Comprehensive Guide to Lithium Battery Manufacturing
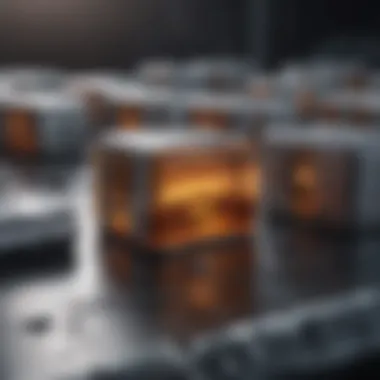
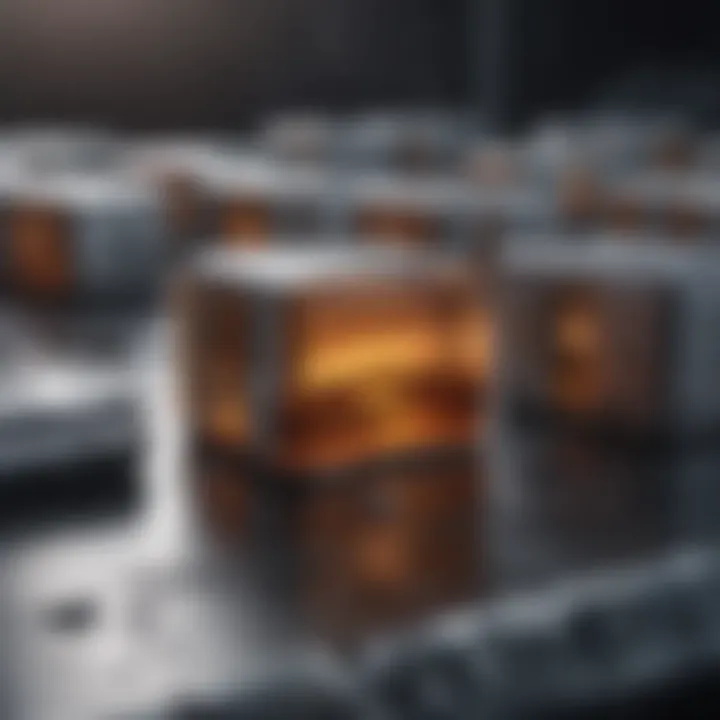
Intro
Lithium batteries play a pivotal role in today’s tech-savvy world, powering everything from laptops to electric vehicles. But have you ever thought about how these tiny electronic dynamo’s come to life? There’s more than meets the eye. The manufacturing process is a complex tapestry woven from various techniques, innovations, and materials. Understanding these processes is crucial, not only for tech enthusiasts but also for anyone who aims to grasp the evolving landscape of energy solutions.
In this journey, we’ll dissect different stages of lithium battery production. We will travel from the extraction of raw materials—like lithium, cobalt, and nickel—right through to the final assembly of the battery cells. Not only will this article shed light on key materials and techniques, but it will also delve into modern advancements that have taken this industry by storm. Plus, it’ll emphasize the importance of quality control to ensure that these batteries function as intended.
"The journey from material to energy storage is a narrative filled with innovation and precision, reflecting the technological prowess necessary to power our future."
As we dissect each process step-by-step, the aim is to equip students, researchers, educators, and professionals with a comprehensive understanding of the intricate workings behind manufacturing lithium batteries. So let’s plug in and get started!
Foreword to Lithium Batteries
Lithium batteries, often seen as the backbone of modern portable energy storage, play a pivotal role in powering a multitude of devices, from smartphones to electric vehicles. Their significance within the realm of energy solutions cannot be overstated; they embody a blend of high energy density, longevity, and reliability that has transformed technology as we know it. Understanding lithium batteries is not solely about grasping their technical specifications but also recognizing their impact on sustainability, economic dynamics, and advancing technology.
The importance of lithium batteries in energy transition and innovation presents a rich subject. As we navigate towards greener alternatives and reduced carbon footprints, lithium batteries are often at the forefront, capturing attention and investment. With their increasing demand across various industries, it becomes essential to dissect their manufacturing processes, from the sourcing of raw materials to the assembly of finished products.
Understanding Lithium Technologies
To delve deeper into the world of lithium batteries, we need to clear the fog around lithium technologies. At its core, lithium ion technology is predicated on the movement of lithium ions from the anode to the cathode during discharge, and vice versa during charging. This movement facilitates energy flow, making lithium batteries an efficient choice for energy storage. Additionally, advancements in lithium technologies, such as solid-state batteries, promise improved safety and performance.
Key advancements in lithium technology include:
- Improved energy densities that allow batteries to hold more power without increasing size.
- Rapid charging capabilities which enable users to quickly recharge devices or vehicles, enhancing usability.
- Enhanced lifecycle management ensures longer lifespan while maintaining performance, reducing the frequency of replacements.
The dynamic evolution of lithium technologies is not just a technical undertaking; it's a reflection of growing consumer needs and environmental responsibility. As innovation unfolds, the dialogue around these technologies emphasizes a commitment to advancing efficiency and sustainability.
The Importance of Lithium Batteries
When we articulate the importance of lithium batteries, their foundational role in a global shift toward renewable energy must be acknowledged. These batteries contribute significantly to the development and deployment of clean technologies. From wind energy storage solutions to solar-powered devices, lithium batteries make it possible to harness energy from more unpredictable sources.
Moreover, lithium batteries are essential in the context of electric vehicles, where they are indispensable for reducing reliance on fossil fuels. With rising fuel prices and the global push for emission reductions, the adoption of lithium battery technology in the automotive industry is not merely advantageous, but imperative.
"The future drives with lithium batteries; it's where innovation meets sustainability."
The pivotal role of lithium batteries extends beyond their immediate applications. As we venture into a future increasingly reliant on technology, the ability of these batteries to facilitate greater energy efficiency and support advanced electronic systems is irrefutable. The conversation surrounding lithium batteries is no longer confined to their scientific attributes; it encompasses a broader consideration of their societal and economic implications.
In summary, the understanding of lithium batteries and the technologies that govern them lays the groundwork for appreciating their significance in our evolving world. As industries adapt and change, so too will the demands and functionalities of lithium batteries, making this an exciting and crucial field for exploration.
Raw Materials Used in Lithium Battery Manufacturing
The manufacturing of lithium batteries is a multifaceted process that hinges on the quality and properties of its raw materials. Understanding these materials is vital because they not only influence the efficacy and longevity of the batteries but also their overall environmental impact. Each component plays a critical role, and choosing the right materials can result in performance enhancements, reliability, and sustainability.
Sources of Lithium
Lithium is the cornerstone of lithium battery production. This metal is obtained mainly from two primary sources: hard rock mining and lithium brine extraction.
- Hard Rock Mining: This method involves extracting lithium primarily from spodumene, a mineral found in pegmatite deposits. The mining of this mineral is intensive, but it yields high-purity lithium products. The trade-off, however, is its significant environmental cost due to land disruption and habitat destruction.
- Brine Extraction: Alternatively, lithium can be obtained from brine pools, primarily found in regions like the Lithium Triangle in South America. Here, lithium-rich brine is pumped to the surface, where it evaporates in the sun, leaving behind lithium salts. This method is generally deemed more environmentally friendly, although it requires massive amounts of water in already arid regions.
Each method comes with its own set of advantages and challenges, making it crucial for manufacturers to carefully consider their selection based on environmental policies and market demands.
Other Key Components
In addition to lithium, several other materials are essential in the construction of lithium batteries. The following components have significant implications in battery performance and safety:
Graphite
Graphite is commonly used as anode material in lithium batteries. Its key characteristic is the ability to efficiently host lithium ions moving in and out during charge and discharge cycles, which is fundamental for battery performance.
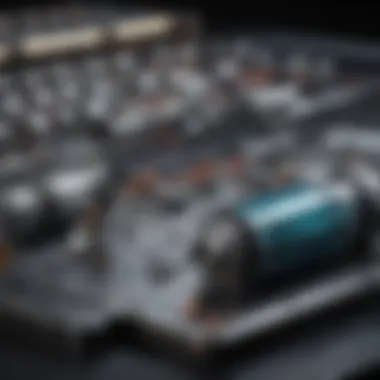
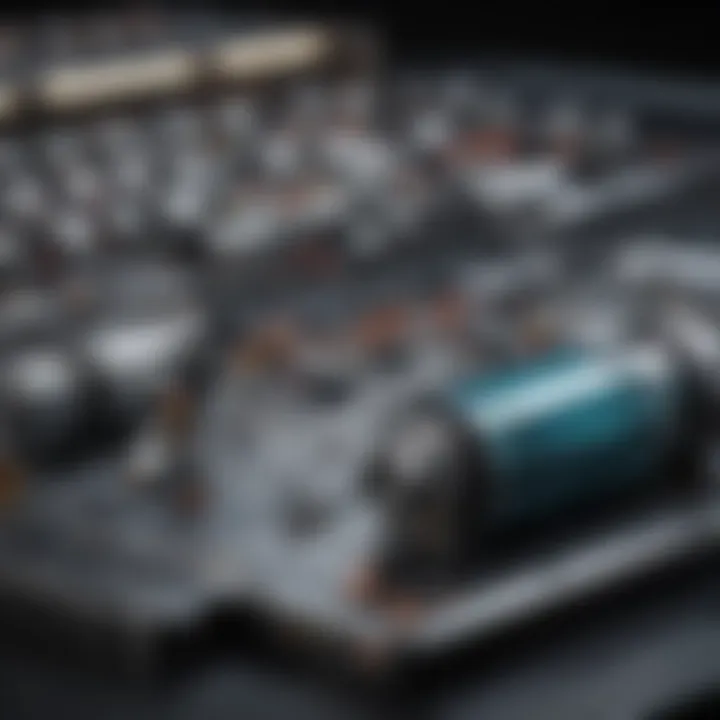
The unique feature of graphite lies in its layered structure, allowing for smooth electron mobility and excellent conductivity. This results in fast charge times and enhanced energy density. However, sourcing natural graphite has environmental implications. Mining often leads to disruption of local ecosystems. As such, researchers are exploring synthetic alternatives to minimize ecological damage without sacrificing performance.
Electrolytes
Electrolytes are crucial for facilitating charge transfers between electrodes. A significant characteristic of electrolytes is their ionic conductivity, which is pivotal for energy transfer within the battery. Commonly used materials include lithium salts, typically dissolved in organic solvents.
One unique aspect of electrolytes is their temperature stability. While some electrolytes are effective at ambient temperatures, others can handle a wider range. However, the liquid nature of many electrolytes poses risks such as flammability and leakage. As a result, solid-state electrolytes are increasingly becoming popular due to their improved safety and performance.
Separators
Separators are thin films that prevent direct contact between the anode and cathode while allowing ionic transfer. Their key characteristic is porosity, which is essential for enabling ion movement while maintaining safety.
The unique feature of separators is that they enhance the safety of the battery pack by minimizing the risks of short circuits, which can lead to severe malfunctions. However, the choice of the separator material can also influence the overall energy efficiency of the battery. Materials like polyethylene and polypropylene are commonly used, but advancements in material science are leading to even more efficient separator options.
The choice of raw materials significantly impacts the efficiency, safety, and environmental footprint of lithium batteries.
In summary, the raw materials used in lithium battery manufacturing are diverse, each contributing uniquely to the battery's performance. A thorough understanding of their properties and implications is essential for manufacturers aiming for excellence in battery technology.
Extraction and Processing of Raw Materials
The extraction and processing of raw materials stand as the foundation for the manufacturing of lithium batteries. Understanding this phase is crucial for appreciating the entire battery production lifecycle. Without high-quality raw materials sourced through rigorous methods, the performance and longevity of lithium batteries could be significantly compromised. Furthermore, the environmental impact of these processes raises considerations about sustainability that have become increasingly relevant in today’s market.
Mining Techniques for Lithium
When we delve into the mining techniques for lithium, two primary methods come into focus: hard rock mining and lithium brine extraction.
- Hard Rock Mining: In this method, lithium-containing minerals, such as spodumene, are extracted directly from the earth. This process often involves traditional mining techniques similar to those used for other metals. As an interesting aside, Australia is known for having some of the largest hard rock lithium mines in the world, such as the Greenbushes mine. The rocky landscape there includes precious lithium deposits that are rigorous to prospect but yield significant rewards.
- Lithium Brine Extraction: This method is often employed in areas like South America where lithium-rich salts are found beneath the surface, usually in salt flats. Here, water is pumped into these brine areas to dissolve the lithium. Afterward, the mixture is contained in large evaporation ponds. As the sun beats down, the water evaporates, leaving behind lithium carbonate, which is then filtered for purity.
Both methods have their pros and cons, with hard rock mining generally being more stable but also more labor-intensive. In contrast, brine extraction is seen as less intrusive on the land. However, it may come with the added cost of requiring extensive water usage—an issue in some regions where water is scarce.
Refining Lithium for Battery Production
Once lithium is extracted, refining it into a form that can be utilized in battery manufacturing is the next critical step. The refinement process involves several stages, aimed at producing high-purity lithium salts suitable for electrodes.
In the initial refinement stage, the extracted mineral undergoes crushing followed by chemical processing. After extraction, the lithium is often contained in forms such as lithium hydroxide or lithium carbonate, depending on the specific needs of the battery design.
- Chemical Processing: This involves methods like roasting and leaching, which help separate lithium from other minerals and impurities. The aim is to isolate lithium in a form that maintains the integrity of its properties. Companies like Albemarle and SQM have made significant strides in optimizing these processes to minimize environmental impact while maximizing yield.
- Purification: At this stage, lithium undergoes various purification techniques, often involving filtration or further chemical reactions. This ensures that any unwanted elements are eliminated, leaving behind a high-quality product that meets regulatory standards.
"The purity of lithium directly influences the performance of the batteries; it’s akin to cooking—using the right ingredients will yield the best results."
Manufacturing Steps of Lithium Batteries
Manufacturing lithium batteries is more than just putting together various components; it involves meticulous planning and execution at each stage. The steps taken during the manufacturing process directly affect the performance, safety, and lifespan of the batteries produced. Understanding these stages sheds light on how innovation and precise engineering come together to create the high-performance batteries we rely on today.
Cell Design and Architecture
The design of a lithium battery cell is fundamental. It determines how efficiently energy is stored and released. Key factors such as size, shape, and configuration all come into play. Each decision made during the design phase impacts energy density, safety, and even thermal management. For example, a cylindrical cell design, often seen in applications like electric vehicles, offers excellent energy capacity and cooling efficiency. This is why a well-thought-out design is crucial,
Electrode Preparation
Coating Processes
Coating processes are a significant step, where the active materials are applied to the substrate. The nature of this process influences the battery's overall efficiency and longevity. Consistency in thickness and uniformity is vital, as any anomalies can lead to improper charging and diminished performance over time. The choice of materials for the coating can also impact the manufacturing cost and environmental footprint. Using advanced techniques like slot-die or gravure coating allows for better control over these factors, making it a popular choice among manufacturers. The unique aspect of these processes is their ability to scale, catering to mass production needs while maintaining quality.
Drying Techniques
Following the coating, drying techniques come into play. Proper drying ensures that solvents from the coatings evaporate completely, which is a must to prevent any reactions during battery operation. Common methods, like infrared drying or convection drying, have their own sets of pros and cons. Infrared drying is faster and more energy-efficient but might not suit all material types. Drying techniques influence the microstructure of the electrodes, so manufacturers must choose carefully to optimize charge capacity and cycle life.
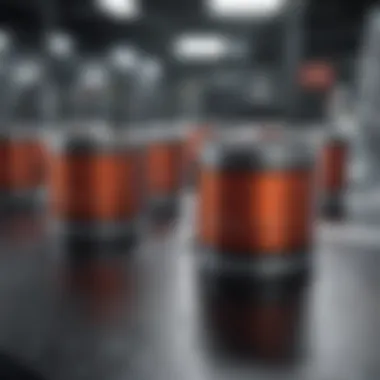
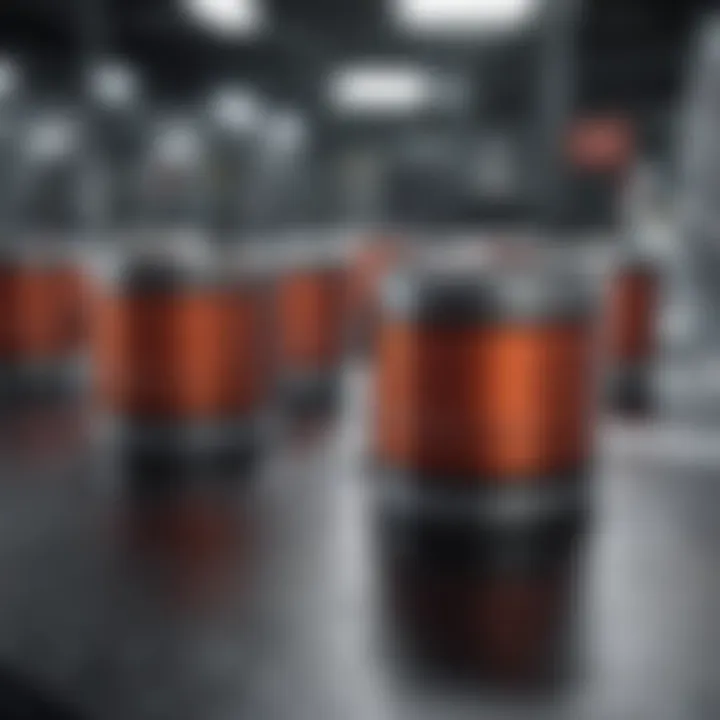
Assembly of Battery Cells
Stacking or Winding
The assembly step is where all the components come together, and manufacturers have two main approaches here: stacking or winding. Stacking layers of electrodes and separators is a straightforward method that lends itself well to high-capacity designs, while winding can be more compact and can reduce space. The choice between these methods ultimately depends on the specific application of the battery and target performance characteristics. Both methods have particular advantages but must be executed with precision to ensure uniformity in the final product.
Filling with Electrolyte
Filling the cells with electrolyte is another critical step that can make or break the battery's reliability. The electrolyte needs to be homogeneous and fully saturate the electrodes without trapping air bubbles. This step influences not only the conductivity of the battery but also its overall safety. Manufacturers must ensure that the filling process occurs under controlled environments to prevent contamination. Furthermore, using a gel-like electrolyte instead of liquid can offer safer handling and better performance but alters the manufacturing complexity.
Formation and Aging
The final manufacturing phase encompasses formation and aging. This involves cycling the battery at specific conditions to stabilize the chemical and physical properties of its materials. The formation step is pivotal; it sets the initial chemistry of the cell and regulates the growth of solid electrolyte interphase, which affects the lifespan. Aging, on the other hand, allows the batteries to stabilize and confirms that they meet pre-defined performance standards before they are sent off for quality assurance.
In manufacturing lithium batteries, the methodical approach ensures that each product is not only functional but also safe and reliable, catering to the demands of the modern world.
Quality Control Measures
Quality control is the cornerstone of lithium battery manufacturing. It guarantees product reliability, performance, and safety. Each stage, from raw materials to final assembling, requires thorough evaluations to confirm that standards are met. This not only enhances the product's longevity but also helps in reducing defects that might lead to security risks or performance issues.
Control measures often encompass a variety of testing procedures that track how well the battery performs under various conditions. In a world progressing rapidly towards electric vehicles and renewable energy solutions, efficient quality control measures ensure that the batteries can endure sustained use and harsh environments.
Testing Procedures
This section delves deep into two crucial testing procedures: Cycle Life Testing and Safety Assessments. Each of these plays a significant role in guaranteeing that the batteries meet the required performance standards.
Cycle Life Testing
Cycle life testing evaluates how many charge and discharge cycles a lithium battery can endure before its capacity drops below a specified threshold. It usually is a pivotal aspect of battery development as it gives insights into a battery’s durability over time. This type of testing typically involves subjecting battery cells to continuous charging and discharging while measuring their performance over many cycles.
Key characteristics of cycle life testing include its ability to reflect real-world usage and conditions. By simulating how the battery will be used, manufacturers can gain valuable data about the battery’s endurance. This makes it a beneficial choice for ensuring the long-term viability of lithium batteries, especially for applications in electric vehicles where long life between charges is critical.
One unique feature of cycle life testing is its capacity retention measurement. By tracking how much storage capacity diminishes after each cycle, manufacturers can forecast the battery's lifespan effectively. However, the disadvantage arises from the lengthy time these tests can take, sometimes extending into several months.
Safety Assessments
On the safety front, safety assessments focus on identifying potential hazards associated with lithium batteries, such as overheating or the risk of combustion. This procedure involves various methods including thermal runaway testing and short-circuit testing.
The key characteristic of safety assessments is that they ensure the battery will function safely under extreme conditions. They are foundational for regulatory compliance and achieving consumer trust, making it a crucial element in the battery manufacturing process.
One unique feature of these assessments is that they often require standardized protocols which are crucial for evaluating safety across different products. While this adds reliability, it can also limit flexibility in design and innovation since manufacturers need to adhere to these regulations.
Standards and Regulations
Standards and regulations surrounding lithium battery manufacturing guide quality control practices and ensure products meet safety and performance benchmarks. Various organizations establish these guidelines, which manufacturers must follow to ensure their batteries are safe for consumer use.
Each region may have different sets of standards, from the International Electrotechnical Commission (IEC) to the Underwriters Laboratories (UL). Following these regulations is essential not only for compliance but also for maintaining consumer confidence in battery technology.
In summary, the integral part that quality control measures play in lithium battery manufacturing cannot be overstated. As technology moves forward, stringent testing and adherence to safety standards are necessary for shaping the future of this vital energy storage technology.
Environmental Impact of Lithium Battery Manufacturing
Understanding the environmental impact of lithium battery manufacturing is essential in today’s context, where sustainability and responsibility take center stage. As the demand for lithium batteries continues to rise, so does the scrutiny around how they are produced and what repercussions stem from their manufacture. This section will delve into various considerations that surround the environmental footprint of lithium batteries, focusing on sustainability in sourcing materials and methods for recycling and disposal.
Sustainability in Material Sourcing
In the quest for more sustainable practices, the sourcing of materials for lithium batteries has emerged as a pivotal concern. Lithium extraction itself can leave a mark on the ecosystem, particularly in areas like South America’s Lithium Triangle. The impact on water scarcity is significant, as extracting lithium consumes vast amounts of groundwater. Companies need to take a hard look at their sourcing methods and find ways to mitigate harm.
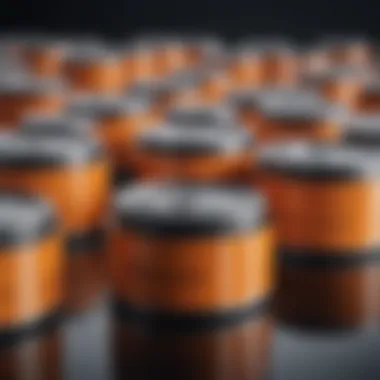
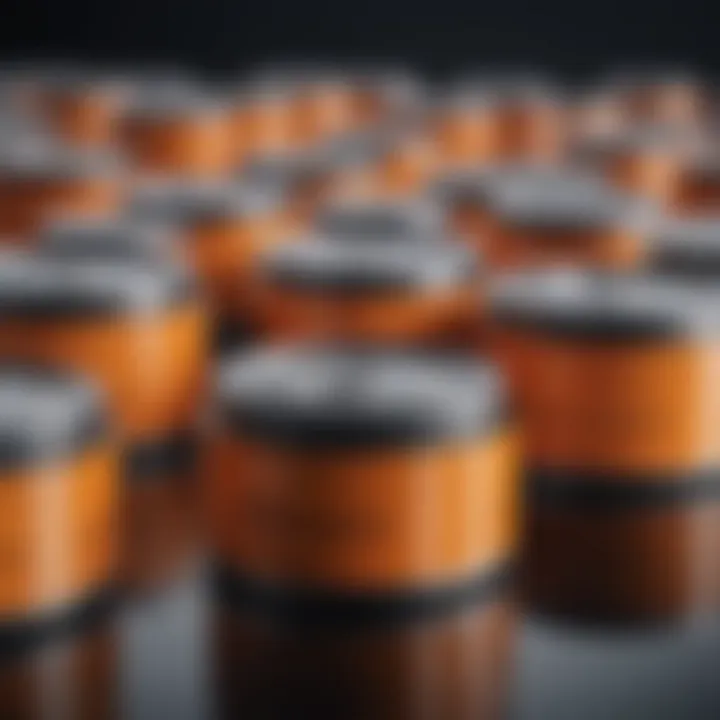
Some advancements have been made, like direct lithium extraction technologies, which are less water-intensive. This method, although still in its infancy, shows potential in reducing the detrimental effects of traditional mining processes. Additionally, exploring alternate lithium sources or substitutes, such as seawater or synthetic options, can pave the path toward more environmentally friendly practices.
"In an age where the earth's resources feel increasingly finite, the approach to sourcing lithium has to shift from exploitative to regenerative."
However, it's crucial to consider that sustainability is not merely about water use. Energy consumption also plays a part. If a mine relies on fossil fuels for energy, even the most water-efficient processes could still contribute to greenhouse gas emissions.
Recycling and Disposal Methods
With the growing circulation of lithium batteries, establishing effective recycling and disposal methods has become a pressing necessity. Unlike traditional batteries that often pollute under improper handling, lithium batteries contain materials that can be recycled. This is not only an opportunity for resource recovery but also a way to significantly reduce waste. Recycling lithium can conserve up to 95% of the energy used to produce new lithium, making it financially viable as well as environmentally friendly.
The recycling process generally involves several steps, including collection, sorting, and material recovery. Here’s a brief overview:
- Collection: Used batteries need to be collected responsibly, often through specialized recycling programs.
- Processing and Sorting: Once collected, batteries are sorted by chemistry to ensure proper processing.
- Material Recovery: Valuable materials like lithium, cobalt, and nickel are extracted for reuse, closing the loop on production resources.
Innovations in recycling technology also show promise. For example, hydrometallurgical processes use less energy than traditional pyrometallurgical methods. Additionally, some companies are developing urban mining techniques, picking lithium and other metals from not just batteries but electronic waste. These innovations could very well steer the industry toward larger-scale sustainability.
In summary, the environmental impact of lithium battery manufacturing is multifaceted and demands thoughtful exploration. Focusing on sustainable sourcing practices and enhancing recycling methods can not only lessen the ecological footprint but also drive the industry toward greener horizons. Engaging with this topic yields insight into how lithium technologies could be revolutionized for a more sustainable future.
Future Trends in Lithium Battery Technology
As we march further into an age dominated by technological advancements, the significance of lithium battery technology cannot be overlooked. This section covers future trends in lithium battery manufacturing, spotlighting innovations that promise to enhance efficiency, sustainability, and overall performance. Understanding these trends is not just for tech enthusiasts; it’s vital for anyone invested in the future of energy solutions, including students, researchers, and industry professionals.
Innovations in Battery Chemistry
One of the most exciting areas of development lies in battery chemistry itself. Researchers are constantly tinkering away in labs, endeavoring to create new materials that offer greater energy density and longer life cycles. Solid-state batteries are gaining traction as they replace liquid electrolytes with solid materials, potentially minimizing safety hazards and maximizing energy storage capabilities. Notably, the use of lithium-sulfur and lithium-air chemistries is being investigated, which promise even higher energy capacities than traditional lithium-ion designs.
- Benefits:
- Increased energy density, leading to longer-lasting batteries.
- Enhanced safety profiles due to reduced risk of leakage or thermal runaway.
- Simpler recycling processes and less environmental impact, as some alternative materials may be more abundant and eco-friendly.
Emerging Manufacturing Technologies
The way batteries are produced is on the cusp of a significant transformation. Automation and robotics are becoming integral in manufacturing lines, increasing precision and productivity while reducing human error.
- Additive manufacturing, known more commonly as 3D printing, is also coming into play, allowing for complex designs that were previously difficult or impossible to achieve. Imagine battery components printed to exact specifications, optimizing both space and functionality within electronic devices.
- In terms of environmental considerations, advancements in materials and processes are focused on reducing waste. For instance, closed-loop recycling systems are being designed to recover key materials from old batteries rapidly, thus lessening the need for new raw resources.
"The adoption of automated systems and innovative manufacturing processes not only boosts efficiency but also paves the way for sustainable practices in lithium battery production."
Potential Market Developments
The market for lithium batteries is expected to explode, fueled by the rising demand in electric vehicles, renewable energy storage, and portable electronics. According to various market analyses, the need for high-performance batteries is only set to skyrocket in the coming years.
- Electric Vehicles (EVs): As more consumers opt for electric cars, the demand for advanced lithium batteries will surge. Major automakers are investing heavily in developing more efficient batteries to extend driving range and lower charging times.
- Energy Storage Solutions: Distributed power generation from renewable sources has highlighted the need for effective energy storage systems. Here, lithium batteries play a critical role in stabilizing the electric grid and ensuring energy availability even when the sun isn't shining or the wind isn't blowing.
- Wearable & Portable Technology: The market for smaller, high-performance batteries has led to exciting developments in wearable technology, pushing manufacturers to innovate in miniaturization, while ensuring safety and long life.
The End
The exploration of lithium battery manufacturing is not merely an academic exercise; it holds significant implications for various sectors of technology and everyday life. With the world increasingly leaning towards sustainable energy solutions, understanding this manufacturing process becomes crucial.
Summary of Key Points
To recap the key elements discussed, we delved into:
- Raw Materials: Recognizing the critical sources of lithium and other components like graphite and electrolytes.
- Manufacturing Steps: Detailing from cell design to assembly, every step is pivotal in ensuring the efficiency of the final product.
- Quality Control: Highlighting the rigorous testing procedures and adherence to standards that ensure the safety and reliability of lithium batteries.
- Environmental Considerations: Addressing the sustainability issues surrounding material sourcing and the importance of recycling and disposal methods.
- Future Trends: A glimpse into battery chemistry innovations and manufacturing advancements, which hold promise for enhanced performance and new applications.
This summary encapsulates the intricate journey of lithium batteries from raw materials to end-use, showcasing not just the processes involved, but also the broad impacts of these technologies.
The Role of Lithium Batteries in the Future
Looking forward, lithium batteries are poised to play a pivotal role in shaping modern technology. As electric vehicles gain traction and renewable energy storage becomes paramount, these batteries are at the forefront of this transformation.
Consider the following points:
- Energy Density: The continuous improvement in energy density means that lithium batteries can store more power without becoming cumbersome. This attribute is essential for applications ranging from consumer electronics to electric vehicles.
- Sustainability Initiatives: With the push for greener alternatives, advancements are underway to reduce the environmental footprint of lithium extraction and recycling processes, ensuring that the future of battery manufacturing aligns with sustainability goals.
- Technological Innovations: Ongoing research into alternatives like solid-state batteries may revolutionize the field, potentially providing even better safety and efficiency.
- Market Demands: As technology evolves, the demand for efficient, reliable, and safe energy storage solutions will continue to grow, and lithium batteries will remain at the heart of these solutions.