability and technological advancement.
Understanding the right parameters can lead to optimal transformations of oils into powdered form while minimizing waste, which is particularly important in the food, pharmaceutical, and cosmetic sectors. When these factors are fine-tuned, companies benefit from cost reduction, enhanced product quality, and waste minimization. The drive for higher efficiency and yield forms the backbone of ongoing investment into research and development within spray drying technologies.
Factors Affecting Yield
Multiple elements affect the yield of the spray drying process. Addressing these factors can be a game changer:
- Feed Composition: The chemical structure and concentration of oils can substantially influence yield. Oils with high viscosity can hinder atomization during the drying process.
- Drying Temperature: The temperature at which the process operates is crucial. High temperatures may lead to thermal degradation of sensitive compounds found in certain oils.
- Nozzle Design: The design and type of nozzle used determine how effectively the oil is atomized. A poorly designed nozzle can lead to uneven droplet sizes, impacting drying efficiency.
- Air Flow Rate: The rate at which air is introduced into the drying chamber affects drying time and particle size. Optimal air flow helps ensure efficient moisture removal without compromising the quality of the product.
- Dwell Time: The time the particles spend in the drying chamber also influences yield. Insufficient dwell time may prevent complete drying, leading to a product that doesn't meet quality standards.
By tackling these factors systematically, manufacturers can significantly enhance their yield and thus improve the profitability of their spray drying operations.
Ways to Optimize Efficiency
Optimizing efficiency is key for maximizing output in spray drying processes. Here are various methods to achieve it:
- Precise Control of Parameters: Monitoring and adjusting parameters like inlet and outlet temperatures, air velocity, and feed rates in real-time ensures the best drying conditions are maintained.
- Quality of Raw Materials: Using high-quality oils with consistent properties can lead to better process stability and product quality.
- Advanced Nozzle Technologies: Employing nozzles that create uniform droplet sizes can improve drying efficiency and ensure more consistent product characteristics.
- Energy Recovery Systems: Implementing systems that recapture and reuse energy within the spray drying process can lower operational costs and enhance overall effectiveness.
- Regular Maintenance: Ensuring that the equipment is maintained and free of blockages or wear and tear can help maintain optimal performance levels over time.
By applying these strategies thoughtfully, producers can tackle the pressing need for improved efficiency, meeting both production goals and customer expectations.
Applications of Spray-Dried Oils
The applications of spray-dried oils stand as a testament to the versatility and ingenuity of this processing technique. Through spray drying, oils transform into a powdered form, which brings along a plethora of benefits. This section focuses on crucial elements such as the enhancements in product stability, delivery mechanisms, and the practical implications across various sectors that adopt this technology. The efficiency of spray-dried oils aids in balancing consumer demands with manufacturing processes, thus making them an important focal point in multiple industries.
Food Industry Applications
In the realm of food, spray-dried oils are becoming increasingly significant. Food manufacturers often face the challenge of preserving the flavor and nutritional value of oils while extending shelf life. Spray drying steps in to offer a workaround; by converting oils into powder, it helps in encapsulation. This technique not only protects delicate flavors and nutrients but also enhances ingredient handling and product formulation.
"Incorporating spray-dried oils into formulations can lead to more homogeneous mixes, which ultimately results in a better end product for consumers."
When you consider products like instant soups, sauces, and seasonings, the role of spray-dried oils is paramount. Here are a few specific applications:
- Dairy Products: Enhancing the creaminess in powdered milk substitutes.
- Snack Foods: Delivering flavor enhancers in a manageable and stable form.
- Baked Goods: Improving shelf stability and texture.
The trend toward health-conscious choices also cannot be overlooked. Consumers are on the lookout for convenient, nutrient-rich options, prompting companies to innovate using spray-dried oils for fortification purposes.
Pharmaceutical Applications
Spray-dried oils have also carved out a niche in the pharmaceutical sector. The stability of bioactive compounds can be a major hurdle during formulation. Through spray drying, these compounds can be effectively encapsulated, rendering them less susceptible to environmental conditions. This ensures a consistent therapeutic effect over a longer period, essentially boosting product reliability.
In the pharmaceutical arena, you might observe applications such as:
- Controlled Release Formulations: Allowing for a gradual release of active ingredients over time.
- Nutraceuticals: Creating dietary supplements with extended shelf lives.
- Taste Masking: Applying spray-dried oils to improve the palatability of certain medications.
This technology facilitates the fusion of convenience with functionality, making medications easier to consume. The ability to maintain integrity while enhancing biodistribution creates a win-win scenario for both manufacturers and patients.
Cosmetic Industry Utilization
In the cosmetic sector, spray-dried oils find useful applications as well. Formulators are eager to leverage the benefits of spray dried oils in emulsions and powders. For instance, they can deliver targeted skin benefits, such as hydration or nourishment, while improving product texture. Specifically focusing on products like foundations, powders, and lotions, these oils enhance performance without altering the intended effect of the formulations.
Key utilizations include:
- Skin Care: Sources of essential fatty acids can be added to creams without compromising texture.
- Makeup: Improving application smoothness with powder formulations, while also providing additional benefits.
- Fragrance Delivery: Encapsulated scents for prolonged release.
Indeed, utilizing spray-dried oils enables the beauty industry to create more sophisticated products that not only adhere to trends but also meet rigorous quality demands. Ultimately, this technology adds an essential dimension to the way we view both health and beauty products.
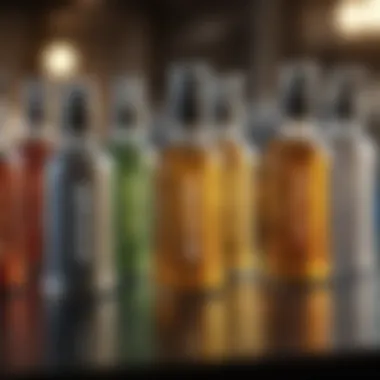
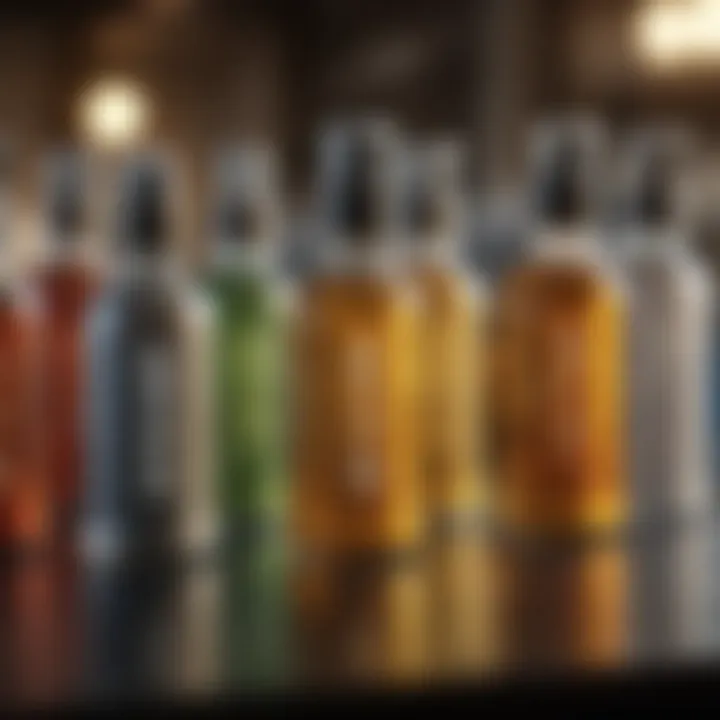
Challenges in Spray Drying Technology
Spray drying is a complex yet dynamic process that offers numerous advantages across various industries. However, lurking behind the curtain is a host of challenges that can complicate its implementation and efficiency. Understanding these challenges is pivotal for professionals who are navigating the intricacies of spray drying, particularly when it comes to maximizing productivity and ensuring quality end products.
Technical Limitations
When we dive into the technical side of spray drying, there are several limitations that can hinder optimal outcomes. First, the particle size distribution is often a sticking point. Depending on the type of oil being sprayed, achieving the desired particle size can be tricky. For instance, smaller particles may clump together, leading to inconsistent quality and problematic rehydration characteristics in food products.
Next, there's the issue of thermal degradation. Some oils, particularly those rich in unsaturated fats, can undergo undesirable reactions when exposed to high heat within the drying chamber. This could lead to compromised flavor profiles and reduced nutritional values, creating a double whammy in both taste and health aspects of the final product.
Moreover, variations in atomization techniques can lead to differences in moisture content. If the atomizer fails to produce a fine mist, the larger droplets may not dry uniformly, resulting in residual moisture that can spur microbial growth, adversely affecting the shelf life. To this point, producer expertise is crucial in selecting the right technology and parameters.
In short, addressing these technical nuances is essential to enhance product quality, ensure safety, and maintain the integrity of the original oils used in spray drying.
Economic Considerations
Turning our focus to the economic factors, the challenges of spray drying also have considerable financial implications. Initially, the capital investment for spray drying equipment can be a major hurdle for smaller businesses. The cost of high-quality spray dryers, combined with maintenance and spare part expenses, often pushes these companies to the edge of their financial limits.
Additionally, energy consumption remains a significant concern. Spray drying is energy-intensive, requiring substantial power to maintain optimal temperatures and air flow. Rising energy prices can quickly turn what was once a profitable venture into a precariously tight operation.
Furthermore, the scalability of spray drying operations poses a challenge. Small-scale spray dryers that cater to niche markets may not experience the same economies of scale as larger operations, potentially resulting in higher costs per unit. Balancing production efficiency with flexibility in serving various market demands becomes critical in realizing profit margins.
The overall takeaway is that managing these economic challenges requires a comprehensive understanding of both market dynamics and operational optimization to ensure that spray drying remains a viable and profitable production method in the long run.
"Navigating both the technical and economic hurdles of spray drying is crucial in maintaining quality and profitability in production processes."
By meticulously addressing these challenges, industry players can maximize the effectiveness of spray drying technology while maintaining competitive edge in a rapidly evolving market.
Future Trends in Spray Drying
As industries continue to evolve, spray drying processes are also undergoing significant shifts. Understanding future trends in spray drying is crucial not only to improve operational practices but also to stay competitive in increasingly global markets. These trends are influenced by technological advancements, consumer demands for sustainable products, and the ongoing pursuit of efficiency across various sectors, particularly in food, pharmaceuticals, and cosmetics.
Advancements in Technology
In recent years, technology related to spray drying has made leaps and bounds. Innovative designs and materials are being adopted that enhance the efficiency and effectiveness of spray drying systems. Key advancements include:
- Smart Spray Drying Systems: Integrating Internet of Things (IoT) technology into spray dryers allows for real-time monitoring and control. These smart systems can analyze data such as temperature and humidity levels and adjust parameters promptly, minimizing fluctuations and enhancing product consistency.
- Advanced Atomization Techniques: New atomization technology enables smaller droplets, improving surface area for evaporation. This results in higher quality powders with better solubility and functionality. These tiny droplets also lead to better uniformity in the final product, which is crucial in applications like pharmaceuticals where precision matters.
- Reduced Energy Consumption: Recent designs focus on energy efficiency, incorporating heat recovery systems and more efficient drying chambers. This not only decreases operational costs but also addresses environmental concerns efficiently.
"Continuous improvement in technology plays a vital role in setting benchmarks for quality and efficiency in spray drying processes."
These technological advancements promise to ease operation complexities and maximize yield, effectively setting the stage for a new era in spray drying.
Sustainability and Environmental Impact
Sustainability is more than just a buzzword; it’s a guiding principle shaping the future of spray drying. Companies are increasingly responsible, seeking to curb their ecological footprints. This trend involves:
- Renewable Energy Sources: The use of solar and wind energy in drying processes is gaining traction. By harnessing renewable resources, companies can drastically reduce their dependence on fossil fuels and lower greenhouse gas emissions.
- Biodegradable Materials: As the emphasis on sustainability grows, there’s a push towards using biodegradable carriers in spray-dried products. These materials help in reducing waste and enhance the acceptability of products, especially in the food and cosmetic industries where consumers are keen on environmentally friendly options.
- Efficient Waste Management: Updated processing technologies have improved the management of by-products. Companies are increasingly looking at ways to recycle water and repurpose other materials, further minimizing waste while optimizing resource usage.
As industries take these steps, they not only comply with regulations but also appeal to a more eco-conscious consumer base that favors products with lesser environmental impact. In the coming years, the focus on sustainability in spray drying will likely intensify, pushing manufacturers to adopt more green technology and practices, ultimately leading to an overall healthier planet.
By staying attuned with these trends, stakeholders in the spray drying arena can ensure they are not just keeping pace, but also paving the way for a more efficient and sustainable future.
Culmination and Implications
In wrapping up our exploration of spray drying oil, it’s crucial to appreciate the intricate relationship between this technology and its multifaceted applications across sectors. The significance of spray drying extends beyond just preserving oils; it's about enhancing their usability and extending their shelf life. In the food industry, for instance, the ability to incorporate rich nutrients without compromising flavor is a game changer. Similarly, in pharmaceuticals, the controlled release of active ingredients through spray-dried formulations can lead to improved patient outcomes. The cosmetic industry also benefits, allowing for the creation of more efficient, concentrated products that resonate with consumer demand for multifunctionality.
But it's not all smooth sailing. There’s still a significant amount of ground to cover when it comes to optimizing this technology and addressing the challenges it faces. Issues like energy consumption and economic viability are pressing concerns that need continued attention. Moreover, as sustainability becomes a more prominent aspect of product development, the industry must adapt to incorporate environmentally friendly practices into spray drying processes. Thus, understanding the implications of these practices is crucial for a better tomorrow.
"The fate of a technology often lies not only in its immediate benefits but also in its impact on broader societal trends."
Summary of Key Findings
From the information detailed throughout the article, several key points emerge clearly:
- Versatility of Application: Spray drying is not just limited to preservation; its application in food, pharmaceuticals, and cosmetics showcases its versatility. Each of these fields reaps distinct benefits, enhancing product quality and functionality.
- Technical Innovations: The evolution of spray drying technology has led to improved efficiencies and yields. Innovations in equipment and operational parameters are crucial to ensuring that these advancements continue to meet industry demands.
- Economic Factors: While there are substantial benefits, economic considerations cannot be overlooked. Assessing the cost implications of spray drying processes remains fundamental to its widespread adoption.
- Sustainability Imperative: The necessity for sustainable practices in all forms of production is more pressing than ever. The spray drying industry must look toward greener solutions not only to meet regulatory demands but to align with consumer expectations as well.
Importance of Continued Research
Research in the field of spray drying technology remains imperative. New methodologies and formulations must be explored to push boundaries further in efficiency and effectiveness. For instance, investigating how different oil characteristics respond to varying drying conditions could yield insights that enhance both food preservation and nutritional delivery. Additionally, economic studies focusing on the cost-benefit analysis of different spray drying technologies will inform business decisions and facilitate wider adoption.
Moreover, as sustainability trends rise, research into eco-friendliness of spray drying techniques must be prioritized. Innovations such as utilizing renewable energy sources and developing biodegradable carriers for the drying process present opportunities for growth and comply with consumer demands for sustainable practices. In essence, continued investment into this field serves not only innovation but also the greater good, fulfilling corporate responsibility towards a more sustainable future.